EBK PRACTICAL MANAGEMENT SCIENCE
5th Edition
ISBN: 9780100655065
Author: ALBRIGHT
Publisher: YUZU
expand_more
expand_more
format_list_bulleted
Concept explainers
Textbook Question
Chapter 12, Problem 55P
In terms of K, D, and h, what is the average length of time that an item spends in inventory before being used to meet demand? Explain how this result can be used to characterize a fast-moving or slow-moving item.
Expert Solution & Answer

Want to see the full answer?
Check out a sample textbook solution
Students have asked these similar questions
Cariveh Co sells automotive supplies from 25 different locations in one country. Each branch has up to 30 staff working there, although most of the accounting systems are designed and implemented from the company's head office. All accounting systems, apart from petty cash, are computerised, with the internal audit department frequently advising and implementing controls within those systems. Cariveh has an internal audit department of six staff, all of whom have been employed at Cariveh for a minimum of five years and some for as long as 15 years. In the past, the chief internal auditor appoints staff within the internal audit department, although the chief executive officer (CEO) is responsible for appointing the chief internal auditor. The chief internal auditor reports directly to the finance director. The finance director also assists the chief internal auditor in deciding on the scope of work of the internal audit department. You are an audit manager in the internal audit…
Cariveh Co sells automotive supplies from 25 different locations in one country. Each branch has up to 30 staff working there, although most of the accounting systems are designed and implemented from the company's head office. All accounting systems, apart from petty cash, are computerised, with the internal audit department frequently advising and implementing controls within those systems. Cariveh has an internal audit department of six staff, all of whom have been employed at Cariveh for a minimum of five years and some for as long as 15 years. In the past, the chief internal auditor appoints staff within the internal audit department, although the chief executive officer (CEO) is responsible for appointing the chief internal auditor. The chief internal auditor reports directly to the finance director. The finance director also assists the chief internal auditor in deciding on the scope of work of the internal audit department. You are an audit manager in the internal audit…
Please show all steps and answers, thank you!
Chapter 12 Solutions
EBK PRACTICAL MANAGEMENT SCIENCE
Ch. 12.4 - Prob. 1PCh. 12.4 - Prob. 2PCh. 12.4 - Prob. 3PCh. 12.4 - Prob. 4PCh. 12.4 - Prob. 5PCh. 12.4 - Prob. 6PCh. 12.4 - Prob. 7PCh. 12.4 - Prob. 8PCh. 12.4 - Prob. 9PCh. 12.4 - Prob. 10P
Ch. 12.4 - Prob. 11PCh. 12.5 - Prob. 12PCh. 12.5 - Prob. 13PCh. 12.5 - Prob. 14PCh. 12.5 - Prob. 15PCh. 12.5 - Prob. 16PCh. 12.5 - Prob. 17PCh. 12.5 - Prob. 18PCh. 12.5 - Prob. 19PCh. 12.5 - Prob. 20PCh. 12.5 - Prob. 21PCh. 12 - Prob. 27PCh. 12 - Prob. 28PCh. 12 - Prob. 29PCh. 12 - Prob. 30PCh. 12 - Prob. 31PCh. 12 - Prob. 32PCh. 12 - Prob. 33PCh. 12 - Prob. 34PCh. 12 - Prob. 35PCh. 12 - Prob. 36PCh. 12 - Prob. 38PCh. 12 - Prob. 39PCh. 12 - Prob. 40PCh. 12 - Prob. 42PCh. 12 - Prob. 43PCh. 12 - Prob. 44PCh. 12 - Prob. 45PCh. 12 - Prob. 46PCh. 12 - Prob. 47PCh. 12 - Prob. 48PCh. 12 - Prob. 49PCh. 12 - Prob. 53PCh. 12 - Prob. 54PCh. 12 - In terms of K, D, and h, what is the average...Ch. 12 - Prob. 56PCh. 12 - Prob. 57PCh. 12 - Prob. 58PCh. 12 - Prob. 59PCh. 12 - Prob. 60PCh. 12 - Prob. 61PCh. 12 - Prob. 62PCh. 12 - Prob. 63PCh. 12 - Prob. 64PCh. 12 - Prob. 65PCh. 12 - Prob. 66PCh. 12 - Prob. 67PCh. 12 - Prob. 68PCh. 12 - Prob. 69PCh. 12 - Prob. 70PCh. 12 - Prob. 71PCh. 12 - Prob. 1.1CCh. 12 - Prob. 1.2CCh. 12 - Prob. 1.3C
Knowledge Booster
Learn more about
Need a deep-dive on the concept behind this application? Look no further. Learn more about this topic, operations-management and related others by exploring similar questions and additional content below.Similar questions
- I am not sure if this is correct, because 8 cannot go directly to 10.arrow_forwardA practical application in real life to the Critical Path Method is the construction of a bridge with references, give a detailed essay on the stages involved in constructing a bridgearrow_forwardPlease assist in writing a complete reasearch project of the following title: Title of research: Study on the impact of Technology in the Work Place.arrow_forward
- Intuition is both an emotional experience and a nonconscious analytic process. One problem, however, is that not all emotions signaling that there is a problem or opportunity represent intuition. Please in your Personal opinion how we would know if our “gut feelings” are intuition or not, and if not intuition, suggest what might be causing them.arrow_forwardA coworker suggests that the company where you both work would be much more effective if there were no organizational politics. Please in your personal and detailed opinion, What would you say to this person in reply?arrow_forwardWhat is a bottleneck? Would you try to reduce a bottleneck? Why or why not? Please provide a referencearrow_forward
