COMPETENCY BASED ASSESSMENT NIssan
docx
keyboard_arrow_up
School
Egerton University *
*We aren’t endorsed by this school
Course
18
Subject
Management
Date
Nov 24, 2024
Type
docx
Pages
23
Uploaded by uvyudennis
1
COMPETENCY BASED ASSESSMENT: PRODUCTION DESIGN IN NISSAN
COMPANY
Student Name:
Student Code:
Institution of Affiliation:
Date:
2
Table of Contents
CHAPTER 1: INTRODUCTION
....................................................................................................
3
1.1 Background of Nissan
............................................................................................................
3
1.2 Supply Chain
.........................................................................................................................
3
1.3 Types of Production Methods
................................................................................................
3
1.4 Selected Product
....................................................................................................................
4
CHAPTER 2; CASH2CASH CYCLE
.............................................................................................
4
CHAPTER 3: SALES & OPERATIONS PLAN
.............................................................................
6
CHAPTER 4: MASTER PRODUCTION SCHEDULING
............................................................
8
CHAPTER 5: MRP
........................................................................................................................
10
5.1 MRP Material Plan for Nissan Altima
.................................................................................
10
5.2 Product Structure for Nissan Altima
....................................................................................
11
5.3 Time-phased product structure back scheduling
..................................................................
12
5.4 Materials required sheet
.......................................................................................................
12
5.5 Materials requirement planning sheet
..................................................................................
12
CHAPTER 6: CAPACITY PLANNING
.......................................................................................
13
CHAPTER 7: PAC
.........................................................................................................................
17
CHAPTER 8: MANAGEMENT OF SUPPLYS, OPERATIONS & STRATEGY
.......................
17
REFERENCES
..............................................................................................................................
20
3
CHAPTER 1: INTRODUCTION
1.1 Background of Nissan Nissan is a well-known brand in the international automotive sector that is renowned for its dedication to quality, innovation, and driving excellence. Nissan was established in 1933 and has
since developed into one of the top automakers in the world, continuously pushing the limits of design and technology. Nissan has a long history and a strong global presence. It is known for building cars that are not just dependable and efficient but also iconic in and of themselves. Nissan has produced a broad variety of automobiles during the course of its existence, including cutting-edge electric cars, tough and adventurous SUVs, and elegant and useful sedans (
Gil et al. 2023)
. The company has become well-known in the automobile market thanks to its dedication to satisfying the various needs of consumers throughout the globe. Nissan's commitment to sustainability is demonstrated by the range of electric vehicles it offers and its ongoing attempts to lessen its environmental impact (Gill, et al. 2023). Nissan has a goal that goes beyond just making cars; it also includes a dedication to promoting social change. The company's goal is to make cars that are safer and more efficient via research and development, protecting the environment and drivers alike. Nissan also actively participates in CSR programs with the goal of enhancing communities and improving the global environment.
1.2 Supply Chain Nissan operates within a complex and global supply chain network. The company sources various components and materials from suppliers worldwide to support its manufacturing processes (Jeong & Chung, 2023). These components are crucial for the assembly of Nissan vehicles, and the company relies on a well-structured supply chain to ensure the timely delivery of these parts. Nissan's supply chain includes a diverse network of suppliers, logistics partners, and distribution channels to facilitate efficient production and delivery.
1.3 Types of Production Methods
Nissan employs a diverse range of production methods to manufacture its vehicles, depending on
the specific model and production facility (Jeong & Chung, 2023). The company uses various production methods, including Flow Production, Repetitive Production, and Just-In-Time (JIT) Production. The selection of the production method depends on factors such as the type of vehicle being produced, market demand, and the production facility's capabilities.
Your preview ends here
Eager to read complete document? Join bartleby learn and gain access to the full version
- Access to all documents
- Unlimited textbook solutions
- 24/7 expert homework help
4
Flow Production:
Nissan utilizes flow production for high-demand models where a continuous production process is essential to meet market demands efficiently. This method is characterized by a continuous assembly line where vehicles move through various stations in a sequential manner.
