Lab 4 Series and Parallel Circuits with data
doc
keyboard_arrow_up
School
Centennial College *
*We aren’t endorsed by this school
Course
122
Subject
Mechanical Engineering
Date
Apr 3, 2024
Type
doc
Pages
11
Uploaded by MegaRiverGull40
Industrial Hydraulics for Colleges Industrial Hydraulics for Colleges Lab 3
Lab 3
College Course Title: Lab Title: Series and Parallel Circuits Student Name: Section Number:
Instructor:
Paul Bligdon
College Credits: Paul Bligdon
Page 1
Industrial Hydraulics for Colleges Industrial Hydraulics for Colleges Lab 3
Lab 3
Lab Exercise 2a
Series Circuit
When the resistances (components) in a hydraulic circuit are connected in such a way that only allows a single flow path from the pump through the remainder of the circuit as the fluid returns back to tank, the components are said to be connected in series with each other
. The resistance created by each component in the fluids flow path accumulates creating a total resistance to flow as seen on the pressure gauge at the pump’s outlet. This pressure gauge is referred to as the system’s pressure gauge (PG main). A pressure gauges may be placed before each component and would indicate the
pressure required to push the fluid through that individual component and any additional components downstream of it. The highest pressure in the circuit is always seen at the pump’s outlet. See the example illustration below:
College Credits: Paul Bligdon
Page 2
Industrial Hydraulics for Colleges Industrial Hydraulics for Colleges Lab 3
Lab 3
Learning Outcomes
Work in compliance with the Ontario //Health and Safety Act and the College’s
Safety Standards during the performance of the lab exercise.
Follow written technical instructions to perform work tasks
Using standard ANSI symbols, sketch the schematic diagram of the lab’s hydraulic
circuit
Identify that pressure is proportional to resistance downstream of the pump
Identify that the flow rate remains a constant as resistance increases in a series
circuit
Identify that the flow rate in a parallel circuit divides proportional to the resistance
in each leg of the circuit
Identify the hydraulic components used in both a series and parallel circuit
Using Auto Cad, draw the schematic diagram of the lab’s hydraulic circuit.
Troubleshoot circuit operation as required
Procedure 1a: Setting the Relief Valve
Note: The relief valve can be adjusted and set without any additional
circuitry being connected on the bench 1.
Ensure that the PDP panel is in the “off” position and the Emergency Stop Button
is “depressed” before proceeding 2.
Ensure that the Vent Shut-off Handle (yellow) is in its horizontal position. (zero
pressure)
3.
Turn the Relief Valves Adjustment Knob fully counter clockwise. (lowest spring
setting)
4.
Release the Emergency Stop Button
5.
Following the learned safety procedure, turn the PNP panel’s switch to the “ON”
position
6.
Depress the Training Benches’ Start Push Button (|green)
7.
Record the pressure indicated on the System’s Main Pressure Gauge (PGM)
0 PSI
.
8.
Turn the Vent Shut-off Handle (yellow) to its vertical position (maximum pressure)
9.
Slowly turn the Relief Valve’s Adjusting Knob clockwise.
College Credits: Paul Bligdon
Page 3
Your preview ends here
Eager to read complete document? Join bartleby learn and gain access to the full version
- Access to all documents
- Unlimited textbook solutions
- 24/7 expert homework help
Industrial Hydraulics for Colleges Industrial Hydraulics for Colleges Lab 3
Lab 3
10. Set the relief valve to its maximum setting based on the bench’s component configuration PSI = .
11.
Turn the Vent Shut-off Handle to the horizontal position
12.
Record the pressure seen on PGM.
0 psi
13.
Depress the Training Benches Motor Stop Button (red)
14.
Depress the Emergency Stop Button
15.
Turn the PDP switch to the Off position
Procedure 2a: Assembling the series circuit
1.
Ensure that the PDP panel is in the “off” position and the Emergency Stop Button is
“depressed” before proceeding to assemble your circuit.
2.