- Your firm has been the auditor of Caribild Products, a listed company, for a number of years. The engagement partner has asked you to describe the matters you would consider when planning the audit for the year ended 31January 2022. During recent visit to the company you obtained the following information: (a) The management accounts for the 10 months to 30 November 2021 show a revenue of $260 million and profit before tax of $8 million. Assume sales and profits accrue evenly throughout the year. In the year ended 31 January 2021 Caribild Products had sales of $220 million and profit before tax of $16 million. (b) The company installed a new computerised inventory control system which has operated from 1 June 2021. As the inventory control system records inventory movements and current inventory quantities, the company is proposing: (i) To use the inventory quantities on the computer to value the inventory at the year-end (ii) Not to carry out an inventory count at the year-end (c)…arrow_forwardDevelop and implement a complex and scientific project for an organisation of your choice. please include report include the following: Introduction Background research to the project The 5 basic phases in the project management process Project Initiation Project Planning Project Execution Project Monitoring and Controlling Project Closing Conclusionarrow_forwardNot use ai pleasearrow_forward
- Sam's Pet Hotel operates 51 weeks per year, 6 days per week, and uses a continuous review inventory system. It purchases kitty litter for $11.00 per bag. The following information is available about these bags: > Demand 95 bags/week > Order cost $52.00/order > Annual holding cost = 25 percent of cost > Desired cycle-service level = 80 percent >Lead time 4 weeks (24 working days) > Standard deviation of weekly demand = 15 bags > Current on-hand inventory is 320 bags, with no open orders or backorders. a. Suppose that the weekly demand forecast of 95 bags is incorrect and actual demand averages only 75 bags per week. How much higher will total costs be, owing to the distorted EOQ caused by this forecast error? The costs will be $ higher owing to the error in EOQ. (Enter your response rounded to two decimal places.)arrow_forwardSam's Pet Hotel operates 50 weeks per year, 6 days per week, and uses a continuous review inventory system. It purchases kitty litter for $10.50 per bag. The following information is available about these bags: > Demand = 95 bags/week > Order cost = $55.00/order > Annual holding cost = 35 percent of cost > Desired cycle-service level = 80 percent > Lead time = 4 weeks (24 working days) > Standard deviation of weekly demand = 15 bags > Current on-hand inventory is 320 bags, with no open orders or backorders. a. Suppose that the weekly demand forecast of 95 bags is incorrect and actual demand averages only 75 bags per week. How much higher will total costs be, owing to the distorted EOQ caused by this forecast error? The costs will be $ 10.64 higher owing to the error in EOQ. (Enter your response rounded to two decimal places.) b. Suppose that actual demand is 75 bags but that ordering costs are cut to only $13.00 by using the internet to automate order placing. However, the buyer does…arrow_forwardBUS-660 Topic 4: Intege... W Midterm Exam - BUS-66... webassign.net b Answered: The binding c... × W Topic 4 Assignment - BU... how to get more chegg... b My Questions | bartleby + macbook screenshot - G... C Consider the following m... As discussed in Section 8.3, the Markowitz model uses the variance of the portfolio as the measure of risk. However, variance includes deviations both below and above the mean return. Semivariance includes only deviations below the mean and is considered by many to be a better measure of risk. (a) Develop a model that minimizes semivariance for the Hauck Financial data given in the file HauckData with a required return of 10%. Assume that the five planning scenarios in the Hauck Financial Services model are equally likely to occur. Hint: Modify model (8.10)-(8.19). Define a variable d for each 5 - scenario and let d≥ Ŕ – R¸ with d¸ ≥ 0. Then make the objective function: Min 1 5 Σας Let Min s.t. 15 FS = proportion of portfolio invested in the foreign…arrow_forward
arrow_back_ios
SEE MORE QUESTIONS
arrow_forward_ios
Recommended textbooks for you
- Practical Management ScienceOperations ManagementISBN:9781337406659Author:WINSTON, Wayne L.Publisher:Cengage,Purchasing and Supply Chain ManagementOperations ManagementISBN:9781285869681Author:Robert M. Monczka, Robert B. Handfield, Larry C. Giunipero, James L. PattersonPublisher:Cengage Learning
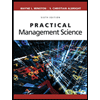
Practical Management Science
Operations Management
ISBN:9781337406659
Author:WINSTON, Wayne L.
Publisher:Cengage,
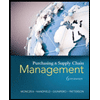
Purchasing and Supply Chain Management
Operations Management
ISBN:9781285869681
Author:Robert M. Monczka, Robert B. Handfield, Larry C. Giunipero, James L. Patterson
Publisher:Cengage Learning
Inventory Management | Concepts, Examples and Solved Problems; Author: Dr. Bharatendra Rai;https://www.youtube.com/watch?v=2n9NLZTIlz8;License: Standard YouTube License, CC-BY