Repetitive Production:
In cases where the company produces a consistent volume of vehicles with minor variations, repetitive production is employed. This method is suitable for models that do not require frequent retooling of production lines (Samaraweera, et al. 2023).
Just-In-Time (JIT) Production:
Nissan is well-known for implementing JIT production techniques, which involve manufacturing components and vehicles just in time to meet customer demand. This method minimizes inventory costs and allows for greater flexibility in production.
1.4 Selected Product
For the purpose of our Production Design project, we have chosen to focus on Nissan's mid-sized
sedan, the Nissan Altima. The Nissan Altima is a popular model known for its blend of style, performance, and advanced technology. By selecting the Nissan Altima as our product, we aim to
explore the production processes and supply chain management specific to this vehicle, providing valuable insights into the manufacturing practices at Nissan.
CHAPTER 2; CASH2CASH CYCLE To calculate the Cash-to-Cash (C2C) cycle for the selected product, the following data is provided:
Component
Number of Days
Days Sales Outstanding (DSO)
45
Days Inventory Outstanding (DIO)
30
Days Payable Outstanding (DPO)
20
5
To calculate the C2C cycle for Nissan:
Calculate the Average Daily Sales (Sd): Sd = Gross Sales / Number of Days Sd = $1,700,000 / 30 days
Sd = $56,666 per day
Calculate the Accounts Receivable Days (ARd): ARd = Accounts Receivable / Sd ARd = $400,000 / $56,666 per day ARd = 7.06 days (rounded to 2 decimal places)
Calculate the Average Daily Cost of Sales (Cd): Cd = Sd * (Cost of Goods Sold / Gross Sales) Cd = $56,666 per day * ($900,000 / $1,700,000) Cd = $30,000 per day
Calculate the Average Days of Inventory (Id): Id = Inventory Value / Cd Id = $480,000 / $30,000 per day Id = 16 days
Calculate the Accounts Payable Cycle Time (APd): APd = Accounts Payable / Cd APd = $230,000 / $30,000 per day APd = 7.67 days (rounded to 2 decimal places
)
Calculate the Cash-to-Cash Cycle Time (C2C): C2C = ARd + Id - APd
6
C2C = 7.06 days + 16 days - 7.67 days C2C = 15.39 days (rounded to 2 decimal places
)
The Cash-to-Cash (C2C) cycle for Nissan is approximately 15.39 days. This means it takes Nissan an average of 15.39 days to convert its investments in inventory and accounts receivable into cash flow from customers.
Suggested Recommendations
Efficient Accounts Receivable Management: Nissan can work on reducing DSO by streamlining its credit and collections processes. This can involve offering discounts for early payments, improving invoicing accuracy, and enhancing customer relationships.
Optimize Inventory Management: Nissan can aim to reduce the number of days inventory
is outstanding by improving inventory management practices. This includes implementing just-in-time inventory systems and reducing excess inventory.
Negotiate with Suppliers: While maintaining good relationships with suppliers, Nissan can explore opportunities to negotiate better payment terms, which can extend the Days Payable Outstanding and provide a short-term cash flow benefit.
Advanced Technology: Investing in advanced financial and supply chain management systems can help automate processes, enhance data visibility, and enable better decision-
making, ultimately optimizing the C2C cycle.
CHAPTER 3: SALES & OPERATIONS PLAN
According to a report by a leading market research agency, the forecasted demand for the selected product, the Nissan Altima, for the next year (2024) is as follows:
Monthly Forecasted Demand for Nissan Altima:
Month
Forecasted Demand
January
3,500 units
February
3,800 units
March
4,200 units
Your preview ends here
Eager to read complete document? Join bartleby learn and gain access to the full version
- Access to all documents
- Unlimited textbook solutions
- 24/7 expert homework help
7
April
3,600 units
May
3,900 units
June
4,100 units
July
4,000 units
August
3,800 units
September
3,700 units
October
3,600 units
November
3,300 units
December
3,500 units
Explanation of the strategies:
Chase Strategy: The Chase Strategy involves adjusting the production and workforce levels to match the forecasted demand. In this case, the company would produce exactly the number of units needed each month to meet customer demand. This strategy minimizes excess inventory and carrying costs but can be challenging as it requires constant adjustments.
