roberto_vargas_4.2_Case Study Analysis_Accident Research
docx
keyboard_arrow_up
School
Embry-Riddle Aeronautical University *
*We aren’t endorsed by this school
Course
335
Subject
Mechanical Engineering
Date
Feb 20, 2024
Type
docx
Pages
11
Uploaded by ConstableInternetParrot
1
Case Study Analysis 4.2: Accident Research on Flight 38
Roberto L. Vargas
Embry Riddle University BSAS 335: Mechanical and Structural Factors in Aviation Safety
Dr. Thomas L. Holmes Jr
November 12, 2023
2
Introduction
On January 17, 2008, A Boeing 777 landed short several hundred feet from the runway in
Heathrow International Airport.
Primary Causal Factors of the Accident Due to the evidence, it appears that the aircraft that went down in Rome was due to structural failure of the fuselage with the one in India it is unclear if the accident was caused due to structural overload due to turbulence since they tried to fly through a storm. It seems that near the squarish windows and emergency Escape hatches were vulnerable to localized high stress how stress acts around more rigid shapes like squares and rectangles versus ovals and circles on the fuselage (Groh, 2017). This structural flaw with the pressurization of the cabin climbing in altitude caused the fuselage to fail and rupture at the localized areas of the windows where it would crack after just a few thousand cycles below its maximum cycle life (HER MAJESTY'S STATIONERY OFFICE, 1962).
3
Fig 1. (Groh, 2017)
Contributing Factors to the Accident
Some of the contributing factors that led to the overall failure of these areas of the fuselage could be traced back to the design of the window edges, The use of countersunk rivets in high-stress corners of the windows and emergency escape hatches, and the method of testing used in the prototype. These factors along with insufficient testing on a new technology can contribute to the failure as well (Her Majesty's Stationery Office, 1962). The window design was one of the big indicators that the area around the window when pressurized would build up stress at the corners of the windows (Groh, 2017). This localized stress increases as the plane is pushed and pulled in different directions due to forces like lift, drag, interior pressure, temperature ranges, and exterior forces like gusts and turbulence acting on the aircraft. The stress could not easily move around the rigid corners of the windows and
Your preview ends here
Eager to read complete document? Join bartleby learn and gain access to the full version
- Access to all documents
- Unlimited textbook solutions
- 24/7 expert homework help
4
hatches collecting there like a roadblock on a highway. As the aircraft experiences more and more cycles of pressurization and depressurization the push and pull would over time create fatigue cracking that over time grows until the material fails.
The countersunk rivets were an area of failure for the cracks to continue growing as the aircraft continued flying. It is known in the Structural mechanical world that countersunk rivet heads or “flush heads” are not strong with bonding two pieces of material like the skin to the mail aircraft structure (
Solid shank rivet,
2023). When preparing the surface of a sheet metal rivet hole for a flush head rivet, the area where the head goes is either countersunk with a cutting tool or dimpled with a special dimpling machine. This process reduces the bonding potential of that area leaving it more vulnerable than if you were to use button head rivets instead. Another factor that contributed to these accidents was how DeHavilland tested the Prototype and how it affected the results of their pressure testing of Comet 1. When testing the prototype, the aircraft was over-pressured to 2 P which is twice the operational pressure of the cabin in flight. When this happened this caused the rivet holes during the pressurization to coldwork which had the effect of strengthening the areas around the holes allowing the test to last the 16,000 cycles they recorded during testing (
De Havilland DH-106 comet 1,
2023). This effect did not apply to the production models of the aircraft and did not have the cold work effect
giving it this property.
