Disc9T4050
docx
keyboard_arrow_up
School
Memorial University of Newfoundland *
*We aren’t endorsed by this school
Course
7900
Subject
Management
Date
Apr 3, 2024
Type
docx
Pages
4
Uploaded by Spriddle2587
Q1: What will you tell the president?
The president of Cignet Plastics Corporation should first be informed that variation is most likely to blame for the rise in flaws in the precision die castings for the model airplane kits.
I would begin by defining the term "process variation." Processes in manufacturing aren't always exactly the same. Process variation can be classified as either special cause (also known as assignable) variation or common cause (also known as random).
Certain identified factors that are not a part of the regular process create special cause variation. These variables might include equipment failures, mistakes made by operators, modifications to the raw materials, or other unforeseen circumstances. Special cause variation is an indication that something is wrong with the process and has to be fixed. Whereas common
cause variation results from small variations and uncertainties in the production process, which are inherent to all processes. It is an inherent component of all production processes and stands for the typical daily fluctuation that happens even in steady processes. Common cause variation is typically anticipated and does not point to a process-related issue.
After that, I would tell the president that the Quality Assurance team thoroughly audited the procedure and found no modifications to the procedure itself. This indicates that common cause variation linked to typical process fluctuations is not the reason of the increase in faults. I would then discuss the Assignment of Causes, where Quality Assurance feels that special cause variation is the explanation for the recent increase in defects. This suggests that there are particular, distinguishable causes for the faults that have happened.
My next goal would be to deal with the problem in an efficient manner. Finding and addressing the precise sources of the defects is crucial. This could entail a root cause analysis, in
which a multidisciplinary team looks into recent modifications, equipment failures, human error, and any other elements that might have led to the faults.
Subsequently, I would stress the significance of embracing an attitude of ongoing development. Special cause variation draws attention to areas where specific process enhancements might be made to stop similar problems from happening in the future. Lastly, in order to identify and correct any particular cause deviations as soon as they arise, it is imperative to establish strong quality control procedures. This could entail increasing the frequency of inspections or improving the tracking of important process variables.
Q2: How to dissuade the president from changing the process?
The president may naturally want to alter the process right away in order to cut down on errors, but it's important to advise him against taking this route because altering an established system without first figuring out what the underlying reasons of the errors are can frequently result in additional problems. To get the president to reconsider, I would first point out the dangers of making changes to the procedure without fully comprehending the situation. Any modification to the process has the potential to add more unknowns and variables, which could make the issue worse or have unforeseen effects. I would assist him in realizing that altering the procedure without determining the precise reasons behind the flaws may result in treating the incorrect problems or implementing adjustments that have no positive impact on the quality. Time, money, and possibly even more flaws could be lost as a result of this.
Next, I would emphasize how crucial a data-driven strategy is. To determine the precise causes of the defects, it is essential to depend on evidence and data rather than making modifications based on gut feeling or conjecture. To do this, current production statistics and any other pertinent information must be thoroughly analyzed.
The maintenance of stability is the following topic I'd address stable processes are generally preferred because they enable consistency in quality and predictability. A production process that is already unstable may become even more unstable if needless adjustments are made.
After that, I would advise carrying out a thorough root cause analysis to pinpoint the precise causes of the current rise in problems. This study will assist in identifying the underlying problems that require attention. Additionally, I would stress that a culture of continuous improvement is supported when a root cause analysis is used to address the problem and targeted remedies are implemented. This presents an opportunity to further strengthen and fortify the process against future modifications.
To make sure the right course of action is followed, I would then advise consulting with specialists in statistical process control, quality management, and root cause analysis. These professionals can direct the inquiry and aid in the creation of workable solutions. Last but not least, it's critical to continuously monitor the process and confirm that the flaws have indeed decreased after putting the adjustments based on the root cause analysis into practice. This continuous observation guarantees the stability of the process and the efficacy of the modifications.
Q3: Approach to Getting Operations Back to Normal
The following strategy is what I would advise doing to restore normalcy to Cignet Plastics Corporation's operations and lower the failure rate:
1.
Root Cause Analysis: To pinpoint the precise reasons behind the recent rise in faults, carry out an exhaustive root cause analysis. Examining production records, examining equipment, and speaking with operators are some of the possible steps in this investigation (Rajendran, 2023). 2.
Address Particular Issues: After determining the underlying reasons, rank them in order of importance and deal with them methodically. This could entail changing process settings to guarantee constant quality, fixing or modernizing equipment, or giving operators further training (Rajendran, 2023).
3.
Data Collection and Analysis: Compile and examine information about the manufacturing process, taking into account any recent modifications to machinery, supplies, or methods of operation. Patterns and possible underlying causes can be found with the use of statistical methods like Pareto analysis, control charts, and cause-and-effect diagrams (Fishbone diagrams). 4.
Quality Control procedures: To identify and stop such problems in the future,
improve quality control procedures. This could entail employing sophisticated inspection technologies, conducting inspections more frequently, or incorporating real-time monitoring of crucial process variables.
5.
Execute remedial measures: Using the information from the root cause analysis, create and carry out remedial measures. The precise variables that contributed to the flaws should be eliminated or mitigated by these steps. Record the modifications made to the procedure (Rajendran, 2023). 6.
Employee Training and Involvement: Make training investments and include staff members in the process of change. Make sure operators are aware of how crucial their contributions are to preserving the quality of the product, and provide them chances to offer advice and ideas.
7.
Documentation and Reporting: Ensure that all actions, including process modifications, training materials, and quality control data, are meticulously documented. Report developments on a regular basis to stakeholders and senior management. 8.
Feedback Loop: Create a loop in which staff members are encouraged to report any inconsistencies, problems, or possible upgrades. By taking a proactive stance, issues can be found and resolved before they become more
serious.
References
Rajendran, G. (2023, July 20). The Power of Root Cause Analysis: Solving Problems at Their Core.
Retrieved from Linkedin: https://www.linkedin.com/pulse/power-root-cause-analysis-
solving-problems-core-gopinath-rajendran/
Your preview ends here
Eager to read complete document? Join bartleby learn and gain access to the full version
- Access to all documents
- Unlimited textbook solutions
- 24/7 expert homework help
Related Documents
Recommended textbooks for you
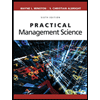
Practical Management Science
Operations Management
ISBN:9781337406659
Author:WINSTON, Wayne L.
Publisher:Cengage,
Recommended textbooks for you
- Practical Management ScienceOperations ManagementISBN:9781337406659Author:WINSTON, Wayne L.Publisher:Cengage,
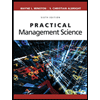
Practical Management Science
Operations Management
ISBN:9781337406659
Author:WINSTON, Wayne L.
Publisher:Cengage,