lab 2 experimental methods
pdf
keyboard_arrow_up
School
University of Illinois, Chicago *
*We aren’t endorsed by this school
Course
341
Subject
Mechanical Engineering
Date
Apr 3, 2024
Type
Pages
20
Uploaded by SargentPolarBearMaster738
THE UNIVERSITY OF ILLINOIS AT CHICAGO
ME 341-EXPERIMENTAL METHODS IN MECHANICAL
ENGINEERING
Spring 2024
Centrifugal Pumps
Experiment # 2
Submitted by:
2/23/2024
1 Background
Centrifugal pumps are mechanical equipment that moves fluid by transferring rotational
energy from motor driven impellers. Testing for centrifugal pumps is done experimentally
because pump head, hydraulic power, and efficiency are all dependent on flow rate and
rotational speed [1]. One way to increase the pump head of a centrifugal pump is to connect
multiple pumps in series. Another way to increase the pump head is to change the impeller
diameter. Pump’s with a larger impeller diameter have a high pump head pressure when flow
rate and rotational speed are held constant. The theoretical head is linearly negatively
correlated with flow rate but due to frictional losses the actual head is less than the theoretical
value. Hydraulic power is the power gained by the fluid. A pump’s efficiency is power gained
divided by the fluid divided shaft power driving the pump shaft power driving the pump. The
purpose of this experiment is to examine the centrifugal pumps of single speed, of a variable
speed and two pumps in series in series.
As a team and through our experiments with centrifugal pumps, we’ve gained insights of
pump performances and operations. We were able to observe flow rate, pressure, and the
power consumption. Performing single pump analysis we saw its performance and effectiveness
with just one pump. We also looked at the performances of pumps in a series and its efficiency
for moving water around.
For a single pump we looked at various speeds and the pressure at certain speeds
depending on the inflows and outflows of the pump. It just is not that efficient as it also wastes
the same amount of energy as the pumps in the series do. Single pumps would not be so
practical in an industrial setting that needs a lot of water, it would not be efficient and one
would really need a single pump on a smaller scale. It would be effective on an agricultural
level, or anywhere where water might not be moved around too much such as a city's sewer
system.
For a pump in a series we were able to observe the total head produced by the system in
pressure delivery. We tested out different speeds and different pressures. We also noticed it
needed the same amount of volts as the single pump. It was a lot faster than a single pump at
all speeds. Multiple pumps working will produce more pressure. Having pumps in a series can
also be beneficial if one pump fails, then there would be another left over to do any work. With
the ability to distribute workload on multiple pumps, it improves the systems reliability and
performance. Pumps in a series just seem to be more beneficial in an industrial setting where
you might need to move a lot of water. It gave us an idea how pumps in a series can also be
beneficial to water distribution systems and sewer lines. Any setting that needs higher water
pressure will benefit from using pumps in a series.
2 Results
Maximum pump efficiency is discovered through experimental testing. These results show the
effects of placing pumps in different configurations; isolated, in parallel and in series. The
following analysis calculates and compares flow rate, pump head and efficiency of these
configurations. Figures 12-14 display curves for the derived theoretical pump heads by
combining pressure heads of the single speed pump and variable speed pump and comparing
them to the experimental P1 and P2 in series. The pressure head readings were graphed with
respect to flow rate. This was reiterated for 2000, 2200, and 2400 rpm.
2.1 Single Speed Pump Analysis
The first trial involves a single pump with varying flow rate. Flow rate is calculated by using the
formula
. The hydraulic bench outputs values with units of liters which are
𝑄 =
∆?
∆?
(1)
converted to
for calculations with a conversion factor of
. The pressure is measured by
𝑚
3
1
1000
a Bourdon tube.Figure one shows how the pump head increases as the flow rate decreases.
Figure 1:
Pump Head versus flow rate for a single non-variable pump.
2.2 Variable Speed Pump Analysis
Your preview ends here
Eager to read complete document? Join bartleby learn and gain access to the full version
- Access to all documents
- Unlimited textbook solutions
- 24/7 expert homework help
A single pump running at different RPMs shows how flowrate and angular speed of the impeller
effect the output pressure of a single pump.
Figure 2 shows the performance characteristics of pump head, shaft input power, and pump
efficiency for P2 running at 2000 RPM. Shaft power started at 148 watts and remained constant
throughout. Efficiency % started at 6% and increased two times to a final efficiency of 8%. Head
pressure started at 7m and decreased three times to 4m throughout the flow rate.
