answer-la017855-assmt-6
pdf
keyboard_arrow_up
School
TAFE NSW - Sydney Institute *
*We aren’t endorsed by this school
Course
CPC40110-0
Subject
Civil Engineering
Date
Dec 6, 2023
Type
Pages
48
Uploaded by MajorChinchilla3333
Studocu is not sponsored or endorsed by any college or university
Answer LA017855 Assmt 6
Apply structural principles to residential low constructions (TAFE New South Wales)
Studocu is not sponsored or endorsed by any college or university
Answer LA017855 Assmt 6
Apply structural principles to residential low constructions (TAFE New South Wales)
Downloaded by Bob Young (bobby319163@gmail.com)
lOMoARcPSD|27337005
CPCCBC4010B: Assessment 6
What you have to do
Refer to Project 1 and Project 3 on the OLS and the sketching guidelines, to help you complete the questions below.
Sketching guidelines
This assessment contains a number of tasks requiring you to prepare sketches of
relevant construction details. The sketches are to be prepared to a standard
acceptable to allow communication of a detail as would occur on a construction site.
Many details are communicated in this manner and everyone involved with building
sites should be skilled in the preparation of sketches.
Sketches are freehand drawings. Line work and proportion are important
considerations that must be satisfied in the assessment. Select a scale/size
appropriate to the detail.
It is not expected everyone will have these skills at the commencement of this
assessment. This first assessment may be presented with a mix of freehand
sketches and ruled drawings. All should be completed in pencil on A4 size paper.
Refer to the project documentation before commencing the drawings to clearly
identify and comply with the documents. This question may require you to carry out
research of the topics to broaden your knowledge before attempting the answers.
Submissions, which are assessed to be not of an acceptable standard, will be
returned with a request to resubmit the assessment.
All questions must be attempted and satisfactorily completed to achieve a pass. Question 1 (15 marks)
(refer to Project 3)
Develop a plan to demolish the existing dwelling shown on the site plan in accordance with
the legislative and planning requirements and at all times utilising safe work practices. The
dwelling will have been constructed from some building materials containing bonded
asbestos.
In your plan, list the relevant Acts, Australian Standards and Codes with which the processes
will need to comply.
Note: This is not a sketch, but a set of steps outlining your approach. You might include a
sketch to indicate specific requirements of the demolition process.
PRELIMINARY DEMOLITION PLAN
Factory Complex Development
1
/ 47
Downloaded by Bob Young (bobby319163@gmail.com)
lOMoARcPSD|27337005
23 May 2014
Factory Development Centre
T: [02] 9787 1233 F: [02] 9787 1234
EXECUTIVE SUMMARY This report provides a brief outline of the works required to demolish the existing buildings
on the factory to be redeveloped into a mixed use development consisting of new factory
units and car spots.
The Preliminary Demolition Plan will be used as a reference document that provides the
framework to ensure that demolition activities on the site do not adversely affect the health,
safety, traffic or the environment of the public and neighbouring properties. The report is preliminary in its nature and will be developed in much more significant detail
as the design is further developed. The Contractor will be required to prepare a detailed
Demolition Plan and Construction Management Plan to the satisfaction of the Applicant and
relevant Authorities prior to the commencement of works on site.
A.
Risk Management before Demolition Work
1.
Olympic Designs has the primary duty to ensure the works and other persons are not
exposed to health and safety risks arising from this demolish job.
According to WHS Regulations, a SWMS for this demolish work should already been
prepared.
A copy of the asbestos register for Layland Factory has been carried out before demolishes
work start.
Olympic Designs will ensure that all asbestos will be removed by competent person before
the demolition commerce.
2.
Olympic Designs should manage risks associated with demolition work. ( Regulation 34-
38)
Olympic Designs will identify hazards that could give rise to the risk, and eliminate the risk or
minimize the risk and maintain the implemented control measure, and review, revise control
measures to maintain a work environment that is without risk to health and safety.
B.
Planning the Demolition Work
1.
Notifiable demolition work (Regulation 142) Tasmegs Development P/L should give
written notice the regulator at least 5 days before any of the work commences
1
:
Demolition of a structure, or a part of a structure that is load bearing or otherwise
Related to the physical integrity of the structure, that is at least 6 meters in height
Demolition work is involving load shifting machinery on a suspended floor, or demolition
work involving explosives.
The following details should be included in the notification:
Name and contact details of authorized person from Olympic Designs
Name and contact details of the person directly supervising the work
The date of the notice
The nature of the demolition
Layland working site address should be disclosure in the notification
1 https://www.safeworkaustralia.gov.au/system/files/documents/1705/mcop-demolition-
work-v1.pdf
, P11
2
/ 47
Downloaded by Bob Young (bobby319163@gmail.com)
lOMoARcPSD|27337005
Your preview ends here
Eager to read complete document? Join bartleby learn and gain access to the full version
- Access to all documents
- Unlimited textbook solutions
- 24/7 expert homework help
Tasmegs must ensure that a copy of the building permit for the demolition is displayed and
accessible to the public.
2.
Olympic Designs has a range of duties in relation to a construction project, including:
Preparing and reviewing a WHS management plan
Obtaining SWMS before any high risk construction work commences
Putting in place arrangements to manage the work environment, including falls, facilities,
first aid, an emergency plan and traffic management
Installing signs showing the principal contactor’s name, contact details and location of any
site office, and securing the construction workplace.
Olympic Designs will also be required to prepare the following documentation prior to the
commencement of demolition and/or excavation works: • Dilapidation Survey • Construction Waste Management Plan • Demolition Management Plan • Excavation Management Plan All works are to be undertaken in accordance with relevant EPA guidelines. In principle, the
demolition process is undertaken in the reverse sequence as construction. Essentially,
internal finishes will be stripped out. Services will then be removed including air conditioning,
pipework and conduit. The facades will be removed where necessary and the structure will
then be demolished using the larger plant and equipment. It is estimated that it will take 3 months to demolish and clear the site. Also refer to the Preliminary Construction Management Plan submitted as part of the
Statement of Environmental Effects. 3.
Setting out Olympic Designs is to engage and pay for a licenses registered surveyor to identify and peg
necessary site boundaries, produce check surveys on footings and walls to verify location
and alignment and produce an Identification Survey on completion. Before making the first
Progress Claim the Builder shall provide a certificate from a registered surveyor stating that
the building has been set out in accordance with the drawings and is wholly within the
boundaries of the site. The existing buildings across the sites are of varying heights ranging from 10 - 15m above
existing street levels. A number of the buildings have been built to within 20mm of the site boundary. Olympic Designs should ensure the two buildings to be demolished are not protected under
the Heritage Act 1977(NSW)
An A Class hoarding will be erected around the perimeter of the construction site prior to the
commencement of demolition works. Additionally, wherever the risk arises of material falling into public areas, overhead protection
will be provided in the form of a B Class hoarding. At this stage, it is anticipated that a B
Class hoarding will be established on the Layland St boundary. Scaffolding will be erected to facades where materials could fall in excess of 4m. The
scaffolding will be clad with chain wire and shade cloth to enclose debris and dust onto the
site. During the demolition, dust control measures will be used to minimise the spread of dust
from site. 3
/ 47
Downloaded by Bob Young (bobby319163@gmail.com)
lOMoARcPSD|27337005
The Contractor will have a senior representative on site at all times to ensure compliance
with the safety guidelines and agreed work methods. 4.
The following design matters should be taken into account when considering demolition
risks
2
:
the stability and structural integrity of the structure at all stages of demolition
the maximum permissible wind speed for partially demolished structures
the effect of the proposed demolition sequence on stability
the stability requirements for all components of the structure as it is sequentially demolished according to the structural engineer’s requirements
the proximity of adjacent or adjoining buildings
the competent persons assessment of loadings at all stages of demolition
the provision of clear instructions for temporary bracing
the plant to be used for the work including the size, type, position and coverage of proposed demolition crane(s) should be indicated on a site plan, locations such as unloading points and storage areas (if any) should be shown the need to ensure that the ground is compacted to any design specifications to enable plant to be moved and used safely at the workplace
the proposed methods for handling heavy, bulky or awkward components
the need for specific lifting arrangements to be detailed on structural member drawings
to facilitate safe lifting
the handling, lifting, storing, stacking and transportation of components, depending
on their size, shape and weight, and the provision of safe access and safe working areas
5.