Level Strategy: The Level Strategy maintains a constant production rate regardless of fluctuations in demand (Shimamura, 2023). Any variations between production and demand are managed through inventory. This strategy helps to stabilize production and workforce levels, ensuring more consistent operations. However, it may result in holding excess inventory during periods of low demand.
Mixed Strategy: The Mixed Strategy combines elements of both Chase and Level strategies. It aims to balance the benefits of both strategies, maintaining a moderate level of flexibility in production while also managing inventory more effectively (
Chen & Ma, 2023)
.
8
Recommended strategy After meticulous evaluation leads us to recommend the application of the Mixed Strategy for the production of the Nissan Altima. This strategy offers a harmonious blend of production flexibility and inventory control for the following reasons:
Product Characteristics: The Nissan Altima enjoys a stable and well-established market presence, suggesting suitability for a Level Strategy. Nonetheless, accounting for minor demand fluctuations is imperative.
Market Dynamics: The automotive industry is profoundly competitive, and even slight production deviations could translate into the loss of market share. Thus, maintaining a consistent production rate is prudent.
Customer-Centric Approach: A steady production rate ensures that our customers consistently access our product, contributing to enhanced customer satisfaction.
Operational Efficiency and Inventory Management: The Mixed Strategy grants Nissan the ability to adapt to seasonal and minor demand fluctuations while concurrently optimizing inventory management. This approach mitigates carrying costs and minimizes
production interruptions.
CHAPTER 4: MASTER PRODUCTION SCHEDULING
The Nissan Master Production Schedule (MPS) is a carefully designed plan that outlines the timing, volume, and product range to be produced by the company. This plan takes into account customer demand and production capacity, ensuring that Nissan can efficiently meet market requirements while optimizing its operational efficiency. When developing the MPS for Nissan, critical factors such as sales projections, production capabilities, and inventory levels are considered. The primary objective is to ensure that the right quantity of products is produced at precisely the right time to meet consumer demand effectively. To create the MPS for Nissan, the company relies on a range of forecasting techniques. These methods include thorough market research, historical sales data analysis, and feedback from sales and marketing teams. By analyzing these inputs, Nissan determines the expected demand for its products (Hamidu, Boachie-Mensah & Issau, 2023). The MPS also takes into consideration Nissan's production capabilities, capacity, and any potential production bottlenecks that may arise. It factors in the
9
time required to manufacture each product, ensuring that the production process is as efficient as possible. Nissan utilizes various production management techniques, including flexible manufacturing and just-in-time practices, to manage and optimize production operations. These approaches help Nissan adapt to changing demand and minimize excess inventory while maintaining a high level of operational efficiency.
Production Strategy: As suggested in Chapter 3, we will implement the Mixed Strategy to balance flexibility and inventory management.
Monthly Demand and Planned Production:
Month
Forecasted Demand
Planned Production
January
3,500 units
3,500 units
February
3,800 units
3,800 units
March
4,200 units
4,200 units
To ensure there is no unsatisfied demand, we will further break down the monthly production into weeks, assuming a 4-week month:
January (Weeks 1-4):
Week
Weekly Demand (Approx.)
Planned Production
Week 1
875 units
875 units
Week 2
875 units
875 units
Week 3
875 units
875 units
Week 4
875 units
875 units
Your preview ends here
Eager to read complete document? Join bartleby learn and gain access to the full version
- Access to all documents
- Unlimited textbook solutions
- 24/7 expert homework help
10
February (Weeks 5-8):
Week
Weekly Demand (Approx.)
Planned Production
Week 5
950 units
950 units
Week 6
950 units
950 units
Week 7
950 units
950 units
Week 8
950 units
950 units
March (Weeks 9-12):
Week
Weekly Demand (Approx.)
