DAT475 Project One
docx
keyboard_arrow_up
School
Southern New Hampshire University *
*We aren’t endorsed by this school
Course
475
Subject
Mechanical Engineering
Date
Feb 20, 2024
Type
docx
Pages
12
Uploaded by ChancellorNightingale2248
Southern New Hampshire University
DAT 475 Applied Data Analysis
Project One Case Study
January 28, 2024
Preliminary Analysis Report
Problem Statement
A manufacturing company in Tijuana, Mexico produces electronic boards that go through a welding process in the Manual Finish area of the production line. Within this process the electronic boards have Thru-Holes components placed on the boards. The assembly of the electronic boards and Thru-Holes components is then welded in a wave soldering machine. The welded assembly is then quality checked by an employee who checks that the assembly does not have any welding defects. After quality check, the assembly is sent to other areas of the production for additional components to be installed.
Recently there has been an increase in demand for products produced by the company. There has also been an uptick in the defects in the welding process of the electronic boards and Thru-Holes components. These defects include the solder bridge, missing components, damaged components, lifted components, insufficient solder, and excessive solder. This increase
in defects has led to a rise in the number of assembly and electronic test problems after the electronic boards have gone through their final assembly stage (SNHU, 2023). The company is now going to comply with the requirements established by the IPC-A-
610E standard for electronic components and the products will need to be fixed before their final release. However, an assessment concluded that fixing the defects after they have gone through final assembly is cost prohibitive, time consuming, and requires staffing with specific skills. The standard IPC-A-610E criteria is not focused on processes to perform assembly operations or allow the change, modification, or repair of the final product.
In reviewing these elements, the company has requested a project to improve manufacturing defects with two outcomes. First, they would like a 20% reduction in defects generated during the welding process in three double production lines (SNHU, 2023). Second, a 20% increase in the capacity of the three double production lines where the boards are processed, while not increasing the percentage of defects (SNHU, 2023). By decreasing the manufacturing defects and expanding the capacity of the production line the company will reduce costs and improve quality of their products. This will allow the company to meet the greater demand for their products.
Cause(s) of the Identified Organizational Problem
The company provided defect data sets for three of their models as well as the entire facility. The data will be analyzed utilizing Pareto charts that I have created. I will use the 80/20 rule. This will allow us to determine what areas are causing the most defects. The company can then focus on the concerns where the defects fall below the 80% defect percentage. The Pareto charts help to determine what the most significant defects are. The most significant causes of defects are shown in Figures 1 thru 4 below.
Model 595407-XXX-00
The Model 595407-XXX-00 issues that had 80% of defects were solder bridge, missing component, lifted component, damaged component, excessive solder, reversed component, and solder void. Component broken, pin hole, and long terminals all had zero defects. All results
are shown in Figure 1 below.
Your preview ends here
Eager to read complete document? Join bartleby learn and gain access to the full version
- Access to all documents
- Unlimited textbook solutions
- 24/7 expert homework help
Figure 1-Defects for Model 595407-XXX-00
Model 595481-00X-00
The Model 595481-00X-00 issues that had 80% of defects were solder bridge, lifted component, wrong component, pin damaged, missing component, excessive solder, and reversed component. Component misalignment, pin holes, and long terminals all had zero defects. All results are shown in Figure 2 below.
Figure 2-Defects for Model 595481-00X-00
Model 595310-001-00
The Model 595310-001-00 issues that had 80% of defects were excessive solder, solder bridge, damaged component, and pin damaged. The issues with zero defects were billboarding, trace open, component broken, and long terminals. All results are seen in Figure 3 below.
Figure 3-Defects for Model 595310-001-00 Entire Facility
Defects that were 80% for the entire facility are solder bridge, excessive solder, missing component, lifted component, damaged component, pin damaged, and wrong component. Long terminals had zero defects. Results are seen in Figure 4 below.