Structural and Mechanical Factors Related to the Accident
The factors that led up to each of these accidents look mainly structural due to the cause most likely to be pressurization failure of the fuselage. This is indicated by the test The Ministry of Aviation ran in 1962. This document directly annotates the factors that led to the fuselage
5
failing in mid-flight. Although some repairs and alterations were done to the Comet to improve the structure after the third accident, an investigation was conducted on the G-ALYP Report (
CIVIL AIRCRAFT ACCIDENT, 1955). The primary cause due to the reports seems to be the windows and emergency escape hatches and their ability to create stress fractures localized around the corners. A few items that I noticed were the rivets they used in these stress areas, the locations of the rivet holes, and the cracks that go through some of them. The rivets seem to have a role in how the fatigue stress grows into the cracks they form. In these areas the countersunk rivets used at the corners of the windows and hatches seem to show the origin of the fatigue and what may have caused the structure to fail. Countersunk rivets are great for aerodynamic applications but are not the best fastener to use in areas known to have high stress. As mentioned in the G-ALYR report para 4.2 cracks entering rivet holes were not stopped during fatigue testing and in someplace could have started in the areas where the skin was countersunk (HER MAJESTY'S STATIONERY OFFICE, 1962). It was noted in the G-ALYP report that the countersunk around the window was
added to strengthen the structure around the corners of the window due to DeHavilland knowing it was a highly stressed area (
CIVIL AIRCRAFT ACCIDENT, 1955).
The design of the windows themselves causes a lot of the localized stress to form in the areas of the corners which created higher than expected fatigue in those areas. The structural shape of these windows allowed for cracks to form over time until the fuselage broke apart. The flight at Elba with an in-flight break up at 27,000 feet and 40 minutes after takeoff, and the Naples flight at 35,000 feet also 40 minutes after takeoff (
De Havilland DH-106 comet 1,
2023). When tested after the accident the stress around them was more than tested by De Havilland when testing the prototypes.
6
I also believe that the prototype and the way it was tested, set a false condition for the production model of aircraft. The cold working process is when metals go through plastic deformation below their recrystallization temperature (
Metallurgy for dummies,
2023). This leaves the cold work areas with certain properties unlike the original material such as the hardness and tensile strength depending on the degree of cold working accomplished. Oddly enough the prototype comet was tested at twice the load required to ensure compliance. At the time it was not clear if this was known but when the test cycled at twice the pressure it would experience in flight 30 times, and 2000 times at other pressure ranges it invertedly cold worked the area around the square window corners strengthening them in the process (
De Havilland DH-
106 comet 1,
2023). This created a false promise that allowed the aircraft to survive 16,000 cycles and rate the aircraft for a 10,000-cycle life. The production models would not be expected to be subject to these pressures often which in turn would not recreate the condition naturally strengthening the rivet holes and localized stress areas against fatigue.
Relevant Human Factors and Organizational Factors Related to the Accident
Regarding the human factors of the accidents, a few factors play a part. When the Comet was being produced and flown for passenger travel, there was a competition to see who could produce the world’s first commercial jet airliner to have the comfort of a pressurized cabin experience. De Havilland along with Lockheed, Boeing, and many others were developing pressurized aircraft for all markets (Novell’s, 2018). Becoming the first in many areas of commercial travel to attract the masses and bring aerial travel to everyone. This rush to market and making history without fully understanding the technology they were developing is partly to blame for these accidents. At the time of the Comet's creation, there were no clear guidelines or regulations to define what was safe until shortly after the aircraft was built and flying in the
Your preview ends here
Eager to read complete document? Join bartleby learn and gain access to the full version
- Access to all documents
- Unlimited textbook solutions
- 24/7 expert homework help
7
fleets (
De Havilland DH-106 Comet 1,
2023). During testing, they did exceed the basic requirements for pressurization, but in doing so led to a misleading conclusion. De Havilland also did not subject any of the production models that came out of the assembly to any form of testing to ensure the standards. The testing of the production model would have prevented the company from committing
to the standard in place if they knew under normal conditions the cycle life would have been less.