Tree Removal requirements
There are few plants in the construction site need to be removed, and Banksia is governing
by Bayside Council. Therefore, the requirements of tree removals from Bayside Council
should be followed.
2 https://www.safeworkaustralia.gov.au/system/files/documents/1705/mcop-demolition-work-
v1.pdf
, P13
4
/ 47
Downloaded by Bob Young (bobby319163@gmail.com)
lOMoARcPSD|27337005
Tree removal permit should be obtained from Bayside Council.
Olympic Designs should fill an application form and waiting for the Council’s accessing, then
can start removing plants on the site.
6.
Demolition Licensing
Olympic Designs should acquire a license for the demolition. If asbestos show up, all
asbestos or asbestos-containing materials at the work place is identified by a competent
person and an asbestos register is prepared for work place (Regulations 422 (1)(2b),
425(1)). A person conducting a business or undertaking that commissions the removal of asbestos
must ensure that the asbestos removal work is carried out by a licensed asbestos removals
who is appropriately licensed to carry out the work, unless specified in the WHS Regulations that a license is not required(Regulation 458).
7.
No part of the demolition process is adversely affecting the structural integrity of any
other building, because there is no adjacent buildings and both adjoining buildings will be
demolish at the same time.
8.
Type of building to demolished
A few general requirements for demolition buildings:
Those building are not exempt development buildings, therefore, a council approval should
be acquired before demolition work start
The demolition site is NOT contaminated
The Demolition site is NOT heritage significance
The demolition site is NOT in a bushfire prone area
The demolition site is NOT a critical habitat of an endangered species, population or
ecological community under the Threatened Species Conservation Act 1995
or the Fisheries
Management Act
1994
;
The demolition site is NOT a wilderness area under the Wilderness Act 1987
.
Buildings constructed before 1987 may contain asbestos. Information of the removal and
disposal of asbestos is available from the Department of Environment, Climate Change and
Water
.
3
Works must be structurally adequate, installed in accordance with manufacturer’s
specifications and comply with the Building Code of Australia (BCA).
4
Any structures that would be located on public land, or on or over a public road (including
temporary structures), must have separate approval from the relevant council, or Roads and
Maritime Services under the Roads Act 1993
and the Local Government Act 1993.
5
With the exception of the existing concrete car park, the buildings to be demolished are
generally constructed with load bearing masonry walls with steel or timber framed roofs and
metal roofs. The buildings range from single to 2-storey. The buildings are generally constructed off a concrete slab on ground, presumably with strip
and pad footings. There are no basement levels in any of the buildings.
The factory complex which fronts Layland St is a conventionally reinforced concrete framed
building. The substructure is comprised of a series of bored concrete piles. 3 https://www.planningportal.nsw.gov.au/understanding-planning/assessment-
systems/exempt-development/demolition-exempt
4 https://www.planningportal.nsw.gov.au/understanding-planning/assessment-
systems/exempt-development/demolition-exempt
5 https://www.planningportal.nsw.gov.au/understanding-planning/assessment-
systems/exempt-development/demolition-exempt
5
/ 47
Downloaded by Bob Young (bobby319163@gmail.com)
lOMoARcPSD|27337005
Your preview ends here
Eager to read complete document? Join bartleby learn and gain access to the full version
- Access to all documents
- Unlimited textbook solutions
- 24/7 expert homework help
Beyond the concrete frame, the room comprises masonry, plasterboard, mechanical
services, some glass skylights and windows, existing escalators, terrazzo and tile floors and
walls.
9.
Disconnection of all essential services.
Essential services include the supply of gas, water, sewerage, telecommunications,
electricity, chemicals, fuel and refrigerant in pipes or lines. Olympic Designs must ensure,
that essential services at the workplace are without risks to health and safety.
Construction work is defined by the WHS Regulations as ‘high risk construction work’ when
carried out:
on or near pressurized gas distribution mains or piping
on or near chemical, fuel or refrigerant lines, and
on or near energized electrical installations.
A SWMS must be prepared before this work commences.
All electric, gas, water, sewer, steam and other service lines not required in the demolition
process should be shut off, capped, or otherwise controlled, at or outside the building line,
before demolition work is started. In this demolish working site, where core holes and embedment of services lines and fittings
are required in the concrete and not shown on the drawings, details of such core holes and
embedment shall be submitted to the Architect. Cores shall not be cut or drilled in the
hardened concrete without the approval of the Engineer. Drains and other underground or
enclosed work shall be left exposed until inspected, tested and approved.
C.
Controlling Risk During Demolition Work
1.Hazardous chemicals and materials
According to Regulation 49, Olympic Designs should make sure there is no person at the
workplace is exposed to a substance or mixture in an airborne concentration that exceeds
the exposure standard for the substance or mixture.
Before starting any demolition work, all areas of the workplace, including basements, cellars,
vaults and waste dumps, should be examined to determine whether:
there are any items which could be a fire and explosion risk any previous use of the site
might cause a risk because of the nature of and/or decomposition of materials, and
there are any toxic, radioactive or other hazardous chemicals present. Appropriate, clean facilities and amenities must be provided for workers to minimize risks
where there are hazardous materials present.
Any construction work including demolition work that involves or is likely to involve the
disturbance of asbestos is defined by the WHS Regulations as high risk construction work
and a SWMS must be prepared before this work commences. Meanwhile, only competent
person can handle asbestos and remove it properly.
Lead is found in paint, old water pipes and other plumbing fittings, sheet lead, solders, lead
flashing, lead light windows and glass. The age of a structure may be directly related to the
amount of lead that can be present. Meanwhile, only competent person could remove lead
properly and reduce contaminations of the site.
PPE should be provided to workers and worn when insulation (Synthetic Mineral Fibers) is
being removed during the demolition process and dust should be suppressed by damping
down. Workers can be exposed to Polychlorinated Biphenys (PCBs) when dismantling electrical
capacitors and transformers or when cleaning up spills and leaks. Appropriate control
measures should be implemented when handling damaged capacitors to ensure that any
spillage does not contact workers and is appropriately cleaned up and disposed of. 6
/ 47
Downloaded by Bob Young (bobby319163@gmail.com)
lOMoARcPSD|27337005
2. Securing the work area
Olympic Designs should do exclusion zones to protect workers undertaking demolition
activities by taking the following activities:
erecting secure impassable barricades with adequate signage and appropriate lock out
procedures to prevent unauthorized pedestrian or vehicular access to the area. 2 meter high
temporary construction fencing must be provided around the allotment throughout the
demolition period by Olympic Designs (AS1725).
Appropriate signage is displayed throughout the works(AS1170)
providing information to workers and other persons at the workplace advising them of the status of the exclusion zones, and
providing supervision so that no unauthorized person enters an exclusion zone.
Exclusion zones and safe distances may be required during:
the stripping, removal and/or dropping of debris
the operation of demolition plant or equipment
pre-weakening activities for a deliberate collapse, and
the deliberate collapse or pulling over of buildings or structures. 3.
Public access and protection
Olympic Designs should make sure adequate public safety should be maintained in public
places and areas adjoining the workplaces as the demolition progresses. Security fencing,
containment sheets and mesh, an overhead protective structure, road closures and specified
exclusion zones.
Overhead protective structures should be provided for public walkways in conjunction with
perimeter fencing.
4.
All plants and equipment should be operated by competent person
5.
Risk of fall must be managed according to WHS Regulations.
6.
Electricity power sources should be strictly controlled and monitor.
7.
Adequate fire prevention equipment should be provided and maintained at all times
during demolition of a structure.
8.
Olympic Designs should make sure that all workers should successfully complete
general construction induction training. (Regulation 317)
D.
Demolition Method
1.Olympic Designs will take mechanical demolition as the main demolition method.
2. All powered mobile plant used for demolition work must be fitted with a suitable
combination of operator protective devices.