Your preview ends here
Eager to read complete document? Join bartleby learn and gain access to the full version
- Access to all documents
- Unlimited textbook solutions
- 24/7 expert homework help
Figure 4-Defects for Entire Facility
Root Cause Analysis
Using the data from the Pareto charts for the three models and entire facility will allow us to gather further insights into the defect problems in the manufacturing company. These insights will then allow us to know what areas of manufacturing process need adjustments based on the types of defects the Pareto charts have identified. Utilizing the 80/20 rule, we can focus on the top 20% of defects provided by the charts. For Model 595407-XXX-00 the highest areas of concern were solder bridge, missing component, lifted component, damaged component, excessive solder, reversed component, and solder void. For Model 595481-00X-00, the areas of concern were solder bridge, lifted component, wrong component, pin damaged, missing component, excessive solder, and reversed component. For Model 595310-001-00, the areas of concern were excessive solder, solder bridge, damaged component, and pin damaged.
Finally, for the entire facility, the highest areas of concern were solder bridge, excessive solder, missing component, lifted component, damaged component, pin damaged, and wrong component.
By identifying the vital few, we know that those areas require the most attention and enhancements (nsw.gov.au). The issues identified in the charts for the models and entire facility that fall under the 80% cutoff line should be the issues that are focused on as they are the most problematic. By focusing on the vital few, we can decrease 20% of the defects in the welding process, in turn leading to a 20% increase in productivity in the three double production lines where the electronic boards are being produced.
Figure 5-Root Cause Analysis Fishbone Diagram
After reviewing the data, the reasons for defects were grouped into four categories as seen in Figure 5 above. These categories are Training, Process, Employees, and Equipment. The company should examine these categories and causes to determine the root cause to why there
has been an increase in defects in their product.
The first category is Process. This has been broken down into four subcategories. These subcategories are confirming the correct placement of the Thru-Holes Components on the Electronic Boards, verification of the placement and solder of components, correct welding of the components, and a quality inspection for welding defects. The company needs to ensure that the welding process of the Thru-Holes Component to the electronic boards was done accurately and to standards. This entails confirming the accurate placement of the Thru-Holes Components to the electronic boards, verifying the correct placement of the assembly on the wave soldering machine, verifying that all components are present, placed, and welded as they should be, and that a quality inspection of the assembly has been completed on all welding components to verify no defects exist. When all employees follow the appropriate process and procedures, this should decrease the number of defects. This, along with the updated training of employees and the training of the usage of tools, should also decrease the number of defects.
The second category is Training which has three subcategories. The subcategories are detailed training is unavailable, current training is unclear, and employees are not receiving training on specific tools that they are using. All employees should have proper training
Your preview ends here
Eager to read complete document? Join bartleby learn and gain access to the full version
- Access to all documents
- Unlimited textbook solutions
- 24/7 expert homework help
conducted in order for them to do their job efficiently, effectively, and correctly. This is not the case. A more detailed training could be created to break down the process into smaller sections so that the employees understand the process they are doing, the types of machines they are using, and the importance of why following the steps outlined are important to the outcome of the product. Employees working with a specific tool should be well trained on how to use that tool. Training that shows how to use each tool, what to look for to ensure accuracy and what defects to look for are imperative for these employees to know as they work with these tools. There could also be a lead employee that is responsible for the training of staff on these specific
tools and areas along with a signoff that training as been completed. Also, a refresher training once a year at minimum is suggested.
The third category is Employees and has four subcategories. The four subcategories are overworked employees, short-staffed, inadequate training, and lack of understand of the welding process. Due to the rise in demand for the company’s products, the current employees may be overworked and that is part of the reason defects are being missed. The company is short staffed as the rise in demand has not coincided with the increase in hiring of new employees. The employees that are working did not receive adequate training and lack the understanding of the welding process, which will also cause them to miss the defects that could be present. Employees should be trained not only on what the correct assembly of welding looks like, but also what an incorrect assembly and welding process looks like. This will help employees identify the defects more accurately. The company would need to increase their staff
to fulfill their increase in orders as well as their capacity to handle to the workload. Having more
employees will allow current staff to not feel overwhelmed and overworked. They can do their
job more efficiently by moving at a slower pace and not feel rushed, which causes defects to be missed as well.
