IND 115 Final Exam Fall 2022A (turn in)
docx
keyboard_arrow_up
School
Tidewater Community College *
*We aren’t endorsed by this school
Course
298
Subject
Mechanical Engineering
Date
Feb 20, 2024
Type
docx
Pages
10
Uploaded by DeaconGerbil2297
IND 115 Final Exam Fall 2022
Name _Maleek Goodman___________________
Professor Pruden
1.
Name the four (4) methods in which a work part can be held in an engine lathe.
Between centers, chuck, face plate, and collet 2. Identify three desirable properties of a cutting-tool material.
Toughness, hot hardness, and wear resistance. 3.
Abrasives commonly found in nature include all of following except:
A.
Emery B.
Garnet *typo maybe? all are natural. C.
Quartz
D.
Garnet
4.
The following are finishing operations except:
A.
Honing
B. Superfinishing
C. Lapping
D.
Barreling
5.
Name the two (2) reasons for using cutting fluid in a machining operation.
To flush away chip pieces from cutting zone and for lubrication 6.
Define machinability.
Machinability is the ease with which a given material may be worked with a cutting tool.
7.
What does the heat treatment of metals process involve?
the use of heating or chilling, normally to extreme temperatures, to achieve the desired result such
as hardening or softening of a material.
8.
Name the five (5) joint types in joining two metal plates or wooden boards.
Butt, corner, T, lap, and edge joints.
9.
Electrode coating functions include all of these except:
A.
To Provide Deoxidizers & Scavengers B.
To Increase Deposit Rates
C.
To Minimize Gases
D.
To Produce a Slag Covering
E.
To Provide Mechanical and Physical Properties
10. Describe the submerged-arc welding (SMAW) process. Submerged arc welding is an arc welding process in which metals are joined using an electrical arc established between a continuous fed bar metal consumable electrode or electrodes and the work.
11. List five (5) methods of mechanical assembly that allow for easy disassembly.
Threaded fasteners such as nuts, bolts, and screws, anchors, and rivets.
12. Identify five (5) advantages of adhesive bonding compared to alternative joining methods.
1.
Process is applicable to a wide variety of material, 2. Parts of different sizes and cross sections be joined,3. Bonding occurs over the welding, 4. Some adhesives are flexible after bonding and are thus tolerant of cuclical loading and differences in thermal expansions, 5. Low temp curing avoids damage to parts being joined
13.The soldering process shown here
Can be described how? 2 different metals are welded with soldering
13. Material handling in manufacturing operations is usually associated with activities that occur inside a facility and not with transportation between facilities involving rail, truck, air, or waterway delivery of goods: TRUE FALSE
14. Automated 100% inspection can be integrated with the manufacturing process to accomplish which TWO of the following. (CIRCLE)
(a) better design of products
(b) feedback of data to adjust the process
(c) 100% perfect quality
(d) sortation of good parts from defects
15. Which one of the following is an example of contact inspection? (CIRCLE)
(a) coordinate measuring systems
(b) machine vision
c) radiation techniques
(d) scanning laser systems
(e) ultrasonic techniques
16. Statistical Process Control (SPC) involves using various statistical methods to assess and analyze variations in a process. One tool is a control chart. What does a control chart show?
show how a process performs over a period of time
17. What is Six Sigma in relation to quality assurance? Six Sigma is
a quality management methodology used to help businesses improve current processes, products, or services by discovering and eliminating defects.
Your preview ends here
Eager to read complete document? Join bartleby learn and gain access to the full version
- Access to all documents
- Unlimited textbook solutions
- 24/7 expert homework help
18. Review the Stress-Strain diagram below. Identify the point on the diagram that engineers use as a maximum anticipated load on a structure’s components. (CIRCLE)
Ultimate strength 19. What five (5) advantages of cold working have over hot working?
(1)
better accuracy, (2) better surface finish, (3) increased strength due to work hardening,
(4) possible directional properties due to grain
flow, and (5) no heating of work required.
20. How is hardness rating determined in metals? The rockwell test
21. Anything over 10 secs is good for transitioning from Austinite to Pearlite T/F
22. Gussets, Islands, shelfs and ceilings are all support structures for rapid prototyping? T/F true
23. Anodizing is an electrolytic treatment that produces an oxide layer on a metallic surface. Applications include:
A.
Zinc
B.
