Lab 5 - AB5 Group D
docx
keyboard_arrow_up
School
University of Illinois, Urbana Champaign *
*We aren’t endorsed by this school
Course
330
Subject
Mechanical Engineering
Date
Dec 6, 2023
Type
docx
Pages
16
Uploaded by HighnessPelican79
Lab 5: Heat Treatment of Steel
ME330 AB5 Group D
J. Signorini, B. Goddard, D. Jhaveri, I. Jhanji, Y. Ramani
1
Table of Contents
Abstract:
.................................................................................................................................
3
Introduction:
...........................................................................................................................
5
2.1 Heat Treatment Variables
.............................................................................................................
5
2.2 Heat Treatment
.............................................................................................................................
5
Procedure:
...............................................................................................................................
5
3.2 Heat Treatments
...........................................................................................................................
6
3.3 Tensile Testing
...............................................................................................................................
6
Conclusions:
............................................................................................................................
8
Stress-Strain Curves for Various Heat Treatment Methods
.................................................................
8
Material Properties for Various Heat Treatments
.............................................................................
11
Relationship between BHN and Ultimate Strength
...........................................................................
12
Differences in Strength between Oil and Water Quenching
..............................................................
13
Physical Results of Various Heat Treatment Methods
.......................................................................
14
Acknowledgements:
..............................................................................................................
17
References:
............................................................................................................................
17
Contribution List:
...................................................................................................................
17
2
Abstract:
The microstructure of iron and steel significantly influences mechanical properties, and one way
of manipulating the microstructure is through heat treatment. Heat treatment drives atomic
diffusion, forming phases with distinct crystalline structure and relative concentrations of carbon.
Desired phase composition, resultant microstructure and material properties are obtained by
heating a material to a specific temperature and cooling it at varying rates. This lab investigates
the mechanisms which form these microstructures in steel during heat treatment and quantifies
the changes in hardness and tensile behavior.
Above the eutectoid temperature of 727
o
C, a phase called austenite (γ) is formed with face
centered cubic crystal structure. This temperature is known as the eutectoid temperature as it
denotes the temperature at which a single solid phase transitions into two solid phases, similar to
how the eutectic temperature denotes the temperature at which a single liquid phase transitions
into two solid phases. The rate of subsequent cooling determines the formation of other phases
described below.
Equilibrium phases are those which, under constant environmental conditions, do not change
with time. For iron at standard temperature and pressure, the equilibrium phases are ferrite ) and
(
(
iron carbide (Fe
C, also called cementite), and their respective crystal structures are body-
₃
centered cubic and orthorhombic. Equilibrium cooling occurs slowly enough that there is
sufficient time for carbon to diffuse and form these equilibrium phases, forming microstructure
called pearlite, which is characterized by alternating layers of ferrite and cementite. The
equilibrium cooling processes investigated in this lab are annealing and normalizing. Annealing
is achieved in a furnace through very slow, controlled cooling rate of half a degree per minute in
this investigation, which results in grain growth. Normalization is achieved through air cooling at
a significantly faster rate, meaning less grain growth occurs, resulting in a stronger but less
ductile material.
Metastable phases are those in which an equilibrium state is never truly achieved, however the
decay of these phases can be so slow that it is negligible for design purposes. Martensite is one
such metastable phase formed during rapid, non-equilibrium cooling, and it is distinct in that it is
a displacive--not a diffusion-driven--reaction. This displacement results in a unique body
centered tetragonal crystal structure, which results in enhanced properties like high hardness and
strength, but also brittleness.
Non-equilibrium cooling can be achieved through several heat transfer mechanisms, but the most
common is convective to a liquid, called quenching. The rate of cooling during quenching can be
tuned both through the thermofluidic properties of the working medium and through convective
enhancement, known to some as stirring. In this investigation, two rates of non-equilibrium
cooling are achieved through water and a heavy-weight, high viscosity oil, creating a higher and
lower cooling rate, respectively.
In addition to forming martensite, quenching can cause residual stresses and microfractures due
to the large temperature gradients inducing differential thermal expansion, which creates internal
shearing. In addition to martensite’s pre-existing brittleness, the resultant as-quenched material
3
Your preview ends here
Eager to read complete document? Join bartleby learn and gain access to the full version
- Access to all documents
- Unlimited textbook solutions
- 24/7 expert homework help
properties are not very desirable for engineering applications, and thus some ductility and
toughness must be reintroduced through a process called tempering. The material is held at an
elevated temperature, driving partial diffusion of the martensite into the equilibrium phases of
carbide and ferrite, while also inducing some creep that allows relaxation of the residual stresses.
Two tempers of 400
o
C and 600
o
C are investigated in this lab, with elevated temperature resulting
in more complete tempered martensite formation and regained ductility.
