Berrian Company manufactures car seats in its Tulsa plant. Each car seat passes through the assembly department and the testing department. This problem focuses on the assembly department. Data for the assembly department for October 2017 are as follows: Read the requirements3. Requirement 1. For each cost category, compute equivalent units in the assembly department. Show physical units in the first column of your schedule. Equivalent Units Physical Direct Conversion Flow of Production Units Materials Costs Work in process beginning Started during current period To account for Completed and transferred out during current period Work in process, ending Accounted for Work done to date Requirement 2. What issues should the manager focus on when reviewing the equivalent-unit calculations? To show better performance, a department supervisor might report a (1) degree of completion resulting in (2) cost per equivalent unit and (3) operating income. In other words, estimates of degree of completion can help (4) (5) managers should ask supervisors specific questions about the process they followed. Top management should always emphasize (6) This emphasis drives (7) throughout the organization. Requirement 3. For each cost category, summarize total assembly department costs for October 2017 and calculate the cost per equivalent unit. Begin by summarizing the total assembly department costs for October 2017. Total Direct Conversion Production Costs Materials Costs (8) (9) Total costs to account for Now calculate the cost per equivalent unit for each cost category. Direct Conversion Materials Costs (10) Divide by (11) Cost per equivalent unit Requirement 4. Assign costs to units completed and transferred out and to units in ending work in process. Total Direct Conversion Production Costs Materials Costs Completed and transferred out Work in process, ending Total costs accounted for 1: More Info The process-costing system at Berrian Company has a single direct-cost category (direct materials) and a single indirect-cost category (conversion costs). Direct materials are added at the beginning of the process. Conversion costs are added evenly during the process. When the assembly department finishes work on each car seat, it is immediately transferred to testing. Berrian Company uses the weighted-average method of process costing. 2: Data Table Physical Units Direct Conversion (Car Seats) Materials Costs Work in process, October 1a 5,100 $1,489,200 $684,675 Started during October 2017 19,500 Completed during October 2017 22,500 Work in process, October 31b 2,100 Total costs added during October 2017 $4,095,000 $1,891,350 aDegree of completion: direct materials, ?%; conversion costs, 60%. bDegree of completion: direct materials, ?%; conversion costs, 75%. 3: Requirements 1. For each cost category, compute equivalent units in the assembly department. Show physical units in the first column of your schedule. 2. What issues should the manager focus on when reviewing the equivalent-unit calculations? 3. For each cost category, summarize total assembly department costs for October 2017 and calculate the cost per equivalent unit. 4. Assign costs to units completed and transferred out and to units in ending work in process.
Process Costing
Process costing is a sort of operation costing which is employed to determine the value of a product at each process or stage of producing process, applicable where goods produced from a series of continuous operations or procedure.
Job Costing
Job costing is adhesive costs of each and every job involved in the production processes. It is an accounting measure. It is a method which determines the cost of specific jobs, which are performed according to the consumer’s specifications. Job costing is possible only in businesses where the production is done as per the customer’s requirement. For example, some customers order to manufacture furniture as per their needs.
ABC Costing
Cost Accounting is a form of managerial accounting that helps the company in assessing the total variable cost so as to compute the cost of production. Cost accounting is generally used by the management so as to ensure better decision-making. In comparison to financial accounting, cost accounting has to follow a set standard ad can be used flexibly by the management as per their needs. The types of Cost Accounting include – Lean Accounting, Standard Costing, Marginal Costing and Activity Based Costing.
|
|
Equivalent Units
|
|
|
Physical
|
Direct
|
Conversion
|
Flow of Production
|
Units
|
Materials
|
Costs
|
Work in process beginning
|
|
||
Started during current period
|
|
||
To account for
|
|
||
Completed and transferred out during current period
|
|
|
|
Work in process, ending
|
|
|
|
Accounted for
|
|
|
|
Work done to date
|
|
|
Total
|
Direct
|
Conversion
|
||
|
|
Production Costs
|
Materials
|
Costs
|
(8)
|
|
|
|
|
(9)
|
|
|
|
|
Total costs to account for
|
|
|
|
Direct
|
Conversion
|
||
|
|
Materials
|
Costs
|
(10)
|
|
|
|
Divide by
|
(11)
|
|
|
Cost per equivalent unit
|
|
|
Total
|
Direct
|
Conversion
|
||
|
|
Production Costs
|
Materials
|
Costs
|
Completed and transferred out
|
|
|
|
|
Work in process, ending
|
|
|
|
|
Total costs accounted for
|
|
|
|
|
Physical Units
|
Direct
|
Conversion
|
|
(Car Seats)
|
Materials
|
Costs
|
Work in process, October 1a
|
5,100
|
$1,489,200
|
$684,675
|
Started during October 2017
|
19,500
|
|
|
Completed during October 2017
|
22,500
|
|
|
Work in process, October 31b
|
2,100
|
|
|
Total costs added during October 2017
|
|
$4,095,000
|
$1,891,350
|
1.
|
For each cost category, compute equivalent units in the assembly department. Show physical units in the first column of your schedule.
|
2.
|
What issues should the manager focus on when reviewing the equivalent-unit calculations?
|
3.
|
For each cost category, summarize total assembly department costs for October
2017
and calculate the cost per equivalent unit. |
4.
|
Assign costs to units completed and transferred out and to units in ending work in process.
|

Trending now
This is a popular solution!
Step by step
Solved in 3 steps with 3 images

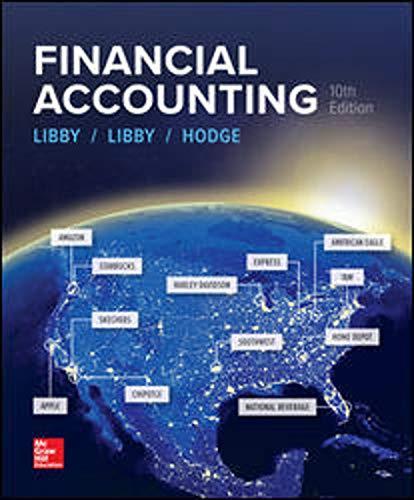
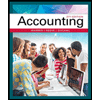
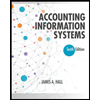
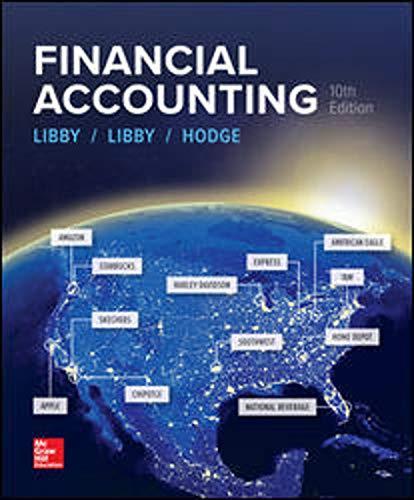
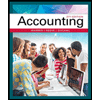
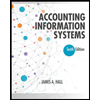
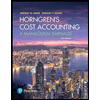
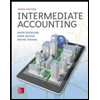
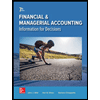