Lab 2 Typical Hydraulic Circuit (1)
pdf
keyboard_arrow_up
School
Centennial College *
*We aren’t endorsed by this school
Course
121
Subject
Mechanical Engineering
Date
Apr 3, 2024
Type
Pages
11
Uploaded by MegaRiverGull40
College Credits: Paul Bligdon Page 1 Industrial Hydraulics for Colleges Intro College Course Title: Lab Title: Typical Hydraulic Circuit Student Name: Section Number:
Instructor:
Paul Bligdon
College Credits: Paul Bligdon Page 2 Industrial Hydraulics for Colleges Intro Lab Exercise Typical Hydraulic Circuit •
This lab introduces the student to the Parker Hydraulic Training Bench and the installation of a typical hydraulic circuit on the benches’ “backboard”. Prior to the installation of the typical hydraulic circuit; the student will turn the hydraulic system “ON” and “Set” the Relief Valve to minimize the maximum pressure obt
ainable by the circuit and measure the rate of flow in gallons being produced by the hydraulic Pump. The student will then turn the training bench “off” and proceed to install the typical hydraulic circuit illustrated in Procedure 2. Once the circuit has been installed and verified by the instructor as correct, the student will proceed to operate the circuit as directed by the lab instructions while observing and recording circuit measurements and operational sequences. Upon completion of the lab, the student will be able to perform various hydraulic system calculation commonly required during the design stages of hydraulic circuitry. As part of the lab submission, the student will be required to draw the ANSI schematic for the lab circuit and answer the review questions
. •
Learning Outcomes •
Work in compliance with the Ontario //Health and Safety Act and the College’s Safety Standards during the performance of the lab exercise. •
Follow written technical instructions to perform work tasks •
Using standard ANSI symbols, sketch the schematic diagram of the lab’s hydraulic circuit •
Create a hydraulic symbol library in Auto Cad •
Using Auto Cad, draw the schematic diagram of the lab’s hydraulic circuit.
•
Troubleshoot circuit operation as required •
Observe the hydraulic principles of flow, pressure and resistance •
Perform hydraulic calculations based on data collected during the lab. •
Describe the basic operation and function of typical hydraulic components
College Credits: Paul Bligdon Page 3 Industrial Hydraulics for Colleges Intro Procedure 1: Setting the Relief Valve Note: The relief valve can be adjusted and set without the any additional circuitry being added to the bench 1.
Ensure that the PDP panel is in the “off” position and the Emergency Stop Button is “depressed” before proceeding 2.
Ensure that the Vent Shut-off Handle (yellow) is in its horizontal position. (zero pressure)
3.
Turn the Relief Valves Adjustment Knob fully counter clockwise. (lowest spring setting) 4.
Release the Emergency Stop Button
5.
Following the learned safety procedure, turn the PNP panel’s switch to the “ON” position
6.
Depress the Training Benches’ Start Push Button (|green)
7.
Record the pressure indicated on the System’s Main Pressure Gauge (PGM)
PSI . 8.
Turn the Vent Shut-off Handle (yellow) to its vertical position (maximum pressure) 9.
Slowly turn the Relief Valve’s A
djusting Knob clockwise. 10. Continue to turn the Relief Valve’s Adjusting Knob Before connecting the circuit, set the relief valve to its maximum setting based on the bench’s component configuration PSI = Note
: The pressure created by the circuit is being limited by the relief valve at this time as there is no flow path from the pump to the reservoir without going through the relief valve. As the adjusting Knob on the relief Valve is adjusted Clockwise, the resistance to flow through the valve increase. An increase in resistance causes an increase in the pressure required to push the fluid through the valve. 11.
Turn the Vent Shut-off Handle to the horizontal position 12.
Record the pressure seen on PGM. psi 13.
Depress the Training Benches Motor Stop Button (red) 14.
Depress the Emergency Stop Button 15.
