EBK PRACTICAL MANAGEMENT SCIENCE
5th Edition
ISBN: 9780100655065
Author: ALBRIGHT
Publisher: YUZU
expand_more
expand_more
format_list_bulleted
Concept explainers
Question
Chapter 12, Problem 61P
Summary Introduction
To minimize: The total annual ordering and holding costs meeting the service level constraint.
Inventory and supply chain models:
The functions of inventory and supply chain are one of the most important business decision areas for an organization. The first important aspect of these concepts is to have adequate inventory on hand. The second important aspect is to carry a little amount of inventory as possible.
Expert Solution & Answer

Want to see the full answer?
Check out a sample textbook solution
Students have asked these similar questions
Question 1 (25 Marks)
Procurement is a key strategic function that directly impacts an organisation’s ability to create value, manage risks, and
maintain a competitive advantage in the market.
Critically analyse the strategic roles of procurement and how procurement practices in the fashion industry can strategically
address complex challenges such as supply chain efficiency, sustainability, cost management, and global sourcing. Provide
examples from the fashion industry to further your analysis.
Question 2 (25 Marks)
There are several enablers that need to be in place for a procurement and supply management function to implement a
value-generating mode.
Examine the extent of these enablers as they present themselves in the fashion industry.
Question 3 (25 Marks)
You are hired by local clothing chain Fashion World. The brand wants to instill a culture of professional
purchasing. Construct a policy document which you would present at the next strategy meeting which inculcates the…
◄ Files
18:11
5G
CSTUDY_Jan25_SCMH_PS...Final_20241203151014.pdf
FORMATIVE ASSESSMENT 1
Read the article below and answer ALL questions that follow
Are your favourite fashion brands using forced labour?
[100 MARKS]
The global fashion and retail industry's reliance on producing quick-tumaround goods at a low cost through outsourcing and
complex, globalised supply chains has allowed forced labour to thrive, workers' rights advocates war, claiming that major
fashion brands profiting from the model seem reluctant to change.
The apparel sector employs over 60 million workers worldwide, according to the World Bank Group. And while 97 percent of
fashion and retail brands have codes of conduct and corporate social responsibility (CSR) standards, such policies are
neither effective in preventing forced labour nor in ensuring remedy outcomes for workers, according to advocacy group
KnowThe Chain
KnowTheChain's 2021 Apparel and Footwear Benchmark Report (PDF) recently ranked 37 of the world's…
What does a Balanced Workout plan ensure comprehensive fitness?
What are the obstacles involved in a Balanced Workout plan to ensure comprehensive Fitness?
How does mental well-being entail implementing techniques such as mindfulness, therapy, physical activity, and social support to cultivate emotional resilience and mitigate stress?
Chapter 12 Solutions
EBK PRACTICAL MANAGEMENT SCIENCE
Ch. 12.4 - Prob. 1PCh. 12.4 - Prob. 2PCh. 12.4 - Prob. 3PCh. 12.4 - Prob. 4PCh. 12.4 - Prob. 5PCh. 12.4 - Prob. 6PCh. 12.4 - Prob. 7PCh. 12.4 - Prob. 8PCh. 12.4 - Prob. 9PCh. 12.4 - Prob. 10P
Ch. 12.4 - Prob. 11PCh. 12.5 - Prob. 12PCh. 12.5 - Prob. 13PCh. 12.5 - Prob. 14PCh. 12.5 - Prob. 15PCh. 12.5 - Prob. 16PCh. 12.5 - Prob. 17PCh. 12.5 - Prob. 18PCh. 12.5 - Prob. 19PCh. 12.5 - Prob. 20PCh. 12.5 - Prob. 21PCh. 12 - Prob. 27PCh. 12 - Prob. 28PCh. 12 - Prob. 29PCh. 12 - Prob. 30PCh. 12 - Prob. 31PCh. 12 - Prob. 32PCh. 12 - Prob. 33PCh. 12 - Prob. 34PCh. 12 - Prob. 35PCh. 12 - Prob. 36PCh. 12 - Prob. 38PCh. 12 - Prob. 39PCh. 12 - Prob. 40PCh. 12 - Prob. 42PCh. 12 - Prob. 43PCh. 12 - Prob. 44PCh. 12 - Prob. 45PCh. 12 - Prob. 46PCh. 12 - Prob. 47PCh. 12 - Prob. 48PCh. 12 - Prob. 49PCh. 12 - Prob. 53PCh. 12 - Prob. 54PCh. 12 - In terms of K, D, and h, what is the average...Ch. 12 - Prob. 56PCh. 12 - Prob. 57PCh. 12 - Prob. 58PCh. 12 - Prob. 59PCh. 12 - Prob. 60PCh. 12 - Prob. 61PCh. 12 - Prob. 62PCh. 12 - Prob. 63PCh. 12 - Prob. 64PCh. 12 - Prob. 65PCh. 12 - Prob. 66PCh. 12 - Prob. 67PCh. 12 - Prob. 68PCh. 12 - Prob. 69PCh. 12 - Prob. 70PCh. 12 - Prob. 71PCh. 12 - Prob. 1.1CCh. 12 - Prob. 1.2CCh. 12 - Prob. 1.3C