Overall results show that non-equilibrium cooling results in high stiffness, but lower ductility
compared to equilibrium processes. There is a limit to the relation of faster cooling rate to
increased strength, as the water-quenched specimen had significantly lower ultimate strength due
to internal stress fractures.
4
Introduction
:
2.1 Heat Treatment Variables
Alloying components, cooling rate, transformation temperature, and carbon content make up the
major four factors. The microstructures and characteristics of the alloying materials change
during the heat treatment process. Phase diagrams can be seen to shift as a result. The final
microstructure of the sample is significantly influenced by the cooling rate. Pearlite would result
from a slow cooling rate of austenite, while bainite would result from a moderate cooling rate,
and martensite would result from a fast-cooling rate. We will see how a slower cooling rate
causes the sample to exhibit more ductility, whereas a quicker cooling rate causes the sample to
exhibit greater strength. The strength of the heated material significantly affects the sample's
carbon content. When other factors are considered, carbon assumes various forms in the
material's structure. The materials' strengths differ as a result.
2.2 Heat Treatment
Austenitizing, annealing, normalizing, water and oil quenching, and tempering will all be
covered in this lab. The first step is austenitizing, which involves heating the materials to
transform them into austenite. We can undertake additional therapies thanks to this approach.
The sample is transformed into ferrite and cementite during the annealing process, which
involves slowly chilling the material under supervision. The microstructure shows larger grains
and coarse pearlites as a result. Normalizing is comparable, but it relies on air to chill the sample
down rather than a well-regulated cooling procedure. Less time is available for diffusion, leading
to finer pearlites and limits changes in grain size. On the other hand, quenching creates
martensite, the strongest type of microstructure. The hot sample is cooled most quickly by
quenching, and water quenching accomplishes this more quickly than oil quenching. This is
because water has a higher heat capacity. Quenching can also be thought of as an addition to
quenching. By enhancing sample strength, quenching causes the creation of brittle material.
Tempering is utilized to strike a balance between the two. This is accomplished by slightly
heating the quenched material to permit some diffusion. This lessens the thermal stress created
during quenching, enhancing the material's ductility while maintaining strength.
Procedure:
3.1 Equipment and Material
A furnace, tongs, insulated gloves, a water bath, an oil bath, a screw load frame, wedge grips and
an extensometer are among the tools utilized in this lab. The 4340 Steel is initially heat treated
using this equipment in a variety of ways. The samples that need to be quenched, normalized,
and tempered are heated in the furnace as well as the samples that need to be annealed. The next
step is to perform the heat treatment methods of normalizing, water quenching, oil quenching,
and tempering (T400 and T600) using tongs, insulated gloves, water baths, and oil baths. Then,
5
4340 steel that has undergone five different types of heating treatment is put through a tensile
test using the screw load frame, wedge grips, and extensometer.
3.2 Heat Treatments
The samples that need to be annealed will be finished before class because the annealing heat
treatment procedure takes a while. The samples that will be quenched, normalized, and tempered
are currently in the oven. Heat gloves and safety eyewear must be worn when handling the tongs
to remove any and all samples because they will be extremely hot. Remove the sample from the
normalized samples and set it on the proper block so it can air dry. The samples that have been
water quenched should be taken out of the oven, dipped vertically into the water bath within 5
seconds, and swirled there for 20 seconds. Then, it ought to be put on the brick to cool. The
process for oil-quenched samples should be the same as for water-quenched samples, with the
exception that the oil bath should be agitated for 2 minutes. The same oil bath technique should
be followed for the tempered specimens, but the oil should be removed before the specimen is
put in the appropriate oven, depending on whether it will be tempered at 400C or 600C. The
samples should be prepared for part 3.3 after cooling. The gauge and grip of the samples should
first be cleaned of iron oxide scale using the wire brush. The preparation should next be
completed with belt sanders. Use the water buckets to chill the specimen if it becomes too warm
during this process. The grip should then be cooled using the bigger belt sander so that the
specimen can be held securely by the tensile grips and the hardness measurement may be
performed. Finally, use the smaller belt sander to remove any scale from the gauge portion, and
then use the Sharpie to identify each specimen with the appropriate heat treatment.
3.3 Tensile Testing
The ASTM standard E8-81 is followed for conducting the tension testing. This specification will
be applied to all specimens of 4340 steel that have undergone various heat treatments. For each
specimen, the Rockwell hardness must first be determined. Because the variety of
microstructures in this lab calls for both B and C scales, one must be careful to use the
appropriate one. The next step is to measure each specimen's original gauge diameter and
average the three measurements for that specimen to obtain the average area. When determining
the curvature for the hardness adjustment, the grip diameter should also be considered. The
specimen should then be secured in the screw load frame, and the standard tensile testing process
should be followed, with the exception that the extensometer should only be balanced, not the
load. The specimen should then be monitored until failure before the Control program is started
at a rate of 4.0 mm/min. Following failure, the specimen should be examined, the fracture
surface marked, and the final neck diameter measured to record the final area. The tempered
specimens should be taken out of the oven after all other heat treatments have been tested, and
the same cleaning and loading procedures should be followed for them. After completing all
tensile tests, the fracture surface will be examined under the stereomicroscope. Then, join the lab
group to examine the heat-treated plain carbon steels' microstructures, which will be displayed
on a projector.
