Jacaranda Builders is undertaking an analysis of supplier costs in order to evaluate the relative costs and performance of each supplier. They have isolated a range of activities that are consumed by suppliers, identified activity drivers, and estimated the cost per unit of activity driver for last year: Activity Cost per unit of activity driver Downtime due to poor quality material $200 per unit reworked Order material $250 per order Receive order $180 per delivery Inspect order $300 per delivery Return material to supplier $220 per return Pay supplier $190 per invoice Dispute invoiced amount $560 per dispute The three major suppliers to the company consumed the following numbers of activities: Activity Possum Timber Wombat Plumbing Emu Insulation Units reworked 10 Order material 40 48 30 Receive order 40 60 38 Inspect order 40 60 38 Return material to supplier 5 4 15 Pay supplier 12 48 12 Dispute invoiced amount 13 In addition, a supplier relationship manager (salary $90 000) was employed. It is estimated that 60 per cent of his time was spent serving Wombat Plumbing, and 40 per cent on the other two suppliers. The cost of material purchased from each supplier was as follows: Page 746 Possum Timber $120 000 Wombat Plumbing $150 000 Emu Insulation S 74 000 Required: 1. Calculate the total cost of ownership for each of the three suppliers, using a format similar to that shown in Exhibit 15.3 0. 2. Determine the supplier performance index for each supplier.
Process Costing
Process costing is a sort of operation costing which is employed to determine the value of a product at each process or stage of producing process, applicable where goods produced from a series of continuous operations or procedure.
Job Costing
Job costing is adhesive costs of each and every job involved in the production processes. It is an accounting measure. It is a method which determines the cost of specific jobs, which are performed according to the consumer’s specifications. Job costing is possible only in businesses where the production is done as per the customer’s requirement. For example, some customers order to manufacture furniture as per their needs.
ABC Costing
Cost Accounting is a form of managerial accounting that helps the company in assessing the total variable cost so as to compute the cost of production. Cost accounting is generally used by the management so as to ensure better decision-making. In comparison to financial accounting, cost accounting has to follow a set standard ad can be used flexibly by the management as per their needs. The types of Cost Accounting include – Lean Accounting, Standard Costing, Marginal Costing and Activity Based Costing.


Step by step
Solved in 5 steps

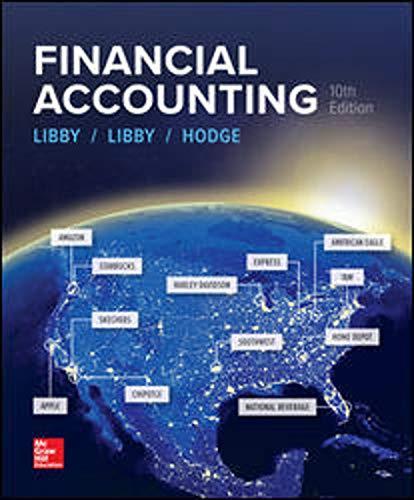
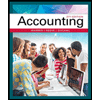
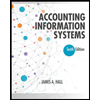
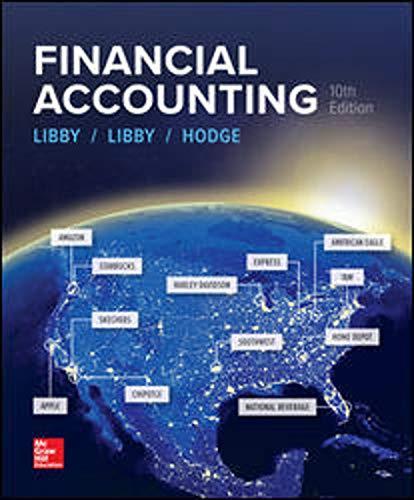
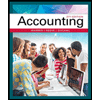
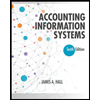
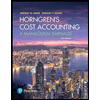
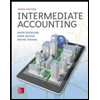
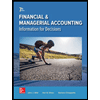