Turn the PDP switch to the Off position
Your preview ends here
Eager to read complete document? Join bartleby learn and gain access to the full version
- Access to all documents
- Unlimited textbook solutions
- 24/7 expert homework help
College Credits: Paul Bligdon Page 4 Industrial Hydraulics for Colleges Intro Procedure 2: Assembling the circuit 16. Ensure that the PDP switch is in the “off” position and the Emergency Stop Button is “depressed” before proceeding to install your circuit. 17. Identify the areas of the hydraulic training bench referred to as the Back Board and the Power Unit 18. Using the ANSI schematic circuit located below, note that the POWER UNIT COMPONENTS are permanently configured and connected together. See the ANSI Schematic Drawing below to identify the typical hydraulic components which make up the POWER UNIT for the training bench. Yellow Handle
College Credits: Paul Bligdon Page 5 Industrial Hydraulics for Colleges Intro 19. List the names of the Power Unit Components in the space provide below. Note:
the only components that need to be connected by hydraulic conduit (hoses) are those components that are referred to as Control Components or Output Components which are both found on the Back Board of the training bench 20. Look inside the drawer on the training bench’s cupboard and locate and remove two Pressure Gauge and three Hydraulic Tees. 21. Install a hydraulic hose from the Pressure quick disconnect on the Manifold Block to the input connection of the flow meter located on the bench’s Back Board
22. Install a hydraulic hose from the output connection of the flow meter located on the bench’s Back Board to the Pressure port of the Solenoid Operated Directional Control Valve 23. Install a Hydraulic Tee on each of the connections of a Flow Control Valve located on the back board of the training bench 24. Install a Pressure Gauge on each of the Hydraulic Tees which you just installed on the Flow Control Valve. 25. Install a hydraulic hose from the “A” port of the Solenoid Operated Directional Control Valve to the inlet connection of the Flow Control Valve (ball side of the valve) 26. Install a hydraulic hose from the outlet connection of the Flow Control Valve to the piston end connection of the Cylinder 27. Install a hose from Cylinder’s rod side connection to the “B” port of the Solenoid Operated Directional Control Valve. 28. Install a hydraulic hose from the “T” port of the Solenoid Operated Directional Control Valve to the Tank quick disconnect connection on the Manifold Block 29.
Before Starting up your circuit, ask the instructor to verify your circuit is complete and correct
.
College Credits: Paul Bligdon Page 6 Industrial Hydraulics for Colleges Intro Procedure 3: Circuit operation 1. Ensure that the Vent Line Shut-off Handle (yellow) is in the passing position. (horizontal) 2. Ensure that the Directional Control V
alve’s Selector Switch is in the center position. 3. Turn the Flow Control Valve’s adjustment knob fully counterclockwise
4. Turn the PDP panel switch to the “On” position.
5. “Release” the Emergency stop button.
6. Depress the Motor Start Button (green) 7. Observe and record the pressure indicated on System’s Main Pressure Gauge (PGM) PSI 8. Turn the Vent Line Shut-off Handle (yellow) is in the non- passing position. (vertical) 9. Observe and record the pressure indicated on System’s Main Pressure Gauge (PGM) PSI 10. Turn the DCV Solenoid S
witch to the “A” position which will now direct the fluid from the pump through the Directional Control Valve into the piston side of cylinder to advance the cylinder
’s rod
. 11. Observe and record the rate at which the fluid is flowing as it leaves the pump and enters the cylinder as indicated on the system’s Flow Meter Gallons (pump’s delivery)
12. Because there is no weight (resistance) attached to the cylinder’s rod, there will be little or no pressure required to move the cylinder
’s
rod. 13. Observe and record the pressure required to move the cylinder rod as indicated on PG1. PSI (pressure to overcome resistance) 14. Why is the pressure seen on Main Pressure Gauge low while the cylinder
’s rod is advancing? 15. Observe and record the pressure seen on Main Pressure Gauge and the flow rate seen on the Flow meter , when the cylinder
’s rod is fully advanced (stopped) Gallons psi 16. What Power Unit component is limiting the maximum pressure in the circuit once the cylinder
’s rod is fully advanced?
Your preview ends here
Eager to read complete document? Join bartleby learn and gain access to the full version
- Access to all documents
- Unlimited textbook solutions
- 24/7 expert homework help
College Credits: Paul Bligdon Page 7 Industrial Hydraulics for Colleges Intro 17. What is the pressure setting of that component? 18. Turn the DCV Soleno
id Switch to the “B” position which will now direct the fluid from the pump through the Directional Control Valve into the rod side of cylinder to retract the cylinder’s rod.