3. Throughout the demolition period, the work shall be under the continuous supervision of
the demolisher or of an experienced foreman from Olympic Designs. 4. Demolition Method
It is anticipated that the Contractor will prepare a detailed Demolition Plan prior to the
commencement of work on site, however, the indicative demolition methodology will be as
follows: The strip out and removal of non-structural elements will be undertaken utilising manual
labour and small plant including – bobcats, 3-5t excavators and dingo type loaders. The
materials will be removed from site using small to medium sized trucks. The structures will be demolished using larger plant and equipment including 15-40t
hydraulic excavators. These machines will be equipped with rock breakers, pulverisers and
the like which would be used in a sequential manner. This sequential nature is the reverse
order to the method of construction (refer to section 3.4 of AS2601-2001). The positioning of plant and equipment onto the suspended slabs will be subject to the
advice of a structural engineer. This engineer will be engaged to provide further engineering
advice in relation to temporary support or back propping of the structure during demolition.
7
/ 47
Downloaded by Bob Young (bobby319163@gmail.com)
lOMoARcPSD|27337005
Additionally, the engineer will be used to assist in the selection and movement of plant
between floors. Equipment will be moved between floors by a number of methods including carnage,
construction of temporary ramps and the like. During the demolition process erosion control measures will be established. These will
include treatment of dust and potential discharge into stormwater systems. 5. Material Handling
Materials handling will be by mechanical plant (including excavators and bobcats) loaded
into trucks (bogie tippers and semi-trailers). The debris will be carted offsite to an approved
waste facility or recycling centre. Given the green star rating of the project, the contractor shall submit a Demolition Waste
Management Plan to Council which outlines the objectives of: • maximisation, reuse and recycling of demolition material • minimisation of waste disposal • evidence of implementation for specified arrangements of waste management On-site storage of reusable materials will occur at the existing car park facing Layland
Street. Recycling and disposal containers will also be accommodated at this location for
collection vehicles. Hazardous materials will be treated separately. A hazardous materials inspection will be
undertaken by an accredited consultant and a report issued. Hazardous materials will be
removed in accordance with “Environmental Guidelines: Assessment, Classification &
Management of Liquid and Non-Liquid Wastes” (NSW, EPA 2004). A final clearance report will be provided by the hygienist who will include the provision of tip
dockets from waste centres. 6. PROTECTIVE MEASURES 7. ENVIRONMENTAL MANAGEMENT PLAN A detailed Environmental Management Plan will be provided by the Contractor prior to the
commencement of the work. 8. OH&S POLICY A detailed OH&S Policy in compliance with AS4801 will be provided by the Contractor prior
to work commencement. A detailed Site Safety Plan will be prepared for the specific project.
9.
Upon completion of the demolition works, notification shall be given to the building
surveyor/Consultant that the work has been completed satisfactorily.
Appendix A
8
/ 47
Downloaded by Bob Young (bobby319163@gmail.com)
lOMoARcPSD|27337005
Your preview ends here
Eager to read complete document? Join bartleby learn and gain access to the full version
- Access to all documents
- Unlimited textbook solutions
- 24/7 expert homework help
*The above sketch is from the Study resource of TAFE digital NSW.
Question 2 (5 marks)
(refer to Project 3)
From the project documentation, illustrate the loads the building will be subjected to during
its life. Prepare a simple sketch of a section passing through the centre of the building,
showing the structural elements of the building and the loads applied. Draw arrows on the section to show the direction the load path will take to transfer the loads
to the foundation of the building. Your illustration(s) should deal with wind loads as well as
dead and live loads.
Tip: Refer to AS1684.4 Fig 9.1.
9
/ 47
Downloaded by Bob Young (bobby319163@gmail.com)
lOMoARcPSD|27337005
Question 3 (10 marks)
(Refer to Project 1)
Research and list the Building Code of Australia requirements for the dwelling if it was to be
built within the following zones:
Project 1
Building Code
Requirements
Bush
Fire
(Medium Risk)
Building
Code
volume two, section
two
performance
provisions,
Part 2.3 Fire safety P2.3.4
Bushfire
areas and P2.3.5
P2.3.4 Bushfire areas
A Class 1 building or a Class 10a building or deck
associated with a Class 1 building that is constructed in a
Open link in same pagedesignated bushfire prone area
must, to the degree necessary, be designed and constructed
to reduce the risk of ignition from a bushfire, appropriate to
the—
(a)
potential for ignition caused by burning embers, radiant heat
or flame generated by a bushfire; and
(b)
intensity of the bushfire attack on the building.
Open link in same pageSTATE AND TERRITORY
VARIATIONS
P2.3.5 Private bushfire shelters
A Open link in same pageprivate bushfire shelter must be
designed and constructed to provide a tenable environment
for occupants during the passage of untenable conditions
arising from a bushfire event, appropriate to the—
10
/ 47
Downloaded by Bob Young (bobby319163@gmail.com)
lOMoARcPSD|27337005
(a)
location of the Open link in same pageprivate bushfire
shelter relative to fire hazards including—
(i)
predominant vegetation; and
(ii)
adjacent buildings and structures; and
(iii)
allotment boundaries; and
(iv)
other combustible materials; and
(b)
occupancy of the Open link in same pageprivate bushfire
shelter; and
(c)
bushfire intensity having regard for the bushfire attack level;
and
(d)
fire intensity from adjacent buildings and structures,
allotment boundaries and other combustible materials; and
(e)
ready access to the Open link in same pageprivate bushfire
shelter from the associated dwelling and occupant egress
after the fire; and
(f)
tenability within the Open link in same pageprivate bushfire
shelter for the estimated maximum period of occupancy; and
(g)
generation of smoke, heat and toxic gases from materials
used to construct the Open link in same pageprivate bushfire
shelter; and
11
/ 47
Downloaded by Bob Young (bobby319163@gmail.com)
lOMoARcPSD|27337005
Your preview ends here
Eager to read complete document? Join bartleby learn and gain access to the full version
- Access to all documents
- Unlimited textbook solutions
- 24/7 expert homework help
(h)
structural and fire loads and actions to which it may
reasonably be subjected, appropriate to—
(i)
the topography between the Open link in same pageprivate
bushfire shelter and the predominant vegetation or other fire
hazards; and
(ii)
the distance between the Open link in same pageprivate
bushfire shelter and the predominant vegetation or other fire
hazards; and
(iii)
the size of the potential fire source and fire intensity; and
(iv)
wind loading; and
(v)
potential impact from debris such as falling tree limbs; and
(i)
degree of external signage identifying the location of the
Open link in same pageprivate bushfire shelter; and
(j)
degree of internal signage identifying the design capacity
and maximum period of occupancy; and
(k)
degree of occupant awareness of outside environmental
conditions; and
(l)
degree of essential maintenance.
High Wind
BCA, Volume
2, Section 3,
Part 3.10.1
3.10.1.0
Performance Requirement
Open link in same page
P2.1.1
is 12
/ 47
Downloaded by Bob Young (bobby319163@gmail.com)
lOMoARcPSD|27337005
satisfied for a building constructed in a Open link in same page
high wind area
if it complies with one or more of the following, as appropriate:
(a)
Masonry:
(i)
AS 3700.
(ii)
AS 4773 Parts 1 and 2.
(b)
The Northern Territory Deemed-to-Comply Standards Manual.
(c)
Timber:
(i)
AS 1684.2.
(ii)
AS 1684.3.
(d)
Steel:
(i)
Steel framing: AS 4100.
(ii)
Cold-formed steel structures: AS 4600.
(iii)
Residential and low-rise steel framing: NASH Standard – Residential and Low-Rise Steel Framing, Part 1 or Part 2.
(e)
Glazed assemblies:
(i)
AS 2047 for the following glazed assemblies in an Open link in same page
external wall
:
13
/ 47
Downloaded by Bob Young (bobby319163@gmail.com)
lOMoARcPSD|27337005
(A)
Open link in same page
Windows
excluding those listed in Open link in same page
(ii)
.
(B)
Sliding and swinging doors with a frame, including french and bi-fold doors with a frame.