Figure 2:
Pump head, shaft input power, and pump efficiency as a function of flow rate for P2 at 2000 RPM
Figure 3 shows the performance characteristics of pump head, shaft input power, and pump
efficiency for P2 running at 2200 RPM. Shaft power remained constant at 160 watts. Efficiency
started at 7%, increased to 11.5%, and dropped to 9%. The pressure head started at 9m and
decreased down to 4m throughout the flow rate.
Figure 3:
Pump head, shaft input power, and pump efficiency as a function of flow rate for P2 at 2200 RPM
Figure 4 shows the performance characteristics of pump head, shaft input power, and pump
efficiency for P2 running at 2200 RPM. Work shaft power was constant from 160 with a slight
increase to 163 watts. Efficiency started at 10%, rose to 13%, fell to 12%, and increased 0.5%
again. The pump head started at 12m and kept decreasing throughout the flow rate down to
4m.
Figure 4:
Pump head, shaft input power, and pump efficiency as a function of flow rate for P2 at 2400 RPM
Figure 5 shows head coefficient vs flow coefficient at 2000, 2200, and 2400 rpm. 2000 rpm
displayed the lowest head pressure throughout except at 0.00035 flow coefficient where it
began to increase. 2400 rpm showed highest head coefficient from a 0 to 0.00025 flow
coefficient. 2200 rpm showed the highest head coefficient from 0.00025 to 0.004 flow
coefficient.
Your preview ends here
Eager to read complete document? Join bartleby learn and gain access to the full version
- Access to all documents
- Unlimited textbook solutions
- 24/7 expert homework help
Figure 5:
Head coefficient vs flow coefficient for 2000, 2200 and 2400 RPM
Figure 6 shows the hydraulic coefficient vs flow coefficient at 2000, 2200, and 2400 rpm. At
2000 rpm, the hydraulic coefficient remained constant with a miniscule increase around a flow
coefficient of 0.0002. At 2200 rpm, hydraulic coefficient remained constant with a miniscule
increase at 0.00035 flow coefficient. At 2400 rpm, the hydraulic coefficient also remained
constant, however at 0.0002 flow coefficient it showed a steeper increase in hydraulic
coefficient compared to 2000 and 2200 rpm.
Figure 6:
Hydraulic power coefficient vs. flow coefficient for 2000, 2200 and 2400 RPM
Figure 7 shows the efficiency coefficient vs flow coefficient at 2000 RPM, 2200 RPM, and 2400
rpm. At 2400 rpm, the efficiency coefficient was highest with 13% at 0.00015 m^3/s and
maintained higher efficiency overall compared to 2000 and 2200 rpm. 2000 rpm showed the
lowest coefficient performance from 6% to 7%. 2200 rpm showed a high peak efficiency of 11%
at 0.00033 m^3/s.
Figure 7:
Efficiency coefficient vs. flow coefficient for 2000, 2200 and 2400 RPM
Using pump laws one can theoretically analyze a similar pump with a different impeller speed.
Using the equation
the values of
can be determined.
. Figure
?
?
=
𝑄
1
ω
1
?
1
3
=
𝑄
2
ω
2
?
2
𝑄
2
ℎ
2
=
ℎ
1
?
2
2
?
1
2
X shows hp vs. Q from P2 (measured values) at 2200 rpm. As Q increases the pump head
decreases.
Figure 8 shows the theoretical flow rate vs. pump head of a pump similar to P2 with an impeller
diameter of 0.1 m at 2200 RPMS. Decreasing the impeller diameter decreases the pump head
and the flow rate.
Your preview ends here
Eager to read complete document? Join bartleby learn and gain access to the full version
- Access to all documents
- Unlimited textbook solutions
- 24/7 expert homework help
Figure 8:
Flow Rate vs. pump head of P2 running at 2200 RPMS with impeller size 0.15 diameter
in blue and impeller size 0.1 diameter in orange.