Also, it should have been the responsibility of the testing team of an engineer to look at these areas for deformation and unforeseen properties. I am sure they looked for cracks and deformation and typical signs of stress, but what they didn’t see was the cold working of the holes allowing them to survive the rigorous testing. With modern technology this would have been easy to do however if the engineers were looking for signs of the effects of pressurization on an airframe instead of narrowing their focus on whether their design could withstand pressurization enough for flight it might have been found and accounted for. Outcomes of the Accident
After the investigation of the original three accidents reported the conclusion arrived at was that more testing was needed to determine the stress applied to the aircraft with the regular use of strain gauges to make calculations more accurate (
CIVIL AIRCRAFT ACCIDENT, 1955). With the suggestion of a new design after testing to address the problems that arise during testing. The testing done at the R.A.E. site was done using a large water tank that the fuselage was pressurized in to simulate loading without the aircraft suffering major damage so they could test the effect more often (HER MAJESTY'S STATIONERY OFFICE, 1962). These tests led to a better understanding which resulted in De Havilland taking every precaution moving forward to cover every possible angle that was suggested caused the accident.
8
At this time of the accidents, there was no Airworthiness Directive issued due to the uncertainty of the accident cause and it being in the infancy of Commercial aviation (
De Havilland DH-106 comet 1,
2023). The Comet 1 was still in circulation but in very limited numbers until the Comet 1A was released as the redesign of the original improved the fuselage strength, and other changes were made. The Comet 1XB was made with an Ovel window to mitigate the fatigue stress of the window on the skin of the aircraft (
Comet 1 SN diagram animation, 2021).
Risk Mitigation or Reduction Strategies
Due to the way the Comet was tested a produced as the first commercial jet airliner, the first thing I would point out is the need to compete. De Haviland did their research and testing at the time to prove that it was safe to the public as much as to the organizations that regulated air travel as publicity to promote their product. Skipping the long-term research required to ensure the safe use of a pressurized cabin, most of the aviation world at this time was unfamiliar with what would happen. Regulators started publishing documentation governing standards over pressurized vessels, but at this time Comet 1 was already flying (
De Havilland DH-106 Comet 1,
2023). The engineers testing the Prototype should have realized at some point that the structure they designed was strengthened in fatigued areas due to the nature of testing. I believe the test was not carried out with a more scientific approach with controls or an open mind. They had a focus on seeing if the fuselage could survive multiple cycles and they missed the effects of testing beyond what was required. They should have had a control like two fuselages test at the same time to simulate. One would be at the standard pressure that would be experienced in flight and the other could have been to test the stress-loading effects of irregular pressurization. This
9
could have allowed the designer, in the beginning, to see how many cycles the aircraft could withstand and would have found that 2 P was Cold working the fuselages localized stress areas like the windows and hatches. From the images I saw in the testing done in R.A.E., I noticed the use of closely packed countersunk rivets supporting the corner of the fatigue areas. Countersunk heads are used as bonding fasteners but are not as strong as other fasteners like button-head rivets. They significantly weaken the skin’s ability to bond to the main structure. Especially in high fatigue areas where flexing and deforming could occur. Engineers today avoid using rivets that could weaken the ability to bond when high-stress loads are present.
Another thing I did not see in my research or understood after reading the report was if cold-working the holes around the windows and hatch worked so well why didn’t they use this process to fix and improve the design? It seems that the cold work process that was accidentally achieved worked well enough for the prototype to survive 16,000 cycles. It could have been refined on later models and used to extend the life of this aircraft.
Conclusion
After reading it I understand why Comet 1 had structural failure well below the cycle life of the airframe. The combination of narrow focus on the problems they aimed to solve and the company’s eagerness to show the aircraft’s safety inadvertently created false assumptions. With the culmination of not testing the production model to ensure their results and knowing that the areas around the windows were susceptible to high stress yet did not find an alternative until a few models later. With more meticulous testing and proper research on how pressure affects the airframe, it would have been caught sooner. This case study brings into view the information and
experience I’ve learned my whole career. I believe these accidents help change the standards and
Your preview ends here
Eager to read complete document? Join bartleby learn and gain access to the full version
- Access to all documents
- Unlimited textbook solutions
- 24/7 expert homework help
10
help us understand the effects better. Shaping our understanding and teaching others to be aware of so they do not occur in the future.