(C)
Adjustable louvres.
(D)
Window walls with one piece framing.
(ii)
AS 1288 for all glazed assemblies not covered by Open link in same page
(i)
and the following glazed
assemblies:
(A)
All glazed assemblies not in an Open link in same page
external wall
.
(B)
Revolving doors.
(C)
Fixed louvres.
(D)
Skylights, roof lights and Open link in same page
windows
in other than the vertical plane.
(E)
Sliding and swinging doors without a frame.
(F)
Windows
constructed on site and architectural one-
off Open link in same page
windows
, which are not design tested in accordance with AS 2047.
(G)
Second-hand Open link in same page
windows
, re-
used Open link in same page
windows
and recycled Open link in same page
windows
.
14
/ 47
Downloaded by Bob Young (bobby319163@gmail.com)
lOMoARcPSD|27337005
Your preview ends here
Eager to read complete document? Join bartleby learn and gain access to the full version
- Access to all documents
- Unlimited textbook solutions
- 24/7 expert homework help
(H)
Heritage Open link in same page
windows
.
(I)
* * * * *
(J)
Glazing used in balustrades and sloping overhead glazing.
(f)
In cyclonic areas, metal roof assemblies, their connections and immediate supporting members must be capable of remaining in position notwithstanding any permanent distortion, fracture or damage that might occur in the sheet or fastenings under the pressure sequences A to G defined in Open
link in same page
Table 3.10.1
.
Table 3.10.1 Low-High-Low pressure sequence
Sequence
Number of cycles
Load
A
4500
0 to 0.45 Pt
B
600
0 to 0.6 Pt
C
80
0 to 0.8 Pt
D
1
0 to 1.0 Pt
E
80
0 to 0.8 Pt
F
600
0 to 0.6 Pt
G
4500
0 to 0.45 Pt
Notes:
1. Pt is the ultimate limit state wind pressure on internal and external surfaces as determined in accordance with AS/NZS 1170.2, modified by an appropriate factor for variability, as determined in accordance with Table B1 of AS/NZS 1170.0.
2. The rate of load cycling must be less than 3Hz.
3. The single load cycle (sequence D) must be held for a minimum of 10 seconds.
15
/ 47
Downloaded by Bob Young (bobby319163@gmail.com)
lOMoARcPSD|27337005
(g)
For the purposes of Open link in same page
(f)
, cyclonic areas are those determined as being located
in wind regions C and D in accordance with Open link
in same page
Figure 3.10.1.4
.
(h)
Garage doors and other large access doors in openings not more than 3 m in height in Open link in same page
external walls
of buildings determined as being located in wind region C or D in accordance with Open link in same page
Figure 3.10.1.4
:
AS/NZS 4505.
Earthquak
e
BCA, Volume
2, Section 3,
Part 3.10.2
3.10.2.0
Performance Requirement
P2.1.1
for Class 1 and 10 buildings constructed in areas subject to seismic activity is satisfied if the building is constructed in accordance with the acceptable construction manuals listed in Open link in same page
Part 3.11
.
Open link in same page
Explanatory information
Alpine area
(NSW)
BCA, Volume
2, Section 2,
Part2.3.6
P2.3.6 Alpine areas
(a)
An external doorway from a building in an Open link in same page
alpine area
must be installed so that opening the door is not obstructed by snow or ice.
(b)
A building in an Open link in same page
alpine area
containing external trafficable structures forming part of the means of egress must be constructed so that they remain, as far as practicable, useable under snow conditions.
(c)
A building in an Open link in same page
alpine area
must be constructed so that snow or ice is not shed from the building onto the allotment, any adjoining allotment, road or public space in a location or manner that will—
16
/ 47
Downloaded by Bob Young (bobby319163@gmail.com)
lOMoARcPSD|27337005
(i)
obstruct a means of egress from any building to a road or open space; or
(ii)
otherwise endanger people.
Question 4 (20 marks)
(refer to Project 1)
a.
(15 marks)
A site inspection is necessary prior to tendering or commencing construction on a project to
assess the natural and developed features of the site which will contribute to the cost and/or
planning of the construction. Consider the site of the dwelling is vacant and you are intending to tender on the
construction of the building. Create a checklist for a preliminary site inspection of the site
which could be used on future projects. The checklist should be word processed and
incorporate tables where suitable. Project Details
Project Reference Number:
Project Title:
Owner:
Property Address:
BA Permit Number:
Title Reference:
Designer:
Building Surveyor:
Builder:
Engineer:
Classification of Building:
Number of Storeys:
Type of Construction:
Inspection Date:
Consultant Reports Checked
Geotechnical Engineers Report
Hydrology Report
Structural Engineers Report
17
/ 47
Downloaded by Bob Young (bobby319163@gmail.com)
lOMoARcPSD|27337005
Your preview ends here
Eager to read complete document? Join bartleby learn and gain access to the full version
- Access to all documents
- Unlimited textbook solutions
- 24/7 expert homework help
Site Inspection Checklist Checked
PPE Gear
Torch and Mirror
Steel bar
Steel reinforcement gauge
Measuring Tapes (8m&30m)/EMD
Compass
Ipad/Tablet
Mobile Phone
Wet Weather Gear
Approved Building Plans and Specifications
Development Approval Conditions
Title Survey
Site Plan
Camera
Site Weather Conditions on Site
Fine
Rain
Humidity
Compliant Checklist Legend
CP
Compliant with approved plans and specifications
NC
Not Compliant with BCA and Standard
Requirements
NAR
No action required
FIR
Further Information Required
N/A
Not Applicable
18
/ 47
Downloaded by Bob Young (bobby319163@gmail.com)
lOMoARcPSD|27337005
To be completed during visit
Checked
Comment
Photos of site
Sketch site
Topography
Building Location
Security Fencing
Boundary identification
Site drainage
Excavations
Sedimentation control
Protection of adjoining properties
Demolition
Asbestos removal
Foundation solil type
Soil to classification
Compacted fill
Landslip
Bearing Value
Wind Classification(BCA)
Access issues
Vegetation
Bushfire management
Surrounding buildings
Site office and amenities
Weather data
19
/ 47
Downloaded by Bob Young (bobby319163@gmail.com)
lOMoARcPSD|27337005
Environmental issues
Services
In accordance with approved plans
Note:
b.
+(5 marks)
Provide a sketch of the site clearly showing salient features such as:
vegetation
rock features existing services
improvements such as fences and existing buildings
orientation
contours
20
/ 47
Downloaded by Bob Young (bobby319163@gmail.com)
lOMoARcPSD|27337005
Your preview ends here
Eager to read complete document? Join bartleby learn and gain access to the full version
- Access to all documents
- Unlimited textbook solutions
- 24/7 expert homework help
21
/ 47
Downloaded by Bob Young (bobby319163@gmail.com)
lOMoARcPSD|27337005
Your preview ends here
Eager to read complete document? Join bartleby learn and gain access to the full version
- Access to all documents
- Unlimited textbook solutions
- 24/7 expert homework help
Question 5 (10 marks)
(refer to Project 1)
22
/ 47
Downloaded by Bob Young (bobby319163@gmail.com)
lOMoARcPSD|27337005
Your preview ends here
Eager to read complete document? Join bartleby learn and gain access to the full version
- Access to all documents
- Unlimited textbook solutions
- 24/7 expert homework help
Prepare a list and description of all the relevant services required or likely to be installed in
and around the building and note any special provisions needed. For each service, list the
Australian Standard or Code with which the service must comply.
NSW P2.6.2 Services
6
Domestic services
, including any associated distribution system and components must, to the degree necessary, have features that facilitate the efficient use of energy appropriate to
—
(a)
the Open link in same page
domestic service
and its usage; and
(b)
the geographic location of the building; and
(c)
the location of the Open link in same page
domestic service
; and
(d)
the energy source.
Limitations
Limitations:
1.
NSW P2.6.2
does not apply to existing services associated with existing buildings being relocated.
2.
Compliance is not Open link in same page
required
with the national BCA provisions of Open link in same page
P2.6.2(b)
as the sources of energy are regulated under BASIX.