Control
Valve
Position
Description
Volume [L]
Time [s]
Inlet
pressure
head @
discharge
manifold [m
H20]
1
Shut-off
0
N/A
24
2
Partially open
10
26.23
18
3
Partially open
10
18.57
12
4
Partially open
10
14.33
6
5
Full open
10
12.21
0
Table 1:
Single Speed Pump P1
Valve
Position
Description
Speed
[RPM]
Volu
me
[L]
Time [s]
Inlet
pressure
head on
P2 [m
H20]
Outlet
pressure
head on
P2 [m
H20]
Voltage
[V]
Curre
nt [A]
1
Shut-off
2000
0
N/A
0
9
159
1.19
2
Partially open
2000
5
40.74
0
7
159
1.19
3
Partially open
2000
5
30.47
0
5
159
1.19
4
Partially open
2000
5
21.98
-2
2
159
1.2
5
Full open
2000
10
33.29
-4
0
159
1.21
1
Shut-off
2200
0
N/A
0
11
173
1.18
2
Partially open
2200
5
41.22
0
9
173
1.2
3
Partially open
2200
5
25.1
0
7
173
1.21
4
Partially open
2200
5
19.33
-2
5
173
1.21
5
Full open
2200
5
13.68
-4
0
173
1.23
1
Shut-off
2400
0
N/A
0
13
187
1.23
2
Partially open
2400
5
30.75
-1
10
187
1.23
3
Partially open
2400
5
19.83
-2
7
187
1.25
4
Partially open
2400
5
14.81
-3
3
187
1.26
5
Full open
2400
5
11.93
-5
0
187
1.28
Table 2:
Variable Speed Pump P2
Valve
Position
Description
Speed
[RPM]
Volu
me
[L]
Time [s]
Inlet
pressure
head on
P2 [m
H20]
Outlet
pressure
head on
P2 [m
H20]
Voltage
[V]
Curre
nt [A]
1
Shut-off
2000
0
N/A
25
34
159
1.17
2
Partially open
2000
5
18.38
21
26
159
1.19
3
Partially open
2000
5
10.78
17
18
159
1.21
4
Partially open
2000
5
8.21
13
10
159
1.22
5
Full open
2000
5
7.56
8
0
159
1.23
1
Shut-off
2200
0
N/A
25
36
173
1.18
2
Partially open
2200
5
15.95
20
27
173
1.22
3
Partially open
2200
5
10.81
16
18
173
1.24
4
Partially open
2200
5
8.53
11
9
173
1.25
5
Full open
2200
5
6.9
7
0
173
1.26
1
Shut-off
2400
0
N/A
25
38
187
1.2
2
Partially open
2400
5
18.32
21
30
187
1.28
3
Partially open
2400
5
11.11
16
20
187
1.3
4
Partially open
2400
5
8.56
11
10
187
1.32
5
Full open
2400
5
6.81
6
0
187
1.35
Table 3:
Trials of Pumps in Series P1+P2.
Your preview ends here
Eager to read complete document? Join bartleby learn and gain access to the full version
- Access to all documents
- Unlimited textbook solutions
- 24/7 expert homework help
2.3 Pumps in Series Analysis
After running experiments that isolated P1 and P2 they were placed in series to show how that
configuration increases the pressure.
Figure 9 shows pump head (m) vs flow rate (m^3/s) for single speed pump p1, variable speed
pump p2, and P1 + P2 series pump. The series pump showed higher pressure readings up until a
flow rate of 0.0005 m^3/s where the readings matched P1 pressure head then fell lower than P1
pressure head afterwards. P2 showed the lowest pressure head readings overall.
Figure 9:
Pump Head, Hp (m) vs flow rate, Q (m^3/s) at 2000 rpm with curves of P1, P2, and P1 and P2 in series.
Figure 10 displays how variable speed pump 1, variable speed pump 2, and P1 + P2 series
pumps’ pressure head readings (m) change with respect to flow rate (m^3/s). P2 readings
displayed lowest pressure head readings, P1 displayed moderate pressure readings, and P1 + P2
displayed the highest pressure readings. However, around 0.0005 m^3/s, P1 showed higher
pressure readings.
Figure 10:
Pump Head, Hp (m) vs flow rate, Q (m^3/s) at 2200 rpm with curves of P1, P2, and P1 and P2 in series.
Figure 11 displays how variable speed pump 1, variable speed pump 2, and P1 + P2 series
pumps’ pressure head readings (m) change with respect to flow rate (m^3/s). The behavior of
the three curves was similar to Fig. 10. However, the pressure head readings were lower by 1m
to 3m in contrast to fig. 10 data.. P2 readings displayed lowest pressure head readings, P1
displayed moderate pressure readings, and P1 + P2 displayed the highest pressure readings.