Titanium
C. Magnesium
D.
All of the above
E.
None of the above
24. Define nanotechnology.
Nanotechnology is
a field of research and innovation concerned with building 'things' - generally,
materials and devices - on the scale of atoms and molecules.
25. What is a polymer?
a long molecule consisting of many similar or identical building blocks linked by a dehydration reactions.
26. What Circuitization Method is shown below? 27. What is unique about a thermoplastic polymer?
They can be melted and reformed multiple times before they start to lose their strength and integrity.
28. What percentage of iron must be in iron ore for it to be profitable to mine?
60%
29. Identify the process used to produce aluminum.
Smelting
Hall-Heroult process
30. Define tolerance in relation to dimensions and surface flatness of work pieces. A tolerance is an acceptable amount of dimensional variation that will still allow an object to function correctly.
31. How are nongraduated measuring devices used in determining the dimensions of a work piece? Non-graduated measuring devices are used
to make comparisons between dimensions or to transfer a dimension for measurement by a graduated device.
Your preview ends here
Eager to read complete document? Join bartleby learn and gain access to the full version
- Access to all documents
- Unlimited textbook solutions
- 24/7 expert homework help
32. Name the two (2) methods for producing steel
today.
Blast furnace and oxygen arc furnace 33. What organizations have oversight over classification of steel alloys? (CIRCLE)
a.
AISI-SAE
b.
SAE
c.
AISI
d.
All the above
34. The _______induction__________________ furnace is used for aluminum alloy production.
35. The Automation pyramid has 5 levels, maintenance is done at what level(s)?
Field level
36. Reasons for using unit loads in material handling include:
A.
Multiple items handled simultaneously
B. Required number of trips is reduced
C. Use of barcodes to track.
D. A and B
D. B and C
E. All of the above
37. This diagram represents what process: Stereolithography
38. Design for manufacturing assembly and design for assembly BOTH attempt to favorably influence manufacturability of a product. (CIRCLE) TRUE FALSE
39. Surface processing often requires coating a metal surface. Identify three (3) reasons for doing so. deburring, improving smoothness, adding luster,
40. Before making a final decision on changing the material in a current component or product, engineers should consult a materials data base to research potential alternative materials to investigate, their characteristics and molecular structure as well as cost. (CIRCLE)
TRUE FALSE
Your preview ends here
Eager to read complete document? Join bartleby learn and gain access to the full version
- Access to all documents
- Unlimited textbook solutions
- 24/7 expert homework help
41. A quality assurance program guarantees that all products made will be 100% perfect and without flaws.
TRUE FALSE
42. Quality of products sold or distributed is a manufacturing “holy grail” that will make future sales more plausible and possible.
TRUE FALSE 43.
Describe the true value on the pictures below a,b,c in terms of accuracy and precision.
a.
the true value is accurate but not precise. That’s why the true value is in the middle if the curve. so large number of values fall in the accurate region. but since the variance is large the precision
is less.
b.
The values are more precise but not accurate. We can see the true value falls in large distance from the mean. so, it shows the value measured is not accurate but more precise due to small variance.
c.
the values are more precise and accurate. since mean coincide with the values are more accurate and the variance is very low, so the values are more precise.
Related Documents
Related Questions
Question 3.
Three tool materials are to be compared for the same finish turning operation on a batch of 100 steel parts: high speed steel, cemented
carbide, and ceramic. For the high speed steel tool, the 170 Taylor equation parameters are: n= 0.125 and C= 70. The price of the HSS
tool is $15.00 and it is estimated that it can be ground and reground 15 times at a cost of $1.50. Tool change time = 3 min. Both carbide
and ceramic tools are in insert form and can be held in the same mechanical toolholder. The Taylor equation parameters for the cemented
carbide are: n = 0.25 and C = 500; and for the ceramic: n = 0.6 and C = 3,000. The cost per insert for the carbide = $6.00 and for the
ceramic = $8.00. Number of cutting edges per insert in both cases = 6. Tool change time = 1.0 min for both tools. Time to change parts
= 2.0 min. Feed = 0.25 mm/rev, and depth = 3.0 mm. The cost of machine time = $30/hr. The part dimensions are: diameter = 56.0 mm
and length = 290 mm. Setup time for the…
arrow_forward
Question 1
By using a labelled diagram describe the function of a horizontal milling machine.