6
Your preview ends here
Eager to read complete document? Join bartleby learn and gain access to the full version
- Access to all documents
- Unlimited textbook solutions
- 24/7 expert homework help
Conclusions:
Stress-Strain Curves for Various Heat Treatment Methods
Figure 1. Annealed 1045 Steel Stress vs
Strain Curve
Figure 2. Cold-Rolled 1045 Steel Stress vs
Strain Curve
Figure 3. Normalized 1045 Steel Stress vs
Strain Curve
Figure 4. Water Quenched 1045 Steel Stress
vs Strain Curve
7
0
0.05
0.1
0.15
0.2
0
500
1000
1500
2000
4340 Steel Stess vs Strain Curves
Annealed
Normalized
Tempered @600
Tempered @350
Oil Quenched
Water Quenched
Strain (mm/mm)
Stress (MPa)
Figure 5. 4340 Steel Stress vs Strain Curve for all Heat Treatments
Heat treatments are crucial for altering the microstructures of metals which affect key
mechanical properties – such as ductility and strength. Different heat treatments have varying
effects on these properties and can also influence the strain hardening after yielding. Above,
Figures 1 – 4 depict the stress-strain curves for annealed, cold-rolled, normalized, and water
quenched 1045 steels. In Figure 5, the stress-strain curve for annealed, normalized, tempered (at
350C and 600C), oil quenched, and water quenched 4340 steels are shown.
Before beginning any of the heat treatment techniques mentioned above for steels, the carbon
inside of the steel needs to be dissolved into FCC iron. This is done by heating up the steel and
holding it at a certain temperature (typically around 850C but can vary based on the alloy) so that
austenite can nucleate and grow new crystals. This process is called austenitizing.
Annealing is the process of cooling the austenitized steel at a controlled rate in a furnace.
Usually, annealing causes materials to have large grain sizes and coarse perlite with a lower
strength and higher ductility. If the steel was air cooled after austenitizing, the process is called
normalizing. Because the specimen is air cooled, there is less time for diffusion and grain growth
than annealing. This results in a fine pearlite and uniform microstructure. Typically, normalized
8
steels have a higher strength and toughness and a lower ductility compared to annealing. This
can be observed in Figure 5, comparing the annealed to normalized stress-strain curves. The
4340 annealed has a much lower strength but is much more ductile than the 4340 normalized.
Quenching is the process of rapidly cooling austenitized steel by submerging it into a quench
media. If the cooling rate from quenching is fast enough, the transformation between austenite to
ferrite and iron carbide does not occur and instead martensite is formed. In this lab, two mediums
were used: oil and water. Water has a higher heat capacity and conducts heat from the surface of
the steel faster than oil. This causes the cooling process to be very fast, however, because of its
severity, it can distort or crack the material. Oil quenching is a significantly less severe medium
which still transfers heat a bit slower but does not cause significant distortions in the material.
Overall, water quenched steels tend to be harder and more brittle, while oil quenched steels tend
to have a more moderate hardness and ductility. Looking at Figure 5 again, this can be confirmed
by comparing the two quenched curves. It was additionally observed that while the strength of
both quenched steels is much higher than other heat treatment methods, they are significantly
more brittle because of the rate at which cooling is conducted.
Tempering follows quenching and involves reheating the martensite to below the eutectoid
temperature and help for several hours. This allows carbides to precipitate and residual stresses
caused by rapid cooling to be relived. This process forms tempered martensite. Regular
martensite formed after quenching is very strong, however, brittle as well. By tempering
martensite, the strength is reduced while the ductility is significantly improved, making the
material more usable in applications. This can be seen comparing the two quenched curves in
Figure 5 to the two tempered curves. The strength of the tempered steel maintains a strength
greater than annealing and increases the ductility from quenching.
Different heat treatment methods also cause different amounts of strain hardening after yielding.
Based on the results shown in the Figures above, quenching leads to the most significant strain
hardening because the rapid cooling process locks dislocations in place and promotes the
formation of martensite (which is strong but brittle). This is followed by normalized steel, 350C
tempered, and 600C tempered. Annealing minimized the strain hardening which can be because
it promoted the formation of a fine-grained, equiaxed, microstructure which leads to increased
ductility but reduced hardness/strength.