Knowledge Booster
Learn more about
Need a deep-dive on the concept behind this application? Look no further. Learn more about this topic, operations-management and related others by exploring similar questions and additional content below.Similar questions
- Identify the ethical principles that apply to the case. Include in your discussion how each of the principles of ethical decision making as discussed in the “Underlying Principles of Ethical Patient Care” chapter factored into your decision (beneficence, non-maleficence, autonomy, respect for dignity, veracity, and justice).arrow_forwardWhat should I do? Generate Potential Actions. Include choices that cannot be justified. What justifies my choice? Decide on proper ethical action and generate responses to those with opposing arguments (Justification for your choice)arrow_forwardin the 2016 "ATB: Digital Disruption in the parking meter industry" case what recommendations would you give to adress the key issues outlined in the case?arrow_forward
- 1) JIT McDonald’s Style (https://media.gaspar.mheducation.com/GASPARPlayer/play.html?id=46KGfedfilYlJzWH4XxxbLS) What challenges did McDonald’s face with its current operating system? 2. What are the five criteria that McDonald’s new “Made for You” operating system had to meet? 3. Describe how the “Made for You” operating system works.arrow_forwardThe first general topic debated in the SHRM Learning System centers around talent acquisition and retention. Discuss how talent is different from skills, and offer two strategies a human resources professional can pursue to recruit “talent” to an organization.arrow_forwardWhat assumptions or biases do you have related to the case? Gather the facts. Known and to be gathered. Identify the stakeholders and their viewpoints. Include the values, obligations and interests of each of the stakeholders. Primary Secondaryarrow_forward
- Perform an internal analysis using SWOT and VRIO analysis of the " ATB: Digital disruption in the parking meter industry" casearrow_forwardPerform a External analysis using PESTEL and Porters five force analysis on the "ATB: Digital disruption in the parking meter industry" casearrow_forwardThere was a most recent poll for which 571 adults that flew in the past year had info collected. This info was their number 1 complaints about flying. A - small cramped seat - 45 complaints B - cost - 18 complaints C - fear or dislike - 81 complaints D - security - 123 complaints E - Poor service - 12 complaints F - Conntected flight issue - 8 complaints G - overcrowded - 41 complaints H - Late and wait - 81 complaints I - Food - 5 complaints J - Lost/missing luggage - 5 complaints K - Other - 51 complaints What percentage of those surveyed found nothing they didnt dislike?arrow_forward
arrow_back_ios
SEE MORE QUESTIONS
arrow_forward_ios
Recommended textbooks for you
- Practical Management ScienceOperations ManagementISBN:9781337406659Author:WINSTON, Wayne L.Publisher:Cengage,Purchasing and Supply Chain ManagementOperations ManagementISBN:9781285869681Author:Robert M. Monczka, Robert B. Handfield, Larry C. Giunipero, James L. PattersonPublisher:Cengage Learning
- MarketingMarketingISBN:9780357033791Author:Pride, William MPublisher:South Western Educational Publishing
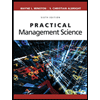
Practical Management Science
Operations Management
ISBN:9781337406659
Author:WINSTON, Wayne L.
Publisher:Cengage,
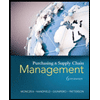
Purchasing and Supply Chain Management
Operations Management
ISBN:9781285869681
Author:Robert M. Monczka, Robert B. Handfield, Larry C. Giunipero, James L. Patterson
Publisher:Cengage Learning
Marketing
Marketing
ISBN:9780357033791
Author:Pride, William M
Publisher:South Western Educational Publishing