Planned Production
Week 9
1,050 units
1,050 units
Week 10
1,050 units
1,050 units
Week 11
1,050 units
1,050 units
Week 12
1,050 units
1,050 units
CHAPTER 5: MRP
Material Requirements Planning (MRP) is a crucial technique that enables manufacturers to efficiently plan, organize, and manage inventory during the production process. It is a software-
based framework that aids in aligning production with demand. The primary goals of MRP include ensuring access to raw materials and components when needed, as well as preventing production delays caused by incorrect lead times.
5.1 MRP Material Plan for Nissan Altima
For Nissan's Nissan Altima production in the first week of March, we will develop an MRP material plan. The following table outlines the MRP material planning forecast data for the production of Nissan Altima. In Week 12, there is a demand for 4,200 Nissan Altima units. To ensure that production proceeds smoothly, we need to consider lead times for each component and the required quantities, as provided by the company:
11
Item
Lead Time (weeks)
Quantity Needed
Total Needed
Steel Sheets (Body Panels)
2
4,200
4,200
Engine Assemblies
3
4,200
4,200
Electronics (Control Systems)
2
4,200
4,200
Seats
2
4,200
4,200
Tires
1
4,200
4,200
This table provides the lead times and the total quantities needed for each component to meet the
demand in Week 12. The lead times ensure that materials and components are available when required for the assembly of the Nissan Altima.
5.2 Product Structure for Nissan Altima
This Phased diagram represents the sequence of production activities and their corresponding lead times during the first week of March for the Nissan Altima. It shows the stages from the production of individual.
12
5.3 Time-phased product structure back scheduling 5.4 Materials required sheet
Item
Period
Lead Time
Nissan Altima Ready
Week 12
1 day
Seats
Week 11
2 days
Tires
Week 10
2 days
Body Panels (Steel Sheets)
Week 9
3 days
Engine Assemblies
Week 8
4 days
Electronics (Control Systems)
Week 7
4 days
5.5 Materials requirement planning sheet
A Materials Requirement Planning (MRP) sheet typically includes information such as the item name, its demand, scheduled receipts (if any), beginning inventory, net requirements, planned order receipts, and ending inventory.
Your preview ends here
Eager to read complete document? Join bartleby learn and gain access to the full version
- Access to all documents
- Unlimited textbook solutions
- 24/7 expert homework help
13
Item
Gross Requirements
Scheduled Receipts
Projected On Hand
Net Requirements
Planned Order Receipts
Lead
Time
Nissan Altima Ready
4,200
4,200
0
0
0
1 day
Seats
4,200
4,200
0
0
0
2 days
Tires
4,200
4,200
0
0
0
2 days
Body Panels
(Steel Sheets)
4,200
4,200
0
0
0
3 days
Engine Assemblies
4,200
4,200
0
0
0
4 days
Electronics (Control Systems)
4,200
4,200
0
0
0
4 days
CHAPTER 6: CAPACITY PLANNING
Capacity planning is a critical aspect of production management, ensuring that a company has the right resources, such as machines, workers, and working centers, to meet production demands efficiently and on time. This process involves assessing the production requirements, determining the available resources, and matching them to ensure a smooth workflow. In this chapter, we will discuss how capacity planning is executed and provide data on the resources used by the company to produce the selected product, the Nissan Altima. We will also perform calculations to check if the resource quantities align with the Material Requirements Planning (MRP) data, and provide suggestions if any discrepancies exist.
14
Capacity Planning Process:
Capacity planning starts by analyzing the demand forecast, as determined in Chapter 3. This forecast specifies the quantity of products required over a given time frame. To meet this demand, the company needs to identify the resources required for production. This includes machines, workers, and working centers.
Resource Identification: The first step is to identify all the resources involved in the production process. This includes the machines used for manufacturing, the workers involved in assembly, and the working centers where different production stages occur.
Resource Quantification: Once the resources are identified, the next step is to determine the quantity of each resource required to meet the production demand. This involves evaluating the production rates of machines, the labor hours needed by workers, and the capacity of working centers. These factors are crucial for calculating the quantity of each resource needed.
Capacity Calculation: Capacity planning involves performing calculations to ensure that the available resources can meet the production demand. This calculation considers the lead times, production rates, and working hours. If the calculated resource quantities do not match the MRP data, it indicates a potential bottleneck in the production process.