However, around 0.0005 m^3/s, P1 showed higher pressure readings.
Figure 11:
Pump Head, Hp (m) vs flow rate, Q (m^3/s) at 2400 rpm with curves of P1, P2, and P1 and P2 in series.
Your preview ends here
Eager to read complete document? Join bartleby learn and gain access to the full version
- Access to all documents
- Unlimited textbook solutions
- 24/7 expert homework help
In figure 12 for 2000 rpm, the experimental curve from 0 m^3/s to 0.000175 shows higher
pressure head values relative to theoretical head pressure. At 0.0002 m^3/s, theoretical and
experimental pressure head values match. After 0.000275 m^3/s, experimental pressure head
value significantly differed from theoretical.
Figure 12:
Pump Head, Hp (m) vs Flow Rate, Q (m^3/s) with curves of the pump heads for derived theoretical and
experimentally obtained at 2000 rpm.
At 2200 rpm, figure 13 shows similar behavior to fig. 12 at 2000 rpm in terms of behavior. From
0 m^3/s to 0.0001 m^3/s, experimental pressure head was higher, 0.0013 m^3/s shows a
matching pressure head value, and experimental deviates from theoretical after. Additionally,
the experimental curve deviates apart earlier at 0.0002 m^3/s in comparison to fig. 12.
Figure 13:
Pump Head, Hp (m) vs Flow Rate, Q (m^3/s) with curves of the pump heads for derived theoretical and
experimentally obtained at 2200 rpm.
At 2400 rpm in fig. 14, the behavior of the curves were similar again. Experimental curve starts
with higher pressure head values from 0 m^3/s to 0.0002 m^3/s, matches the pressure head at
0.0002 m^3/s, and then departs from the theoretical curve afterwards.
Figure 14:
Pump Head, Hp (m) vs Flow Rate, Q (m^3/s) with curves of the pump heads for derived theoretical and
experimentally obtained at 2400 rpm.
3 Discussion
For a centrifugal pump the pump head (
decreases as the flow rate increases. This
ℎ
?
) occurs because frictional losses within the pump increase which reduces the head pressure
produced by the pump. The shaft input power (
) initially increases with an increase in flow
?
?
rate, it reaches a maximum power, and then decreases. This occurs because the shaft input
power is related to the product of flow rate, pump head, and fluid density, considering pump
efficiency. Pump efficiency (
η
) has a bell-shaped curve as a function of flow rate. There is an
optimum flow rate at which the pump operates at maximum efficiency. This is because at very
low or high flow rates, the pump operates inefficiently due to factors like hydraulic and
mechanical losses. Increasing the pump speed results in increases in flow rate, head, and power.
The head coefficient relates the ratio of the head produced by the pump to the kinetic
energy per unit weight imparted to the fluid by the impeller. The flow coefficient relates the
flow rate of the pump relative to its size and speed. The hydraulic power coefficient describes
how efficiently the pump converts the kinetic energy in the fluid flow into mechanical power.
Figure 6 shows a relatively flat hydraulic power coefficient vs. flow coefficient graph.
That means that the system operates with stable efficiency across different flow conditions. The
pump is capable of handling variations in flow without significant losses in hydraulic power
Your preview ends here
Eager to read complete document? Join bartleby learn and gain access to the full version
- Access to all documents
- Unlimited textbook solutions
- 24/7 expert homework help
efficiency. Figure 7 shows that the pump is most efficient at each rpm at different flow rates
which is what the theory for the experiment predicts.
The pump scaling laws show that decreasing the impeller diameter results in a decrease
in the flow rate. This makes sense because a smaller impeller moves less fluid through the pump
for each rotation.
The pump head is proportional to the square of the impeller diameter.
Reducing the impeller diameter therefore decreases the head. A smaller impeller transfers less
mechanical energy to the fluid which leads to a lower elevation that the fluid can be pumped.
However, a reason to decrease the impeller speed is that the power required to operate a pump
is proportional to the cube of the impeller diameter. Therefore in applications where a smaller
impeller can achieve acceptable levels of flowrate and pressure the smaller impeller can save
operational power costs.
4. For pumps in series, plot the theoretical pump head vs. flow rate curve derived from
the individual pump head vs. Q of the two pumps. Compare this theoretical plot with the one
that is experimentally obtained.
