CEE370L_Lab_05_Shi, He
pdf
keyboard_arrow_up
School
University of Hawaii *
*We aren’t endorsed by this school
Course
370
Subject
Mechanical Engineering
Date
Feb 20, 2024
Type
Pages
14
Uploaded by SuperDangerPuppy48
CEE 370 Mechanics of Materials Lab
BEAM BENDING THEORY
He Shi
University of Hawaii at Manoa
CEE 370L Mechanics of Materials
Nov 26, 2023
1
CEE 370L Mechanics of Materials
Laboratory 1
Fall 2023
EXECUTIVE SUMMARY
During an experiment, an aluminum beam was examined to validate the principles of
beam bending. The theory suggests that a beam made of flexible & homogeneous material with
an equivalent modulus of elasticity in tension and compression will deform equally under the
same stress. The moment of inertia (I) was calculated for bending around the horizontal centroid
axis using the provided properties of the beam section. The moment about the maximum load at
the plane section was determined using a shear force and bending moment diagram. Stresses
were computed using the moment of inertia, moment about the plane surface, and distance from
the centroid axis. It was proven that the distributed loads on the top and bottom flanges were
very close to each other, thus confirming the theory.
During the beam experiment, loads were applied which caused sagging. As a result,
throughout the beam, there was a positive bending moment. Gauges on the plane section of the
beam indicated that a plane section within the beam before bending remains plane after bending
throughout a constant moment section of the beam. This proves that the beam bending theory is
accurate. The experiment concluded that the material is linearly elastic, as the relationships
between stress and strain were directly proportional. When a load was applied, the top of the
beam was in compression while the bottom of the beam was in tension. The lowest sagging point
of the beam showed the largest strains, and therefore had the largest stresses.
CEE 370L Mechanics of Materials
Laboratory 1
Fall 2023
1 Introduction
1.1 Background
A transverse load is applied to an aluminum beam in order to test the beam bending
theory. A number of electrical resistance strain gauges are attached at various points on the
beam to measure strain. The purpose of the testing is to confirm the relationship between
moment and bending stresses.
1.2 Reason for Experiment
The purpose of this lab was to test the deflection limits of beams that are installed in
buildings. The experiment provided valuable information to engineers regarding how beams
support and resist loads, which enables them to ensure the safety and stability of structures.
Finding the maximum values of quantities and their locations along the beam is essential for
beam design.
1.3 Theory
When a beam is subjected to loads that are transverse to its length, there is no axial load
applied. However, when a transverse load is applied, a relationship can be found between the
bending moment and the transverse deflection of the beam. The beam is made of a linearly
elastic material, which means it follows Hooke's Law. Therefore, a small deflection should cause
small angles due to the deflection.
The moment-curvature equation ( is determined by the bending moment divided by
the modulus of elasticity times the moment of inertia (also known as the flexural rigidity).
The equation given for the moment-curvature is:
Your preview ends here
Eager to read complete document? Join bartleby learn and gain access to the full version
- Access to all documents
- Unlimited textbook solutions
- 24/7 expert homework help
CEE 370L Mechanics of Materials
Laboratory 1
Fall 2023
where M is the bending moment and EI is the flexural rigidity.
The flexure formula ( is determined by the bending moment multiplied by the distance from
the neutral distance divided by the inertia of the cross section. The equation given for the flexure
formula is:
where M is the bending moment, y is the distance from the neutral axis, and I is the moment of inertia of
the cross section
1.4 Objective
The goal of this laboratory experiment was to confirm the correlation between bending
moments and bending stresses and assess whether the stress distribution aligns with the
principles of beam bending theory.
CEE 370L Mechanics of Materials
Laboratory 1
Fall 2023
2 Approach
2.1 Test Setup and Instrumentation
The experiment was done with a load cell. There were a total of 20 strains on the steel,
five on the back, front, top, and bottom. Each of the strains were 6 inches apart from each other.
