700 Ti-5AI-2.5Sn titanium alloy 600 4340 steel 500 S 400 1045 steel 300 Ductile cast iron 200 70Cu-30Zn brass 2014-T6 Al alloy 100 EQ21A-T6 Mg alloy 105 106 104 107 108 109 Cycles to failure, N Maximum stress, S (MPa)
Design Against Fluctuating Loads
Machine elements are subjected to varieties of loads, some components are subjected to static loads, while some machine components are subjected to fluctuating loads, whose load magnitude tends to fluctuate. The components of a machine, when rotating at a high speed, are subjected to a high degree of load, which fluctuates from a high value to a low value. For the machine elements under the action of static loads, static failure theories are applied to know the safe and hazardous working conditions and regions. However, most of the machine elements are subjected to variable or fluctuating stresses, due to the nature of load that fluctuates from high magnitude to low magnitude. Also, the nature of the loads is repetitive. For instance, shafts, bearings, cams and followers, and so on.
Design Against Fluctuating Load
Stress is defined as force per unit area. When there is localization of huge stresses in mechanical components, due to irregularities present in components and sudden changes in cross-section is known as stress concentration. For example, groves, keyways, screw threads, oil holes, splines etc. are irregularities.
A cylindrical rod of diameter 9.5 mm fabricated from a 2014-T6 aluminum alloy is subjected to rotating–bending load cycling; test results (as S–N behavior) are shown in Figure 8.21. If the maximum and minimum loads are +400 N and −400 N, respectively, determine its fatigue life. Assume that the separation between load-bearing points is 72.5 mm.
Figure 8.21 is attached


Trending now
This is a popular solution!
Step by step
Solved in 4 steps with 3 images

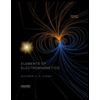
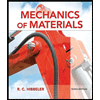
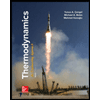
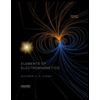
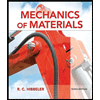
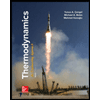
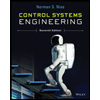
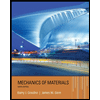
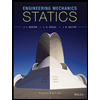