In all three RPM settings tested, a distinct trend arises. For lower flow rates, the
observed experimental curve is higher than predicted theoretically. This discrepancy could stem
from measurement error in the bourdon gauge or the exclusion of the measurement of inlet
pressure of the single speed pump. As flow rate increases, the experimental curve falls beneath
the theoretical, with an increasingly steep negative slope. This is anticipated given the
relationship that losses escalate due to the square of velocity.
Author Contribution and Teamwork
4 References
[1] Department of Mechanical and Industrial Engineering.
“Experiment #2: Performance of
Centrifugal Pumps.” Chicago, IL: University of Illinois at Chicago, Fall 2022.
[2] Figliola, R., and D. Beasley. “Theory and Design for Mechanical Measurements, 6th Ed.,”
Hoboken: Wiley, 2015.
5 Appendix: Sample Calculations
Flow Rate
𝑄 =
∆?
∆?
1𝑚
3
=
1𝐿
1000
18
26.23*1000
= 0. 00068624
Hydraulic Power
?
𝑓
= 𝑄γℎ
?
=
?
𝑓
0. 000123 · 9800 · 7 = 8
Pump Shaft Power
?
?
= η
𝑚????
𝐼?
?
?
= 0. 75 · 159 · 1. 19 = 142
Pump Efficiency
η
??𝑚?
=
?
𝑓
?
?
η
??𝑚?
=
8
142
= 0. 0593 = 5. 93%
Pump Scaling Laws
?
?
=
𝑄
1
ω
1
?
1
3
=
𝑄
2
ω
2
?
2
3
𝑄
2
=
𝑄
1
?
2
3
?
1
3
𝑄
2
=
0.000124*.1
3
.15
3
= 3. 59 * 10
−5
Related Documents
Related Questions
Hab. Tiruneh, [4/2/2023 1:23 AM]A solar flux q ^ * falls on a unit length of a very thin tube of diameter d. Inside the tube is a stationary water with initial temperature T_{i} (same as ambient and no gradient inside at any time) and absorbs some of the heat while the rest leaves by convection from the surface to the ambient at T_{m} Develop an equation that can help to determine the temperature of the water at any time. Plot the temperature of the water against time. For a long elapsed time what will be the temperature? To simplify the analysis use theta = T*T_{e} * d*theta = dT theta_{i} = T_{i}*T_{o} (initial condition.
Hab. Tiruneh, [4/2/2023 11:53 AM]A flat wall is exposed to an environmental temperature of 38°C. The wall is covered with a layer of insulation 2.5 cm thick whose thermal conductivity is 1.4W / (m ^2 *` C and the temperature of the wall on the inside of the insulation is 315°C. The wall loses heat to the environment by convection. Compute the value of the convection…
arrow_forward
Given:
The plane accelerates in its current trajectory with a= 100 m/s^2
Farag
Angle theta= 5°
W=105 kips
F_drag= 80 kips
m= 1000 lbs
Find: F_thrust, F_lift
Please include the KD.
Fthrust
Futel t Fueight
000
BY NC SA
2013 Michael Swanbom
arrow_forward
fluid mechanics 1
can you solve this one plz in details ?
arrow_forward
Problem 7
For water flow through the control volume shown in Figure 10. Use the Reynolds transport theorem
with parameter b equal to the velocity to determine the momentum flow rates across the vertical surfaces
A-D and B-C.
A
1 ft/s
2 ft
6 ft/s
1 ft
5 ft
2 ft/s
1 ft/s
2 ft
Control surface
Figure 10: Water flow in a control volume
[Ans : 38.8 lb, 77.6 lb)
arrow_forward
ES
Font
English (United Kingdom)
▬▬ Q Search
>
Text Predictions: On
ALT
Paragraph
S
Accessibility: Good to go
Styles
The following parameters characterise a liquid-fuelled rocket engine: stagnation
pressure P0=100bar; stagnation temperature TO=3300K; nozzle exit diameter DE=1.0m;
throat diameter=0.1 m; gas constant R=692 Jkg-1 K -1; ratio of specific heats
cp/cV=y=1.25. Estimate the following: static pressure at the exit plane, exit Mach
number.
Heading
Focus
Editing
ENG
UK
arrow_forward
!
Required information
The power P generated by a certain windmill design depends upon its diameter D, the air density p, the wind velocity V,
the rotation rate 2, and the number of blades n.