The last category is Equipment, and it has three subcategories. The three subcategories are maintenance of equipment and/or machines, proper utilization of the equipment, and configuration and calibration of the equipment. Equipment is the largest factor in a manufacturing process. The proper utilization of equipment that is needed for each step of the manufacturing process is imperative. The equipment needs to be configured for each specific task, calibrated for its specific function, and maintained as required. The failure and breakdown of these machines could have a significant impact on the production of the electronic boards and could cause a number of defects.
Like any problem, there will be factors that are dependent on others. One the causal factor in this organizational problem is that the current training is inadequate. This is seen in both the Employee and Training factors and could also fall under Process factor. If the employees are not trained properly, they will not fully understand the process and procedure, or know what to look for in a properly constructed product versus a product with defects. This is
a crucial factor that needs to be addressed. Delving deeper into these four categories and their causal factors will allow the manufacturing company to determine ways to improve their performance and decrease their defects.
References
NSW Government (n.d.). Pareto Charts & 80/20 Rule. Pareto Charts & 80-20 Rule - Clinical Excellence Commission (nsw.gov.au)
SNHU (2023). DAT-475 Project Case Study. SNHU. DAT 475 Project Case Study.pdf (snhu.edu)
Your preview ends here
Eager to read complete document? Join bartleby learn and gain access to the full version
- Access to all documents
- Unlimited textbook solutions
- 24/7 expert homework help
Related Documents
Related Questions
A Team of Engineers asked for an internal combustion engine to use it in a designed car. Your role is to describe the operation sequence of different types of available engines, explain their mechanical efficiency, and deliver a detailed technical report to show your approach in solving and discussing the following tasks and issues.
You must follow the following steps to help the team:
STEP 1
Describe the operational sequence of four-stroke spark ignition and four-stroke compression ignition engines with the aid of sketches by constructing simple sketch representing the operation and plotting the P-V diagrams for each process during the cycle to show the following:
The input and output heat and net output work
The expansion and compression strokes
The air-fuel mixture intake and exhaust gasses
The spark plug when it is in the active mode
The complete cycle of ideal Otto and Diesel cycles that shows the input and output heat and net output work.
STEP 2
Explain the mechanical…
arrow_forward
Case Study – The New Engineer
Jeff was just hired by GSI, Inc. to be their Environmental and Safety Coordinator. This is Jeff's first position after completing his engineering degree. He had taken a course in safety engineering as part of his studies and felt confident that he could handle the job.
Management at GSI, Inc. has assured him that they are committed to maintaining a safe workplace. They have never had an individual dedicated to this task full-time. They will implement his recommendations if he can justify them.
As Jeff begins to get familiar with the operations, he spends considerable time on the production floor. He notices workers clean their tools before break with a liquid from an unmarked 55-gallon drum. They also use this liquid to clean residue from their skin. They use paper towels to dry their tools and hands, throw these towels in the trash, and head to the break room for a snack and/or smoke.
In talking with the workers, Jeff learns of some of…
arrow_forward
Case Study – The New Engineer
Jeff was just hired by GSI, Inc. to be their Environmental and Safety Coordinator. This is Jeff's first position after completing his engineering degree. He had taken a course in safety engineering as part of his studies and felt confident that he could handle the job.
Management at GSI, Inc. has assured him that they are committed to maintaining a safe workplace. They have never had an individual dedicated to this task full-time. They will implement his recommendations if he can justify them.
As Jeff begins to get familiar with the operations, he spends considerable time on the production floor. He notices workers clean their tools before break with a liquid from an unmarked 55-gallon drum. They also use this liquid to clean residue from their skin. They use paper towels to dry their tools and hands, throw these towels in the trash, and head to the break room for a snack and/or smoke.
