_Case Study Part A - Group 9_
docx
keyboard_arrow_up
School
Fanshawe College *
*We aren’t endorsed by this school
Course
3069
Subject
Management
Date
Apr 3, 2024
Type
docx
Pages
11
Uploaded by AmbassadorHippopotamusMaster1117
1
MGMT 3069- Operations Management
Part A: Case Study Report
Case Title: Mike & Bike
Submitted by Group No: 9
Hana Kim: Process Flow Indra Prasad Chapagain: Executive Summary & Table of contents
Kien Thanh Ly: Bottleneck, Responsibility Matrix, References, Conclusion & Final Check
Mary Keshinro: Synopsis & Challenges Faced Submitted to: Dennis M. Jewlal
Date: February 9, 2024
2
Table of contents Executive summary………………………………………………………………………… 3 Synopsis…………………………………………………………………………………….. 4 Challenges faced by mike and tom………………………………………………………….. 5 Workflow backlogs…………………………………………………………………… 5.1 Inventory Management……………………………………………………………… 5.2 Effective capacity Uncertainty………………………………………………………. 5.3 Operational map lacking……………………………………………………………. 5.4 Inventory cost Issues………………………………………………………………… 5.5 Process Flow Diagram of Operation………………………………………………………….. 6 Process Flow Explanation………………………………………………………………………7
Identification of bottleneck within the system……………………………………………….. 8 Conclusion……………………………………………………………………………….…..9 References…………………………………………………………………………………… 9 Responsibility matrix………………………………………………………………………… 10
3
1-
Executive Summary:
Mike & Bike is a renowned bicycle workshop in Toronto that specialize in manufacturing bicycles for online shops and large retailers such as Walmart and Canadian Tire. Mike Tylor runs a company which provides significant repairs on racing bikes and has established an excellent track record for quality. A good deal of their time involves creating three different types of bicycles: men's, ladies', and children's. Mike was concerned about order backlogs, regular component shortages, and the need for an overview of the shop's activities. During a visit to the workplace, it came out that assembly tasks include three major processes: frame/wheel, top mounting, and adjustment. The Repair Department disassembles modules, assesses repairability, and completes repairs with or without part replacements. Before motorbikes are released to customers, they go through quality inspections. Assembly tasks are roughly split into two categories: assembly and repair, with ladies' and children's assembly accounting for 30% each. Mike wants to know the effective capacity per worker hour for assembly orders. Tom, the foreman, struggles with inventory, obtaining the correct number and time for things such as spacers required for repairing freewheels. Tom highlighted the difficulties of handling part orders, particularly for oil-treated spacers, and requested support in identifying the proper quantity and timing for orders. The store currently orders components every three weeks, costing a $60 shipping price, and keeps them in an annual $10 oil container. The research study will address these concerns through providing insights into operational efficiency, effective capacity, and inventory.
Your preview ends here
Eager to read complete document? Join bartleby learn and gain access to the full version
- Access to all documents
- Unlimited textbook solutions
- 24/7 expert homework help
4
2-
Synopsis:
Mike & Bike is a well-established bicycle workshop in Toronto owned and managed by Mike Tylor. Originally a small bike repair store, it has grown substantially and now assembles bikes for customers of online suppliers as well as major retailers like Walmart and Canadian Tire. With a character for celestial craftsmanship, the shop also caters to professional bikers by providing major repairs and enhancements to racing bikes.
The shop's principal activity is assembling new bikes, which make up about 70% of its business. The assembly line includes the following stages: Frame/Wheel, Top Mount, and Adjustment. Men's, Women's, and Children's bikes take different times at the Top Mount station, but all jobs eventually go through an Adjustment station that takes an average of 5 minutes.
In addition to assembly, about 30% of the shop's operations include repairs. Repair jobs involve a detailed dismantling process, an examination for repairability, the actual repair (with or without part replacement), and reinstallation. Each repaired job goes through a final quality check.
Mike values quality and timely delivery but he is concerned about occasional backlogs and parts shortages, especially for repairs, having a negative impact on their capacity to finish jobs on time. He aims to maintain a job completion rate within 5% of the target. Therefore mike hired my team to consult
him on the matter, he considered a process map to be made to find out where his problem is and how to solve it.