19. Observe and record the rate at which the fluid is flowing as it leaves the pump and enters the cylinder as indicated on the system’s Flow Meter Gallons (pump’s delivery)
20. The cylinder rod has no weight attached; therefore, little of no resistance to motion. 21. . Observe and record the pressure required to move the cylinder rod as indicated on Main Pressure Gauge located on the Power Unit PSI (pressure to overcome resistance) 22. Why is the pressure seen on Main Pressure Gauge low while the cylinder’s rod is retracting? 23. Observe and record the pressure seen on Main Pressure Gauge and the flow rate seen on the Flow meter , when the cylinder’s rod is fully retracted (stopped)
Gallons psi 24. What Power Unit component is limiting the maximum pressure in the circuit once the cylinder’s rod is fully retracted? 25. What is the pressure setting of that component? 26. Turn the DCV solenoid selector switch to the “A” to advance the cylinder rod and then turn the DCV selector switch to the “B’ position
to retract the cylinder rod. 27. Compare the speed of the cylinder rod extending versus retracting even though the pump is pushing the cylinder in both directions with the same GPM 28. Which direction does the cylinder rod travel the fastest? Return the cylinder rod to the retracted position (back) and turn the DCV solenoid selector switch to the “mid” position. 29. Depress the Motor
’s
Stop pushbutton. 30. Depress the Emergency Stop pushbutton 31. Turn the PDP switch to the “Off” position
32. Disconnect your hydraulic circuit and place the hoses on the rack. 33. Apply “speedy dry” to any area in your hydraulic cell which ha
s fluid on the floor and sweep area if required. 34. Remove all books and papers from the cell 35. Wash your hands. 36. Answer and submit the lab assignment next week.
College Credits: Paul Bligdon Page 8 Industrial Hydraulics for Colleges Intro Summary •
Industrial hydraulic pumps are traditional driven by electric motors which they are coupled to by way of a flexible mechanical coupling •
Pumps produce flow determined by the displacement of the pump and the driven speed (rpm) •
Pumps produce flow to the circuit which is measured by a flow meter in gpm. •
The pressure in a hydraulic circuit is a by produce of the resistance to hydraulic fluid flow in the circuit •
Pressure is measure by a pressure gauge and displays its reading in psi •
The maximum system pressure obtainable by the circuit is limited by the system’s relief valve •
Linear actuators known as a cylinder convert the hydraulic energy ( flow and pressure) into linear mechanical energy •
Directional control valves are used to distribute the flow from the pump to the actuator so the direction of the actuator can be reversed •
The size of the circuit’
s connecting lines known as Conduit is determined by were the lines are placed in the circuit. (suction, working or return lines) •
The speed of a linear actuator is determined by how quickly the fluid can fill the volume of the cylinder Integrate the Concepts The hydraulic system’s flow meter indicates 25 gpm is flowing and the pressure gauges indicates 0 psi is present in the system. The production supervisor suggests that the trouble with the circuit is pump related. Is his suspicion true? Submission Requirements Your Submission should only include the following
: a. Scranton Card Review Questions 1 to 7
… (7 marks)
b. Lab Cover Page c. Pencil ANSI Circuit Schematic Drawing
…(3 marks)
d. Auto Cad drawing of the circuit
College Credits: Paul Bligdon Page 9 Industrial Hydraulics for Colleges Intro Review Questions 1. Hydraulic pumps convert what form of energy from the prime mover into fluid energy a. Electrical energy into fluid energy b. Solar energy into fluid energy c. Electrical energy to fluid energy d. Gas energy into fluid energy 2. Industrial hydraulic pumps create: a. Flow and pressure b. Pressure and resistance c. Flow only d. All of the above 3. What hydraulic line (conduit) in a hydraulic circuit is always the largest diameter? a. Suction line b. Working (pressure) line c. Return line d. All lines are the same diameter 4. The speed of a cylinder is determine by a. The pres
