Laredo Leather Company manufactures high-quality leather goods. The company’s profits have declined during the past nine months. In an attempt to isolate the causes of poor profit performance, management is investigating the manufacturing operations of each of its products. One of the company’s main products is leather belts. The belts are produced in a single, continuous process in the Dallas plant. During the process, leather strips are sewn, punched, and dyed. The belts then enter a final finishing stage to conclude the process. Labor and overhead are applied continuously during the manufacturing process. All materials, leather strips, and buckles are introduced at the beginning of the process. The firm uses the weighted-average method to calculate its unit costs. The leather belts produced at the Dallas plant are sold wholesale for $9.95 each. Management wants to compare the current manufacturing costs per unit with the market prices for leather belts. Top management has asked the Dallas plant controller to submit data on the cost of manufacturing the leather belts for the month of October. These cost data will be used to determine whether modifications in the production process should be initiated or whether an increase in the selling price of the belts is justified. The cost per belt used for planning and control is $5.35. The work-in-process inventory consisted of 400 partially completed units on October 1. The belts were 25 percent complete as to conversion. The costs included in the inventory on October 1 were as follows: Leather strips…………………..$ 990 Buckles……………………………260 Conversion costs…………………..300 Total……………………………$1,550 During October 7,600 leather strips were placed into production. A total of 7,000 leather belts were completed. The work-in-process inventory on October 31 consisted of 1,000 belts, which were 50 percent complete as to conversion. The costs charged to production during October were as follows: Leather strips………………….$19,900 Buckles …………………………..5,250 Conversion costs………………..20,700 Total…………………………...$45,850 Required: In order to provide cost data regarding the manufacture of leather belts in the Dallas Plant to the top management of Laredo Leather Company, compute the following amounts for the month of October. Laredo Leather Company’s production manager, Jack Murray, has been under pressure from the company president to reduce the cost of conversion. In spite of several attempts to reduce conversion costs, they have remained more or less constant. Now Murray is faced with an upcoming meeting with the company president, at which he will have to explain why he has failed to reduce conversion costs. Murray has approached his friend, Jeff Daley, who is the corporate controller, with the following request: “Jeff, I’m under pressure to reduce costs in the production process. There is no way to reduce material cost, so I’ve got to get the conversion costs down. If I can show just a little progress in next week’s meeting with the president, then I can buy a little time to try some other cost-cutting measures I’ve been considering. I want you to do me a favor. If we raise the estimate of the percentage of completion of October’s inventory to 60 percent, that will increase the number of equivalent units. Then the unit conversion cost will be a little lower.” By how much would Murray’s suggested manipulation lower the unit conversion cost? What should Daley do? Discuss this situation, citing specific ethical standards for managerial accountants.
Laredo Leather Company manufactures high-quality leather goods. The company’s profits have declined during the past nine months. In an attempt to isolate the causes of poor profit performance, management is investigating the manufacturing operations of each of its products.
One of the company’s main products is leather belts. The belts are produced in a single, continuous process in the Dallas plant. During the process, leather strips are sewn, punched, and dyed. The belts then enter a final finishing stage to conclude the process. Labor and
The leather belts produced at the Dallas plant are sold wholesale for $9.95 each. Management wants to compare the current
The work-in-process inventory consisted of 400 partially completed units on October 1. The belts were 25 percent complete as to conversion. The costs included in the inventory on October 1 were as follows:
Leather strips…………………..$ 990
Buckles……………………………260
Conversion costs…………………..300
Total……………………………$1,550
During October 7,600 leather strips were placed into production. A total of 7,000 leather belts were completed. The work-in-process inventory on October 31 consisted of 1,000 belts, which were 50 percent complete as to conversion.
The costs charged to production during October were as follows:
Leather strips………………….$19,900
Buckles …………………………..5,250
Conversion costs………………..20,700
Total…………………………...$45,850
Required: In order to provide cost data regarding the manufacture of leather belts in the Dallas Plant to the top management of Laredo Leather Company, compute the following amounts for the month of October.
- Laredo Leather Company’s production manager, Jack Murray, has been under pressure from the company president to reduce the cost of conversion. In spite of several attempts to reduce conversion costs, they have remained more or less constant. Now Murray is faced with an upcoming meeting with the company president, at which he will have to explain why he has failed to reduce conversion costs. Murray has approached his friend, Jeff Daley, who is the corporate controller, with the following request: “Jeff, I’m under pressure to reduce costs in the production process. There is no way to reduce material cost, so I’ve got to get the conversion costs down. If I can show just a little progress in next week’s meeting with the president, then I can buy a little time to try some other cost-cutting measures I’ve been considering. I want you to do me a favor. If we raise the estimate of the percentage of completion of October’s inventory to 60 percent, that will increase the number of equivalent units. Then the unit conversion cost will be a little lower.” By how much would Murray’s suggested manipulation lower the unit conversion cost? What should Daley do? Discuss this situation, citing specific ethical standards for managerial accountants.

Trending now
This is a popular solution!
Step by step
Solved in 2 steps

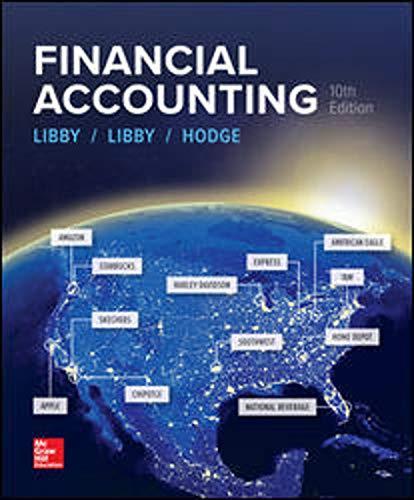
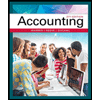
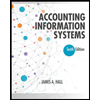
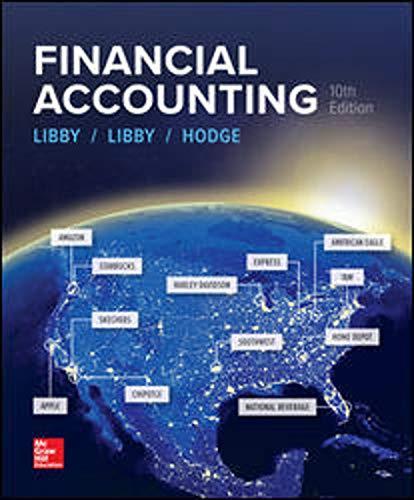
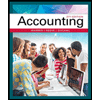
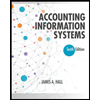
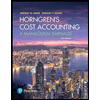
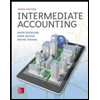
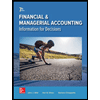