References
Blogger. (2023, January 4). Solid shank rivet - aircraft structural fasteners
. Aircraft Systems. https://www.aircraftsystemstech.com/2018/12/solid-shank-rivet-aircraft-structural.html
De Havilland DH-106 comet 1
. Federal Aviation Administration. (2023, March 7). https://www.faa.gov/lessons_learned/transport_airplane/accidents/G-ALYV
Federal Aviation Administration . (2021, January 4). Comet 1 SN diagram animation
. YouTube. https://www.youtube.com/watch?
time_continue=9&v=QgjoN15kfAk&embeds_referring_euri=https%3A%2F%2Fif-
cdn.com%2F&source_ve_path=Mjg2NjY&feature=emb_logo
Groh, R. (2017, May 9). The dehavilland comet crash
. AeroCert Online. https://www.aerocertonline.com/the-dehavilland-comet-crash/
HER MAJESTY’S STATIONERY OFFICE. (1962). Behaviour of Skin Fatigue Cracks at the Corners of Windows in a Comet I Fuselage . FAA. https://www.faa.gov/sites/faa.gov/files/2022-10/G-ALYR_Report_0.pdf
Metallurgy for dummies
. Metallurgy for Dummies Cold Working Processes Comments. (2023). https://www.metallurgyfordummies.com/cold-working-processes.html
MINISTRY OF TRANSPORT AND CIVIL AVIATI. (1955, February 1). CIVIL AIRCRAFT ACCIDENT Report of the Court of Inquiry into the Accidents to Comet G-ALYP on 10th January 1954 and Comet G-ALYY on 8th April, 1954 . Federal Aviation Administration. https://aviation-safety.net/database/record.php?id=19540110-1
Novells, R. (2018, May 25). When did pressurized cabins on commercial airliners become a reality – May 25, 2018
. Robert Novell’s Third Demension Blog. https://www.robertnovell.com/when-did-pressurized-cabins-on-commercial-airliners-
become-a-reality-may-25-2018/
11
Related Documents
Related Questions
Which of these statements are correct?
arrow_forward
Test Specimen
4140 CF steel
6061 T6 Al
Gray Cast iron 40
FC Brass 360
Impact Energy (J or ft-lb)
48.5 ft-lb
25 ft-lb
12 ft-lb
27 ft-lb
Impact Strength (J/m
or ft-lb/in)
123.096 ft-lb/in
63.452 ft-lb/in
What is the final analysis/ overall observation from the data?
30.457 ft-lb/in
68.528 ft-lb/in
arrow_forward
MECT361
Mechatronics Components and Instrumentation
8.1. Why is it not possible to connect sensors such as thermocouples, strain gages, and
accelerometers directly to a digital computer or microprocessor?
PLEASE GIVE ME THE REFRENCE
I Will get zero if you didn't put the refrence
arrow_forward
Answer the following question:
1. What are the different elements of wreckage distribution in an aircraft accident investigation?
arrow_forward
1. Since experimentations are always subject to errors, what techniques are employed to
neutralize the effects of these errors in the accuracy and validity of the experiment?
2. Why is the "factorial experiment" better in any way than a "one-factor-at-a-time"
approach?
3. True or False: As soon as the experimental data (measurements) are obtained, the
experimenter can already proceed with the usual significance testing. Explain.
4. What is "hypothesis testing"? How is it performed?
5.What makes ANOVA a powerful tool in hypothesis testing?
What happens if you use a 2k full Factorial design to explore a set of variables which is
known to have a non-linear response?
6. When is the addition of center points to a 2k full factorial design beneficial? Give a
particular case that warrants its use.
7. In practical terms, explain how a LOW p-value connote SIGNIFICANCE (Recall that the
smaller the p-value is, the more significant the factor becomes)?
arrow_forward
Presented below are the quality ratings with regard to soil moisture availability.
Erosion rating
Moisture rating
Erosion
Rating
MC (%)
Rating
Slope
Slope rating
Rating
hazard class
Low
1
0-5
4
0-5
1
Moderate
2
5-15
3
5-10
2
High
3
15-20
2
10-25
3
Very high
4
>20
1
>25
4
Quality ratings of three land units are tabulated below.