sure applied to the cylinder’s area
b. How quickly the cylinder’s volume can be filled
c. The amount of load attached to the cylinders rod d. The size of the Connecting Lines 5. A flow meter is used to measure: a. The pressure of the fluid at a specific point in the circuit b. The velocity at which the cylinder rod is travelling usually measured in Feet per Second c. The rate of flow of the fluid per unit of time usually measured in Gallons per Minute d. The load being applied to the cylinder measure in Pounds per Square Inch 6. Hydraulic cylinders convert: a. Electrical energy into mechanical energy b. Fluid energy into mechanical energy c. Rotary mechanical energy into linear mechanical energy d. Mechanical energy into fluid energy 7. What pressure is required to clamp the hydraulic cylinder at 3534 lbs of force? The cylinder’s piston is 1.5 inch in diameter
a. 20 psi b. 200 psi c. 2000 psi d. 20000 psi
Your preview ends here
Eager to read complete document? Join bartleby learn and gain access to the full version
- Access to all documents
- Unlimited textbook solutions
- 24/7 expert homework help
College Credits: Paul Bligdon Page 10 Industrial Hydraulics for Colleges Intro 8. What volume of oil to the cylinder is required to cause the cylinder to advance at a speed of 392 inches per minute if the piston diameter is 1.5 inches a. 0.3 gpm b. 3 gpm c. 30 gpm d. 300 gpm 9. How fast will that same cylinder retract if the gpm is the same as question 8 and the rod diameter is 1 inch a. 7.06 inches per minute b. 70.6 inches per minute c. 706.0 inches per minute d. 7060 inches per minute 10. Calculate the displacement of the hydraulic pump if the drive rpm is 1800 and the flow rate is 4 gpm a. 0.0513 cu. in b. 0.513 cu.in c. 5.13 cu. in d. 51.3 cu in 11. Calculate the hydraulic horsepower produced by the pump when the flow rate is 4 gpm and the maximum pressure is 1200 psi a. 0.28 Hp b. 2.8 Hp c. 28. Hp d. 280 Hp 12. Calculate the horsepower require to drive the pump in question 11 if the pump’s efficiency is 85 percent a. .329 Hp b. 3.29 Hp c. 32.9 Hp d. 329. Hp 13. Calculate the amount of wasted energy in the form of heat (BTU/hr.) being generated when the pump
’s full displacement is returning to tank through the relief valve there by not going any Work. Pump’s flow rate is 4gpm and the relief valve is set at 1200 psi a. 7.20 BTU b. 72. 0 BTU c. 720 BTU d. 7200 BTU
College Credits: Paul Bligdon Page 11 Industrial Hydraulics for Colleges Intro 14. Industrial hydraulics; as discovered by Pascal, relates to the use of fluids in a confined space to be used for: a. Transmitting power b. Multiplying force c. Modifying motion d. All of the above Definitions: Sketch: Using a Pencil and a Ruler, sketch the schematic circuit diagram used during this lab. Use the schematic drawing supplied by the instructor as a guide. Do not attach the sketch or drawing to the Scantron Card. Drawing: Using Auto Cad, draw the schematic circuit diagram used during this lab. Use the schematic drawing supplied by the instructor as a guide. Do not attach drawing to the Scantron Card
Related Documents
Related Questions
Idc about bartleby rules answer it all
Strictly no plagiarism i will check 3times
Asap
Do it fast if u want helpful rating
arrow_forward
Problem 3: A small gearing system in your brand-new 3D printer fails as you were printing,
leading to an overload in the motor and a fire in your home. The fire spreads, burning half of
Everglades National Park in the worst environmental disaster in US history.
The printer company blames you! Stating that you must have been misusing the printer some-
how. Use your engineering knowledge to "show those jerks you mean business!"
You investigate and find a serial number on the gears and type it into Google, finding the
company that manufactures the gears. Their website provides some info that this series of gear is
made from AISI 4340 steel and the yield strength is 125 kpsi.