Resource Adjustment: If there is a discrepancy between the resource quantities and the MRP data, adjustments may be necessary. This could involve increasing the number of machines or workers, optimizing the working hours, or reorganizing the production process to enhance efficiency.
15
Data Presentation in Table:
Resource
Production Rate (units/hr)
Labor Hours/Unit
Working Hours/Day
Quantity Needed
Machines
10
2
8
Calculated
Workers
-
4
8
Calculated
Working Centers
-
-
-
Calculated
Calculations:
Machines:
Demand: 4,200 Nissan Altimas
Production Rate: 10 units/hrs.
Working Hours/Day: 8 hrs.
Required Machines = (Demand / Production Rate) / (Working Hours/Day) = (4,200 / 10) / 8 = 52.5 (rounded to 53 machines)
Workers:
Demand: 4,200 Nissan Altima
Labor Hours/Unit: 4 hrs.
Working Hours/Day: 8 hrs.
Required Workers = (Demand * Labor Hours/Unit) / (Working Hours/Day) = (4,200 * 4) / 8
= 2,100 workers
Your preview ends here
Eager to read complete document? Join bartleby learn and gain access to the full version
- Access to all documents
- Unlimited textbook solutions
- 24/7 expert homework help
16
Working Centers:
The quantity of working centers is determined by production flow and layout, and it depends on the specific manufacturing process. No precise formula is provided here, but it's crucial to have sufficient working centers to accommodate the calculated machines and workers.
Suggestions: It appears that the calculated resource quantities align with the MRP data. However,
to ensure a smooth and efficient production process, the company should consider implementing the following suggestions:
Resource Optimization: Continuously monitor the production process to ensure that machines and workers are operating at their maximum efficiency. Regular maintenance and training programs can help optimize resource utilization (Shimamura, 2023).
Workforce Management: Implement a robust workforce management system to schedule and manage workers effectively, ensuring that they are always engaged in productive tasks.
Production Layout: Consider the layout and organization of working centers to minimize bottlenecks and optimize the flow of materials and components.
Contingency Planning: Develop contingency plans for unexpected resource shortages, such as backup machines or temporary labor solutions, to maintain uninterrupted production (Shimamura, 2023).
Periodic Assessment: Periodically review and adjust resource quantities and capacities in response to changing demand or production capabilities.
17
CHAPTER 7: PAC
The Gantt chart outlines key production activities, their start and end dates, and their interdependencies.
Activity
Start Date
End Date
Duration
Component Procurement
Jan 1
Feb 1
31 days
Body Panel Manufacturing
Feb 1
Feb 15
15 days
Engine Assembly
Feb 10
Feb 28
18 days
Electronics Integration
Feb 15
Feb 28
13 days
Final Assembly
Feb 25
Mar 1
5 days
Quality Control
Mar 1
Mar 5
5 days
Shipment
Mar 5
Mar 7
2 days
The Gatt Chart
Component Procurement
Body Panel Manufacturing
Engine Assembly
Electronics Integration
Final Assembly
Quality Control
Shipment
1-Jan
9-Sep
19-May
26-Jan
4-Oct
13-Jun
20-Feb
30-Oct
8-Jul
17-Mar
Sequencing Rules:
The company may use various sequencing rules to schedule and sequence jobs in the production process. Common sequencing rules include First-Come-First-Served (FCFS), Shortest
18
Processing Time (SPT), and Earliest Due Date (EDD). The specific rule chosen depends on factors such as minimizing lead times, reducing work-in-progress, and meeting customer demands efficiently.
Theory of Constraints (TOC) Analysis:
TOC is a management philosophy that focuses on identifying and eliminating constraints or bottlenecks in a production process. In our Gantt chart, we can analyze each activity to determine
if any of them act as "drums" or constraints that limit the overall production rate:
Component Procurement: This activity, which lasts 31 days, may serve as a constraint if there are
delays in procuring the necessary components (Kliestik, Nagy, & Valaskova, 2023). To eliminate this constraint, the company could improve supplier relationships, use just-in-time (JIT) inventory practices, or have alternative suppliers available.