In talking with the workers, Jeff learns of some of…
arrow_forward
The foreman in the welding department wanted to know what value of allowance to use for a particular section of the shop. A work sampling study was authorized. Only two activity categories were considered: (1) welding and other productive work, (2) personal time, rest breaks and delays. Over a four-week period, where there are 40 hours per week, 161 observations are made at random times. Each observation captured the category of activity of each of 12 welders in the shop section of interest. Results indicated that category 2 constituted 17 % of the total observations.
(a) Can you conclude that realized PFD is 17 % in the factory at 100*(1-0.02) % confidence level with 7% precision?
(b) If a total of 88 work units were produced during the 4 weeks, and all category 1 activity was devoted to producing these units, what was the average time spent on each unit?
arrow_forward
The worker shown below is using a 10-lb pneumatic nut runner to tighten nuts within a tractor cab compartment. What are health and safety problems likely to result from her job? Evaluate the job and the
workstation identifying poor work design features. Please come up with at least five poor design features.
(Please refer to the format of the answers in the class example solution)
No.
1
2
3
4
園
5
Problem
Ergonomics Improvement
Design Principle
arrow_forward
LESSON: AUTODESK AUTOCAD
Choose from the choices:
arrow_forward
Please answer the 4th question
arrow_forward
Problem 2:
Review the below link, and choose 3 practical examples to solve structural/performance-based issues using
finite element product. Discuss what you understand from these examples. Use your own words.
https://www.hitechfea.com/fea-projects.html
hitech
Since
Your Partner in Digital Excellence 1992
SERVICES ✓ PROJECTS ✓
» FEA Projects
CLIENTS
FEA shortens the Design
Cycle for Thermal Radiation
Detector System for Power
Plant
BLOG
ABOUT US CONTACT US
Finite Element Analysis - FEA Projects / Case Studies
Please review few of the FEA projects, FEA case studies and FEA work samples that represent the FEA
solutions HiTech FEA engineers have provided to our global clientele from different industries.
Simulation using ANSYS
Professional NLS helps to
reduce Product Development
Cycle
Effective Static Structural
Services conducting
Structural Seismic Analysis of
RTO System Base
arrow_forward
Which one is the correct answer for this question please ?
arrow_forward
5 Look at the flow chart showing the steps of the design process. Then read the list of
steps for designing a thermos. These steps are not in order. Write the letter of each
step in the appropriate box of the flow chart.
The Design Process
Find a problem
Keep records
Plan and build
a prototype
Keep records
Test and
improve
Keep records
Communicate
the solution
arrow_forward
Please assist with answering the following question?
arrow_forward
I need answers to questions 10, 11, and 12 pertaining to the print provided.
Note: A tutor keeps putting 1 question into 3 parts and wasted so many of my questions. Never had a issue before until now, please allow a different tutor to answer because I was told I am allowed 3 of these questions.
arrow_forward
Do not provide handwritten solution,Maintain accuracy and quality in your answer,Take care of plagiarism,Answer completely,You will get up vote for sure.
arrow_forward
SEE MORE QUESTIONS
Recommended textbooks for you
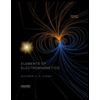
Elements Of Electromagnetics
Mechanical Engineering
ISBN:9780190698614
Author:Sadiku, Matthew N. O.