9
Your preview ends here
Eager to read complete document? Join bartleby learn and gain access to the full version
- Access to all documents
- Unlimited textbook solutions
- 24/7 expert homework help
Material Properties for Various Heat Treatments
Table 1. Properties for all Heat Treatments of 4340 Steel
Annealed
Normalized
Tempered
@ 600C
Tempered
@ 350C
Oil
Quenched
Water
Quenched
Hardness
(BHN)
90.67
281.5
230.43
297.97
396.14
251.04
σ
0.2%
(
MPa
)
390.490
775.995
962.365
1464.890
1424.050
1729.925
σ
ultimate
(
MPa
)
672.791
1694.361
1065.8
1620.062
2012.922
1957.030
% Elongation
25.239
15.491
36.219
19.034
4.189
1.752
Table 2. Properties of 1018 CR Steel with Varying Treatments
As Received
Normalized
Annealed
Spheroidized
Water
Quenched
Rockwell
Hardness #
100.3 (R)
78 (Rb)
67.4 (Rb)
52.1 (Rb)
42.3 (Rc)
BHN
227.90
148.52
121.17
90.33
382.40
UTS (MPa)
727.93
517.13
469.23
341.60
1462.97
Table 3. Properties of 1045 HR Steel with Varying Treatments
As
Received
Normalized Annealed Spheroidized
Water
Quenched
Oil
Quenched
at 500C
Oil
Quenched
at 350C
Rockwell
Hardness #
93.4 (Rb)
91.4 (Rb)
82.6 (Rb)
66.8 (Rb)
57.9 (Rc)
28.4 (Rc)
37.5 (Rc)
BHN
199.62
192.10
162.23
119.78
566.57
269.40
338.82
UTS (MPa)
729.50
696.01
649.70
466.00
444.19
976.83
1220.95
In Table 1 above, several properties of heat treated 4340 Steel are given. These properties
corroborate with the explanation of Figure 5 where these heat treatments were plotted on a
stress-strain curve. The Harness for the samples above were adjusted based on the curvature of
the surface where necessary and were additionally converted from the Rockwell scale to the
Brinell scale. The Annealed sample was converted from HRB to BHN, and the additional 5
samples were converted from HRC to BHN. The formulas used in the conversions are given
below.
10
BHN
=
33.22
e
(
0.0192
R
B
)
BHN
=
131.7
e
(
0.0252
R
C
)
Relationship between BHN and Ultimate Strength
0.000
50.000
100.000
150.000
200.000
250.000
300.000
350.000
400.000
450.000
500.000
0
500
1000
1500
2000
f(x) = 3.45 x
Ultimate Stength vs Hardness
4340 Anealed
1018 CR - Annealed
1045 HR - Annealed
4340 Normalized
1018 CR - Normalized
1045 HR - Normalized
4340 Tempered @ 600C
4340 Tempered @ 350C
4340 Oil Quenched
1045 HR - OQ @350
1045 HR - OQ @500
4340 Water Quenched
1018 CR - Water Quenched
1045 HR - Water Quenched
1018 CR - As Received
1045 HR - As Received
1018 CR - Spheroidized
1045 HR - Spheroidized
UTS
= 3.45 * BHN
Linear (UTS
= 3.45 * BHN)
BHN
Ultimate Stress (MPa)
Figure 6. Ultimate vs Hardness Linear Plot of 4340, 1018, and 1045 Steels
Figure 6 above plots the ultimate tensile strength (UTS) against the Brinell hardness (BHN). The
following legend can be used to better understand the graph:
o
Square = Annealed
o
Diamond = Normalized
o
X = Tempered
o
+ = Spheroidized
o
Orange, Red = 4340 Steel
o
Yellow = 1018 Steel
11
o
⚹
= Oil Quenched
o
Circle = Water Quenched
o
– = As Received
o
Blue, Purple = 1045 Steel
In addition to the BHN and UTS values, a “rule of thumb” for steel line is additionally plotted in
Figure 6. This best fit line follows the relations listed below:
UTS
(
MPa
)
=
3.45
×BHN
Analyzing Figure 6 based on the heat treatment method – annealed, spheroidized,
normalized (for 1018/1045), and oil quenched (for 1018/1045) are very similar to the rule of
thumb. The tempered (for 4340) and water quenched had the most disparity from the rule of
thumb. Another valuable characteristic of the plot is that the 4340 Steel data points are all
significantly above the best fit line which indicates that there could have been some human error
in the creation of the test samples or in the physical testing of them. Some examples of human
error could be not quenching the samples fast enough or allowing the samples to cool for too
long while the oven door is open (which also can create an uneven heat distribution for a period).
All heat treatments, other than water quenched, for 1018 and 1045 steel follow very closely to
the trend.