Tom Moberlaw, the foreman, shared with us how he is facing issues with inventory management, particularly for parts like spacers used in freewheel repairs. Parts ordering and inventory levels are inconsistent which hinders smooth workflow.
5
3-
Challenges faced by Mike and Tom Below are the main challenges faced by mike & bike:
1. Workflow Backlogs: The workshop sometimes takes in more work than it can complete in a timely manner, causing concerns for Mike about keeping up with the demand and maintaining the shop's reputation for fast and quality service.
2. Inventory Management: Tom struggles with managing the inventory, often running out of necessary parts like spacers for repair jobs. The current ordering system sees delays and irregularities that do not align with the fluctuating demand, leading to hold-ups in job completion.
3. Effective Capacity Uncertainty: Mike and his team do not have a clear understanding of the shop's effective capacity per labor hour for assembly and repair jobs. This makes it difficult to forecast their ability to manage incoming orders and workload.
4. Operational Map Lacking: Mike believes that an operational map might reveal bottlenecks and inefficiencies in the shop's processes, which could then be addressed to improve the overall workflow.
5. Inventory Cost Issues: There is an uncertainty about whether Tom is ordering the right amount of parts at the right time to optimize the inventory while minimizing costs, including regular expenses on parts, oil containers, and shipping charges.
By tackling these challenges, Mike & Bike have the opportunity to smoothly run their operations, ensure timely deliveries, maintain high-quality standards, and optimize their inventory management, also customer satisfaction .
6
4-
Process Flow Diagram of Operation
Inspection: The crates will be inspected by our receivers to make sure they are all good.
Your preview ends here
Eager to read complete document? Join bartleby learn and gain access to the full version
- Access to all documents
- Unlimited textbook solutions
- 24/7 expert homework help
7
Process Flow Explanation:
The flow processes for the assembly of bikes as follows:
●
Frame/Wheel Process
1.
Mount pedals and cranks on the frame.
2.
Add cassettes and freewheels to the back wheel.
3.
Mount the back wheel on the frame.
4.
Install the front wheel on the frame.
●
Top Mount Process
1.
Install the handle and seat.
2.
Route and connect brake and gear shift cables.
3.
Connect brake pad modules to the front and back wheel rims.
●
Adjustment Station
1.
Install the chain with the correct tightness.
2.
Adjust the gap between the brake pads and the wheel rims for ease of application and grip.
●
Final check
The flow processes for the repair of bikes as follows:
●
Dismantling and Disassembly: Dismantle and disassemble the module in need of repair.
●
Examination of Repairability: Examine the module to determine if it can be repaired without replacing parts or if replacement parts are needed.
●
Module Repair: Perform repairs according to the determined method (with or without replaced parts).
●
Reinstallation: Reinstall the repaired module.
8
●
Final Check: Perform a final quality check on the repaired jobs. Ensure brakes are working properly, seats are steady, gears shift easily, tire shafts are centered, and all joints are torqued to specification.
5-
Identification of Bottleneck within the system
The bottleneck throughout the process of bike assembly occurs during the Top Mounting stage for Men, Women and Children bikes. This stage will require extra time based on the type of the bike, specifically 10 minutes for Men’s bike ; 8 minutes for Women’s bike and 6 minutes for Children’s bike. The structure of these bikes could be the reason that causes this bottleneck, as a Children’s bike tends to be simpler, smaller, which makes it easier for the technician to inspect and adjust. A man’s bike is much larger, and depending on the working area, the technician may need more time to move around this bike to do their job.
Another bottleneck will occur during the repairing process due to the variability of the bike’s status, which means it will be assessed further to determine whether it’s necessary to repair with replacing parts or to repair without them. It will take approximately 5 minutes to repair without replacing parts, whereas this time will be doubled if the repair includes a replacement part. Furthermore, before deciding to repair the bike with parts or not, the technician will need to ask the client for permission in order to alert them of the potential extra charges. Also, finding the appropriate replacing part may cause
extra time to repair, sometimes the parts will match other current parts in terms of structure, but their color doesn't. Sometimes the necessary parts are not available in the inventory and the technician will need to order them. It is always uncertain how long it will take the parts to arrive and this will make them postpone the repair jobs.
