Hydraulic System and Components Matthew Skelton
docx
keyboard_arrow_up
School
Embry-Riddle Aeronautical University *
*We aren’t endorsed by this school
Course
270
Subject
Mechanical Engineering
Date
Jan 9, 2024
Type
docx
Pages
4
Uploaded by Skelt04
Hydraulic System and Components
Matthew A. Skelton
Embry-Riddle Aeronautical University
AMNT 270: Airframe Structures & Application
Professor Brandon Gelb
December 4, 2022
1
From small to large aircraft hydraulic systems are in use to assist the pilot in controlling
the aircraft. Smaller and light aircraft may only use hydraulics for braking while larger aircraft
will use hydraulics to help in the control of flight controls, sure beats the days of flying using
only wires and cables. Hydraulic systems are comprised of many different components and
require safety precautions when performing maintenance due to the fluid and the pressure the
fluid is under which ranges from about 3000 psi to 5000 psi for most aircraft (Skybrary, n.d.).
There are three major components to a hydraulic system and they are the hydraulic pump,
motor and the system plumbing (Skybrary, n.d.). The pump, in which its name implies, pumps
the fluid into the system to create the fluid pressure. The next component is the hydraulic motor
which converts the pressure from the fluid into a mechanical output, an example of this would be
the motor on the vertically driven landing gear found on a C-130 (Skybrary, n.d.). Now the most
complex part of the system is the plumbing. The plumbing is comprised of a reservoir, filters,
shut off valves, control valves, pressure relief valves, hydraulic fuses, and accumulators
(Skybrary, n.d.). A reservoir is used to hold an optimized amount of fluid needed to provide a
ready source to pumps and the system, this will vary with aircraft needs. Filters are used to
protect the system and keep contaminants out of the fluid and system. Shut off valves are
typically found near the engine firewall and are used in the event of an engine fire to cut off fluid
supply and prevent the fluid from catching fire. Control valves control where the fluid goes, a
component such as the flaps will have an up and downside to the motor and depending on what
the input is the control valve will send fluid to the correct side to move flaps (Skybrary, n.d.).
Pressure relief valves are in place to ensure system pressure does not exceed what the system can
handle, this is important because damage to the system, aircraft and surrounding personnel could
be serious is the system reach too high of pressure. Now if system pressure becomes too low then
2
a hydraulic fuse in a line would kick in and cut off supply to the line to allow pressure to build
back up for components that are more essential.
The hydraulic system is complex and consists of numerous parts and components that
allow for its operation. The maintenance required on the system requires the upmost care and
attention and there are multiple risk factors. Hydraulic fluid alone is not only very flammable,
but it also poses health concerns due to its chemical properties. Aside from the risk potentials
associated with the fluid there is also the concern of ensuring that system pressure has been
depleted before removing and working on components as a pressurized system would cause
potential major injuries.
3
Your preview ends here
Eager to read complete document? Join bartleby learn and gain access to the full version
- Access to all documents
- Unlimited textbook solutions
- 24/7 expert homework help
References
Skybrary Aviation Safety. (n.d.). Hydraulic Systems. SKYbrary Aviation Safety. Retrieved
December 4, 2022, from https://www.skybrary.aero/articles/hydraulic-systems.
4
Related Documents
Related Questions
level 3 autonomous system in transportation sector
arrow_forward
what is the difference between the terms fluid power and hydraulics and pneumatics?
arrow_forward
Energy Star Washing Machine
Model #: GTW500ASN
Style: Top Loader
Cubic Feet: 4.5 cubic feet
Yearly Energy Usage (from Energy Guide): 210
kWh/y
Non-Energy Star Washing Machine
Model #: GTW465ASN
Style: Top Loader
Cubic Feet: 4.5 cubic feet
Yearly Energy Usage (from Energy Guide): 175
kWh/yr
Picture of Appliance:
Website Link to Retail Store
Purchase Price: (1) $498.00
Yearly Energy Use (in kWh): 175 kWh/yr
Energy Cost per Year
(Energy usage in kWh from above x .1111
cents/kWh): (3)
Cost Recuperation Estimation
1
Picture of Appliance:
Website Link to Retail Store
Purchase Price: (2) $478.00
Yearly Energy Use (in kWh): 210 kWh/yr
Energy Cost per Year
(Energy usage in kWh from above x.1111
cents/kWh): (4)
Initial Cost Difference: Energy Star Appliance Price (1) - Non-Energy Star Appliance Price (2)
Calculation (Show Your Work):
This is the original upfront price difference. In other words, how much more money the Energy-Star
Appliance costs.
2.