Assuming each gear tooth acts as a small cantilever, prove to the 3D printer company that they
are liable for the fire.
oct
#
Gear Information
Gear radius (r): 1.00 in
Tooth length (1): 0.15 in
Tooth height (h): 0.15 in
Tooth thickness (b): 0.1 in
Angular velocity (w): 0.1 rad/s
Motor Information
Power (H): 0.009 hp
1…
arrow_forward
Help!!! Please answer part B correctly!!! Please
arrow_forward
Assignment Booklet 4B
ce 24: Module 4
6 Identify the safety features shown in this automobile from the following list. Place
your answers in the blank spaces given.
• bumper
• hood
• crumple zones
• roll cage
• side-impact beams
Return to page 75 of the Student Module Booklet and begin Lesson 2.
For questions 7 to 10, read each question carefully. Decide which of the choices BEST
completes the statement or answers the question. Place your answer in the blank
space given.
7. According to Transport Canada, how many Canadians owe their lives to
seat belts between 1990 and 2000?
A. 690
В. 1690
С. 1960
D. 11 690
8. By what percent is the webbing of a seat belt designed to stretch to help
absorb energy in a collision?
A. 0%
B. 5-10%
C. 10-15%
D. 15-20%
9. What is the level of seat belt use in Alberta?
A. 90%
В. 70%
С. 50%
D. 30%
Teacher
arrow_forward
What type of CAD software could be used to test the medical scaffold made out of TPU that will be printed using stereolithography (SLA). The medical scaffold will be surgically implanted around the pancreas to enable the infusion of Islet beta cells which are encapsulated within the scaffold to provide diabetic patients with a functional pancreas.
E.g. hydrostatic pressure testing/torsion tests
What other type of physical testings should be taken? E.g. Brunauer–Emmett–Teller (BET) test to check the porosity of the material
arrow_forward
What do you know about the discipline of mechanical engineering's Pro/Engineer program? What are the names of three computer-aided design (CAD) programs?
arrow_forward
4
arrow_forward
people in a collision.
* Decide whether each of the following statements is true (T) or false (F). Place your
answer in the blank space provided.
a. Restraining features operate continuously while you are driving.
b. Operational features hold vehicle occupants in place.
C. Brakes are an example of a structural feature.
d. Crumple zones are examples of operational features.
e. An air bag is an example of a restraining feature.
5. Crumple zones increase the
occupants and the interior of the vehicle.
of the collision between the
arrow_forward
A person is required to perform a lifting task. After conducting the analysis of the task shown below using the NIOSH lifting guidelines you determined that the task need to be redesigned to be acceptable. Unfortunately, the only factor that you can modify is the frequency of lifts per minute. What is the maximum number of lifts per minute that need to be used for this task so the NIOSH lifting guidelines are not exceeded?
ANSWER: ________________
arrow_forward
Question 4
A RWD Formula SAE car is given with the following information
m = 600 lbm (including the driver), 1=64.0 inches
the CG is located at a1 = 0.6 l, h = 12.8 inches
Determine the following with all resistances ignored
a) Normal force (lbf) at the front tires if accelerating at a4 = 20 ft/sec?
b) Normal force at the rear tires if accelerating at aa
20 ft/sec2
c) Total driving force if accelerating at a4 = 20 ft/sec2
d) Total braking force if the vehicle decelerates at ag = 10 ft/sec?
arrow_forward
Assignment 1: Killer Robot
Summary of the case: Bart Matthews, a robot operator at Cybernetics, Inc., has been killed by an out-
of-control robot named Robbie. The creator of the robot, Silicon Technologies, is also in a tight
financial position and had hoped that the robot would put the company back on its feet. It has been
determined that several situations contributed to the death of Matthews:
1. Improper methodology was used in developing the software.
2. Testing of the software was faked.
3. The company pressured Robbie's creators to by-pass testing.
4. Part of the software used in the robot was stolen from another vendor's application.
5. The programmer did not understand or know the code which he used.
6. Security measures used were illegal, and therefore all information gathered in regard to the case
might not be permissible in court.
7. The project leader did not understand or use proper design methodologies.
8. The end-user interface was designed improperly.
Questions for…
arrow_forward
SEE MORE QUESTIONS
Recommended textbooks for you
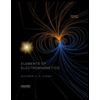
Elements Of Electromagnetics
Mechanical Engineering
ISBN:9780190698614
Author:Sadiku, Matthew N. O.