Land quality rating
Land unit
Nutrient availability
Trafficability
1
2
1
2
3
1
3
2
2
Additional characteristics of the land units areas follows:
Land Permeability Land use M.C. Slope Clay V. Silt OM Structure
% % Fine % %
unit
sand
%
1
2
Slow
Moderate
Rangeland
Arable
10
9
40% 10
30 4
blocky
18
8
30% 20
20
2
Coarse
granular
3
Moderate to Settled
22
12
20% 15
50 3
Fine
rapid
granular
Suitability
Class
Nutrient
The suitability rating for land qualities for tomatoes and cabbage production is also
indicated below;
Suitability classes for Tomato production
Trafficability Moisture
Land Qualities
Slope
Erosion
availability
hazard
S1
1
2
2
2
2
S2
2
3
3
2
S3
3
4
3
3
4
S4…
arrow_forward
dear tutor please provide neat and clean and detailed answer.
dont copy from google
adress both questions well
arrow_forward
Problem 1: (50 points)
In Avengers 2, Captain America's improved
shield is made from unobtainium, a new
material that will soon be available in a store
near you. Unobtainium has the normal stress-
strain diagram shown. The proportional limit,
the elastic limit and the yield point are
identical in this material.
o [MPa]
2001
175
150
125
100
Fig.1 Normal stress-strain
75
50
25
0
0. 0.05 0.1 0.15 0.2 0.25
Unobtainium has a Poisson's ratio of 0.3.
a. [6pts] Identify the yield point oy, the ultimate stress ou and the fracture
stress of. Include units.
c. [25pts] A bar of unobtainium has a length of
1.5 m, a width of 100mm and a height of 50
mm, as shown. The cross-sectional area is
50mm 100mm = 5 x 10-³m². The bar is
subjected to an axial force of 375 kN.
Find the normal stress in a cross-section of the bar.
b. [5pts] How do you find Young's modulus from this graph? Find its value with units.
whesta fins dus al hoss
P = 375 KN
1.5 m
0.3
50 mm
100 mm
& [mm/mm]
Is the material within its…
arrow_forward
Summarize how at least two reference materials relate to the basic scientific principles of flying a paper plane. Each reference material must come from a different source. Be sure to describe how the references provide a foundational background for the experiment.
arrow_forward
9
arrow_forward
Question 2
In a test measuring the life span of a certain brand of tire, 100 tires are tested. The results
showed an average lifetime of 50,000 miles, with a standard deviation of 5,000 miles. One
hundred thousand of these tires have been sold and are on the road.
(a) After what mileage would you expect 10% of the tires to have worn out?
(b) How many tires are expected to wear out between 60,000 and 70,000 miles?
(c) How many tires are expected to have a life of less than 20,000 miles?
(d) What are your major assumptions in the calculations for (a), (b) and (c)?
(e) Estimate the 95% confidence interval on the population mean.
arrow_forward
I need an answer in half an hour
arrow_forward
PHYS X PHYS X
印 PHYS X
PHYS X
POTPHYS X
PHYS X
E PHYS X E PHYS
top/semester2/physics%20for%20engineers/PHYS220_CH15_Lecture%20Notes_Problems%2015 19,15.29 S
(D Page view
A Read aloud
V Draw
Problem-15-19: page-475
A 0.500-kg object attached to a spring with a force constant of 8.00 N/m vibrates in simple harmonic motion
with an amplitude of 10.0 cm. Calculate the maximum value of its
(a) speed, and acceleration.
(b) the speed and the acceleration when the object is 6.00 em from the equilibrium position, and
(c) the time interval required for the object to move from.r50 to r5 8.O0 cm.
Solution:
arrow_forward
SEE MORE QUESTIONS
Recommended textbooks for you
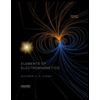
Elements Of Electromagnetics
Mechanical Engineering
ISBN:9780190698614
Author:Sadiku, Matthew N. O.