The strains are then hooked up to three different boxes. The load cell co impressed the aluminum
beam at 0 kips to 2 kips in 1 increment and back down to 0 kips
CEE 370L Mechanics of Materials
Laboratory 1
Fall 2023
2.2 Test Specimens
Material
Length
(inches)
Length
Between
Load
Points
(inches)
Tube Steel
96.00
48.00
2.3 Test Procedure
• Load applied to specimen: total transverse load - 0, 1, 2, 1, 0 kips
• At each load level, record the microstrain reading from each gage
Your preview ends here
Eager to read complete document? Join bartleby learn and gain access to the full version
- Access to all documents
- Unlimited textbook solutions
- 24/7 expert homework help
CEE 370L Mechanics of Materials
Laboratory 1
Fall 2023
The moment of inertia, span length, and length between load points of the tube steel were
measured and recorded. Then, the measurements were placed in the frame of the
RIEHLE machine. After that, 20 different electrical resistance strains were applied to
the front, back, top, and bottom of the object. The data was collected from the steel
specimen at 0 kips, 20 times for each strain. Later, a force of 1 kip was loaded and 20
measurements were recorded from each side. Finally, the entire process was repeated
three more times for forces of 2 kips, 1 kip, and 0 kips.
3 Results
3.1 Overview
Table 3-1.1: Measured Strains
Load(kips)
Strain(ksi)
T1
T2
T3
T4
T5
0
-0.000003
-0.000002
-0.000002
-0.000002
0
1
0.000088
0.00009
0.00009
0.000083
0.000068
2
0.000182
0.000182
0.000184
0.000168
0.000139
1
0.00009
0.000093
0.000092
0.000084
0.000071
0
-0.000005
-0.000002
-0.000003
-0.000003
0.000002
U1
U2
U3
U4
U5
0
0
0
0
0
-0.000004
1
-0.000089
-0.000088
-0.000089
-0.000074
-0.000068
2
-0.000175
-0.000172
-0.00017
-0.000148
-0.000131
1
-0.000094
-0.00009
-0.000083
-0.000074
-0.000068
0
-0.000005
0
0.000011
0.000003
0
F1
F2
F3
F4
F5
0
-0.000005
-0.000003
-0.000003
-0.000003
0
CEE 370L Mechanics of Materials
Laboratory 1
Fall 2023
1
0.00006
0.000031
0
-0.000032
-0.00006
2
0.000119
0.000059
-0.000003
-0.000064
-0.000121
1
0.000058
0.000028
-0.000005
-0.000036
-0.000065
0
-0.000006
-0.000006
-0.000004
-0.000005
-0.000003
B1
B2
B3
B4
B5
0
-0.000004
-0.000002
0
-0.000005
-0.000001
1
0.000057
0.000029
-0.000003
-0.000036
-0.000062
2
0.000119
0.000061
-0.000001
-0.000065
-0.000119
1
0.000059
0.00003
-0.000003
-0.000038
-0.000065
0
-0.000006
-0.000004
-0.000003
-0.000006
-0.000003
Table 3-1.2: Measured Stress
Load(kips)
Stress(ksi)
T1
T2
T3
T4
T5
0
-0.087
-0.058
-0.058
-0.058
0.000
1
2.552
2.610
2.610
2.407
1.972
2
5.278
5.278
5.336
4.872
4.031
1
2.610
2.697
2.668
2.436
2.059
0
-0.145
-0.058
-0.087
-0.087
0.058
U1
U2
U3
U4
U5
0
0.000
0.000
0.000
0.000
-0.116
1
-2.581
-2.552
-2.581
-2.146
-1.972
2
-5.075
-4.988
-4.930
-4.292
-3.799
1
-2.726
-2.610
-2.407
-2.146
-1.972
0
-0.145
0.000
0.319
0.087
0.000
F1
F2
F3
F4
F5
0
-0.145
-0.087
-0.087
-0.087
0.000
CEE 370L Mechanics of Materials
Laboratory 1
Fall 2023
1
1.740
0.899
0.000
-0.928
-1.740
2
3.451
1.711
-0.087
-1.856
-3.509
1
1.682
0.812
-0.145
-1.044
-1.885
0
-0.174
-0.174
-0.116
-0.145
-0.087
B1
B2
B3
B4
B5
0
-0.116
-0.058
0.000
-0.145
-0.029
1
1.653
0.841
-0.087
-1.044
-1.798
2
3.451
1.769
-0.029
-1.885
-3.451
1
1.711
0.870
-0.087
-1.102
-1.885
0
-0.174
-0.116
-0.087
-0.174
-0.087
Figure 3-1.1 stresses in the top and bottom gages at mid-span for each load level
Figure 3-1.1 Stresses of the Top and Bottom Strain Gages
In Figure 3-1.1, the graph depicts the relationship between the load at each level and the
stresses on the top and bottom. The blue line in the graph represents the top stress data, while the
Your preview ends here
Eager to read complete document? Join bartleby learn and gain access to the full version
- Access to all documents
- Unlimited textbook solutions
- 24/7 expert homework help
CEE 370L Mechanics of Materials
Laboratory 1
Fall 2023
red line represents the bottom stress data. It's important to note that the graph only pertains to the
mid-span portion, specifically T1 and U1.