Differences in Strength between Oil and Water Quenching
Oil and water quenching are two mediums used to cool down heated samples, however,
they do so at much different rates. Water has a much higher heat transfer coefficient than oil
meaning it can cool the sample significantly faster. The difference in cooling rates yield samples
with varying characteristics. One such difference is their microstructure. The water quenching
tends to produce a harder, more brittle sample compared to oil quenching. Table 1 does not
support this claim, however, this likely can be attributed to error when recording the data.
Additionally, the strength of our samples will change with different cooling rates. The rapid
cooling of the water quenched sample resulted in many small, fine grains. This allows the sample
to be able to withstand more stress than the oil quenched sample, as evident in the elastic region
shown in figure 5. The steeper slope in the elastic region shows it takes more stress to cause
deformation, indicating a greater strength. In summary, both methods will produce different
properties in our steel sample. Water quenching tends to have small, fine grains resulting in a
hard and strong material. Oil quenching produces coarser grains which gives the sample a
moderate balance of hardness and strength.
12
Your preview ends here
Eager to read complete document? Join bartleby learn and gain access to the full version
- Access to all documents
- Unlimited textbook solutions
- 24/7 expert homework help
Physical Results of Various Heat Treatment Methods
Figure 7. Spheroidized 1045 Steel Microstructure
The spheroidized 1045 steel microstructure consists of a soft ferrite matrix with spherical carbide
particles. Spheroidization primarily affects the machinability of steel. The soft ferrite matrix
provides increased ductility, while the spheroidal carbides contribute to the dispersion
strengthening mechanism. This dispersion hinders dislocation movement and provides resistance
to deformation, contributing to the material's improved machinability and resistance to wear.
Figure 8. Water Quenched 1045 Steel Microstructure
This microstructure mainly consists of martensite, characterized by a lath or needle-like
structure. The rapid cooling rate during quenching suppresses the formation of pearlite and traps
carbon atoms within the iron lattice. The primary strengthening mechanism in this case is solid-
solution strengthening. The rapid cooling traps carbon atoms in the interstices of the iron lattice,
leading to the formation of the hard and brittle phase called martensite. This phase offers high
strength and hardness due to the limited movement of dislocations, providing increased wear
resistance and improved mechanical properties.
13
Figure 9. Normalized 1045 Steel Microstructure
This microstructure consists of fine pearlite and ferrite, achieved through heating the steel above
the critical range followed by cooling in still air. This process refines the grain structure and
creates a uniform distribution of pearlite. The main strengthening mechanisms at play here are
grain refinement and precipitation hardening. Grain refinement improves the strength and
toughness of the steel by reducing the grain size, which hinders dislocation movement.
14
Figure 10. Annealed Steel Tensile Test Fracture Surface
Figure 11. Normalized Steel Tensile Test Fracture Surface
Figure 12. Oil Quenched Steel Tensile Test Fracture Surface
Figure 13. 600C Temper Tensile Test Fracture Surface
Acknowledgements:
We would like to thank groups D and C in lab section AB5 for collecting tensile data of different
heat-treated specimens.
15
Your preview ends here
Eager to read complete document? Join bartleby learn and gain access to the full version
- Access to all documents
- Unlimited textbook solutions
- 24/7 expert homework help
References:
"HEAT TREATMENT OF STEEL - ME330 Lab 5 Manual." (n.d.): Print. 2022 Board of Trustees
of the University of Illinois
Contribution List:
Dhruv Jhaveri – Introduction and Procedure
Ishaan Jhani – Scaffolding, Conclusions, Formatting Data, Formatting Report, Question 1, 2, 3
Yogesh Ramani – Formatting Report, Table of Contents, Conclusions, Question 5,
Jacob Signorini – Excel data, question 4, abstract & general formatting
Ben Goddard – Abstract, Fracture Surface images
16
Related Documents
Related Questions
When performing a quench to cool a product, the quench rate affects the outcome of the process. TRUE OR FALSE:
3 principal driving forces for the development of mechanical properties during heat treatment.
Group of answer choices
Microstructure Changes
Formation of Surface Oxide
Cooling Rate
Ambient Temperature
Heating Rate
Diffusion Rate
Heating Method
arrow_forward
This question is for mechanical engineering. Please help me with this and explain. Thank you.
arrow_forward
6. Answer the following questions regarding the Lever Rule. [
a. Describe the purpose of the Lever Rule and write the equation.
b. Using the lever rule for 52 wt% Zn-48 wt% Cu, cite the phases present and mass fractions at the
following temperatures: 1000°C, 800°C, 500°C, and 300°C. Refer to the Cu-Zn diagram from
problem 3 or use the book diagram on p. 326.
