Evaluate, using language that is technically correct and of a high standard, the results from safely conducted and accurate checks and tests to establish how components failed in service, recommending a design solution from a range of alternatives. Figure 1 The 220mm-long bolt was used to fasten one of the engine mount to a supporting structure. In an effort to prevent the bolt from coming loose, the torque-prevailing nut and split pin were utilized to tighten the bolt. The bolt held through an aluminum housing. Due to the reduced stiffness of the fastened parts, the bolt supported a greater proportion of the applied force. The bolt's size necessitated a high tightening torque of 660 Nm (487 Lbft). Since this level of torque could not be achieved with the tools at the time, this torque was not specified. The aluminum's maximum bearing pressure was far exceeded by the bearing stress under the nut's head and face. As a result, there was excessive preload loss due to creep. fan shaft First of all, the fan shaft was required to be made of cold-drawn 1040 or 1045 steel with a yield strength of 586 MPa and the expected life is 6440km. After analyzing the picture of figure 2 b I came to the conclusion that the bolt started failing and cracking from the side suggesting that the bolt its being wobbling about. Looking at figure 2a I noticed the bolt is bent at the end so that means they probably using the wrong material or maybe the materials wasn’t cold-drawn, how it is supposed to be.
Evaluate, using language that is technically correct and of a high standard, the results from safely conducted and accurate checks and tests to establish how components failed in service, recommending a design solution from a range of alternatives.
Figure 1
The 220mm-long bolt was used to fasten one of the engine mount to a supporting structure. In an effort to prevent the bolt from coming loose, the torque-prevailing nut and split pin were utilized to tighten the bolt.
The bolt held through an aluminum housing. Due to the reduced stiffness of the fastened parts, the bolt supported a greater proportion of the applied force.
The bolt's size necessitated a high tightening torque of 660 Nm (487 Lbft). Since this level of torque could not be achieved with the tools at the time, this torque was not specified.
The aluminum's maximum bearing pressure was far exceeded by the bearing stress under the nut's head and face. As a result, there was excessive preload loss due to creep.
fan shaft
First of all, the fan shaft was required to be made of cold-drawn 1040 or 1045 steel with a yield strength of 586 MPa and the expected life is 6440km.
After analyzing the picture of figure 2 b I came to the conclusion that the bolt started failing and cracking from the side suggesting that the bolt its being wobbling about.
Looking at figure 2a I noticed the bolt is bent at the end so that means they probably using the wrong material or maybe the materials wasn’t cold-drawn, how it is supposed to be.



Step by step
Solved in 6 steps

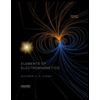
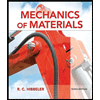
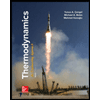
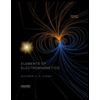
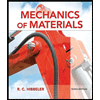
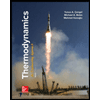
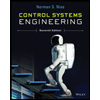
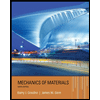
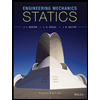