Service
Building
Code
Requirements 7
Heating
Water
BCA,
Volume
2,
Section
3.12.5.2
Central heating water that is not within a
conditioned space
must be
thermally insulated to achieve the minimum material
R-Value
in
accordance with
Table 3.12.5.1
.
Table 3.12.5.1 CENTRAL HEATING WATER PIPING—MINIMUM
MATERIAL R-VALUE
to be insulated
Minimum material
R-Value
for
each Climate Zone
1, 2, 3
and 5
4, 6 and 7
8
1.
Internal
6 http://abcb.gov.au/ncc-online/NCC/2016-A1/NCC-2016-Volume-Two/New-South-
Wales/Nsw-Part-3125-Services
7All details statements are from http://abcb.gov.au/ncc-online/NCC/2016-A1/NCC-2016-Volume-Two/Part-312-
Energy-Efficiency/Part-3125-Services
23
/ 47
Downloaded by Bob Young (bobby319163@gmail.com)
lOMoARcPSD|27337005
Your preview ends here
Eager to read complete document? Join bartleby learn and gain access to the full version
- Access to all documents
- Unlimited textbook solutions
- 24/7 expert homework help
1. All flow and return that is—
1.
within an
unventilated wall
space; or
2.
within an internal
floor between
storeys; or
3.
between ceiling
insulation and a
ceiling.
2. All heated water encased
within a concrete floor slab
(except that which is part of a
floor heating system).
0.4
0.4
0.4
2.
located within a ventilated wall space, an enclosed building
subfloor or a roof space
1. All flow and return
Open link in
same page
piping
.
2. Cold water supply
Open link in
same page
piping
— within
500 mm of the connection to
the central water heating
system.
3. Relief valve
Open link in same
page
piping
— within 500 mm
of the connection to the
central water heating system.
0.6
0.9
1.3
3.
located outside the building or in an unenclosed building
subfloor or roof space
1. All flow and return
2. Cold water supply — within
500 mm of the connection to
the central water heating
system.
3. Relief valve — within 500 mm
of the connection to the
0.6
1.3
1.3
24
/ 47
Downloaded by Bob Young (bobby319163@gmail.com)
lOMoARcPSD|27337005
Your preview ends here
Eager to read complete document? Join bartleby learn and gain access to the full version
- Access to all documents
- Unlimited textbook solutions
- 24/7 expert homework help
central water heating system.
Heating
and
Cooling
Ductwork
BCA,
Volume
2,
Section
3.12.5.3
3.12.5.3 Heating and cooling ductwork
(a)
Heating and cooling ductwork and fittings must—
(i)
achieve the material
R-Value
in
Table 3.12.5.2
; and
(ii)
be sealed against air loss—
(A)
by closing all openings in the surface, joints and seams of
ductwork with adhesives, mastics, sealants or gaskets in
accordance with AS 4254 Parts 1 and 2 for a Class C seal; or
(B)
for flexible ductwork, with a draw band in conjunction with a
sealant or adhesive tape.
(b)
Duct insulation must—
(i)
abut adjoining duct insulation to form a continuous barrier; and
(ii)
be installed so that it maintains its position and thickness, other
than at flanges and supports; and
(iii)
where located outside the building, under a suspended floor, in
an attached Class 10a building or in a roof space—
(A)
be protected by an outer sleeve of protective sheeting to
prevent the insulation becoming damp; and
(B)
have the outer protective sleeve sealed with adhesive tape not
less than 48 mm wide creating an airtight and waterproof seal.
(c)
The requirements of
(a)
do not apply to heating and cooling
ductwork and fittings located within the insulated
building
envelope
including a service riser within
the
conditioned space
, internal floors between storeys and the
25
/ 47
Downloaded by Bob Young (bobby319163@gmail.com)
lOMoARcPSD|27337005
Your preview ends here
Eager to read complete document? Join bartleby learn and gain access to the full version
- Access to all documents
- Unlimited textbook solutions
- 24/7 expert homework help
like.
Table 3.12.5.2 HEATING AND COOLING DUCTWORK AND
FITTINGS—MINIMUM MATERIAL R-VALUE
Ductwork
element
Minimum material R-Value
for ductwork and
fittings in each climate zone
Heating-only system or
cooling-only system
including an evaporative
cooling system
Combined heating and
refrigerated cooling
system
1, 2, 3, 4, 5, 6 and 7
8
1, 2, 3, 4,
5, 6 and 7
2 and
5
8
Ductwork
1.0
1.5
1.5 (see
note)
1.0
1.5
Fittings
0.4
Note:
The minimum material R-Value
Open link in same page
required
for ductwork may be reduced by 0.5 for combined heating and refrigerated cooling systems in climate zones
1, 3, 4, 6, and 7 if the ducts are—
1. under a suspended floor with an enclosed perimeter; or
2. in a roof space that has insulation of not less than R0.5 directly
beneath the roofing.
Artificial
lighting
BCA,
Volume
2,
Section
3.12.5.5
3.12.5.5 Artificial lighting
(a)
The
lamp power density
or
illumination power density
of artificial
lighting, excluding heaters that emit light, must not exceed the
allowance of—
(i)
5 W/m
2
in a Class 1 building; and
(ii)
4 W/m
2
on a verandah, balcony or the like attached to a Class 1
building; and
(iii)
3 W/m
2
in a Class 10a building associated with a Class 1 building.
(b)
The
illumination power density
allowance in
(a)
may be increased
by dividing it by the
illumination power density
adjustment factor for a
control device in
Table 3.12.5.3
as applicable.
(c)
When designing the
lamp power density
or
illumination power density
, the power of the proposed installation must be used rather
than nominal allowances for exposed batten holders or luminaires.
26
/ 47
Downloaded by Bob Young (bobby319163@gmail.com)
lOMoARcPSD|27337005
Your preview ends here
Eager to read complete document? Join bartleby learn and gain access to the full version
- Access to all documents
- Unlimited textbook solutions
- 24/7 expert homework help
(d)
Halogen lamps must be separately switched from fluorescent
lamps.
(e)
Artificial lighting around the perimeter of a building must—
(i)
be controlled by a daylight sensor; or
(ii)
have an average light source efficacy of not less than
40 Lumens/W.
Table 3.12.5.3 ILLUMINATION POWER DENSITY ADJUSTMENT
FACTOR FOR A CONTROL DEVICE
Item
Description
Illumination
power
density
adjustment
factor
Lighting timer
For corridor lighting
0.7
Motion detector
1. Where—
1.
at least 75% of the area of
a space is controlled by one or more motion detectors; or
2.
an area of less than 200 m
2
is switched as a
block by one or more detectors.
0.9
2. Where up to 6 lights are switched as a block by one or more detectors.
0.7
3. Where up to 2 lights are switched as a block by one or more detectors.
0.55
Manual dimming system Note 1
Where not less than 75% of the area of a space is controlled by manually operated dimmers.
0.85
Programmable dimming Where not less than 75% of the area of a space is controlled by 0.85
27
/ 47
Downloaded by Bob Young (bobby319163@gmail.com)
lOMoARcPSD|27337005
Your preview ends here
Eager to read complete document? Join bartleby learn and gain access to the full version
- Access to all documents
- Unlimited textbook solutions
- 24/7 expert homework help
system Note 2
programmable dimmers.
Dynamic dimming
system Note 3
Automatic compensation for lumen depreciation.
The design lumen depreciation factor of not less than—
1. for fluorescent lights, 0.9; or
2. for high pressure discharge lights, 0.8.
Fixed dimming Note 4
Where at least 75% of the area is controlled by fixed dimmers that reduce the overall lighting level and the power consumption of the lighting.
% of full power to which the dimmer is
set divided by 0.95.
Daylight sensor and dynamic lighting control device – dimmed or stepped switching of lights
adjacent window
s
1. Lights within the space adjacent to page
windows
other than
roof lights
for a distance from the
window
equal to the depth of the floor to
window
head height.
0.5 Note 5
2. Lights within the space adjacent to
roof lights
.