Figure 3-1.2: Average Stresses of the Front and Back Strains
Figure 3-1.2 shows the relationship of the distance from the neutral axis to the average
stresses of the front and back strains. The graph only shows the data collected from the 2 kips
load. The graph also shows the stresses from T1 and U1.
CEE 370L Mechanics of Materials
Laboratory 1
Fall 2023
Figure 3-1.3: Top and Bottom Stresses from Mid-Span to Support
In Figure 3-1.3, we can see how the top and bottom stresses vary in relation to the distance
from mid-span to the support. The blue line represents the data collected for the top stress while
the red line represents the data collected for the bottom stress.
4 Analysis
4.1 Tube Steel Specimen Analysis
Based on the data collected during the experiment, it was found that the force with the highest
load (2 kips) resulted in the most strain. The strain gages located at the top of the specimen
showed the largest strain, while those at the bottom showed the smallest. Moreover, the front and
back strain gages displayed a deviation of the data going from positive to negative.
CEE 370L Mechanics of Materials
Laboratory 1
Fall 2023
In Figure 3-1.1, there are two linear lines in blue and red colors. The blue line represents the top
stresses and moves towards the positive direction, while the red line represents the bottom
stresses and moves towards the negative direction. The theoretical stress would show two linear
lines originating from the origin and extending towards the positive or negative direction. Upon
comparing the measured stress with the theoretical stress, we observe that both the top and
bottom measured stresses align with the theoretical stress. However, upon closer inspection of
the red line, we can see a gap indicating that the data collected from the bottom strain was larger
when reverting to 2 kips to 1 kip than the first time we recorded the bottom data.
The graph in Figure 3-1.2 represents the average stress of the front and back, which is shown by
a semi-straight line. The theoretical stress should be a straight line through the origin. Comparing
these two stresses, the measured stress shows a slight curve at the end, but the data was still able
to create a line.
In Figure 3-1.3, there are two lines going towards zero. The blue line indicates the top stresses
collected from the mid-span to the support, while the red line indicates the bottom stresses. The
theoretical stress will show a linear line in the first half and then begin to travel to zero.
Comparing the stresses, both the measured stresses align with the theoretical stress.
Based on what we learned in class, a plane will be perpendicular to the neutral axis of the
theoretical lines if they are correct. Based on the graphs shown, all theoretical lines almost or
perfectly line up with the measured lines. The stress distribution agrees with the beam bending
theory because the theory states that cross-sections of the beam must remain plane during
Your preview ends here
Eager to read complete document? Join bartleby learn and gain access to the full version
- Access to all documents
- Unlimited textbook solutions
- 24/7 expert homework help
CEE 370L Mechanics of Materials
Laboratory 1
Fall 2023
bending. The tube steel remained symmetric to the longitudinal axis during the experiment, and
there were not any significant errors in the results of the experiment.
5 Conclusions/Recommendations
Based on the data collected, the following conclusions can be made:
- The top strains had the highest number of strains, while the bottom strains showed the
smallest number of strains.
- Both strains data were observed when the load was at 2 kips.
- The front and back strain gauges showed both positive and negative data.
- All the graphs almost or perfectly aligned with the theoretical stress.
- As the steel beam remained unchanged after the experiment and the stresses aligned
with the theoretical, the stress distribution corroborates the beam bending theorem.
- No significant errors were discovered during the experiment.
