Concept explainers
a)
To determine: The number of tires Company RMT should order each time it places an order.
Introduction: Inventory management is the process of ordering, storing and using inventory of the company such raw material, components and finished goods. It governs the flow of goods from manufacturers to warehouse and to the point of sale. The key function is to maintain record of flow of new or returned products which enters or leaves the company.
a)

Answer to Problem 25P
The number of tires Company RMT should order each time it places an order is 667.
Explanation of Solution
Given information:
Formula:
Where
Calculation of optimal order quantity:
Calculation of EOQ for orders less than 500 tires:
EOQ for order less than 500 tires is calculated by multiplying 2, 20,000 and 40 and dividing the resultant with the product of 0.2 and 20 and taking square root which gives 632.5 tires.
Calculation of EOQ for orders between 500 to 999 tires:
EOQ for order between 500 to 999 tires is calculated by multiplying 2, 20,000 and 40 and dividing the resultant with the product of 0.2 and 18 and taking square root which gives 667 tires.
Calculation of EOQ for orders more than 1,000 tires:
EOQ for order orders more than 1,000 tires is calculated by multiplying 2, 20,000 and 40 and dividing the resultant with the product of 0.2 and 17 and taking square root which gives 686 tires.
Based on the above calculations, EOQ of orders between 500 to 999 tires gives optimal order quantity as the EOQ lies within the quantities ordered. Therefore the optimal order quantity is 667 tires at $0.18.
Hence, the number of tires Company RMT should order each time it places an order is 667.
b)
To determine: The total annual cost of the policy.
b)

Answer to Problem 25P
The total annual cost of the policy is $342,500 per year.
Explanation of Solution
Given information:
Formula:
Calculation of total annual cost:
The total annual cost for ordering quantity 667 tires is compared with 1000 tires to find the optimal total cost and quantities to be ordered by the company.
Total annual cost for 667 tires:
Total annual cost is calculated by adding holding cost, ordering cost and unit cost and the values are substituted in the above formula which yields $362,400 as total cost per year.
The total annual cost for 667 ordering quantity is $362,400/year.
Total annual cost for 1000 tires:
Total annual cost is calculated by adding holding cost, ordering cost and unit cost and the values are substituted in the above formula which yields $342,500 as total cost per year.
The total annual cost for 1000 tires is $342,500/year.
The total annual cost for 1000 tires is lesser than total annual cost for 667 tires and so company RMT should order 1,000 tires each time.
Hence, the total annual cost of the policy is $342,500 per year.
Want to see more full solutions like this?
Chapter 12 Solutions
PRIN.OF OPERATIONS MANAGEMENT-MYOMLAB
- PepsiCo South Africa says the incident where a woman discovered part of a rodent in her loaf of bread, is anisolated occurrence.Durban woman, Nombulelo Mkumla, took to social media last week to share how she discovered the rodent.In a lengthy Facebook post, she said she purchased the loaf of bread from a local shop after work on August 27.For the next days, Mkumla proceeded to use slices of bread from the load to make toast."Then, on the morning of August 31, I took the bread out of the fridge to make toast and noticed something disgusting andscary. I took a picture and sent it to my friends, and one of them said, 'Yi mpuku leyo tshomi' [That's a rat friend]“."I was in denial and suggested it might be something else, but the rat scenario made sense - it's possible the rat got into thebread at the factory, and no one noticed," Mkumla said.She went back to the shop she'd bought the bread from and was told to lay a complaint directly with the supplier.She sent an email with a video and…arrow_forwardThe deaths are included in the discharges; this includes deaths occurring in less than 48 hours and postoperative deaths. Rehabilitation had 362 discharges, 22 deaths, 1<48 hours, 0 Postoperative. what is the gross death rate for the rehabilitation service?arrow_forwardA copy machine is available 24 hours a day. On a typical day, the machine produces 100 jobs. Each job takes about 3 minutes on the machine, 2 minutes of which is processing time and 1 minute is setup time (logging in, defining the job). About 20 percent of the jobs need to be reworked, in which case the setup time and the processing time have to be repeated. The remainder of the time, the equipment is idle. What is the OEE of the equipment?arrow_forward
- How do you think we can keep updating Toyota's ideas as new technologies come out and what customers want keeps changing?arrow_forwardGiven how TPS has helped change things in so many fields, do you think there are parts of it that might be hard to use in areas that aren’t about making things, like in healthcare or services? If so, why do you think that might be?arrow_forwardDo you feel there is anything positive about rework?arrow_forward
- Do you think technology can achieve faster setup times? How would it be implemented in the hospital workforce?arrow_forwardIn your experience or opinion, do you think process changes like organizing workspaces make a bigger difference, or is investing in technology usually the better solution for faster setups?arrow_forwardHave you seen rework done in your business, and what was done to prevent that from occurring again?arrow_forward
- Research a company different than case studies examined and search the internet and find an example of a business that had to rework a process. How was the organization affected to rework a process in order to restore a good flow unit? Did rework hurt a process or improve the organization's operational efficiency? • Note: Include a reference with supportive citations in the discussion reply in your post.arrow_forwardSetup time is very important in affecting a process and the capacity of a process. How do you reduce setup time? Give examples of reducing setup time. Please Provide a referenecearrow_forwardDo you think TPS was successful? If so, how? Are there other companies that have used TPS? If so, give examples. Please provide a referencearrow_forward
- Purchasing and Supply Chain ManagementOperations ManagementISBN:9781285869681Author:Robert M. Monczka, Robert B. Handfield, Larry C. Giunipero, James L. PattersonPublisher:Cengage LearningPractical Management ScienceOperations ManagementISBN:9781337406659Author:WINSTON, Wayne L.Publisher:Cengage,
- MarketingMarketingISBN:9780357033791Author:Pride, William MPublisher:South Western Educational Publishing
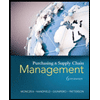
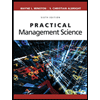