0.6 Note 5
Notes:
1. Manual dimming is where lights are controlled by a knob, slider
or other mechanism or where there are pre-selected scenes that are manually selected.
2. Programmed dimming is where pre-selected scenes or levels are automatically selected by the time of day, photoelectric cell or occupancy sensor.
3. Dynamic dimming is where the lighting level is varied automatically by a photoelectric cell to either proportionally compensate for the availability of daylight or the lumen depreciation of the lamps.
4. Fixed dimming is where lights are controlled to a level and that level cannot be adjusted by the user.
28
/ 47
Downloaded by Bob Young (bobby319163@gmail.com)
lOMoARcPSD|27337005
Your preview ends here
Eager to read complete document? Join bartleby learn and gain access to the full version
- Access to all documents
- Unlimited textbook solutions
- 24/7 expert homework help
5. The illumination power density
adjustment factor is only applied to lights controlled by that item. This adjustment factor
does not apply to tungsten halogen or other incandescent sources.
Electric
BCA,
Volume
2,
Section
3.12.5.4
3.12.5.4 Electric resistance space heating
An electric resistance space heating system that serves more than
one room must have—
(a)
separate isolating switches for each room; and
(b)
a separate temperature controller and time switch for each group of
rooms with common heating needs; and
(c)
power loads of not more than 110 W/m
2
for living areas, and
150 W/m
2
for bathrooms.
Question 6 (35 marks)
(refer to Project 1)
Prepare a checklist to ensure the quality of each of the following systems to the building:
footing Timber floor
Concrete Floor
Timber frame walls
Masonry walls
Truss roof
Framed Roof
Checklist
Australian Standard reference list
29
/ 47
Downloaded by Bob Young (bobby319163@gmail.com)
lOMoARcPSD|27337005
Your preview ends here
Eager to read complete document? Join bartleby learn and gain access to the full version
- Access to all documents
- Unlimited textbook solutions
- 24/7 expert homework help
*The Above table is from the following link: http://www.fairtrading.nsw.gov.au/biz_res/ftweb/pdfs/Tenants_and_home_owners/NSW_Guid
e_to_Standards_and_Tolerances.pdf
Check list
1.
Footing System
30
/ 47
Downloaded by Bob Young (bobby319163@gmail.com)
lOMoARcPSD|27337005
Your preview ends here
Eager to read complete document? Join bartleby learn and gain access to the full version
- Access to all documents
- Unlimited textbook solutions
- 24/7 expert homework help
Customer: Mr & Mrs Education
Contract Number:0412 123456
Contract/Project Name: House
INSPECTION AND TEST PLAN for: REINFORCED CONCRETE
Work area: 14 Hemming street, Perith, NSW
R
e
f
Operation or stage of work
Stag
e/ freq
uen
cy
Rec
ords
Requir
ement/
standa
rd/ specif
cation
Accep
tance
criter
ia
Inspe
ction/
test proce
dure
Inspection *what/who
Descripti
on
Charact
eristics
Empl
oyee
Serv
ice prov
ider
Cust
omer
1
Prelimin
ary activities
(requirin
g Principal
’s notifcati
on)
Notifca
tion provide
d
Pres
tart conc
rete
wor
k
Che
cklis
t
House Specif
cation
All tasks comp
leted
2
Prelimin
ary activities
(requirin
g Contract
or’s acceptan
ce)
Approv
als require
d obtaine
d
Pres
tart conc
rete
wor
k
Che
cklis
t
House Specif
cation
All tasks comp
leted
3
Order concrete
To specifc
ation
Eac
h pou
r
Cop
y of orde
r
House Specif
cation WHS practic
e & Regula
tion AS287
0, BCA Volum
e 1, B1.4
Refe
cts spec./
safe, secur
e
4
Pre pour
inspectio
n
Task complet
ion
Eac
h pou
r
Che
cklis
t
House Specif
cation/
drawin
gs, AS287
0 BCA Volum
e 1, B1.4
Right levels
& dime
nsion
s/ clean/
safe
31
/ 47
Downloaded by Bob Young (bobby319163@gmail.com)
lOMoARcPSD|27337005
Your preview ends here
Eager to read complete document? Join bartleby learn and gain access to the full version
- Access to all documents
- Unlimited textbook solutions
- 24/7 expert homework help
5
Slump test
Workabi
lity of mix
Eac
h deli
very
Atta
che
d reco
rd
House Specif
cation AS287
0 BCA Volum
e 1, B1.4
50 to 100 mm
6
Concrete
test cylinder
Concret
e strengt
h
2 per pou
r
Test
lab certi
f.
House Specif
cation
AS287
0 BCA Volum
e 1, B1.4
30 Mpa mini
mum
7
Concrete
pour
To specifc
ation
Eac
h pou
r
Che
cklis
t
House Specif
cation AS287
0 BCA Volum
e 1, B1.4
Corre
ct place
ment
8
Strippin
g & curing
To specifc
ation
Eac
h pou
r
Che
cklis
t
House Specif
cation AS287
0 BCA Volum
e 1, B1.4
Finis
h/ curin
g/ maint
ained
9
Pre-
handove
r activities
All matters
fnalise
d, clean
and tidy
Eac
h pou
r
Che
cklis
t
House Specif
cation AS287
0 BCA Volum
e 1, B1.4
Comp
leted to spec./
clean and tidy
*W = Witness Point; H = Hold Point; H(A) = Inspection/Test by Authority; U(C) = Inspection/Test by Consultant; S = Surveillance or monitoring; X = Self inspection by performer of work.
32
/ 47
Downloaded by Bob Young (bobby319163@gmail.com)
lOMoARcPSD|27337005
Your preview ends here
Eager to read complete document? Join bartleby learn and gain access to the full version
- Access to all documents
- Unlimited textbook solutions
- 24/7 expert homework help
2.