Using the ANSI schematic circuit as a guide, connect the circuit
on the training bench.
Remember; the Power Unit components are permanently configured and connected,
therefore only the “Backboard” components beginning at the pressure manifold need to be
connected by you
College Credits: Paul Bligdon
Page 4
Orifice 2
PG 3
FM 1
Orifice 1
PG 2
PG 1
1500 psi
4 gpm
Industrial Hydraulics for Colleges Industrial Hydraulics for Colleges Lab 3
Lab 3
Procedure 3a: Series circuit operation
1.
Ensure that the Vent handle is in the passing position. (horizontal)
2.
Turn both Adjustable Orifices ( orifice 1 and 2) completely passing( counter clockwise)
3.
Turn the PDP panel switch to the “On” position.
4.
“Release” the Emergency Stop Button.
5.
Depress the Motor Start Button
6.
Turn the Vent Handle to the vertical position
7.
Turn the appropriate Adjustable Orifices until the various pressures are indicated on the
pressure gauges as illustrated in the table below
8.
Record all other data observed into the table under the appropriate headings. Note:
The BULLET (•) indicates which adjustable orifice to turn for each data column. FP
means fully passing (open) and NP is non- passing. (closed) Same means leave setting at
previous setting.
Pump
Delivery
(gpm)
Orifice 1
Orifice
2
Flow
Meter
(gpm)
PG M
(psi)
PG 1
(psi)
PG 2
(psi)
Relief Valve
(calculated)
(gpm)
4
FP
FP
400
300
215
4
FP
•
400
300
215
4
FP
•
600
500
429
4
•
Same
800
660
600
4
•
Same
1000
760
695
9.
Turn the Vent handle to the passing position (horizontal)
10. Depress the Motor’s stop pushbutton.
11. Depress the Emergency stop pushbutton
12. Turn the PDP switch to the “Off” position
13. Disconnect your hydraulic circuit and place the hoses on the rack.
College Credits: Paul Bligdon
Page 5
Industrial Hydraulics for Colleges Industrial Hydraulics for Colleges Lab 3
Lab 3
Lab Exercise 2b
Parallel Circuit
An inherent characteristic of liquids is that they always take the path of least resistance.
Thus when two or more alternative flow paths are available for the fluid to return to tank,
pressure will only build up to the pressure required to push the fluid through the path of
least resistance. If two on more flow paths have equal resistance to flow then the fluid
would divide equally through each path. In a parallel circuit the flow always divides based
on the resistance in each path. See the illustration below:
College Credits: Paul Bligdon
Page 6
Your preview ends here
Eager to read complete document? Join bartleby learn and gain access to the full version
- Access to all documents
- Unlimited textbook solutions
- 24/7 expert homework help
Industrial Hydraulics for Colleges Industrial Hydraulics for Colleges Lab 3
Lab 3
Procedure 1b: Assembling the parallel circuit
1.
Ensure that the PDP panel is in the “off” position and the Emergency stop button is
“depressed” before proceeding to assemble your circuit.
2.
Using the ANSI schematic circuit as a guide, connect the circuit on the training bench.
Remember; the Power Unit components are permanently configured and connected,
therefore only the “Backboard” components beginning with the pressure manifold need to
be connected by you.
College Credits: Paul Bligdon
Page 7
FM 2
Orifice 2
Orifice 1
FM 1
PG 2
PG 1
PG 3
1500 psi
4 gpm
Industrial Hydraulics for Colleges Industrial Hydraulics for Colleges Lab 3
Lab 3
Procedure 2b: Parallel circuit operation
Turn the appropriate Adjustable Orifices until the various flow rates are indicated on the flow
meters as illustrated in the table below. Record all other data observed into the table under the
appropriate headings. Note:
The BULLET (•) indicates which adjustable orifice to turn for each data column. FP
means fully passing (open) and NP is non- passing. (closed) Same means leave setting at
previous setting
Pump
Delivery
(gpm)
Orifice
1
Orifice
2
PGM
(psi)
PG 1
(psi)
PG 2
(psi)
Flow
Meter
1
(gpm)
Flow
Meter
2
(gpm)
Relief Valve (calculated)
(gpm)
4 FP
FP 150
0
22
2.75
1.5
4 FP
•
175
0
44
3.5
1
4 •
FP
250
0
75
1
3
4 •
•
750
0
45
2
2
4 NP
NP
150
0
0
0
0
0
4.
