Throughput contribution. Auburn Foods produces frozen meals aimed at the college student market. The production takes place in four stages: Preparation, in which the food is cleaned and cut; Cooking; Freezing; and Packaging. The company has a bottleneck in the Preparation stage, as shown below. Each ‘‘unit’’ refers to a container of 144 frozen meals. Preparation Cooking Freezing Packaging Hourly Capacity Actual Hourly Production 300 Units 300 Units 312 Units 300 Units 320 Units 300 Units 340 Units 300 Units Each unit sells for $200 and has a variable cost of $120. Option a. Auburn can increase Preparation output by renting additional equipment that would cost $200 per hour and increase the hourly capacity in Preparation by 5 units. Option b. Auburn can pay its suppliers to perform some of the food preparation. This option would cost Auburn $2 more per unit and would enable the company to increase its hourly output in Preparation by 10 units. Auburn can take either or both options as presented. If both options are taken, the cost increase in Option b would apply to 310 units. What do you recommend?
Master Budget
A master budget can be defined as an estimation of the revenue earned or expenses incurred over a specified period of time in the future and it is generally prepared on a periodic basis which can be either monthly, quarterly, half-yearly, or annually. It helps a business, an organization, or even an individual to manage the money effectively. A budget also helps in monitoring the performance of the people in the organization and helps in better decision-making.
Sales Budget and Selling
A budget is a financial plan designed by an undertaking for a definite period in future which acts as a major contributor towards enhancing the financial success of the business undertaking. The budget generally takes into account both current and future income and expenses.
53. Throughput contribution. Auburn Foods produces frozen meals aimed at the college student market. The production takes place in four stages: Preparation, in which the food is cleaned and cut; Cooking; Freezing; and Packaging. The company has a bottleneck in the Preparation stage, as shown below. Each ‘‘unit’’ refers to a container of 144 frozen meals.
| Preparation | Cooking | Freezing | Packaging |
Hourly Capacity Actual Hourly Production | 300 Units 300 Units | 312 Units 300 Units | 320 Units 300 Units | 340 Units 300 Units |
Each unit sells for $200 and has a variable cost of $120.
Option a. Auburn can increase Preparation output by renting additional equipment that would cost $200 per hour and increase the hourly capacity in Preparation by 5 units.
Option b. Auburn can pay its suppliers to perform some of the food preparation. This option would cost Auburn $2 more per unit and would enable the company to increase its hourly output in Preparation by 10 units.
Auburn can take either or both options as presented. If both options are taken, the cost increase in Option b would apply to 310 units. What do you recommend?

Step by step
Solved in 3 steps with 6 images

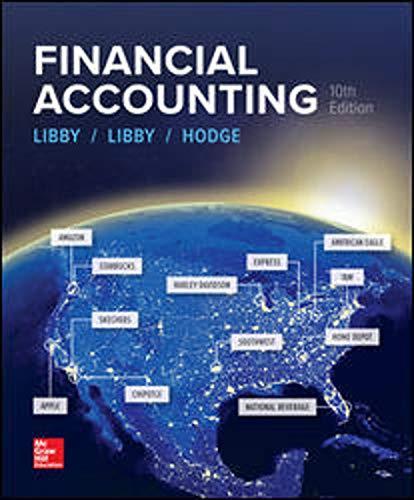
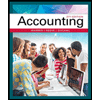
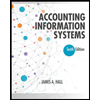
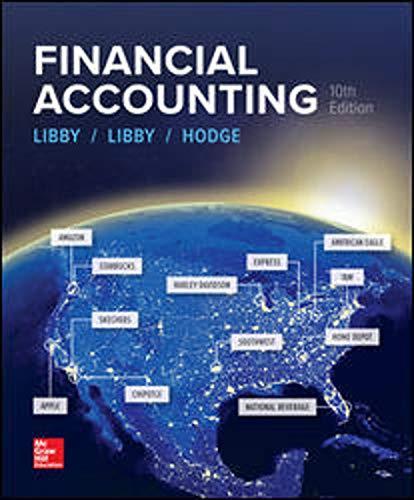
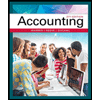
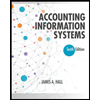
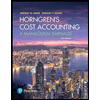
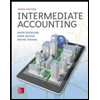
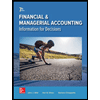