Publisher:Oxford University Press
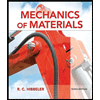
Mechanics of Materials (10th Edition)
Mechanical Engineering
ISBN:9780134319650
Author:Russell C. Hibbeler
Publisher:PEARSON
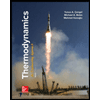
Thermodynamics: An Engineering Approach
Mechanical Engineering
ISBN:9781259822674
Author:Yunus A. Cengel Dr., Michael A. Boles
Publisher:McGraw-Hill Education
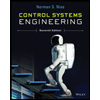
Control Systems Engineering
Mechanical Engineering
ISBN:9781118170519
Author:Norman S. Nise
Publisher:WILEY
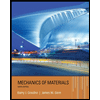
Mechanics of Materials (MindTap Course List)
Mechanical Engineering
ISBN:9781337093347
Author:Barry J. Goodno, James M. Gere
Publisher:Cengage Learning
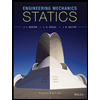
Engineering Mechanics: Statics
Mechanical Engineering
ISBN:9781118807330
Author:James L. Meriam, L. G. Kraige, J. N. Bolton
Publisher:WILEY
Related Questions
- A Team of Engineers asked for an internal combustion engine to use it in a designed car. Your role is to describe the operation sequence of different types of available engines, explain their mechanical efficiency, and deliver a detailed technical report to show your approach in solving and discussing the following tasks and issues. You must follow the following steps to help the team: STEP 1 Describe the operational sequence of four-stroke spark ignition and four-stroke compression ignition engines with the aid of sketches by constructing simple sketch representing the operation and plotting the P-V diagrams for each process during the cycle to show the following: The input and output heat and net output work The expansion and compression strokes The air-fuel mixture intake and exhaust gasses The spark plug when it is in the active mode The complete cycle of ideal Otto and Diesel cycles that shows the input and output heat and net output work. STEP 2 Explain the mechanical…arrow_forwardCase Study – The New Engineer Jeff was just hired by GSI, Inc. to be their Environmental and Safety Coordinator. This is Jeff's first position after completing his engineering degree. He had taken a course in safety engineering as part of his studies and felt confident that he could handle the job. Management at GSI, Inc. has assured him that they are committed to maintaining a safe workplace. They have never had an individual dedicated to this task full-time. They will implement his recommendations if he can justify them. As Jeff begins to get familiar with the operations, he spends considerable time on the production floor. He notices workers clean their tools before break with a liquid from an unmarked 55-gallon drum. They also use this liquid to clean residue from their skin. They use paper towels to dry their tools and hands, throw these towels in the trash, and head to the break room for a snack and/or smoke. In talking with the workers, Jeff learns of some of…arrow_forwardCase Study – The New Engineer Jeff was just hired by GSI, Inc. to be their Environmental and Safety Coordinator. This is Jeff's first position after completing his engineering degree. He had taken a course in safety engineering as part of his studies and felt confident that he could handle the job. Management at GSI, Inc. has assured him that they are committed to maintaining a safe workplace. They have never had an individual dedicated to this task full-time. They will implement his recommendations if he can justify them. As Jeff begins to get familiar with the operations, he spends considerable time on the production floor. He notices workers clean their tools before break with a liquid from an unmarked 55-gallon drum. They also use this liquid to clean residue from their skin. They use paper towels to dry their tools and hands, throw these towels in the trash, and head to the break room for a snack and/or smoke. In talking with the workers, Jeff learns of some of…arrow_forward