Turn the Vent handle to the passing position (horizontal)
5.
Depress the Motor’s stop pushbutton.
6.
Depress the Emergency stop pushbutton
7.
Turn the PDP switch to the “Off” position
8.
Disconnect your hydraulic circuit and place the hoses on the rack
College Credits: Paul Bligdon
Page 8
Industrial Hydraulics for Colleges Industrial Hydraulics for Colleges Lab 3
Lab 3
Summary
Pressure increases as resistance to flow increases
In a series circuit, pressure is equal to the resistance of flow downstream
In a series circuit, the resistance to flow hence the pressure is equal to the accumulation of resistance between a point and the tank
Flow Rate in a series circuit is equal in all portions of the circuit
When there is flow through a component, a pressure differential from inlet to outlet is created. This differential pressure across components is know as a “pressure drop”
Flow divides in the various legs of a parallel circuit based resistance
The pressure drop across each leg of a parallel circuit are equal
Integrate the Concepts
How is the hydraulic system’s relief valve connected in the circuit. Submission Requirements Your Submission should only include the following
:
a.
Scranton Card Review Questions 1 to 7… (7 marks)
b.
Lab Cover Page
c.
Pencil ANSI Circuit Schematic Drawing of each circuit…(3 marks)
d.
Auto Cad drawing of each circuit
College Credits: Paul Bligdon
Page 9
Your preview ends here
Eager to read complete document? Join bartleby learn and gain access to the full version
- Access to all documents
- Unlimited textbook solutions
- 24/7 expert homework help
Industrial Hydraulics for Colleges Industrial Hydraulics for Colleges Lab 3
Lab 3
Review Questions
1.
What hydraulic component creates flow in the hydraulic circuit?
a.
Prime mover.
b.
Pump
c.
Adjustable orifice.
d.
Check Valve
2.
What property of hydraulic fluid allows the creation of pressure within the fluid?
a.
Lubrication
b.
Viscosity
c.
Non Compressibility
d.
Oxidation Inhibitors
3.
In a Series Circuit, the Flow Rate (gallons per minute) throughout the circuit:
a.
Increases as resistance increases
b.
Decreases as resistance increases
c.
Remains the same throughout the circuit
d.
Increase or decreases as velocity changes
4.
Pump’s delivery (flow rate) in all hydraulic circuits is measured using what component?
a.
Flow Control Valve
b.
Pressure Gauge
c.
Flow Meter
d.
Vacuum Gauge
5.
What statement describes the characteristics of fluid when flowing through an orifice
which is connected in a series with other components
a.
Flow rate remains the same but fluid velocity may change
b.
Pressure at the inlet to the orifice is always greater than pressure at its outlet
c.
Pressure at the inlet of the orifice is determined by the resistance to flow of the
orifice
d.
All of the above
6.
Hydraulic fluid will: a.
Will always flow in the part of the circuit with the highest resistance
b.
Will always divide based on the resistance
c.
Will only flow through components connected in parallel
d.
Will only flow through components connected in series
7.
The relief valve is always connected in with the pump.
a.
In series b.
In parallel c.
In either series or parallel
d.
