Concept explainers
a)
To determine: The optimal order quantity with the minimum annual cost for purchasing the integrated chips.
Introduction:
Quantity discount model:
Quantity discount model is a scenario where manufacturing companies receive price discount for ordering large quantities. The firm will estimate if the discount quantity is profitable for the firm and make the decision.
Economic order quantity (EOQ):
EOQ is the quantity of units a company must add to its inventory so as to minimize the total inventory costs. It will determine the ideal order quantity which will decrease the inventory management costs.
Annual holding cost:
Annual holding cost is the cost involved in holding the excess inventory present within a firm. The excess inventory will be carried on for the next year and used for production.
Annual ordering cost:
Annual ordering cost is the cost involved in making a purchase order and the following up of that order. It will account for the labor involved and other associated costs.
Purchase cost:
Purchase cost is the cost incurred to purchase the require components to satisfy the demand of the firm. The cost will vary according to the demand.
Total cost:
Total cost is the overall cost taking into estimation of the holding, ordering and the purchase cost of the materials.
a)

Answer to Problem 22P
The optimal order quantity is 200 units with the minimum annual cost of $1,446,380
Explanation of Solution
Given information:
Monthly demand (d)= 400 / month
Holding cost (H) = $35 / unit / year
Ordering cost (S) = $120 / order
Purchase price (P) = $350 / chip
Price structure:
Quantity purchased | Price / unit |
1 – 99 units | $350 |
100 – 199 units | $325 |
200 or more units | $300 |
Formula to calculate EOQ:
Formula to calculate annual holding cost:
Formula to calculate annual ordering cost:
Formula to calculate purchase cost:
Formula to calculate total cost:
Calculation of EOQ:
The obtained EOQ value is in the range of (100 – 199 units). Hence, the price of that range will be used for calculation.
Calculation of values at (EOQ = 181):
Calculation of annual holding cost at (EOQ = 181):
Calculation of annual ordering cost at (EOQ = 181):
Calculation of purchase cost:
Calculation of total cost at (EOQ = 181):
The total cost at the (EOQ = 181) is $1,566,350.
Calculation of values at discount quantity (200):
The next price break after the EOQ at 181 units is (200 or more units). The price of that range will be used in the following calculation.
Calculation of annual holding cost at (EOQ = 200):
Calculation of annual ordering cost at (EOQ = 200):
Calculation of purchase cost:
Calculation of total cost at (EOQ = 200):
The total cost at the (EOQ = 200) is $1,446,380
Calculation of difference in cost:
The total cost at (EOQ = 181) is $1,566,350. The total cost at (EOQ = 200) is $1,446,380. Therefore (EOQ = 200) has lesser cost ($1,446,380 < 1,566,350).
Hence, the optimal order quantity is 200 units with the minimum annual cost of $1,446,380
b)
To determine: The optimal order quantity with the minimum annual cost for purchasing the integrated chips.
b)

Answer to Problem 22P
The optimal order quantity is 200 units with the minimum annual cost of $1,445,880
Explanation of Solution
Given information:
Monthly demand (d)= 400 / month
Holding cost (H) = 10 % of purchase price of the price structure
Ordering cost (S) = $120 / order
Purchase price (P) = $350 / chip
Price structure:
Quantity purchased | Price / unit |
1 – 99 units | $350 |
100 – 199 units | $325 |
200 or more units | $300 |
Formula to calculate EOQ:
Formula to calculate annual holding cost:
Formula to calculate annual ordering cost:
Formula to calculate purchase cost:
Formula to calculate total cost:
Calculation of EOQ at each price structure:
EOQ at price = $350
EOQ at price = $325
EOQ at price = $300
EOQ = 181, cannot be bought at the price of $350. EOQ = 196 cannot be bought at the price of $300.
Hence, the EOQ is 188 units.
The obtained EOQ value is in the range of (100 – 199 units). Hence, the price of that range will be used for calculation.
Calculation of values at (EOQ = 188):
Calculation of annual holding cost at (EOQ = 188):
Calculation of annual ordering cost at (EOQ = 188):
Calculation of purchase cost:
Calculation of total cost at (EOQ = 188):
The total cost at the (EOQ = 188) is $1,566,319.
Calculation of values at discount quantity (200):
The next price break after the EOQ at 188 units is (200 or more units). The price of that range will be used in the following calculation.
Calculation of annual holding cost at (EOQ = 200):
Calculation of annual ordering cost at (EOQ = 200):
Calculation of purchase cost:
Calculation of total cost at (EOQ = 200):
The total cost at the (EOQ = 200) is $1,445,880
Calculation of difference in cost:
The total cost at (EOQ = 188) is $1,566,319. The total cost at (EOQ = 200) is $1,445,880. Therefore (EOQ = 200) has lesser cost ($1,445,880 < 1,566,319).
Hence, the optimal order quantity is 200 units with the minimum annual cost of $1,445,880.
Want to see more full solutions like this?