Concrete foor
INSPECTION AND TEST PLAN CHECKLIST for: CONCRETE FLOOR
(To be completed by the person(s) directly responsible for the work)
Contract Number:
Contract/Project Name:
Contractor:
Subcontractor
Work area:14 Hemming street, Perith, NSW
Work
Items/activities to be verifed
Referenc
e
Initiall
ed/OK
Comments
Prelimin
ary activities
(requirin
g Principal
’s notifcati
on)
Structural design check
House Specifcat
ion
AS3600
Concrete supplier/ form worker
House Specifcat
ion
AS3600
Admixtures House Specifcat
ion
AS3600
Formwork design
House Specifcat
ion
AS3600
I have carried out all necessary inspections and verify that the above items/activities conform to the contract specifcation/documents
Name:
Signature:
Date:
Prelimin
ary activities
(requirin
g Contract
or’s acceptan
ce)
Access obtained
House Specifcat
ion
AS3600
Signage/barricades/fa
lsework
House Specifcat
ion
AS3600
Reinforcing scheduled
and ordered
House Specifcat
ion
AS3600
Testing and sampling equipment
House Specifcat
ion
AS3600
Instruction to Subcontractors on ITP
requirements
House Specifcat
ion
AS3600
33
/ 47
Downloaded by Bob Young (bobby319163@gmail.com)
lOMoARcPSD|27337005
Your preview ends here
Eager to read complete document? Join bartleby learn and gain access to the full version
- Access to all documents
- Unlimited textbook solutions
- 24/7 expert homework help
I have carried out all necessary inspections and verify that the above items/activities conform to the contract specifcation/documents
Name:
Signature:
Date:
Order concrete
Strength
House Specifcat
ion
AS3600
Slump
House Specifcat
ion
AS3600
Water/cement ratio
House Specifcat
ion
AS3600
Type of cement
House Specifcat
ion
AS3600
Admixture
House Specifcat
ion
AS3600
Delivery notice and arrangements
House Specifcat
ion
AS3600
I have carried out all necessary inspections and verify that the above items/activities conform to the contract specifcation/documents
Name:
Signature:
Date:
Pre pour
inspectio
n
Formwork checked (dimensions, levels and capacity)
House Specifcat
ion
AS3600
Formwork design certifed
House Specifcat
ion
AS3600
Foundation (clean, scabbled, starter bars
etc)
House Specifcat
ion
AS3600
Cover to reo. Laps as specifed
House Specifcat
ion
AS3600
Termite treatment
House Specifcat
ion
AS3600
34
/ 47
Downloaded by Bob Young (bobby319163@gmail.com)
lOMoARcPSD|27337005
Your preview ends here
Eager to read complete document? Join bartleby learn and gain access to the full version
- Access to all documents
- Unlimited textbook solutions
- 24/7 expert homework help
Membranes
House Specifcat
ion
AS3600
Blockouts
House Specifcat
ion
AS3600
Expansion strips/water stop
House Specifcat
ion
AS3600
I have carried out all necessary inspections and verify that the above items/activities conform to the contract specifcation/documents
Name:
Signature:
Date:
Concrete
pour
Slump test taken/ results recorded
House Specifcat
ion
AS3600
Concrete test cylinders taken and marked
House Specifcat
ion
AS3600
Time for delivery
House Specifcat
ion
AS3600
Time for pour
House Specifcat
ion
AS3600
Pouring techniques conform (height, vibration, tremmying,
pumping)
House Specifcat
ion
AS3600
I have carried out all necessary inspections and verify that the above items/activities conform to the contract specifcation/documents
Name:
Signature:
Date:
Strippin
g & curing
When stripped
House Specifcat
ion
AS3600
Repairs
House Specifcat
ion
AS3600
Curing method
House Specifcat
ion
AS3600
35
/ 47
Downloaded by Bob Young (bobby319163@gmail.com)
lOMoARcPSD|27337005
Your preview ends here
Eager to read complete document? Join bartleby learn and gain access to the full version
- Access to all documents
- Unlimited textbook solutions
- 24/7 expert homework help
Curing maintained ………….. days
House Specifcat
ion
AS3600
I have carried out all necessary inspections and verify that the above items/activities conform to the contract specifcation/documents
Name:
Signature:
Date:
Pre-
handove
r activities
Finish
House Specifcat
ion
AS3600
Levels/ dimensions
House Specifcat
ion
AS3600
Equipment cleaned and site clean
House Specifcat
ion
AS3600
Test results for concrete cylinders
House Specifcat
ion
AS3600
I have carried out all necessary inspections and verify that the above items/activities conform to the contract specifcation/documents
Name:
Signature:
Date:
I have carried out all necessary inspections and verify that the above work for this work area has been completed and conforms to the contract specifcation/documents
Name:
Signature:
Date:
3.
Timber Floor
INSPECTION AND TEST PLAN CHECKLIST for: CONCRETE FLOOR
(To be completed by the person(s) directly responsible for the work)
Contract Number:
Contract/Project Name:
Contractor:
Subcontractor
Work area:14 Hemming street, Perith, NSW
Work
Items/activities to be verifed
Referenc
e
Initiall
ed/OK
Comments
Timber foor installati
on
Start with a dry ventilated subfoor space. House Specifcat
ion
AS4786.2
36
/ 47
Downloaded by Bob Young (bobby319163@gmail.com)
lOMoARcPSD|27337005
Your preview ends here
Eager to read complete document? Join bartleby learn and gain access to the full version
- Access to all documents
- Unlimited textbook solutions
- 24/7 expert homework help
Builder’s plastic on ground
House Specifcat
ion
AS4786.2
Sheet subfoor glued and nailed ( if needed screwed to joists)
House Specifcat
ion
AS4786.2
Subfoor fat, dry and clean, sanded
House Specifcat
ion
AS4786.2
Boards including wider boards are glued and nailed through subfoor to joists.
House Specifcat
ion
AS4786.2
Boards from some manufacturers up to 135mm wide can be secret nailed
House Specifcat
ion
AS4786.2
Sanded and fnished in-
situ.
House Specifcat
ion
AS4786.2
I have carried out all necessary inspections and verify that the above items/activities conform to the contract specifcation/documents
Name:
Signature:
Date:
4.
Timber Frame Wall
INSPECTION AND TEST PLAN CHECKLIST for: CONCRETE FLOOR
(To be completed by the person(s) directly responsible for the work)
Contract Number:
Contract/Project Name:
Contractor:
Subcontractor
Work area:14 Hemming street, Perith, NSW
Work
Items/activities to be verifed
Reference
Initiall
ed/OK
Comments
Timber Frame Wall construc
tion
Subsidence
House Specifcatio
n
AS1684, Part 2&3, AS1720.1, BCA Volume 1, B1.4.2
37
/ 47
Downloaded by Bob Young (bobby319163@gmail.com)
lOMoARcPSD|27337005
Your preview ends here
Eager to read complete document? Join bartleby learn and gain access to the full version
- Access to all documents
- Unlimited textbook solutions
- 24/7 expert homework help
Check that all framing is straight and plumb
House Specifcatio
n
AS1684, Part 2&3 AS1720.1, BCA Volume 1, B1.4.2
Wall frame member spacings are adequate with blocking & nogging installed
for wall and ceiling linings.
House Specifcatio
n
AS1684, Part 2&3 AS1720.1, BCA Volume 1, B1.4.2
The connection of frame members.
House Specifcatio
n
AS1684, Part 2&3 AS1720.1, BCA Volume 1, B1.4.2
Location of under-slab services - visual check that service penetrations through the foor are in appropriate rooms. Building services to wall and ceiling frames installed using new materials, in good condition.
House Specifcatio
n
AS1684, Part 2&3 AS1720.1, BCA Volume 1, B1.4.2
Roof truss/frame is installed, tied down & braced
House Specifcatio
n
AS1684, Part 2&3 AS1720.1, BCA Volume 1, B1.4.2
Structural steel members such as columns, beams and
lintels checked for support and fxings
House Specifcatio
n
AS1684, Part 2&3 AS1720.1, BCA Volume 1, B1.4.2
38
/ 47
Downloaded by Bob Young (bobby319163@gmail.com)
lOMoARcPSD|27337005
Your preview ends here
Eager to read complete document? Join bartleby learn and gain access to the full version
- Access to all documents
- Unlimited textbook solutions
- 24/7 expert homework help
Window and door openings
House Specifcatio
n
AS1684, Part 2&3 AS1720.1, BCA Volume 1, B1.4.2
Check for the installation of a perimeter termite barrier
House Specifcatio
n
AS1684, Part 2&3 AS1720.1, BCA Volume 1, B1.4.2
Wall frames secured to top/bottom plate.
House Specifcatio
n
AS1684, Part 2&3 AS1720.1, BCA Volume 1, B1.4.2
I have carried out all necessary inspections and verify that the above items/activities conform to the contract specifcation/documents
Name:
Signature:
Date:
5.