- Plane sections remained plane in constant moment portions of the beam
From the experiment, recommendations for the lab would be to use a more accurate
loader and to use a beam that has not been in many previous experiments. This could lower the
margin of error in the lab.
CEE 370L Mechanics of Materials
Laboratory 1
Fall 2023
Related Documents
Related Questions
Which of these statements are correct?
arrow_forward
Q1 please
arrow_forward
O True
O False
QUESTION 3
Compute the expected properties of modulus of elasticity (Ec) of a composite made from S-glass fibers and a Polyester matrix. The volume fraction of fibers is
30%. (Unit is psi.)
Properties of Sample Matrix and Filler Materials
Tensile strength
Tఅబండి
Specific weight
bai
MPa
10 psi
GPa
Iblin
Matrix materials:
Polyester
Ероху
Aluminum
10
18
45
69
124
310
1170
0.40
0.56
10.0
165
2.76
3.86
69
114
0.047
12.7
0.047
12.7
0.100
0.160
27.1
Titanium
Filler materials:
170
43.4
S-glass
Carbon-PAN
Carbon-PAN (high-strength)
Carbon (high-modulus)
Aramid
600
470
4140
3240
5650
2200
3450
12.5
33.5
40
100
86.2
231
276
690
131
0.09
0.064
24.4
17.4
17.7
820
325
500
0రవ
0.078
0.052
21.2
19.0
14.1
Click Save and Submit to save and submit. Click Save All Answers to save all answers.
earch
arrow_forward
Study Area
Document Sharing
User Settings
Access Pearson
mylabmastering.pearson.com
P Pearson MyLab and Mastering
The crash cushion for a highway barrier consists of a
nest of barrels filled with an impact-absorbing material.
The barrier stopping force is measured versus the vehicle
penetration into the barrier. (Figure 1)
Part A
P Course Home
b My Questions | bartleby
Review
Determine the distance a car having a weight of 4000 lb will penetrate the barrier if it is originally traveling at 55 ft/s when it
strikes the first barrel.
Express your answer to three significant figures and include the appropriate units.
Figure
1 of 1
36
μΑ
S =
Value
Units
Submit
Request Answer
Provide Feedback
?
Next >
arrow_forward
PHYS X PHYS X
印 PHYS X
PHYS X
POTPHYS X
PHYS X
E PHYS X E PHYS
top/semester2/physics%20for%20engineers/PHYS220_CH15_Lecture%20Notes_Problems%2015 19,15.29 S
(D Page view
A Read aloud
V Draw
Problem-15-19: page-475
A 0.500-kg object attached to a spring with a force constant of 8.00 N/m vibrates in simple harmonic motion
with an amplitude of 10.0 cm. Calculate the maximum value of its
(a) speed, and acceleration.
(b) the speed and the acceleration when the object is 6.00 em from the equilibrium position, and
(c) the time interval required for the object to move from.r50 to r5 8.O0 cm.
Solution:
arrow_forward
Hello Good Evening Sir,I have a question in my homework related structural mechanics lesson. The following below is my question. Please advice. Thank you so much
Regards,
Yusuf
arrow_forward
Problem 1: (50 points)
In Avengers 2, Captain America's improved
shield is made from unobtainium, a new
material that will soon be available in a store
near you. Unobtainium has the normal stress-
strain diagram shown. The proportional limit,
the elastic limit and the yield point are
identical in this material.
o [MPa]
2001
175
150
125
100
Fig.1 Normal stress-strain
75
50
25
0
0. 0.05 0.1 0.15 0.2 0.25
Unobtainium has a Poisson's ratio of 0.3.
a. [6pts] Identify the yield point oy, the ultimate stress ou and the fracture
stress of. Include units.
c. [25pts] A bar of unobtainium has a length of
1.5 m, a width of 100mm and a height of 50
mm, as shown. The cross-sectional area is
50mm 100mm = 5 x 10-³m². The bar is
subjected to an axial force of 375 kN.
Find the normal stress in a cross-section of the bar.
b. [5pts] How do you find Young's modulus from this graph? Find its value with units.
whesta fins dus al hoss
P = 375 KN
1.5 m
0.3
50 mm
100 mm
& [mm/mm]
Is the material within its…
arrow_forward
HEAT TRANSFER
CASE: I want to know what temperature in (°F) the cylinder will have inside. It's a heat transfer problem.
what is T2 ?