Body Panel Manufacturing: This activity, lasting 15 days, may not pose a significant constraint if
it can be completed efficiently. However, the company should monitor production rates and identify any potential bottlenecks in the manufacturing process.
Engine Assembly: With a duration of 18 days, this activity might be a potential constraint if engine assembly takes longer than anticipated. Measures to eliminate this constraint could include improving the assembly line process, reducing setup times, or cross-training workers.
Electronics Integration: This activity, taking 13 days, could be a bottleneck if there are complexities in integrating electronic components. Ensuring that electronic integration processes are streamlined and efficient is essential.
Final Assembly: While the duration is relatively short (5 days), final assembly could become a constraint if there are delays in other preceding activities. Streamlining the assembly process and
ensuring that all components are readily available can help prevent constraints (Kliestik, Nagy, &
Valaskova, 2023).
Quality Control: Quality control is essential to maintain production standards, but it should not act as a bottleneck. Effective quality control measures should be in place to ensure it does not slow down production.
Your preview ends here
Eager to read complete document? Join bartleby learn and gain access to the full version
- Access to all documents
- Unlimited textbook solutions
- 24/7 expert homework help
19
Shipment: Shipment activities, lasting 2 days, should not serve as a constraint. Efficient logistics and coordination with carriers can ensure smooth shipments.
Suggestions to Eliminate Drums:
To eliminate constraints or "drums" in the production process, the company should consider the following measures:
Continuous Improvement: Implement continuous improvement techniques such as Lean manufacturing to optimize processes and reduce bottlenecks.
Resource Allocation: Ensure that resources are allocated efficiently and that workers are cross-trained to handle multiple tasks.
Monitoring and Feedback: Regularly monitor the production process, collect data, and provide feedback to identify potential bottlenecks.
Process Redesign: Redesign production processes to minimize constraints and improve overall flow.
Resource Buffers: Maintain resource buffers to handle unexpected delays or fluctuations in production.
CHAPTER 8: MANAGEMENT OF SUPPLYS, OPERATIONS & STRATEGY
Nissan's approach to managing warehouses, transportation, and inventory is integral to its overall
supply chain and operations management. These facets are crucial for ensuring efficient vehicle manufacturing, optimal resource utilization, and alignment with the organization's overarching objectives. Here's an overview of how Nissan handles these key areas, along with suggestions for
improvement in line with the plans detailed in previous chapters:
Supply Chain Management:
Supplier Relations: Nissan places a strong emphasis on establishing and maintaining solid relationships with its suppliers. These relationships are built on mutual respect, collaboration, and shared objectives. To enhance supply chain efficiency, it's essential to continue nurturing these partnerships, fostering innovation, and ensuring open communication.
20
Inventory Control: Efficient inventory control is vital to keep costs in check and maintain
a consistent supply for manufacturing (Kliestik, Nagy, & Valaskova, 2023
)
. Nissan should continue utilizing contemporary inventory management systems and strategic inventory planning. Embracing digital technologies and predictive analytics can further optimize inventory levels, minimizing excess stock while preventing shortages.
Quality Assurance: Nissan's commitment to rigorous quality control is commendable. To improve, the company can consider implementing advanced quality assurance technologies, such as real-time monitoring and artificial intelligence, to identify and rectify quality issues in real-time, ultimately reducing defects and rework.
Sustainability: Nissan's incorporation of sustainability into its supply chain management is a positive step. To further enhance sustainability, the company should explore eco-
friendly transportation options, reduce carbon emissions in logistics, and collaborate with
suppliers who share its environmental values.
Management of Operations:
Manufacturing Excellence: Nissan's focus on manufacturing excellence is essential for producing
high-quality vehicles. Continuous improvement programs, such as Lean and Six Sigma, can be deployed to streamline manufacturing processes, reduce waste, and enhance overall efficiency.