All of the above
College Credits: Paul Bligdon
Page 10
Industrial Hydraulics for Colleges Industrial Hydraulics for Colleges Lab 3
Lab 3
College Credits: Paul Bligdon
Page 11
Related Documents
Related Questions
a)Determine the relationship between the air pressure in the tank and the maximum height to which the water fountain can rise above the discharge nozzle.
b)If a water fountain height of 10 mm is desired, what air pressure should be used?
arrow_forward
2
arrow_forward
please find the solution
arrow_forward
please help me with these questions ,i will be very very appreciate!!!!Please do not copy other's work
arrow_forward
Homework Parts A-C and label them
QUESTION: In Tinyland, houses are less than a foot high! The rainfall is laminar! The drainpipe in the figure is only 2 mm in diameter.
Part (A) - When the gutter is full, what is the rate of draining?
Part (B) - The gutter is designed for a sudden rainstorm of up to 4 mm per hour. For this condition, what is the maximum roof area that can be drained successfully
Part (C) What is Red? Neglect minor losses.
HINT : 4mm PER HOUR ***
arrow_forward
Hydraulic circuits use schematic drawings to
1-Make untrained and improper knowledgeable person to realize
2-To have good looking and attractive
3-Simplify components function in details
4-Make the drawing look impressive
arrow_forward
This is a hydraulics lab question
Please answer question 6 ASAP
Thank you in advance
arrow_forward
A hydraulic cylinder has these specs:
Bore: 3.5"
Stroke: 20"
Rod diameter: 1.25"
Pressure: 1800 PSI
Flow rate at cylinder: 4 GPM
a. What is the extension area of this cylinder?
b. What is the retraction area of this cylinder?
c. What is the extending force of the cylinder?
d. What is the retraction force of the cylinder?
e. What Volume of fluid is used when extending the cylinder?
f. What is the speed of extension for this cylinder (in/min)?
arrow_forward
Need only a handwritten solution only (not a typed one).
arrow_forward
: By Bligh's and Lane's theory For the hydraulic structures shown below calculate 1- Sketch the HGL from U/s to D/s 2- Fine the uplift pressure from at key point 3- Find the thickness of floor at point A&B 4m 15m 10m 10m 6m 8m 35 m
arrow_forward
engineering economics course
QUESTION:
Freeport McMoran purchased two model MTVS peristaltic pumps (to inject sulfuric acid and King Lee antiscalant) for use at its nanofiltration water conditioning plant. The cost of the pumps was $950 each. If the chemical cost is $11 per day, determine the equivalent cost per month at an interest rate of 12% per year, compounded monthly. Assume 30 days per month and a 3-year pump life. Notes: On the first page of your answer sheet, write down your group number (Group A, Group B, Group C......etc ), student names, and submit your file by uploading it here.
arrow_forward
Match each of the steady-flow engineering devices with its best description:
Question 1 options:
A device that increases the pressure of a fluid by slowing it down
A device where two fluids exchange heat without mixing
A device that increases the velocity of a fluid at the expense of pressure
Increases pressure of gasses and vapors
Increases pressure for liquids
Increases the pressure of a gas slightly and is mainly used to mobilize a gas
Produces shaft work
A device where two or more fluids are mixed
1.
Turbine
2.
Fan
3.
Compressor
4.
Pump
5.
Heat exchanger
6.
Mixing chamber
7.
Nozzle
8.
Diffuser
arrow_forward
Task 1
You are employed as a mechanical engineer within an unnamed research center, specializing in the development.
of innovative air conditioning systems. Your division is tasked with providing computer-based modeling and
design solutions using computational fluid dynamics through ANSYS software. Your primary responsibilities.
involve the analysis of horizontal channel dynamics to meet specific criteria. Under the guidance of your
immediate supervisor, you have been assigned unique responsibilities within an ongoing project. As a member of
the research team, your role includes constructing an appropriate model and executing a sequence of simulation.
iterations to explore and enhance channel performance. Figure 1 provides a visualization of the horizontal channel
under consideration. Consider 2D, incompressible, steady flowin a horizontal channel at a Reynolds number of
150. The schematic below illustrates the channel flow, not drawn to scale. For simplicity, neglect gravity. The…
arrow_forward
Course name: fluid mechanics
Course code: CHE-311
Division: Petroleum Engineering
Ministry of Higher Education and Scientific Research
Sabratha Universit
Faculty of Engineering Sabratha-Department of Petroleum
Engineering
01/a) Water leaves the 25 mm diameter nozzle of a fire hose at a velocity of 25 m/s. What
will be the reaction force at the nozzle which the fireman will need to counterbalance?
wat 1000 Kg/m'.