Publisher:Oxford University Press
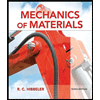
Mechanics of Materials (10th Edition)
Mechanical Engineering
ISBN:9780134319650
Author:Russell C. Hibbeler
Publisher:PEARSON
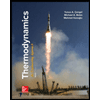
Thermodynamics: An Engineering Approach
Mechanical Engineering
ISBN:9781259822674
Author:Yunus A. Cengel Dr., Michael A. Boles
Publisher:McGraw-Hill Education
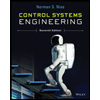
Control Systems Engineering
Mechanical Engineering
ISBN:9781118170519
Author:Norman S. Nise
Publisher:WILEY
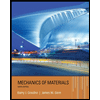
Mechanics of Materials (MindTap Course List)
Mechanical Engineering
ISBN:9781337093347
Author:Barry J. Goodno, James M. Gere
Publisher:Cengage Learning
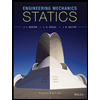
Engineering Mechanics: Statics
Mechanical Engineering
ISBN:9781118807330
Author:James L. Meriam, L. G. Kraige, J. N. Bolton
Publisher:WILEY
Related Questions
- Idc about bartleby rules answer it all Strictly no plagiarism i will check 3times Asap Do it fast if u want helpful ratingarrow_forwardProblem 3: A small gearing system in your brand-new 3D printer fails as you were printing, leading to an overload in the motor and a fire in your home. The fire spreads, burning half of Everglades National Park in the worst environmental disaster in US history. The printer company blames you! Stating that you must have been misusing the printer some- how. Use your engineering knowledge to "show those jerks you mean business!" You investigate and find a serial number on the gears and type it into Google, finding the company that manufactures the gears. Their website provides some info that this series of gear is made from AISI 4340 steel and the yield strength is 125 kpsi. Assuming each gear tooth acts as a small cantilever, prove to the 3D printer company that they are liable for the fire. oct # Gear Information Gear radius (r): 1.00 in Tooth length (1): 0.15 in Tooth height (h): 0.15 in Tooth thickness (b): 0.1 in Angular velocity (w): 0.1 rad/s Motor Information Power (H): 0.009 hp 1…arrow_forwardHelp!!! Please answer part B correctly!!! Pleasearrow_forward
- Assignment Booklet 4B ce 24: Module 4 6 Identify the safety features shown in this automobile from the following list. Place your answers in the blank spaces given. • bumper • hood • crumple zones • roll cage • side-impact beams Return to page 75 of the Student Module Booklet and begin Lesson 2. For questions 7 to 10, read each question carefully. Decide which of the choices BEST completes the statement or answers the question. Place your answer in the blank space given. 7. According to Transport Canada, how many Canadians owe their lives to seat belts between 1990 and 2000? A. 690 В. 1690 С. 1960 D. 11 690 8. By what percent is the webbing of a seat belt designed to stretch to help absorb energy in a collision? A. 0% B. 5-10% C. 10-15% D. 15-20% 9. What is the level of seat belt use in Alberta? A. 90% В. 70% С. 50% D. 30% Teacherarrow_forwardWhat type of CAD software could be used to test the medical scaffold made out of TPU that will be printed using stereolithography (SLA). The medical scaffold will be surgically implanted around the pancreas to enable the infusion of Islet beta cells which are encapsulated within the scaffold to provide diabetic patients with a functional pancreas. E.g. hydrostatic pressure testing/torsion tests What other type of physical testings should be taken? E.g. Brunauer–Emmett–Teller (BET) test to check the porosity of the materialarrow_forwardWhat do you know about the discipline of mechanical engineering's Pro/Engineer program? What are the names of three computer-aided design (CAD) programs?arrow_forward
