At the end of 20x1, Mejorar Company implemented a low-cost strategy to improve its competitive position. Its objective was to become the low-cost producer in its industry. A Balanced Scorecard was developed to guide the company toward this objective. To lower costs, Mejorar undertook a number of improvement activities such as JIT production, total quality management, and activity-based management. Now, after two years of operation, the president of Mejorar wants some assessment of the achievements. To help provide this assessment, the following information on one product has been gathered: 20x1 20x3 Theoretical annual capacity* 249,600 249,600 Actual production** 208,000 234,000 Market size (in units sold) 1,300,000 1,300,000 Production hours available (40 workers) 104,000 104,000 Very satisfied customers 62,400 117,000 Actual cost per unit $340 $272 Days of inventory 14 7 Number of defective units 12,480 7,020 Total worker suggestions 80 320 Hours of training 260 1,040 Selling price per unit $190 $190 Number of new customers 5,200 25,740 *Amount that could be produced given the available production hours; everything produced is sold. **Amount that was produced given the available production hours. Required: j. Total revenue. 20x1 $fill in the blank 20x3 $fill in the blank k. Number of new customers. 20x1 fill in the blank 20x3 fill in the blank
At the end of 20x1, Mejorar Company implemented a low-cost strategy to improve its competitive position. Its objective was to become the low-cost producer in its industry. A Balanced Scorecard was developed to guide the company toward this objective. To lower costs, Mejorar undertook a number of improvement activities such as JIT production, total
20x1 | 20x3 | |||
Theoretical annual capacity* | 249,600 | 249,600 | ||
Actual production** | 208,000 | 234,000 | ||
Market size (in units sold) | 1,300,000 | 1,300,000 | ||
Production hours available (40 workers) | 104,000 | 104,000 | ||
Very satisfied customers | 62,400 | 117,000 | ||
Actual cost per unit | $340 | $272 | ||
Days of inventory | 14 | 7 | ||
Number of defective units | 12,480 | 7,020 | ||
Total worker suggestions | 80 | 320 | ||
Hours of training | 260 | 1,040 | ||
Selling price per unit | $190 | $190 | ||
Number of new customers | 5,200 | 25,740 |
*Amount that could be produced given the available production hours; everything produced is sold.
**Amount that was produced given the available production hours.
Required:
j. Total revenue.
20x1 | $fill in the blank |
20x3 | $fill in the blank |
k. Number of new customers.
20x1 | fill in the blank |
20x3 | fill in the blank |

Trending now
This is a popular solution!
Step by step
Solved in 2 steps

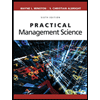
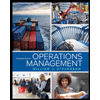
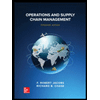
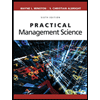
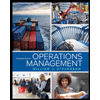
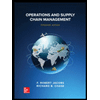
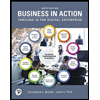
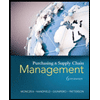
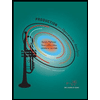