هائي أمر ولا
A closed tank contains 0.7 m of mercury, 2 m of water. 2.8 m of oil of sp.gr-0.8 and air
space a bove the oil. If the pressure at the bottom of the tank is 3.21 bar gauge. What should
be the reading of mechanical gauge at the top of the tank?, P mercurs 13600 Kg/m³, pwater
1000 Kg/m.
Exam: Final Exam
Duration: 165 min
Semester: autumn (2022)
024) Water flows from a tap at a pressure of 250 kN/m² above atmospheric. What is the
velocity of the jet if frictional effects are neglected?
buid dynamic and flow in pipe, Calculate the fraction factor and head loss?…
arrow_forward
what are the four primary functions of a hydraulic fluid
arrow_forward
SEE MORE QUESTIONS
Recommended textbooks for you
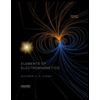
Elements Of Electromagnetics
Mechanical Engineering
ISBN:9780190698614
Author:Sadiku, Matthew N. O.
Publisher:Oxford University Press
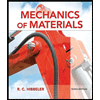
Mechanics of Materials (10th Edition)
Mechanical Engineering
ISBN:9780134319650
Author:Russell C. Hibbeler
Publisher:PEARSON
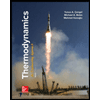
Thermodynamics: An Engineering Approach
Mechanical Engineering
ISBN:9781259822674
Author:Yunus A. Cengel Dr., Michael A. Boles
Publisher:McGraw-Hill Education
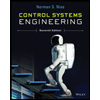
Control Systems Engineering
Mechanical Engineering
ISBN:9781118170519
Author:Norman S. Nise
Publisher:WILEY
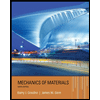
Mechanics of Materials (MindTap Course List)
Mechanical Engineering
ISBN:9781337093347
Author:Barry J. Goodno, James M. Gere
Publisher:Cengage Learning
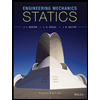
Engineering Mechanics: Statics
Mechanical Engineering
ISBN:9781118807330
Author:James L. Meriam, L. G. Kraige, J. N. Bolton
Publisher:WILEY
Related Questions
- a)Determine the relationship between the air pressure in the tank and the maximum height to which the water fountain can rise above the discharge nozzle. b)If a water fountain height of 10 mm is desired, what air pressure should be used?arrow_forward2arrow_forwardplease find the solutionarrow_forward
- please help me with these questions ,i will be very very appreciate!!!!Please do not copy other's workarrow_forwardHomework Parts A-C and label them QUESTION: In Tinyland, houses are less than a foot high! The rainfall is laminar! The drainpipe in the figure is only 2 mm in diameter. Part (A) - When the gutter is full, what is the rate of draining? Part (B) - The gutter is designed for a sudden rainstorm of up to 4 mm per hour. For this condition, what is the maximum roof area that can be drained successfully Part (C) What is Red? Neglect minor losses. HINT : 4mm PER HOUR ***arrow_forwardHydraulic circuits use schematic drawings to 1-Make untrained and improper knowledgeable person to realize 2-To have good looking and attractive 3-Simplify components function in details 4-Make the drawing look impressivearrow_forward
- This is a hydraulics lab question Please answer question 6 ASAP Thank you in advancearrow_forwardA hydraulic cylinder has these specs: Bore: 3.5" Stroke: 20" Rod diameter: 1.25" Pressure: 1800 PSI Flow rate at cylinder: 4 GPM a. What is the extension area of this cylinder? b. What is the retraction area of this cylinder? c. What is the extending force of the cylinder? d. What is the retraction force of the cylinder? e. What Volume of fluid is used when extending the cylinder? f. What is the speed of extension for this cylinder (in/min)?arrow_forwardNeed only a handwritten solution only (not a typed one).arrow_forward