7. Returning to the Zn-Cu phase diagram, using the composition 52 wt% Zn-48 wt% Cu, draw schematics
of the microstructures if you were to undergo a slow cooling process. Draw representations for 950°C,
860°C, 800°C, and 600°C. Make sure to properly label each phase and determine their approximate
compositions.
arrow_forward
Stuck need help!
Problem is attached. please view attachment before answering.
Really struggling with this concept.
Please show all work so I can better understand !
Thank you so much.
arrow_forward
Need help with this Mechanics of Materials review
arrow_forward
Don’t use ai pls
arrow_forward
How would you callout magnesium in an engineering drawing note?
I want to call out Magnesium AZ31B, plate, AMS4376. This is what I have so far:
Notes:
1. Material: MAGNESIUM ALLOY, PLATE, UNS M11311 (AZ31B), PER AMS4376, CONDITION -H26
Is this correct?
arrow_forward
steel:SCM440(two of the pictures are the same )
x80
x50
what is the heat treatment process and discuss the organization structure
arrow_forward
Circle all correct statements for the Young's or elastic modulus, E:
a. Has units of force per unit area.
b. Is a measure of the ductility of a metal.
c. Can be used to determine transverse strains in uniaxial loading.
d. Is a material property.
e. Is the slope of the elastic portion of a stress-strain (s-e) tensile curve
Circle all of the statements that describe interstitial solid solutions:
a. Is an example of a line defect.
b. A solute atom replaces a solvent atom in the matrix.
c. Would predict formation when adding carbon (C) to iron (Fe).
d. Would predict formation when adding chromium (Cr) to iron (Fe).
e. Requires the formation of a cation-anion vacancy pair.
f. The solute atom has a smaller radius than the solvent atom.
arrow_forward
Pick the best soultion for the multiple choices.
Modulus of resilience is:
Slope of elastic portion of stress – strain curve
Area under the elastic portion of the stress –strain curve
Energy absorbed during fracture in a tension test
Energy absorbed during fracture in an impact test
Slope of the plastic portion of the stress- strain curve ( )
Fatigue failure occurs under the condition of:
High elastic stress
High corrosivity
High stress fluctuations
High temperature
High rate of loading ( )
Creep failure of a material occurs most rapidly when the operating temperature is:
Cryogenic temperature
Equal to its melting point
Grater than 0.4 times its melting point in K
Greater than 200 oF
Close to boiling point ( )
Young’s modulus of a material is indicative of its:
Tensile strength
Yield Strength
Ductility
Stiffness
Corrosion Resistance…
arrow_forward
For each question, provide an explanation, identifying the correct choice ( it is marked in red) and explaining why it's the right answer, as well as why the other options are incorrect.
Please do 1, 2.
arrow_forward
3. The starting length of a shaft is 25.00 mm. This shaft is to be inserted into a hole in an
expansion fit assembly operation. To be readily inserted, the shaft must be reduced in length
by cooling. Determine the temperature to which the shaft must be reduced from room
temperature (20° C) in order to reduce its length to 24.98 mm. Refer to the Table below.
Volumetric properties in U.S. customary units for selected engineering materials.
Coefficient of Thermal
Density, p
Expansion, a
Melting Point, T
Material
g/cm
Ib/in
c'x 10
x 10
°C
'F
Metals
Aluminum
2.70
0.098
24
13.3
660
1220
Copper
Iron
0.324
0.284
0.410
8.97
17
9.4
1083
1981
2802
7.87
12.1
6.7
1539
Lead
11.35
29
16.1
327
621
Magnesium
Nickel
1.74
0.063
0.322
0.284
26
14.4
7.4
650
1202
8.92
13.3
1455
2651
7.87
7.31
19.30
7.15
Steel
Tin
12
23
6.7
0.264
12.7
232
449
Tungsten
Zinc
0.697
4.0
2.2
3410
6170
0.258
40
22.2
420
787
Ceramics
b.
Glass
2.5
0,090
1.8-9.0
1.0-5.0
Alumina
3.8
0.137
9.0
5.0
NA
NA
b.
Silica
2.66
0,096
NA
NA…
arrow_forward
Hardness is defined as:
a.
The density of the materials surface layer
b.
The density of the packing of the materials atoms
c.
The ability to resist cracking
d.
The ability to resist indentation
arrow_forward
For each question, provide an explanation, identifying the correct choice ( it is marked in red) and explaining why it's the right answer, as well as why the other options are incorrect.
arrow_forward
What would be the specific heat of sample 1? The block’s initial temperature is 98 degrees C
arrow_forward
Which of the following describes the crystal structure of steel?
Group of answer choices
Steel is a iron-carbon alloy with carbon creating a vacancy crystal defect resulting in decreased hardness compared to pure iron.
Steel is a iron-carbon alloy with carbon as an substitutional crystal defect resulting in decreased hardness compared to pure iron.