Chapter 12 Solutions
PRIN.OF OPERATIONS MANAGEMENT-MYOMLAB
- Bobby Flay is responsible for assigning steel workers to a structural steel infrastructure construction task. Having taken Project Management at the University of Portland, he understands the importance of managing risk. To ensure that the task takes place as scheduled, Bobby must ensure that there are at least 8 steel workers available at the start of the task. Based on analysis of similar tasks, he estimates that steel workers will show up for the task with probability 0.9. If Bobby wants to be 97% sure that there are enough tasks to begin as scheduled, he should assign ______ steel workers to the task.arrow_forwardMarcela Valladolid needs to assign resources to a task on a new high-tech development project at Jonathon's Pool Supplies. According to her estimates, the task's work content (in hours) is 408. Marcela needs help in determining an appropriate number of resources to allocate to the task. Marcela read somewhere that, when it comes to project staffing, more is not always better. Assuming that the direct labor rate per hour is $93, the indirect and over head rate per unit time is $73.62, assigned resources are dedicated to the task full time, and that 0.02 hours of communication per coordination are required per link per hour worked, help Marcela by determining the following: What is the minimum total cost: What resource allocation minimizes the total cost: What is the minimum duration: What is the duration minimizing number of resources: If Marcela assigns 12 FTEs to the task, the task metrics would be: Total Cost: Total Duration: Note: enter durations to 1 decimal place and costs…arrow_forward1 point) Market Fresh Foods is looking to develop a new strategic plan. Guillermo Santiago has been developing a project plan and has identified the following tasks, precedence relations, normal task durations, and resource requirements. Guillermo has studied project management at the University of Portland and knows that the makespan of the project may be determined from the information in the table using the critical path method. Guillermo also learned a simple heuristic for evaluating resource sufficiency. Help Guillermo by answering the following related assuming 3 workers per week and a due date of 302.8: Project Work Content: Total Resource Capacity: Minimum due date for which 3 resources is sufficient: Minimum resource level that could make due date of 302.8 feasible:arrow_forward
- How an individual attending a university can help the development of a country?arrow_forwardWhat are the job description or role in Operations management? Please answer at your own easy words.arrow_forwardI am currently working as a Sub Assistant Manager at Advance Personal Care Limited (APCL), a concern of Pran Group. I hold a Bachelor of Pharmacy (Professional) degree. I recently came across a job posting on BD Jobs for a position in Project Management within Quality Operations. I want to apply for this role and need to update my CV accordingly. Could you please guide me on what key information, achievements, and skills I should add or highlight in my CV to align with this new role? Note that i have 8 months experience on this role. Please write at your own easy words. Please don't use Ai answering this question. I will rate you positive if you do so.arrow_forward
- I am currently working as a Sub Assistant Manager at Advance Personal Care Limited (APCL), a concern of Pran Group. I hold a Bachelor of Pharmacy (Professional) degree. I recently came across a job posting on BD Jobs for a position in Project Management within Quality Operations. I want to apply for this role and need to update my CV accordingly. Could you please guide me on what key information, achievements, and skills I should add or highlight in my CV to align with this new role? Note that i have 8 months experience on this role. Please don't use Ai answering this question. I will rate you positive if you do so.arrow_forwardWhat are the three main concepts of understanding in Operations Management?arrow_forwardNeed help please not sure where to start or how to write it.arrow_forward
- Need help please not sure where to start or how to write it.arrow_forwardSIPOC Process Supplier Machines Quality Group Leader Double Output Customers Inputs Solutions End of batch Inspection verification Scrap evaluation Sampling Verification Batch complete Evaluation Completed Quality Group Leader Samplings verified Quality Samplings verified Quality Barcode programed Mechanic Parameters registered Quality Line verified Quality Line Verified Quality Second verification Barcode Parameters Line Inspection Second Line Inspection Lot and Expiration Date Quality Quality Mechanic Mechanic Quality Machines Quality Group Leader Quality Quality Quality Batch Verification Process complete Revision Review Sampling Verification Barcode Scanner Machine Parameters Line Clearance Line Clearance Machine Remove Lot Status Verification Close floor Final MFG Review Final QA Review Close Batch Machine removed Lot verified Floor closed MFG Reviewed Process reviewed Batch closed Mechanic Group Leader Quality Quality Quality Group Leaderarrow_forwardAn assessment of gender leadership and corporate culture.Kindly provide the following, citing it using in-text referencing: • A thorough exploration of gender dynamics and concepts.• Creating a clear plan to address gender bias and promote inclusive leadership.• An examination of female leadership dynamics and their impact on performance. • Comprehensive justification behind the proposal.arrow_forward
- Purchasing and Supply Chain ManagementOperations ManagementISBN:9781285869681Author:Robert M. Monczka, Robert B. Handfield, Larry C. Giunipero, James L. PattersonPublisher:Cengage LearningPractical Management ScienceOperations ManagementISBN:9781337406659Author:WINSTON, Wayne L.Publisher:Cengage,
- Contemporary MarketingMarketingISBN:9780357033777Author:Louis E. Boone, David L. KurtzPublisher:Cengage LearningMarketingMarketingISBN:9780357033791Author:Pride, William MPublisher:South Western Educational Publishing
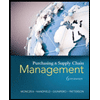
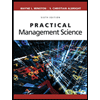
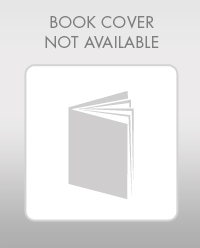