HEAT TRANSFER
They gave me an answer all squashed together that i can't make sense of it. If you could help me makes sense of it thank you!
arrow_forward
I Review
Learning Goal:
Part A- Vertical impact
To calculate displacement and stresses due to vertical and horizontal impact loads.
A 10-kg block is dropped from 1.5 m onto the center of a simply supported beam with a length 3 m. The beam has a square section with side length 6.5 cm. The material has E = 200 GPa . What is the maximum
deflection?
When an object strikes a structure that responds by deforming in linear elastic fashion, the
object comes to rest when the structure has undergone maximum deflection. At that
moment, the structure's strain energy must equal the sum of the energies before the impact,
including both the object's kinetic energy and its gravitational potential energy.
Express your answer with appropriate units to three significant figures.
> View Available Hint(s)
When an object falls from rest onto a structure, the object's gravitational potential energy is
converted into strain energy in the structure. The total strain energy in the structure at the
point of…
arrow_forward
Please show work
arrow_forward
Constants | Periodic Table
Part A
A 71 kg man's arm, including the hand, can be modeled
as a 79-cm-long uniform cylinder with a mass of 3.5 kg
In raising both his arms, from hanging down to straight up, by how much does he raise his center of gravity?
Express your answer with the appropriate units.
?
h =
Value
Units
Submit
Request Answer
arrow_forward
HW4 Q9
arrow_forward
Question 16
ABC
Question 16
Jennifer watched as movers used a ramp to load a heavy dresser into a moving truck. The dresser, that had to be lifted 1.5 m from the street to the back of the moving truck, was pushed along a 6.6 m
ramp. What is the mechanical advantage of the ramp?
A
2.98
B
3.06
4.0
D
4.4
©20 Illuminate EducationTM, Inc.
O Time Remaining: 40 minutes
四
O9 0 1:08
hp
SC
DI
@
#
2$
2
3
4
5
7
8.
9.
arrow_forward
Help!!! Please answer it correctly
arrow_forward
Access Pearson
P Pearson MyLab and Mastering
Study Area
Document Sharing
User Settings
The man having a weight of 180 lb is able to run up a
18-ft-high flight of stairs shiwn in (Figure 1) in 4 s.
Figure
1 of 1
R
mylabmastering.pearson.com
Part A
P Course Home
b My Questions | bartleby
Determine the power generated.
Express your answer in horsepower to three significant figures.
ΜΕ ΑΣΦ. Η
vec
P =
Submit
Request Answer
Part B
?
hp
How long would a 100-W light bulb have to burn to expend the same amount of energy?
Express your answer to three significant figures and include the appropriate units.
HÅ
?
t =
Value
Units
Submit
Request Answer
Provide Feedback
Review
Next >
arrow_forward
Academic)
The following tensile data were collected from a standard 12.827 mm diameter test specimen of
copper alloy. The specimen was tested under tensile load until rupture.
After fracture, the sample length is 76.708 mm and the diameter is 9.5 mm.
Load (kN) Sample Length (mm)
50.8
13.4
50.842
26.7
50.897
33.4
50.957
40.0
51.0286
46.7
51.816
53.4
57.404
55.2
63.5
50.7
76.708
Calculate:
1. Ultimate Engineering Tensile strength:
2. Engineering stress at fracture:
3. True stress at fracture:
4. Percent elongation of the tested copper alloy specimen:
5. Percent reduction of area of the tested copper alloy specimen:
arrow_forward
SEE MORE QUESTIONS
Recommended textbooks for you
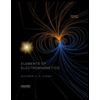
Elements Of Electromagnetics
Mechanical Engineering
ISBN:9780190698614
Author:Sadiku, Matthew N. O.