Steel is a iron-carbon alloy with carbon as an interstitial crystal defect resulting in decreased hardness compared to pure iron.
Steel is a iron-carbon alloy with carbon creating a vacancy crystal defect resulting in increased hardness compared to pure iron.
Steel is a iron-carbon alloy with carbon as an interstitial crystal defect resulting in increased hardness compared to pure iron.
Steel is a iron-carbon alloy with carbon as an substitutional crystal defect resulting in increased hardness compared to pure iron.
arrow_forward
Select 3 principal driving forces for the development of mechanical properties during heat treatment.
Group of answer choices:
Microstructure Changes
Formation of Surface Oxide
Cooling Rate
Ambient Temperature
Heating Rate
Diffusion Rate
Heating Method
arrow_forward
Manufacturing 1-V2 (1) - Compatibility Mode
Saved -
O Search
Review
View
Help
E E - E EE
>T T I
AaBbCcDd AaBbCcDd AaBbC AaBbCcl Aa
1 Normal
1 No Spac. Heading 1
Heading 2
Title
Paragraph
Styles
7. Assuming that the density of steel and aluminium are 7.9 and 2.7 g/cm, respectively,
which material has the best strength-to-weight ratio? (Hint: the strength-to-weight ratio is
called specific strength, equal to yield strength divided by density).
arrow_forward
SEE MORE QUESTIONS
Recommended textbooks for you
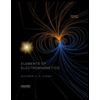
Elements Of Electromagnetics
Mechanical Engineering
ISBN:9780190698614
Author:Sadiku, Matthew N. O.
Publisher:Oxford University Press
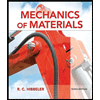
Mechanics of Materials (10th Edition)
Mechanical Engineering
ISBN:9780134319650
Author:Russell C. Hibbeler
Publisher:PEARSON
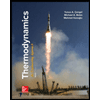
Thermodynamics: An Engineering Approach
Mechanical Engineering
ISBN:9781259822674
Author:Yunus A. Cengel Dr., Michael A. Boles
Publisher:McGraw-Hill Education
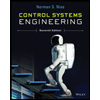
Control Systems Engineering
Mechanical Engineering
ISBN:9781118170519
Author:Norman S. Nise
Publisher:WILEY
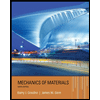
Mechanics of Materials (MindTap Course List)
Mechanical Engineering
ISBN:9781337093347
Author:Barry J. Goodno, James M. Gere
Publisher:Cengage Learning
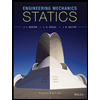
Engineering Mechanics: Statics
Mechanical Engineering
ISBN:9781118807330
Author:James L. Meriam, L. G. Kraige, J. N. Bolton
Publisher:WILEY
Related Questions
- When performing a quench to cool a product, the quench rate affects the outcome of the process. TRUE OR FALSE: 3 principal driving forces for the development of mechanical properties during heat treatment. Group of answer choices Microstructure Changes Formation of Surface Oxide Cooling Rate Ambient Temperature Heating Rate Diffusion Rate Heating Methodarrow_forwardThis question is for mechanical engineering. Please help me with this and explain. Thank you.arrow_forward6. Answer the following questions regarding the Lever Rule. [ a. Describe the purpose of the Lever Rule and write the equation. b. Using the lever rule for 52 wt% Zn-48 wt% Cu, cite the phases present and mass fractions at the following temperatures: 1000°C, 800°C, 500°C, and 300°C. Refer to the Cu-Zn diagram from problem 3 or use the book diagram on p. 326. 7. Returning to the Zn-Cu phase diagram, using the composition 52 wt% Zn-48 wt% Cu, draw schematics of the microstructures if you were to undergo a slow cooling process. Draw representations for 950°C, 860°C, 800°C, and 600°C. Make sure to properly label each phase and determine their approximate compositions.arrow_forward
- How would you callout magnesium in an engineering drawing note? I want to call out Magnesium AZ31B, plate, AMS4376. This is what I have so far: Notes: 1. Material: MAGNESIUM ALLOY, PLATE, UNS M11311 (AZ31B), PER AMS4376, CONDITION -H26 Is this correct?arrow_forwardsteel:SCM440(two of the pictures are the same ) x80 x50 what is the heat treatment process and discuss the organization structurearrow_forwardCircle all correct statements for the Young's or elastic modulus, E: a. Has units of force per unit area. b. Is a measure of the ductility of a metal. c. Can be used to determine transverse strains in uniaxial loading. d. Is a material property. e. Is the slope of the elastic portion of a stress-strain (s-e) tensile curve Circle all of the statements that describe interstitial solid solutions: a. Is an example of a line defect. b. A solute atom replaces a solvent atom in the matrix. c. Would predict formation when adding carbon (C) to iron (Fe). d. Would predict formation when adding chromium (Cr) to iron (Fe). e. Requires the formation of a cation-anion vacancy pair. f. The solute atom has a smaller radius than the solvent atom.arrow_forward