- 4arrow_forwardpeople in a collision. * Decide whether each of the following statements is true (T) or false (F). Place your answer in the blank space provided. a. Restraining features operate continuously while you are driving. b. Operational features hold vehicle occupants in place. C. Brakes are an example of a structural feature. d. Crumple zones are examples of operational features. e. An air bag is an example of a restraining feature. 5. Crumple zones increase the occupants and the interior of the vehicle. of the collision between thearrow_forwardA person is required to perform a lifting task. After conducting the analysis of the task shown below using the NIOSH lifting guidelines you determined that the task need to be redesigned to be acceptable. Unfortunately, the only factor that you can modify is the frequency of lifts per minute. What is the maximum number of lifts per minute that need to be used for this task so the NIOSH lifting guidelines are not exceeded? ANSWER: ________________arrow_forward
- Question 4 A RWD Formula SAE car is given with the following information m = 600 lbm (including the driver), 1=64.0 inches the CG is located at a1 = 0.6 l, h = 12.8 inches Determine the following with all resistances ignored a) Normal force (lbf) at the front tires if accelerating at a4 = 20 ft/sec? b) Normal force at the rear tires if accelerating at aa 20 ft/sec2 c) Total driving force if accelerating at a4 = 20 ft/sec2 d) Total braking force if the vehicle decelerates at ag = 10 ft/sec?arrow_forwardAssignment 1: Killer Robot Summary of the case: Bart Matthews, a robot operator at Cybernetics, Inc., has been killed by an out- of-control robot named Robbie. The creator of the robot, Silicon Technologies, is also in a tight financial position and had hoped that the robot would put the company back on its feet. It has been determined that several situations contributed to the death of Matthews: 1. Improper methodology was used in developing the software. 2. Testing of the software was faked. 3. The company pressured Robbie's creators to by-pass testing. 4. Part of the software used in the robot was stolen from another vendor's application. 5. The programmer did not understand or know the code which he used. 6. Security measures used were illegal, and therefore all information gathered in regard to the case might not be permissible in court. 7. The project leader did not understand or use proper design methodologies. 8. The end-user interface was designed improperly. Questions for…arrow_forward
arrow_back_ios
arrow_forward_ios
Recommended textbooks for you
- Elements Of ElectromagneticsMechanical EngineeringISBN:9780190698614Author:Sadiku, Matthew N. O.Publisher:Oxford University PressMechanics of Materials (10th Edition)Mechanical EngineeringISBN:9780134319650Author:Russell C. HibbelerPublisher:PEARSONThermodynamics: An Engineering ApproachMechanical EngineeringISBN:9781259822674Author:Yunus A. Cengel Dr., Michael A. BolesPublisher:McGraw-Hill Education
- Control Systems EngineeringMechanical EngineeringISBN:9781118170519Author:Norman S. NisePublisher:WILEYMechanics of Materials (MindTap Course List)Mechanical EngineeringISBN:9781337093347Author:Barry J. Goodno, James M. GerePublisher:Cengage LearningEngineering Mechanics: StaticsMechanical EngineeringISBN:9781118807330Author:James L. Meriam, L. G. Kraige, J. N. BoltonPublisher:WILEY
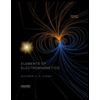
Elements Of Electromagnetics
Mechanical Engineering
ISBN:9780190698614
Author:Sadiku, Matthew N. O.
Publisher:Oxford University Press
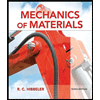
Mechanics of Materials (10th Edition)
Mechanical Engineering
ISBN:9780134319650
Author:Russell C. Hibbeler
Publisher:PEARSON
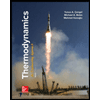
Thermodynamics: An Engineering Approach
Mechanical Engineering
ISBN:9781259822674
Author:Yunus A. Cengel Dr., Michael A. Boles
Publisher:McGraw-Hill Education
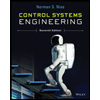
Control Systems Engineering
Mechanical Engineering
ISBN:9781118170519
Author:Norman S. Nise
Publisher:WILEY
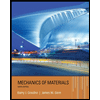
Mechanics of Materials (MindTap Course List)
Mechanical Engineering
ISBN:9781337093347
Author:Barry J. Goodno, James M. Gere
Publisher:Cengage Learning
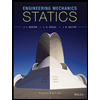
Engineering Mechanics: Statics
Mechanical Engineering
ISBN:9781118807330
Author:James L. Meriam, L. G. Kraige, J. N. Bolton
Publisher:WILEY