Publisher:Oxford University Press
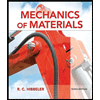
Mechanics of Materials (10th Edition)
Mechanical Engineering
ISBN:9780134319650
Author:Russell C. Hibbeler
Publisher:PEARSON
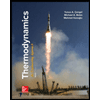
Thermodynamics: An Engineering Approach
Mechanical Engineering
ISBN:9781259822674
Author:Yunus A. Cengel Dr., Michael A. Boles
Publisher:McGraw-Hill Education
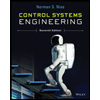
Control Systems Engineering
Mechanical Engineering
ISBN:9781118170519
Author:Norman S. Nise
Publisher:WILEY
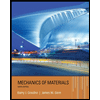
Mechanics of Materials (MindTap Course List)
Mechanical Engineering
ISBN:9781337093347
Author:Barry J. Goodno, James M. Gere
Publisher:Cengage Learning
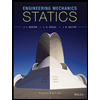
Engineering Mechanics: Statics
Mechanical Engineering
ISBN:9781118807330
Author:James L. Meriam, L. G. Kraige, J. N. Bolton
Publisher:WILEY
Related Questions
- Which of these statements are correct?arrow_forwardQ1 pleasearrow_forwardO True O False QUESTION 3 Compute the expected properties of modulus of elasticity (Ec) of a composite made from S-glass fibers and a Polyester matrix. The volume fraction of fibers is 30%. (Unit is psi.) Properties of Sample Matrix and Filler Materials Tensile strength Tఅబండి Specific weight bai MPa 10 psi GPa Iblin Matrix materials: Polyester Ероху Aluminum 10 18 45 69 124 310 1170 0.40 0.56 10.0 165 2.76 3.86 69 114 0.047 12.7 0.047 12.7 0.100 0.160 27.1 Titanium Filler materials: 170 43.4 S-glass Carbon-PAN Carbon-PAN (high-strength) Carbon (high-modulus) Aramid 600 470 4140 3240 5650 2200 3450 12.5 33.5 40 100 86.2 231 276 690 131 0.09 0.064 24.4 17.4 17.7 820 325 500 0రవ 0.078 0.052 21.2 19.0 14.1 Click Save and Submit to save and submit. Click Save All Answers to save all answers. earcharrow_forward
- Study Area Document Sharing User Settings Access Pearson mylabmastering.pearson.com P Pearson MyLab and Mastering The crash cushion for a highway barrier consists of a nest of barrels filled with an impact-absorbing material. The barrier stopping force is measured versus the vehicle penetration into the barrier. (Figure 1) Part A P Course Home b My Questions | bartleby Review Determine the distance a car having a weight of 4000 lb will penetrate the barrier if it is originally traveling at 55 ft/s when it strikes the first barrel. Express your answer to three significant figures and include the appropriate units. Figure 1 of 1 36 μΑ S = Value Units Submit Request Answer Provide Feedback ? Next >arrow_forwardPHYS X PHYS X 印 PHYS X PHYS X POTPHYS X PHYS X E PHYS X E PHYS top/semester2/physics%20for%20engineers/PHYS220_CH15_Lecture%20Notes_Problems%2015 19,15.29 S (D Page view A Read aloud V Draw Problem-15-19: page-475 A 0.500-kg object attached to a spring with a force constant of 8.00 N/m vibrates in simple harmonic motion with an amplitude of 10.0 cm. Calculate the maximum value of its (a) speed, and acceleration. (b) the speed and the acceleration when the object is 6.00 em from the equilibrium position, and (c) the time interval required for the object to move from.r50 to r5 8.O0 cm. Solution:arrow_forwardHello Good Evening Sir,I have a question in my homework related structural mechanics lesson. The following below is my question. Please advice. Thank you so much Regards, Yusufarrow_forward
- Problem 1: (50 points) In Avengers 2, Captain America's improved shield is made from unobtainium, a new material that will soon be available in a store near you. Unobtainium has the normal stress- strain diagram shown. The proportional limit, the elastic limit and the yield point are identical in this material. o [MPa] 2001 175 150 125 100 Fig.1 Normal stress-strain 75 50 25 0 0. 