9
6-
Conclusion.
In conclusion, from what has been provided from the case study, Mike seems to be mildly satisfied with the overall operation of his business. However, Mike is expecting to meet the demand for jobs as his business tend to receive more jobs than they can finish them at the regular pace. To combat this issue, it
is recommended for Mike to take a look at our Process Flow of Operation and focuses on the Bottleneck to further analyze what is needed to enhance the efficiency during these stages. Since Men’s bike take up more percentage of job orders compared to Women and Children bike, Mike may reduce the production of Women and Children bike and prioritize Men’s bike. For Tom’s issue, he may need to consider the Economic Order Quantity (EOC) to avoid uncertainty in demand, eliminate transportation costs and lead time for oil delivery. Specifically, Tom will place the oil order at 100% inventory capacity, when the oil inventory has been used by 50%, he will place another 100% worth of inventory capacity for oil. As soon as the 1
st
order of oil has been used 100%, the second order will arrive and ready for use without wait time. Tom may consider another carrier for the oil order too. With the above recommendations, it will be easy for Mike and Tom to implement and see the results in a couple of weeks. 7-
References
Ritzman. P & Krajewski. L, Malhotra. M & Klassen. R. (n.d). Foundations of Operation Management.
Pearson Education, Inc. https://bibliu.com/app/#/view/books/1001202250728/pdf2htmlex/index.html#page_iv
Your preview ends here
Eager to read complete document? Join bartleby learn and gain access to the full version
- Access to all documents
- Unlimited textbook solutions
- 24/7 expert homework help
10
8-
Responsibility Matrix
Group #9
Responsibility Matrix
Part A Case Study Report: Mike & Bike
Tasks
Date Completed
Kien Thanh Ly
Hana Kim
Indra Prasad Chapagain
Mary Keshinro
Performance
Cover Page
FEB 2
nd
2024
R
E
Table of contents
FEB 7
th
2024
S
R
G
Executive Summary
FEB 7
th
2024
R
E
Synopsis
FEB 6
th
2024
R
E
Challenges faced
by Mike and Tom
FEB 6
th
2024
R E
Process flow diagram
of operations
FEB 6
th
2024
R
E
Identification of Bottleneck in the system
FEB 9
TH
2024
R
G
Conclusion
FEB 6
th
2024
R
G
References
FEB 6
th
2024
R
E
11
Responsibility Matrix
FEB 6
th
2024
R
E
Related Documents
Recommended textbooks for you
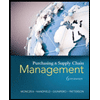
Purchasing and Supply Chain Management
Operations Management
ISBN:9781285869681
Author:Robert M. Monczka, Robert B. Handfield, Larry C. Giunipero, James L. Patterson
Publisher:Cengage Learning
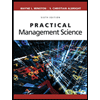
Practical Management Science
Operations Management
ISBN:9781337406659
Author:WINSTON, Wayne L.
Publisher:Cengage,
Marketing
Marketing
ISBN:9780357033791
Author:Pride, William M
Publisher:South Western Educational Publishing
Recommended textbooks for you
- Purchasing and Supply Chain ManagementOperations ManagementISBN:9781285869681Author:Robert M. Monczka, Robert B. Handfield, Larry C. Giunipero, James L. PattersonPublisher:Cengage LearningPractical Management ScienceOperations ManagementISBN:9781337406659Author:WINSTON, Wayne L.Publisher:Cengage,MarketingMarketingISBN:9780357033791Author:Pride, William MPublisher:South Western Educational Publishing
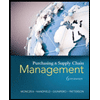
Purchasing and Supply Chain Management
Operations Management
ISBN:9781285869681
Author:Robert M. Monczka, Robert B. Handfield, Larry C. Giunipero, James L. Patterson
Publisher:Cengage Learning
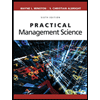
Practical Management Science
Operations Management
ISBN:9781337406659
Author:WINSTON, Wayne L.
Publisher:Cengage,
Marketing
Marketing
ISBN:9780357033791
Author:Pride, William M
Publisher:South Western Educational Publishing