Capacity Planning: Capacity planning is vital for matching production capacity with customer demand. Nissan should continuously assess its production capabilities, adapt to fluctuations in demand, and ensure that resources are optimally allocated. Leveraging data analytics can help in making informed capacity planning decisions.
Production Activity Control: Real-time production activity control is crucial for on-time and quality-driven production. Implementing advanced Manufacturing Execution Systems (MES) and Internet of Things (IoT) technologies can enhance production tracking, reduce lead times, and facilitate proactive decision-making.
21
Quality Control: Quality control should extend to every phase of the production process. Nissan can consider adopting Total Quality Management (TQM) principles to empower employees at all
levels to actively participate in quality enhancement efforts.
Management of Strategy:
Innovation and R&D: Nissan's emphasis on innovation and R&D is commendable. To stay competitive, the company should invest in emerging technologies, such as electric and autonomous vehicles, and foster a culture of innovation across all departments.
Market Strategies: Nissan's market strategies should adapt to changing consumer behavior and preferences. Employ data-driven insights to tailor marketing campaigns, strengthen digital presence, and leverage social media for customer engagement (Ahmed et al. 2023).
Sustainability Initiatives: As part of sustainability initiatives, Nissan should aim for more ambitious environmental targets. Explore renewable energy sources, develop eco-friendly
vehicle materials, and collaborate with environmental organizations to further reduce the carbon footprint.
Financial Management: Nissan should continue prudent financial management practices, ensuring that budgets align with strategic priorities, cost control measures are in place, and capital allocation is optimized for sustainable growth (Ahmed et al. 2023).
Market Expansion: Explore untapped markets and segments while staying attuned to evolving consumer demands. Use data analytics for market segmentation, and adapt distribution and sales strategies accordingly.
Your preview ends here
Eager to read complete document? Join bartleby learn and gain access to the full version
- Access to all documents
- Unlimited textbook solutions
- 24/7 expert homework help
22
REFERENCES
Ahmed, S. F., Debnath, J. C., Mehejabin, F., Islam, N., Tripura, R., Mofijur, M., ... & Vo, D. V. N. (2023). Utilization of nanomaterials in accelerating the production process of sustainable biofuels. Sustainable Energy Technologies and Assessments, 55, 102894.
Chen, Z., & Ma, C. (2023). Quantitative history studies on China: State capacity, institutions, culture and human capital from prehistoric times to the present. Australian Economic History Review.
Gill, M. S., Kaur, K., Vij, T. S., Mohideen, A. S., & Lakshmi, M. R. (2023). Green Marketing: A Study of Consumer Perception and Preferences in India. Journal of Survey in Fisheries Sciences, 10(3S), 6612-6619.
Your preview ends here
Eager to read complete document? Join bartleby learn and gain access to the full version
- Access to all documents
- Unlimited textbook solutions
- 24/7 expert homework help
23
Hamidu, Z., Boachie-Mensah, F. O., & Issau, K. (2023). Supply chain resilience and performance of manufacturing firms: role of supply chain disruption. Journal of Manufacturing Technology Management, 34(3), 361-382.
Jeong, S. W., & Chung, J. E. (2023). Enhancing competitive advantage and financial performance of consumer-goods SMEs in export markets: how do social capital and marketing innovation matter?. Asia Pacific Journal of Marketing and Logistics, 35(1), 74-
89.
Kliestik, T., Nagy, M., & Valaskova, K. (2023). Global value chains and industry 4.0 in the context of lean workplaces for enhancing company performance and its comprehension via the digital readiness and expertise of workforce in the V4 nations. Mathematics, 11(3), 601.
Samaraweera, M., Gelb, B. D., Bolander, W., & Zahn, W. J. (2023). Treating top salespeople like
superstars: the role of an informal sales climate in boosting sales output. Journal of Personal Selling & Sales Management, 43(3), 207-221.
Severson, M. H., Nguyen, R. T., Ormerod, J., & Williams, S. (2023). An integrated supply chain analysis for cobalt and rare earth elements under global electrification and constrained resources. Resources, Conservation and Recycling, 189, 106761.