0.05 0.1 0.15 0.2 0.25 Unobtainium has a Poisson's ratio of 0.3. a. [6pts] Identify the yield point oy, the ultimate stress ou and the fracture stress of. Include units. c. [25pts] A bar of unobtainium has a length of 1.5 m, a width of 100mm and a height of 50 mm, as shown. The cross-sectional area is 50mm 100mm = 5 x 10-³m². The bar is subjected to an axial force of 375 kN. Find the normal stress in a cross-section of the bar. b. [5pts] How do you find Young's modulus from this graph? Find its value with units. whesta fins dus al hoss P = 375 KN 1.5 m 0.3 50 mm 100 mm & [mm/mm] Is the material within its…arrow_forwardHEAT TRANSFER CASE: I want to know what temperature in (°F) the cylinder will have inside. It's a heat transfer problem. what is T2 ? HEAT TRANSFER They gave me an answer all squashed together that i can't make sense of it. If you could help me makes sense of it thank you!arrow_forwardI Review Learning Goal: Part A- Vertical impact To calculate displacement and stresses due to vertical and horizontal impact loads. A 10-kg block is dropped from 1.5 m onto the center of a simply supported beam with a length 3 m. The beam has a square section with side length 6.5 cm. The material has E = 200 GPa . What is the maximum deflection? When an object strikes a structure that responds by deforming in linear elastic fashion, the object comes to rest when the structure has undergone maximum deflection. At that moment, the structure's strain energy must equal the sum of the energies before the impact, including both the object's kinetic energy and its gravitational potential energy. Express your answer with appropriate units to three significant figures. > View Available Hint(s) When an object falls from rest onto a structure, the object's gravitational potential energy is converted into strain energy in the structure. The total strain energy in the structure at the point of…arrow_forward
- Please show workarrow_forwardConstants | Periodic Table Part A A 71 kg man's arm, including the hand, can be modeled as a 79-cm-long uniform cylinder with a mass of 3.5 kg In raising both his arms, from hanging down to straight up, by how much does he raise his center of gravity? Express your answer with the appropriate units. ? h = Value Units Submit Request Answerarrow_forwardHW4 Q9arrow_forward
arrow_back_ios
SEE MORE QUESTIONS
arrow_forward_ios
Recommended textbooks for you
- Elements Of ElectromagneticsMechanical EngineeringISBN:9780190698614Author:Sadiku, Matthew N. O.Publisher:Oxford University PressMechanics of Materials (10th Edition)Mechanical EngineeringISBN:9780134319650Author:Russell C. HibbelerPublisher:PEARSONThermodynamics: An Engineering ApproachMechanical EngineeringISBN:9781259822674Author:Yunus A. Cengel Dr., Michael A. BolesPublisher:McGraw-Hill Education
- Control Systems EngineeringMechanical EngineeringISBN:9781118170519Author:Norman S. NisePublisher:WILEYMechanics of Materials (MindTap Course List)Mechanical EngineeringISBN:9781337093347Author:Barry J. Goodno, James M. GerePublisher:Cengage LearningEngineering Mechanics: StaticsMechanical EngineeringISBN:9781118807330Author:James L. Meriam, L. G. Kraige, J. N. BoltonPublisher:WILEY
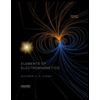
Elements Of Electromagnetics
Mechanical Engineering
ISBN:9780190698614
Author:Sadiku, Matthew N. O.
Publisher:Oxford University Press
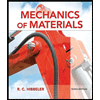
Mechanics of Materials (10th Edition)
Mechanical Engineering
ISBN:9780134319650
Author:Russell C. Hibbeler
Publisher:PEARSON
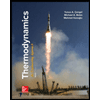
Thermodynamics: An Engineering Approach
Mechanical Engineering
ISBN:9781259822674
Author:Yunus A. Cengel Dr., Michael A. Boles
Publisher:McGraw-Hill Education
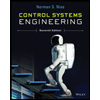
Control Systems Engineering
Mechanical Engineering
ISBN:9781118170519
Author:Norman S. Nise
Publisher:WILEY
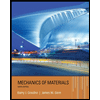
Mechanics of Materials (MindTap Course List)
Mechanical Engineering
ISBN:9781337093347
Author:Barry J. Goodno, James M. Gere
Publisher:Cengage Learning
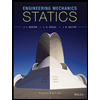
Engineering Mechanics: Statics
Mechanical Engineering
ISBN:9781118807330
Author:James L. Meriam, L. G. Kraige, J. N. Bolton
Publisher:WILEY