Publisher:Oxford University Press
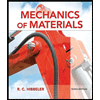
Mechanics of Materials (10th Edition)
Mechanical Engineering
ISBN:9780134319650
Author:Russell C. Hibbeler
Publisher:PEARSON
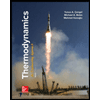
Thermodynamics: An Engineering Approach
Mechanical Engineering
ISBN:9781259822674
Author:Yunus A. Cengel Dr., Michael A. Boles
Publisher:McGraw-Hill Education
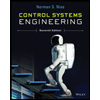
Control Systems Engineering
Mechanical Engineering
ISBN:9781118170519
Author:Norman S. Nise
Publisher:WILEY
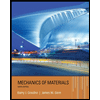
Mechanics of Materials (MindTap Course List)
Mechanical Engineering
ISBN:9781337093347
Author:Barry J. Goodno, James M. Gere
Publisher:Cengage Learning
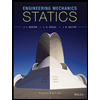
Engineering Mechanics: Statics
Mechanical Engineering
ISBN:9781118807330
Author:James L. Meriam, L. G. Kraige, J. N. Bolton
Publisher:WILEY
Related Questions
- Which of these statements are correct?arrow_forwardTest Specimen 4140 CF steel 6061 T6 Al Gray Cast iron 40 FC Brass 360 Impact Energy (J or ft-lb) 48.5 ft-lb 25 ft-lb 12 ft-lb 27 ft-lb Impact Strength (J/m or ft-lb/in) 123.096 ft-lb/in 63.452 ft-lb/in What is the final analysis/ overall observation from the data? 30.457 ft-lb/in 68.528 ft-lb/inarrow_forwardMECT361 Mechatronics Components and Instrumentation 8.1. Why is it not possible to connect sensors such as thermocouples, strain gages, and accelerometers directly to a digital computer or microprocessor? PLEASE GIVE ME THE REFRENCE I Will get zero if you didn't put the refrencearrow_forward
- Answer the following question: 1. What are the different elements of wreckage distribution in an aircraft accident investigation?arrow_forward1. Since experimentations are always subject to errors, what techniques are employed to neutralize the effects of these errors in the accuracy and validity of the experiment? 2. Why is the "factorial experiment" better in any way than a "one-factor-at-a-time" approach? 3. True or False: As soon as the experimental data (measurements) are obtained, the experimenter can already proceed with the usual significance testing. Explain. 4. What is "hypothesis testing"? How is it performed? 5.What makes ANOVA a powerful tool in hypothesis testing? What happens if you use a 2k full Factorial design to explore a set of variables which is known to have a non-linear response? 6. When is the addition of center points to a 2k full factorial design beneficial? Give a particular case that warrants its use. 7. In practical terms, explain how a LOW p-value connote SIGNIFICANCE (Recall that the smaller the p-value is, the more significant the factor becomes)?arrow_forwardPresented below are the quality ratings with regard to soil moisture availability. Erosion rating Moisture rating Erosion Rating MC (%) Rating Slope Slope rating Rating hazard class Low 1 0-5 4 0-5 1 Moderate 2 5-15 3 5-10 2 High 3 15-20 2 10-25 3 Very high 4 >20 1 >25 4 Quality ratings of three land units are tabulated below. Land quality rating Land unit Nutrient availability Trafficability 1 2 1 2 3 1 3 2 2 Additional characteristics of the land units areas follows: Land Permeability Land use M.C. Slope Clay V. Silt OM Structure % % Fine % % unit sand % 1 2 Slow Moderate Rangeland Arable 10 9 40% 10 30 4 blocky 18 8 30% 20 20 2 Coarse granular 3 Moderate to Settled 22 12 20% 15 50 3 Fine rapid granular Suitability Class Nutrient The suitability rating for land qualities for tomatoes and cabbage production is also indicated below; Suitability classes for Tomato production Trafficability Moisture Land Qualities Slope Erosion availability hazard S1 1 2 2 2 2 S2 2 3 3 2 S3 3 4 3 3 4 S4…arrow_forward