Describe two methods of producing screw threads in the workshop.
Describe the various tool life criteria that are used to estimate the life of a cutting tool.
Describe the various milling cutters that are used on a vertical and horizontal milling machine and state for what purpose they are used.
Describe 2 methods of producing tapers on a lathe machine.
Your answers to each question should be supported by suitable diagrams for clarity.
arrow_forward
a) A face milling operation is not yielding the required surface finish on the work. The cutter is a
four-tooth insert type face milling cutter. The machine shop foreman thinks the problem is that
the work material is too ductile for the job, but this property tests well within the ductility range
for the material specified by the designer. Without knowing any more about the job, describe
THREE (3) changes in
i.
cutting conditions
ii. tooling
would you suggest to improve the surface finish?
arrow_forward
5. What are the adverse effects of tool wear in cutting processes?
6. What characteristics are required for cutting tool materials?
V. Comprehensive questions.
1. Match each part with the most proper manufacturing process.
(1) Aluminum beverage can
Centrifugal casting
(2) Copper wire
Closed-die forging
(3) Engine cylinder
Die casting
(4) Lathe body
Drawing
(5) Link rod of an engine
Sand casting
(6) Magnesium alloy camera frame
Sheet-metal forming
arrow_forward
Write TRUE is the statement/s is True. If the statement is false, identify the word/s that makes the sentence incorrect and write its corresponding correct answer.
Alterations on the independent factors during cutting process can cause tool wear. Surface finish and surface integrity of the workpiece are affected by the tool shape and its sharpness.
arrow_forward
how would i do the Chamfering for this part on the lathe?
what cutting tool would i use
what angle
what rpm
arrow_forward
a. If rough milling of mild steel is performed using High Speed Steel (HSS) side and face
milling cutter of 100 mm diameter, what rpm should be used.
b. If finish turning of a shaft is done to reduce its diameter from 24 mm to 20 mm using
carbide tool, what rpm should be used.
Metric Surface Speeds in m/min (Cutting Speed)
Tool Material
Aluminum
Drilling
Carbide
90 - 115
Milling - Rough
Carbide
Milling - Finish
Carbide
120 - 240
Turning
Carbide Rough Carbide Finish
HSS
HSS
HSS
55 - 60
120 - 240
150 - 270
75 - 105
60 - 90
60 - 90
135 - 180
Brass
40 - 45
75 - 100
45 - 60
60 - 75
90 - 210
105 - 210
135 - 260
35 - 45
55 - 75
60 - 90
75 - 105
60 - 100
Cast Iron
12 - 18
15 - 25
25 - 30
60 - 90
75 - 135
Mild Steel
10 - 15
75 - 105
75 - 120
18 - 27
18 -3-
45 - 60
23 - 40
100 - 145
Stainless Steel
8 - 18
25 - 37
10 - 15
55 - 67
12 - 25
85 - 150
arrow_forward
The following data was obtained from an
orthogonal cutting test.
Rake angle = 20° Depth of cut = 6 mm
Feed rate = 0.25 mm/rev Cutting speed = 0.6
m/s
Chip length before cutting = 29.4 mm
Vertical cutting force = 1050 N
Horizontal cutting force = 630 N
Chip length after cutting = 12.9 mm
Using Merchant's analysis, calculate
(a) Magnitude of resultant force, (b) shear plane
angle, (c) friction force and friction angle, and (d)
various energies consumed.
arrow_forward
SEE MORE QUESTIONS
Recommended textbooks for you
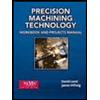
Precision Machining Technology (MindTap Course Li...