- Pick the best soultion for the multiple choices. Modulus of resilience is: Slope of elastic portion of stress – strain curve Area under the elastic portion of the stress –strain curve Energy absorbed during fracture in a tension test Energy absorbed during fracture in an impact test Slope of the plastic portion of the stress- strain curve ( ) Fatigue failure occurs under the condition of: High elastic stress High corrosivity High stress fluctuations High temperature High rate of loading ( ) Creep failure of a material occurs most rapidly when the operating temperature is: Cryogenic temperature Equal to its melting point Grater than 0.4 times its melting point in K Greater than 200 oF Close to boiling point ( ) Young’s modulus of a material is indicative of its: Tensile strength Yield Strength Ductility Stiffness Corrosion Resistance…arrow_forwardFor each question, provide an explanation, identifying the correct choice ( it is marked in red) and explaining why it's the right answer, as well as why the other options are incorrect. Please do 1, 2.arrow_forward3. The starting length of a shaft is 25.00 mm. This shaft is to be inserted into a hole in an expansion fit assembly operation. To be readily inserted, the shaft must be reduced in length by cooling. Determine the temperature to which the shaft must be reduced from room temperature (20° C) in order to reduce its length to 24.98 mm. Refer to the Table below. Volumetric properties in U.S. customary units for selected engineering materials. Coefficient of Thermal Density, p Expansion, a Melting Point, T Material g/cm Ib/in c'x 10 x 10 °C 'F Metals Aluminum 2.70 0.098 24 13.3 660 1220 Copper Iron 0.324 0.284 0.410 8.97 17 9.4 1083 1981 2802 7.87 12.1 6.7 1539 Lead 11.35 29 16.1 327 621 Magnesium Nickel 1.74 0.063 0.322 0.284 26 14.4 7.4 650 1202 8.92 13.3 1455 2651 7.87 7.31 19.30 7.15 Steel Tin 12 23 6.7 0.264 12.7 232 449 Tungsten Zinc 0.697 4.0 2.2 3410 6170 0.258 40 22.2 420 787 Ceramics b. Glass 2.5 0,090 1.8-9.0 1.0-5.0 Alumina 3.8 0.137 9.0 5.0 NA NA b. Silica 2.66 0,096 NA NA…arrow_forward
arrow_back_ios
SEE MORE QUESTIONS
arrow_forward_ios
Recommended textbooks for you
- Elements Of ElectromagneticsMechanical EngineeringISBN:9780190698614Author:Sadiku, Matthew N. O.Publisher:Oxford University PressMechanics of Materials (10th Edition)Mechanical EngineeringISBN:9780134319650Author:Russell C. HibbelerPublisher:PEARSONThermodynamics: An Engineering ApproachMechanical EngineeringISBN:9781259822674Author:Yunus A. Cengel Dr., Michael A. BolesPublisher:McGraw-Hill Education
- Control Systems EngineeringMechanical EngineeringISBN:9781118170519Author:Norman S. NisePublisher:WILEYMechanics of Materials (MindTap Course List)Mechanical EngineeringISBN:9781337093347Author:Barry J. Goodno, James M. GerePublisher:Cengage LearningEngineering Mechanics: StaticsMechanical EngineeringISBN:9781118807330Author:James L. Meriam, L. G. Kraige, J. N. BoltonPublisher:WILEY
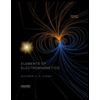
Elements Of Electromagnetics
Mechanical Engineering
ISBN:9780190698614
Author:Sadiku, Matthew N. O.
Publisher:Oxford University Press
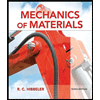
Mechanics of Materials (10th Edition)
Mechanical Engineering
ISBN:9780134319650
Author:Russell C. Hibbeler
Publisher:PEARSON
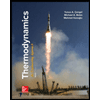
Thermodynamics: An Engineering Approach
Mechanical Engineering
ISBN:9781259822674
Author:Yunus A. Cengel Dr., Michael A. Boles
Publisher:McGraw-Hill Education
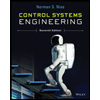
Control Systems Engineering
Mechanical Engineering
ISBN:9781118170519
Author:Norman S. Nise
Publisher:WILEY
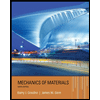
Mechanics of Materials (MindTap Course List)
Mechanical Engineering
ISBN:9781337093347
Author:Barry J. Goodno, James M. Gere
Publisher:Cengage Learning
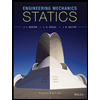
Engineering Mechanics: Statics
Mechanical Engineering
ISBN:9781118807330
Author:James L. Meriam, L. G. Kraige, J. N. Bolton
Publisher:WILEY