A model windmill, of diameter 50 cm, develops 2.7 kW at sea level when V= 40 m/s and when rotating at 4800 rev/min. What power
will be developed by a geometrically and dynamically similar prototype, of diameter 5 m, in winds of 10 m/s at 2000 m standard
altitude? At 2000 m altitude, p = 1.0067 kg/m3. At sea level, p= 1.2255 kg/m3.
The power developed is
]KW.
arrow_forward
Electric drives have a wide range of applications in various industries. One common application is in the manufacturing industry, where electric drives are used to control the speed and torque of electric motors that drive various machines and equipment. For example, electric drives are used in conveyor systems, pumps, fans, compressors, and machine tools to regulate the motion and force required for different manufacturing processes.
1. Create simple Process Flow Diagram (PFD) of electric motor used in pumps.
arrow_forward
7.
Pump
50mm Þ
17m
Data: f = 0.0067
Pressure at 3 = 194 kN/m² gauge
Velocity at 3 = 2.7 m/s
p = 830 kg/m³
Pump efficiency = 88%
Motor efficiency = 84%
Pressure at 1 is atmospheric
Velocity at 1 is negligible
Determine required input power to motor [1.64 kW]
8.
200mm turbine
water
gen
Data: At 1, p = 230 kN/m² gauge, v =
At 2, p = 0 = 0 gauge, v = 0
Turbine efficiency = 80%
Generator efficiency = 90%
3.6 m/s
%3D
Determine output power from generator [19.3 kW]
arrow_forward
LR = 5m, LG = 2.5m and LC = 1.1m
Q2. The Skylark family of sounding rockets consisted of a number of variants (denoted Skylark
5, Skylark 7, and Skylark 12 respectively). These are illustrated on Page 3. The data given
below is based on that for the rocket motors they used (all manufactured and named by what
was Royal Ordinance – now part of Roxel):
Raven XI Motor
Total mass: 1280 kg
Length = LR See Case Table (units are m)
Diameter = 0.44 m
Goldfinch IIA Motor
Total mass: 420 kg
Length = LG See Case Table (units are m)
Diameter = 0.44 m
Cuckoo IV Motor
Total mass: 242 kg
Length = LC See Case Table (units are m)
Diameter = 0.44 m
The payload mass which is additional to the motor masses is to be taken as 100 kg.
(a) For the configurations of the three rockets shown on Page 3 in Fig. Q2:
(i) Determine the Pitching/Yawing moment of inertia of each rocket about the base of
each rocket.
(ii) Explain how you could then find the the Pitching/Yawing moment of inertia of each
rocket about its…
arrow_forward
Please solve and answer the question correctly. Thank you!!
arrow_forward
Cakulate the time rate of change of air density during expiration Assume that the lung
(Fig. 3.11) has a total volume of 6000 ml, the diameter of the trachea is 18 mm, the airflow
velocity out of the trachea is 20 cm/s, and the density of air is 1.225 kg/m. Also assume that
lung volume is decreasing at a rate of 100 mL/s.
Hello sir, I want the same
solution, but in a detailed
way and mention his data, a
question, and a solution in
detailing mathematics
without words.
Solution
We will start from Eq. (3.24) because we are asked for the time rate of change of density. We
are asked to find the time rate of change of air density; this suggests that Example 3.5 condis
tions are representing a nonsteady flow scenario. In addition, we were told what the rate of
change in the lung volume is during this procedure, further supporting the use of Eq. (3.24).
pdV+
(3.24
ams
Assume that at the instant in time that we are measuring the system, density is uniform
within the volume of interest. This…
arrow_forward
SEE MORE QUESTIONS
Recommended textbooks for you
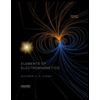
Elements Of Electromagnetics
Mechanical Engineering
ISBN:9780190698614
Author:Sadiku, Matthew N. O.