Mechanical Engineering
ISBN:9781285444543
Author:Peter J. Hoffman, Eric S. Hopewell, Brian Janes
Publisher:Cengage Learning
Related Questions
- Question 3. Three tool materials are to be compared for the same finish turning operation on a batch of 100 steel parts: high speed steel, cemented carbide, and ceramic. For the high speed steel tool, the 170 Taylor equation parameters are: n= 0.125 and C= 70. The price of the HSS tool is $15.00 and it is estimated that it can be ground and reground 15 times at a cost of $1.50. Tool change time = 3 min. Both carbide and ceramic tools are in insert form and can be held in the same mechanical toolholder. The Taylor equation parameters for the cemented carbide are: n = 0.25 and C = 500; and for the ceramic: n = 0.6 and C = 3,000. The cost per insert for the carbide = $6.00 and for the ceramic = $8.00. Number of cutting edges per insert in both cases = 6. Tool change time = 1.0 min for both tools. Time to change parts = 2.0 min. Feed = 0.25 mm/rev, and depth = 3.0 mm. The cost of machine time = $30/hr. The part dimensions are: diameter = 56.0 mm and length = 290 mm. Setup time for the…arrow_forwardQuestion 1 By using a labelled diagram describe the function of a horizontal milling machine. Describe two methods of producing screw threads in the workshop. Describe the various tool life criteria that are used to estimate the life of a cutting tool. Describe the various milling cutters that are used on a vertical and horizontal milling machine and state for what purpose they are used. Describe 2 methods of producing tapers on a lathe machine. Your answers to each question should be supported by suitable diagrams for clarity.arrow_forwarda) A face milling operation is not yielding the required surface finish on the work. The cutter is a four-tooth insert type face milling cutter. The machine shop foreman thinks the problem is that the work material is too ductile for the job, but this property tests well within the ductility range for the material specified by the designer. Without knowing any more about the job, describe THREE (3) changes in i. cutting conditions ii. tooling would you suggest to improve the surface finish?arrow_forward
- 5. What are the adverse effects of tool wear in cutting processes? 6. What characteristics are required for cutting tool materials? V. Comprehensive questions. 1. Match each part with the most proper manufacturing process. (1) Aluminum beverage can Centrifugal casting (2) Copper wire Closed-die forging (3) Engine cylinder Die casting (4) Lathe body Drawing (5) Link rod of an engine Sand casting (6) Magnesium alloy camera frame Sheet-metal formingarrow_forwardWrite TRUE is the statement/s is True. If the statement is false, identify the word/s that makes the sentence incorrect and write its corresponding correct answer. Alterations on the independent factors during cutting process can cause tool wear. Surface finish and surface integrity of the workpiece are affected by the tool shape and its sharpness.arrow_forwardhow would i do the Chamfering for this part on the lathe? what cutting tool would i use what angle what rpmarrow_forward
- a. If rough milling of mild steel is performed using High Speed Steel (HSS) side and face milling cutter of 100 mm diameter, what rpm should be used. b. If finish turning of a shaft is done to reduce its diameter from 24 mm to 20 mm using carbide tool, what rpm should be used. Metric Surface Speeds in m/min (Cutting Speed) Tool Material Aluminum Drilling Carbide 90 - 115 Milling - Rough Carbide Milling - Finish Carbide 120 - 240 Turning Carbide Rough Carbide Finish HSS HSS HSS 55 - 60 120 - 240 150 - 270 75 - 105 60 - 90 60 - 90 135 - 180 Brass 40 - 45 75 - 100 45 - 60 60 - 75 90 - 210 105 - 210 135 - 260 35 - 45 55 - 75 60 - 90 75 - 105 60 - 100 Cast Iron 12 - 18 15 - 25 25 - 30 60 - 90 75 - 135 Mild Steel 10 - 15 75 - 105 75 - 120 18 - 27 18 -3- 45 - 60 23 - 40 100 - 145 Stainless Steel 8 - 18 25 - 37 10 - 15 55 - 67 12 - 25 85 - 150arrow_forwardThe following data was obtained from an orthogonal cutting test. Rake angle = 20° Depth of cut = 6 mm Feed rate = 0.25 mm/rev Cutting speed = 0.6 m/s Chip length before cutting = 29.4 mm Vertical cutting force = 1050 N Horizontal cutting force = 630 N Chip length after cutting = 12.9 mm Using Merchant's analysis, calculate (a) Magnitude of resultant force, (b) shear plane angle, (c) friction force and friction angle, and (d) various energies consumed.arrow_forward
arrow_back_ios
arrow_forward_ios
Recommended textbooks for you
- Precision Machining Technology (MindTap Course Li...Mechanical EngineeringISBN:9781285444543Author:Peter J. Hoffman, Eric S. Hopewell, Brian JanesPublisher:Cengage Learning
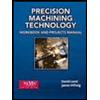
Precision Machining Technology (MindTap Course Li...
Mechanical Engineering
ISBN:9781285444543
Author:Peter J. Hoffman, Eric S. Hopewell, Brian Janes
Publisher:Cengage Learning