Cost Per Year Difference: Non-Energy Star…
arrow_forward
Select correct formula and description of the mechanical efficiency for fluid motors________
arrow_forward
15
arrow_forward
linear hydraulic actuators consists of a hollow cylinder that contains fluid and a piston, when pressure is applied onto the piston, objects can be moved by the force produced.True or flase
arrow_forward
Instrumentation & Measurements
This homework measures your capability to design/analyze various components/variables of ameasurement system based on what you have studied.
Question 1 Attached.
arrow_forward
Problem 2:
It is important when designing ships to ensure that gyroscopic effect of the mounted turbine engine and its
direction (torque reaction of the gyroscopic effect) are well identified prior to mounting the engine along with
body axis. Your role in a team working in ship manufacturing company is to analyse the mounting process and
calculate the required information to prevent any expected gyroscopic effect on the ship navigation line (no
unwanted steering of the ship due to gyroscopic torque). Your manger asked you to provide detailed report of
your calculations and final professional recommendations after giving you the following information:
- The mounted engine rotates anticlockwise at 8000 rpm, when viewed from front.
- The moment of inertia of all the rotating parts are 230 kg.m².
The ship makes a right-hand turn of radius of 400 m at speed of 2.2 m/s.
arrow_forward
How will you differentiate the three flight control systems used in large aircraft? (Mechanical, Hydromechanical, and Fly-by-wire)
arrow_forward
hydraulic actuator consist of a cylinder or motor that utilizes mechanical process to facilitate hydraulic power True or false
arrow_forward
SEE MORE QUESTIONS
Recommended textbooks for you
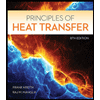
Principles of Heat Transfer (Activate Learning wi...
Mechanical Engineering
ISBN:9781305387102
Author:Kreith, Frank; Manglik, Raj M.
Publisher:Cengage Learning
Related Questions
- level 3 autonomous system in transportation sectorarrow_forwardwhat is the difference between the terms fluid power and hydraulics and pneumatics?arrow_forwardEnergy Star Washing Machine Model #: GTW500ASN Style: Top Loader Cubic Feet: 4.5 cubic feet Yearly Energy Usage (from Energy Guide): 210 kWh/y Non-Energy Star Washing Machine Model #: GTW465ASN Style: Top Loader Cubic Feet: 4.5 cubic feet Yearly Energy Usage (from Energy Guide): 175 kWh/yr Picture of Appliance: Website Link to Retail Store Purchase Price: (1) $498.00 Yearly Energy Use (in kWh): 175 kWh/yr Energy Cost per Year (Energy usage in kWh from above x .1111 cents/kWh): (3) Cost Recuperation Estimation 1 Picture of Appliance: Website Link to Retail Store Purchase Price: (2) $478.00 Yearly Energy Use (in kWh): 210 kWh/yr Energy Cost per Year (Energy usage in kWh from above x.1111 cents/kWh): (4) Initial Cost Difference: Energy Star Appliance Price (1) - Non-Energy Star Appliance Price (2) Calculation (Show Your Work): This is the original upfront price difference. In other words, how much more money the Energy-Star Appliance costs. 2. Cost Per Year Difference: Non-Energy Star…arrow_forward
- Select correct formula and description of the mechanical efficiency for fluid motors________arrow_forward15arrow_forwardlinear hydraulic actuators consists of a hollow cylinder that contains fluid and a piston, when pressure is applied onto the piston, objects can be moved by the force produced.True or flasearrow_forward
- Instrumentation & Measurements This homework measures your capability to design/analyze various components/variables of ameasurement system based on what you have studied. Question 1 Attached.arrow_forwardProblem 2: It is important when designing ships to ensure that gyroscopic effect of the mounted turbine engine and its direction (torque reaction of the gyroscopic effect) are well identified prior to mounting the engine along with body axis. Your role in a team working in ship manufacturing company is to analyse the mounting process and calculate the required information to prevent any expected gyroscopic effect on the ship navigation line (no unwanted steering of the ship due to gyroscopic torque). Your manger asked you to provide detailed report of your calculations and final professional recommendations after giving you the following information: - The mounted engine rotates anticlockwise at 8000 rpm, when viewed from front. - The moment of inertia of all the rotating parts are 230 kg.m². The ship makes a right-hand turn of radius of 400 m at speed of 2.2 m/s.arrow_forwardHow will you differentiate the three flight control systems used in large aircraft? (Mechanical, Hydromechanical, and Fly-by-wire)arrow_forward
arrow_back_ios
arrow_forward_ios
Recommended textbooks for you
- Principles of Heat Transfer (Activate Learning wi...Mechanical EngineeringISBN:9781305387102Author:Kreith, Frank; Manglik, Raj M.Publisher:Cengage Learning
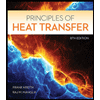
Principles of Heat Transfer (Activate Learning wi...
Mechanical Engineering
ISBN:9781305387102
Author:Kreith, Frank; Manglik, Raj M.
Publisher:Cengage Learning