- : By Bligh's and Lane's theory For the hydraulic structures shown below calculate 1- Sketch the HGL from U/s to D/s 2- Fine the uplift pressure from at key point 3- Find the thickness of floor at point A&B 4m 15m 10m 10m 6m 8m 35 marrow_forwardengineering economics course QUESTION: Freeport McMoran purchased two model MTVS peristaltic pumps (to inject sulfuric acid and King Lee antiscalant) for use at its nanofiltration water conditioning plant. The cost of the pumps was $950 each. If the chemical cost is $11 per day, determine the equivalent cost per month at an interest rate of 12% per year, compounded monthly. Assume 30 days per month and a 3-year pump life. Notes: On the first page of your answer sheet, write down your group number (Group A, Group B, Group C......etc ), student names, and submit your file by uploading it here.arrow_forwardMatch each of the steady-flow engineering devices with its best description: Question 1 options: A device that increases the pressure of a fluid by slowing it down A device where two fluids exchange heat without mixing A device that increases the velocity of a fluid at the expense of pressure Increases pressure of gasses and vapors Increases pressure for liquids Increases the pressure of a gas slightly and is mainly used to mobilize a gas Produces shaft work A device where two or more fluids are mixed 1. Turbine 2. Fan 3. Compressor 4. Pump 5. Heat exchanger 6. Mixing chamber 7. Nozzle 8. Diffuserarrow_forward
arrow_back_ios
SEE MORE QUESTIONS
arrow_forward_ios
Recommended textbooks for you
- Elements Of ElectromagneticsMechanical EngineeringISBN:9780190698614Author:Sadiku, Matthew N. O.Publisher:Oxford University PressMechanics of Materials (10th Edition)Mechanical EngineeringISBN:9780134319650Author:Russell C. HibbelerPublisher:PEARSONThermodynamics: An Engineering ApproachMechanical EngineeringISBN:9781259822674Author:Yunus A. Cengel Dr., Michael A. BolesPublisher:McGraw-Hill Education
- Control Systems EngineeringMechanical EngineeringISBN:9781118170519Author:Norman S. NisePublisher:WILEYMechanics of Materials (MindTap Course List)Mechanical EngineeringISBN:9781337093347Author:Barry J. Goodno, James M. GerePublisher:Cengage LearningEngineering Mechanics: StaticsMechanical EngineeringISBN:9781118807330Author:James L. Meriam, L. G. Kraige, J. N. BoltonPublisher:WILEY
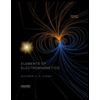
Elements Of Electromagnetics
Mechanical Engineering
ISBN:9780190698614
Author:Sadiku, Matthew N. O.
Publisher:Oxford University Press
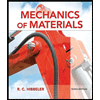
Mechanics of Materials (10th Edition)
Mechanical Engineering
ISBN:9780134319650
Author:Russell C. Hibbeler
Publisher:PEARSON
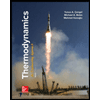
Thermodynamics: An Engineering Approach
Mechanical Engineering
ISBN:9781259822674
Author:Yunus A. Cengel Dr., Michael A. Boles
Publisher:McGraw-Hill Education
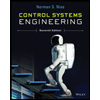
Control Systems Engineering
Mechanical Engineering
ISBN:9781118170519
Author:Norman S. Nise
Publisher:WILEY
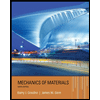
Mechanics of Materials (MindTap Course List)
Mechanical Engineering
ISBN:9781337093347
Author:Barry J. Goodno, James M. Gere
Publisher:Cengage Learning
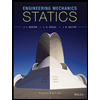
Engineering Mechanics: Statics
Mechanical Engineering
ISBN:9781118807330
Author:James L. Meriam, L. G. Kraige, J. N. Bolton
Publisher:WILEY