- dear tutor please provide neat and clean and detailed answer. dont copy from google adress both questions wellarrow_forwardProblem 1: (50 points) In Avengers 2, Captain America's improved shield is made from unobtainium, a new material that will soon be available in a store near you. Unobtainium has the normal stress- strain diagram shown. The proportional limit, the elastic limit and the yield point are identical in this material. o [MPa] 2001 175 150 125 100 Fig.1 Normal stress-strain 75 50 25 0 0. 0.05 0.1 0.15 0.2 0.25 Unobtainium has a Poisson's ratio of 0.3. a. [6pts] Identify the yield point oy, the ultimate stress ou and the fracture stress of. Include units. c. [25pts] A bar of unobtainium has a length of 1.5 m, a width of 100mm and a height of 50 mm, as shown. The cross-sectional area is 50mm 100mm = 5 x 10-³m². The bar is subjected to an axial force of 375 kN. Find the normal stress in a cross-section of the bar. b. [5pts] How do you find Young's modulus from this graph? Find its value with units. whesta fins dus al hoss P = 375 KN 1.5 m 0.3 50 mm 100 mm & [mm/mm] Is the material within its…arrow_forwardSummarize how at least two reference materials relate to the basic scientific principles of flying a paper plane. Each reference material must come from a different source. Be sure to describe how the references provide a foundational background for the experiment.arrow_forward
- 9arrow_forwardQuestion 2 In a test measuring the life span of a certain brand of tire, 100 tires are tested. The results showed an average lifetime of 50,000 miles, with a standard deviation of 5,000 miles. One hundred thousand of these tires have been sold and are on the road. (a) After what mileage would you expect 10% of the tires to have worn out? (b) How many tires are expected to wear out between 60,000 and 70,000 miles? (c) How many tires are expected to have a life of less than 20,000 miles? (d) What are your major assumptions in the calculations for (a), (b) and (c)? (e) Estimate the 95% confidence interval on the population mean.arrow_forwardI need an answer in half an hourarrow_forward
arrow_back_ios
SEE MORE QUESTIONS
arrow_forward_ios
Recommended textbooks for you
- Elements Of ElectromagneticsMechanical EngineeringISBN:9780190698614Author:Sadiku, Matthew N. O.Publisher:Oxford University PressMechanics of Materials (10th Edition)Mechanical EngineeringISBN:9780134319650Author:Russell C. HibbelerPublisher:PEARSONThermodynamics: An Engineering ApproachMechanical EngineeringISBN:9781259822674Author:Yunus A. Cengel Dr., Michael A. BolesPublisher:McGraw-Hill Education
- Control Systems EngineeringMechanical EngineeringISBN:9781118170519Author:Norman S. NisePublisher:WILEYMechanics of Materials (MindTap Course List)Mechanical EngineeringISBN:9781337093347Author:Barry J. Goodno, James M. GerePublisher:Cengage LearningEngineering Mechanics: StaticsMechanical EngineeringISBN:9781118807330Author:James L. Meriam, L. G. Kraige, J. N. BoltonPublisher:WILEY
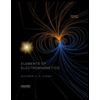
Elements Of Electromagnetics
Mechanical Engineering
ISBN:9780190698614
Author:Sadiku, Matthew N. O.
Publisher:Oxford University Press
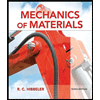
Mechanics of Materials (10th Edition)
Mechanical Engineering
ISBN:9780134319650
Author:Russell C. Hibbeler
Publisher:PEARSON
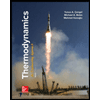
Thermodynamics: An Engineering Approach
Mechanical Engineering
ISBN:9781259822674
Author:Yunus A. Cengel Dr., Michael A. Boles
Publisher:McGraw-Hill Education
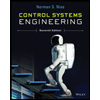
Control Systems Engineering
Mechanical Engineering
ISBN:9781118170519
Author:Norman S. Nise
Publisher:WILEY
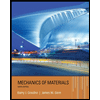
Mechanics of Materials (MindTap Course List)
Mechanical Engineering
ISBN:9781337093347
Author:Barry J. Goodno, James M. Gere
Publisher:Cengage Learning
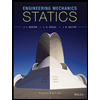
Engineering Mechanics: Statics
Mechanical Engineering
ISBN:9781118807330
Author:James L. Meriam, L. G. Kraige, J. N. Bolton
Publisher:WILEY