Publisher:Oxford University Press
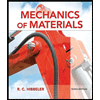
Mechanics of Materials (10th Edition)
Mechanical Engineering
ISBN:9780134319650
Author:Russell C. Hibbeler
Publisher:PEARSON
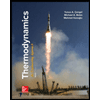
Thermodynamics: An Engineering Approach
Mechanical Engineering
ISBN:9781259822674
Author:Yunus A. Cengel Dr., Michael A. Boles
Publisher:McGraw-Hill Education
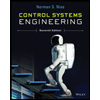
Control Systems Engineering
Mechanical Engineering
ISBN:9781118170519
Author:Norman S. Nise
Publisher:WILEY
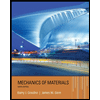
Mechanics of Materials (MindTap Course List)
Mechanical Engineering
ISBN:9781337093347
Author:Barry J. Goodno, James M. Gere
Publisher:Cengage Learning
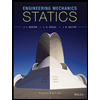
Engineering Mechanics: Statics
Mechanical Engineering
ISBN:9781118807330
Author:James L. Meriam, L. G. Kraige, J. N. Bolton
Publisher:WILEY
Related Questions
- Hab. Tiruneh, [4/2/2023 1:23 AM]A solar flux q ^ * falls on a unit length of a very thin tube of diameter d. Inside the tube is a stationary water with initial temperature T_{i} (same as ambient and no gradient inside at any time) and absorbs some of the heat while the rest leaves by convection from the surface to the ambient at T_{m} Develop an equation that can help to determine the temperature of the water at any time. Plot the temperature of the water against time. For a long elapsed time what will be the temperature? To simplify the analysis use theta = T*T_{e} * d*theta = dT theta_{i} = T_{i}*T_{o} (initial condition. Hab. Tiruneh, [4/2/2023 11:53 AM]A flat wall is exposed to an environmental temperature of 38°C. The wall is covered with a layer of insulation 2.5 cm thick whose thermal conductivity is 1.4W / (m ^2 *` C and the temperature of the wall on the inside of the insulation is 315°C. The wall loses heat to the environment by convection. Compute the value of the convection…arrow_forwardGiven: The plane accelerates in its current trajectory with a= 100 m/s^2 Farag Angle theta= 5° W=105 kips F_drag= 80 kips m= 1000 lbs Find: F_thrust, F_lift Please include the KD. Fthrust Futel t Fueight 000 BY NC SA 2013 Michael Swanbomarrow_forwardfluid mechanics 1 can you solve this one plz in details ?arrow_forward
- Problem 7 For water flow through the control volume shown in Figure 10. Use the Reynolds transport theorem with parameter b equal to the velocity to determine the momentum flow rates across the vertical surfaces A-D and B-C. A 1 ft/s 2 ft 6 ft/s 1 ft 5 ft 2 ft/s 1 ft/s 2 ft Control surface Figure 10: Water flow in a control volume [Ans : 38.8 lb, 77.6 lb)arrow_forwardES Font English (United Kingdom) ▬▬ Q Search > Text Predictions: On ALT Paragraph S Accessibility: Good to go Styles The following parameters characterise a liquid-fuelled rocket engine: stagnation pressure P0=100bar; stagnation temperature TO=3300K; nozzle exit diameter DE=1.0m; throat diameter=0.1 m; gas constant R=692 Jkg-1 K -1; ratio of specific heats cp/cV=y=1.25. Estimate the following: static pressure at the exit plane, exit Mach number. Heading Focus Editing ENG UKarrow_forward! Required information The power P generated by a certain windmill design depends upon its diameter D, the air density p, the wind velocity V, the rotation rate 2, and the number of blades n. A model windmill, of diameter 50 cm, develops 2.7 kW at sea level when V= 40 m/s and when rotating at 4800 rev/min. What power will be developed by a geometrically and dynamically similar prototype, of diameter 5 m, in winds of 10 m/s at 2000 m standard altitude? At 2000 m altitude, p = 1.0067 kg/m3. At sea level, p= 1.2255 kg/m3. The power developed is ]KW.arrow_forward
- Electric drives have a wide range of applications in various industries. One common application is in the manufacturing industry, where electric drives are used to control the speed and torque of electric motors that drive various machines and equipment. For example, electric drives are used in conveyor systems, pumps, fans, compressors, and machine tools to regulate the motion and force required for different manufacturing processes. 1. Create simple Process Flow Diagram (PFD) of electric motor used in pumps.arrow_forward7. Pump 50mm Þ 17m Data: f = 0.0067 Pressure at 3 = 194 kN/m² gauge Velocity at 3 = 2.7 m/s p = 830 kg/m³ Pump efficiency = 88% Motor efficiency = 84% Pressure at 1 is atmospheric Velocity at 1 is negligible Determine required input power to motor [1.64 kW] 8. 