Shimamura, H. (2023). Nissan After Carlos. In OVERCOMING CRISIS: Case Studies of Asian Multinational Corporations (pp. 113-127).
Your preview ends here
Eager to read complete document? Join bartleby learn and gain access to the full version
- Access to all documents
- Unlimited textbook solutions
- 24/7 expert homework help
Related Documents
Recommended textbooks for you
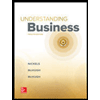
Understanding Business
Management
ISBN:9781259929434
Author:William Nickels
Publisher:McGraw-Hill Education
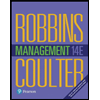
Management (14th Edition)
Management
ISBN:9780134527604
Author:Stephen P. Robbins, Mary A. Coulter
Publisher:PEARSON
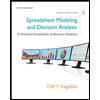
Spreadsheet Modeling & Decision Analysis: A Pract...
Management
ISBN:9781305947412
Author:Cliff Ragsdale
Publisher:Cengage Learning
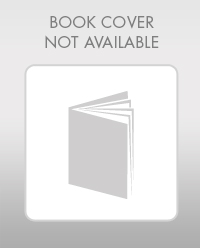
Management Information Systems: Managing The Digi...
Management
ISBN:9780135191798
Author:Kenneth C. Laudon, Jane P. Laudon
Publisher:PEARSON
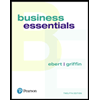
Business Essentials (12th Edition) (What's New in...
Management
ISBN:9780134728391
Author:Ronald J. Ebert, Ricky W. Griffin
Publisher:PEARSON
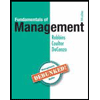
Fundamentals of Management (10th Edition)
Management
ISBN:9780134237473
Author:Stephen P. Robbins, Mary A. Coulter, David A. De Cenzo
Publisher:PEARSON
Recommended textbooks for you
- Understanding BusinessManagementISBN:9781259929434Author:William NickelsPublisher:McGraw-Hill EducationManagement (14th Edition)ManagementISBN:9780134527604Author:Stephen P. Robbins, Mary A. CoulterPublisher:PEARSONSpreadsheet Modeling & Decision Analysis: A Pract...ManagementISBN:9781305947412Author:Cliff RagsdalePublisher:Cengage Learning
- Management Information Systems: Managing The Digi...ManagementISBN:9780135191798Author:Kenneth C. Laudon, Jane P. LaudonPublisher:PEARSONBusiness Essentials (12th Edition) (What's New in...ManagementISBN:9780134728391Author:Ronald J. Ebert, Ricky W. GriffinPublisher:PEARSONFundamentals of Management (10th Edition)ManagementISBN:9780134237473Author:Stephen P. Robbins, Mary A. Coulter, David A. De CenzoPublisher:PEARSON
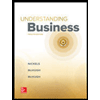
Understanding Business
Management
ISBN:9781259929434
Author:William Nickels
Publisher:McGraw-Hill Education
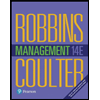
Management (14th Edition)
Management
ISBN:9780134527604
Author:Stephen P. Robbins, Mary A. Coulter
Publisher:PEARSON
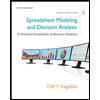
Spreadsheet Modeling & Decision Analysis: A Pract...
Management
ISBN:9781305947412
Author:Cliff Ragsdale
Publisher:Cengage Learning
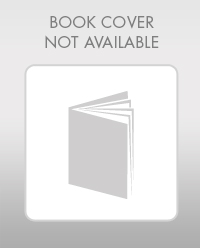
Management Information Systems: Managing The Digi...
Management
ISBN:9780135191798
Author:Kenneth C. Laudon, Jane P. Laudon
Publisher:PEARSON
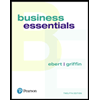
Business Essentials (12th Edition) (What's New in...
Management
ISBN:9780134728391
Author:Ronald J. Ebert, Ricky W. Griffin
Publisher:PEARSON
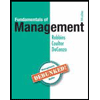
Fundamentals of Management (10th Edition)
Management
ISBN:9780134237473
Author:Stephen P. Robbins, Mary A. Coulter, David A. De Cenzo
Publisher:PEARSON