- The foreman in the welding department wanted to know what value of allowance to use for a particular section of the shop. A work sampling study was authorized. Only two activity categories were considered: (1) welding and other productive work, (2) personal time, rest breaks and delays. Over a four-week period, where there are 40 hours per week, 161 observations are made at random times. Each observation captured the category of activity of each of 12 welders in the shop section of interest. Results indicated that category 2 constituted 17 % of the total observations. (a) Can you conclude that realized PFD is 17 % in the factory at 100*(1-0.02) % confidence level with 7% precision? (b) If a total of 88 work units were produced during the 4 weeks, and all category 1 activity was devoted to producing these units, what was the average time spent on each unit?arrow_forwardThe worker shown below is using a 10-lb pneumatic nut runner to tighten nuts within a tractor cab compartment. What are health and safety problems likely to result from her job? Evaluate the job and the workstation identifying poor work design features. Please come up with at least five poor design features. (Please refer to the format of the answers in the class example solution) No. 1 2 3 4 園 5 Problem Ergonomics Improvement Design Principlearrow_forwardLESSON: AUTODESK AUTOCAD Choose from the choices:arrow_forward
- Please answer the 4th questionarrow_forwardProblem 2: Review the below link, and choose 3 practical examples to solve structural/performance-based issues using finite element product. Discuss what you understand from these examples. Use your own words. https://www.hitechfea.com/fea-projects.html hitech Since Your Partner in Digital Excellence 1992 SERVICES ✓ PROJECTS ✓ » FEA Projects CLIENTS FEA shortens the Design Cycle for Thermal Radiation Detector System for Power Plant BLOG ABOUT US CONTACT US Finite Element Analysis - FEA Projects / Case Studies Please review few of the FEA projects, FEA case studies and FEA work samples that represent the FEA solutions HiTech FEA engineers have provided to our global clientele from different industries. Simulation using ANSYS Professional NLS helps to reduce Product Development Cycle Effective Static Structural Services conducting Structural Seismic Analysis of RTO System Basearrow_forwardWhich one is the correct answer for this question please ?arrow_forward
- 5 Look at the flow chart showing the steps of the design process. Then read the list of steps for designing a thermos. These steps are not in order. Write the letter of each step in the appropriate box of the flow chart. The Design Process Find a problem Keep records Plan and build a prototype Keep records Test and improve Keep records Communicate the solutionarrow_forwardPlease assist with answering the following question?arrow_forwardI need answers to questions 10, 11, and 12 pertaining to the print provided. Note: A tutor keeps putting 1 question into 3 parts and wasted so many of my questions. Never had a issue before until now, please allow a different tutor to answer because I was told I am allowed 3 of these questions.arrow_forward
arrow_back_ios
SEE MORE QUESTIONS
arrow_forward_ios
Recommended textbooks for you
- Elements Of ElectromagneticsMechanical EngineeringISBN:9780190698614Author:Sadiku, Matthew N. O.Publisher:Oxford University PressMechanics of Materials (10th Edition)Mechanical EngineeringISBN:9780134319650Author:Russell C. HibbelerPublisher:PEARSONThermodynamics: An Engineering ApproachMechanical EngineeringISBN:9781259822674Author:Yunus A. Cengel Dr., Michael A. BolesPublisher:McGraw-Hill Education
- Control Systems EngineeringMechanical EngineeringISBN:9781118170519Author:Norman S. NisePublisher:WILEYMechanics of Materials (MindTap Course List)Mechanical EngineeringISBN:9781337093347Author:Barry J. Goodno, James M. GerePublisher:Cengage LearningEngineering Mechanics: StaticsMechanical EngineeringISBN:9781118807330Author:James L. Meriam, L. G. Kraige, J. N. BoltonPublisher:WILEY
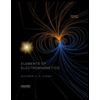
Elements Of Electromagnetics
Mechanical Engineering
ISBN:9780190698614
Author:Sadiku, Matthew N. O.
Publisher:Oxford University Press
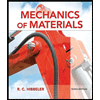
Mechanics of Materials (10th Edition)
Mechanical Engineering
ISBN:9780134319650
Author:Russell C. Hibbeler
Publisher:PEARSON
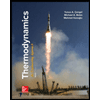
Thermodynamics: An Engineering Approach
Mechanical Engineering
ISBN:9781259822674
Author:Yunus A. Cengel Dr., Michael A. Boles
Publisher:McGraw-Hill Education
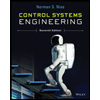
Control Systems Engineering
Mechanical Engineering
ISBN:9781118170519
Author:Norman S. Nise
Publisher:WILEY
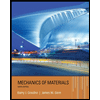
Mechanics of Materials (MindTap Course List)
Mechanical Engineering
ISBN:9781337093347
Author:Barry J. Goodno, James M. Gere
Publisher:Cengage Learning
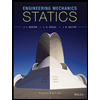
Engineering Mechanics: Statics
Mechanical Engineering
ISBN:9781118807330
Author:James L. Meriam, L. G. Kraige, J. N. Bolton
Publisher:WILEY