200mm turbine water gen Data: At 1, p = 230 kN/m² gauge, v = At 2, p = 0 = 0 gauge, v = 0 Turbine efficiency = 80% Generator efficiency = 90% 3.6 m/s %3D Determine output power from generator [19.3 kW]arrow_forwardLR = 5m, LG = 2.5m and LC = 1.1m Q2. The Skylark family of sounding rockets consisted of a number of variants (denoted Skylark 5, Skylark 7, and Skylark 12 respectively). These are illustrated on Page 3. The data given below is based on that for the rocket motors they used (all manufactured and named by what was Royal Ordinance – now part of Roxel): Raven XI Motor Total mass: 1280 kg Length = LR See Case Table (units are m) Diameter = 0.44 m Goldfinch IIA Motor Total mass: 420 kg Length = LG See Case Table (units are m) Diameter = 0.44 m Cuckoo IV Motor Total mass: 242 kg Length = LC See Case Table (units are m) Diameter = 0.44 m The payload mass which is additional to the motor masses is to be taken as 100 kg. (a) For the configurations of the three rockets shown on Page 3 in Fig. Q2: (i) Determine the Pitching/Yawing moment of inertia of each rocket about the base of each rocket. (ii) Explain how you could then find the the Pitching/Yawing moment of inertia of each rocket about its…arrow_forward
- Please solve and answer the question correctly. Thank you!!arrow_forwardCakulate the time rate of change of air density during expiration Assume that the lung (Fig. 3.11) has a total volume of 6000 ml, the diameter of the trachea is 18 mm, the airflow velocity out of the trachea is 20 cm/s, and the density of air is 1.225 kg/m. Also assume that lung volume is decreasing at a rate of 100 mL/s. Hello sir, I want the same solution, but in a detailed way and mention his data, a question, and a solution in detailing mathematics without words. Solution We will start from Eq. (3.24) because we are asked for the time rate of change of density. We are asked to find the time rate of change of air density; this suggests that Example 3.5 condis tions are representing a nonsteady flow scenario. In addition, we were told what the rate of change in the lung volume is during this procedure, further supporting the use of Eq. (3.24). pdV+ (3.24 ams Assume that at the instant in time that we are measuring the system, density is uniform within the volume of interest. This…arrow_forward
arrow_back_ios
arrow_forward_ios
Recommended textbooks for you
- Elements Of ElectromagneticsMechanical EngineeringISBN:9780190698614Author:Sadiku, Matthew N. O.Publisher:Oxford University PressMechanics of Materials (10th Edition)Mechanical EngineeringISBN:9780134319650Author:Russell C. HibbelerPublisher:PEARSONThermodynamics: An Engineering ApproachMechanical EngineeringISBN:9781259822674Author:Yunus A. Cengel Dr., Michael A. BolesPublisher:McGraw-Hill Education
- Control Systems EngineeringMechanical EngineeringISBN:9781118170519Author:Norman S. NisePublisher:WILEYMechanics of Materials (MindTap Course List)Mechanical EngineeringISBN:9781337093347Author:Barry J. Goodno, James M. GerePublisher:Cengage LearningEngineering Mechanics: StaticsMechanical EngineeringISBN:9781118807330Author:James L. Meriam, L. G. Kraige, J. N. BoltonPublisher:WILEY
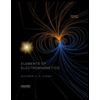
Elements Of Electromagnetics
Mechanical Engineering
ISBN:9780190698614
Author:Sadiku, Matthew N. O.
Publisher:Oxford University Press
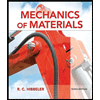
Mechanics of Materials (10th Edition)
Mechanical Engineering
ISBN:9780134319650
Author:Russell C. Hibbeler
Publisher:PEARSON
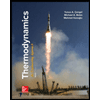
Thermodynamics: An Engineering Approach
Mechanical Engineering
ISBN:9781259822674
Author:Yunus A. Cengel Dr., Michael A. Boles
Publisher:McGraw-Hill Education
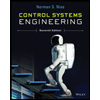
Control Systems Engineering
Mechanical Engineering
ISBN:9781118170519
Author:Norman S. Nise
Publisher:WILEY
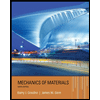
Mechanics of Materials (MindTap Course List)
Mechanical Engineering
ISBN:9781337093347
Author:Barry J. Goodno, James M. Gere
Publisher:Cengage Learning
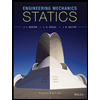
Engineering Mechanics: Statics
Mechanical Engineering
ISBN:9781118807330
Author:James L. Meriam, L. G. Kraige, J. N. Bolton
Publisher:WILEY