Masonry Wall
INSPECTION AND TEST PLAN CHECKLIST for: Masonry Wall
(To be completed by the person(s) directly responsible for the work)
Contract Number:
Contract/Project Name:
Contractor:
Subcontractor
Work area:14 Hemming street, Perith, NSW
Work
Items/activities to be verifed
Referenc
e
Initiall
ed/OK
Comments
Masonry wall installati
on
Well-designed temporary support
House Specifcat
ion
AS1170, AS3700, AS4455, BCA Volume 1,
B1.4(a)
39
/ 47
Downloaded by Bob Young (bobby319163@gmail.com)
lOMoARcPSD|27337005
Your preview ends here
Eager to read complete document? Join bartleby learn and gain access to the full version
- Access to all documents
- Unlimited textbook solutions
- 24/7 expert homework help
Temporary support has been inspected and removed according to project requirements
House Specifcat
ion
AS1170, AS3700, AS4455, BCA Volume 1,
B1.4(a)
Choose proper control joints, lintels, damp proof course, bond type
and opening to ensure the wall strength
House Specifcat
ion
AS1170, AS3700, AS4455, BCA Volume 1,
B1.4(a)
The wall was constructed through a proposed sequence
House Specifcat
ion
AS1170, AS3700, AS4455, BCA Volume 1,
B1.4(a)
No Leaning materials against walls
House Specifcat
ion
AS1170, AS3700, AS4455, BCA Volume 1,
B1.4(a)
Not backflling behind masonry retaining walls
until they are permanently supported
House Specifcat
ion
AS1170, AS3700, AS4455, BCA Volume 1,
B1.4(a)
The structural adequacy
of the foundations is good
House Specifcat
ion
AS1170, AS3700, AS4455, BCA Volume 1,
B1.4(a)
40
/ 47
Downloaded by Bob Young (bobby319163@gmail.com)
lOMoARcPSD|27337005
Your preview ends here
Eager to read complete document? Join bartleby learn and gain access to the full version
- Access to all documents
- Unlimited textbook solutions
- 24/7 expert homework help
Storing materials away from unsupported masonry walls
House Specifcat
ion
AS1170, AS3700, AS4455, BCA Volume 1,
B1.4(a)
Preventing the collapse of excavation behind masonry retaining walls
House Specifcat
ion
AS1170, AS3700, AS4455, BCA Volume 1,
B1.4(a)
Stopping work if the existing top course is afected by rain to the point where the mortar bond strength will be impaired
House Specifcat
ion
AS1170, AS3700, AS4455, BCA Volume 1,
B1.4(a)
Preventing inadvertent impact on walls by plant such as wheelbarrows, cranes or pallet trolleys
House Specifcat
ion
AS1170, AS3700, AS4455, BCA Volume 1,
B1.4(a)
Establishing stop heights to allow mortar to gain adequate strength before further construction
House Specifcat
ion
AS1170, AS3700, AS4455, BCA Volume 1,
B1.4(a)
I have carried out all necessary inspections and verify that the above items/activities conform to the contract specifcation/documents
Name:
Signature:
Date:
6.
Truss Roof
INSPECTION AND TEST PLAN CHECKLIST for: Truss Roof
(To be completed by the person(s) directly responsible for the work)
Contract Number:
Work area:14 Hemming street, Perith, 41
/ 47
Downloaded by Bob Young (bobby319163@gmail.com)
lOMoARcPSD|27337005
Your preview ends here
Eager to read complete document? Join bartleby learn and gain access to the full version
- Access to all documents
- Unlimited textbook solutions
- 24/7 expert homework help
Contract/Project Name:
Contractor:
Subcontractor
NSW
Work
Items/activities to be verifed
Reference
Initiall
ed/OK
Comments
Truss Roof Installati
on
All materials are loading in the proper place
House Specifcatio
n
AS4400
Truss has been installed straight and plumb
Truss are in-plane and all in line vertically
Truss are erected with minimal bow, not exceeding
the lesser of length/200 and 50mm
Truss has been installed in the correct position
I have carried out all necessary inspections and verify that the above items/activities conform to the contract specifcation/documents
Name:
Signature:
Date:
7.
Framed Roof
INSPECTION AND TEST PLAN CHECKLIST for: Framed Roof
(To be completed by the person(s) directly responsible for the work)
Contract Number:
Contract/Project Name:
Contractor:
Subcontractor
Work area:14 Hemming street, Perith, NSW
Work
Items/activities to be verifed
Reference
Initiall
ed/OK
Comments
Framed Roof Installati
on
Truss has been unload in a proper handling place and are in good condition
House Specifcatio
n, AS1684.2
All framing is straight and plumb
House Specifcatio
n, AS1684.2
Roof frame member spacing s are adequate with blocking &nogging installed for roof and ceiling linings
House Specifcatio
n, AS1684.2
42
/ 47
Downloaded by Bob Young (bobby319163@gmail.com)
lOMoARcPSD|27337005
Your preview ends here
Eager to read complete document? Join bartleby learn and gain access to the full version
- Access to all documents
- Unlimited textbook solutions
- 24/7 expert homework help
Roof frame is tied down and braced
House Specifcatio
n, AS1684.2
Installation of a perimeter termite barrier
House Specifcatio
n, AS1684.2
I have carried out all necessary inspections and verify that the above items/activities conform to the contract specifcation/documents
Name:
Signature:
Date:
1.
MATERIAL
Flashings comply with AS 2904 Metal finishes to comply with AS 1789 (zinc plating), AS/NZS 1866 (aluminium
extrusions) Anodising complies with AS 1231 Thermoset powder coating AS 3715 Glass Selection and installation complies with AS 1288 Types and quality complies with AS/NZS 4667 Safety glazing complies with AS/NZS 2208 Doors comply with AS 2688, AS 2689, AS 1909 Windows selection complies with AS 2047 Preglazing: bushfire screens comply with BCA table SA 3.7.4.1 and AS 3959 Lockset and hardware complies with AS 4145 DOORS AND WINDOWS
Flashing and weatherings in place to avoid water penetration All doorsets and windows installed plumb, level, straight and true Doorsets and windows adequately fixed or anchored to building structure STEEL DOOR FRAMES
Correct frames and necessary accessories used All welds ground smooth and welded joints galvanised prior to priming Ensure all frames are in masonry, and packed behind fixing points TIMBER DOORS Ensure correct door type is used ( NT designated or other) All areas subject to paint removal, primed prior to hanging HINGES Number of hinges is as specified DOOR FURNITURE Door stops installed Door seals secured to external doors and adjusted correctly Correct hinges to suit door as specified 43
/ 47
Downloaded by Bob Young (bobby319163@gmail.com)
lOMoARcPSD|27337005
Your preview ends here
Eager to read complete document? Join bartleby learn and gain access to the full version
- Access to all documents
- Unlimited textbook solutions
- 24/7 expert homework help
SLIDING INTERNAL DOORS All accessories including wheel carriages are appropriate to the size and mass of
door SECURITY SCREEN DOORS AND GRILLES Infill mesh secured to extruded aluminium frames Hinges and pneumatic closer functioning correctly Comply with AS 5039 and AS 5040 Method of tests comply with 5041 ROLLER SHUTTERS Manual operation – fixings and operation handle functioning Motorised operation – Operating switch secure and functioning Comply with AS 1170.2 for wind action resistance LOCKSETS Mounting height correct Ensure all passage, privacy and key-lockable sets are functioning correctly 2 keys provided for each lockset Comply with AS 4145 series WINDOWS Assemblies comply with AS/NZS 1170.1, AS/NZS 1170.2, AS 4055, AS 1288 and AS
2047 GLAZING Glass thickness to AS/NZS 2208 Glass type is as specified Safety mirrors to AS/NZS 2208 CONSTRUCTION All fixings not visible on exposed side Aluminium screen mesh tightly strung and fasten with plastic continuous spline
material Security screens and grilles to AS 5039 Security screens and grilles installation to AS 5040 Debris screen to AS 1170.2 2.
MATERIALS AND COMPONENTS Flashing material as specified; complies with AS/NZS 2904 Sarking material as specified; complies with AS 4200.1 Steel nails comply with AS/NZS 4680 (hot dipped galvanised) and AS 3566 (self-
drilling screws) All materials free from corrosion CLADDING Materials used are specified Comply with AS 4256.4 (Unplasticised polyvinyl chloride) 44
/ 47
Downloaded by Bob Young (bobby319163@gmail.com)
lOMoARcPSD|27337005
Your preview ends here
Eager to read complete document? Join bartleby learn and gain access to the full version
- Access to all documents
- Unlimited textbook solutions
- 24/7 expert homework help
Comply with AS 4256.3 (Glass fibre reinforce polyester) Comply with AS 4256.5 (polycarbonate) Plastic cladding installation complies with AS 1562.3 Comply with AS/NZS 2908.2 (Fibre cement cladding) Comply with AS/NZS 2908.2 Type A, category 5 (Compressed fibre cement
cladding) Design and installation comply with AS 1562.1 (Sheet metal cladding) LINING Plasterboard to AS/NZS 2588 Fibre cement to AS/NZS 2908.2, Type B, Category 2, minimum thickness 4.5mm
PLASTERBOARD Installation as specified Framed construction screw or nail or combine with adhesive Masonry construction adhesive fix Flush jointing materials correct Control joints in position CLADDING AND LINING FIBRE CEMENT SHEET LINING Correct screws used Control Joints as specified V joints as specified TONGUE AND GROOVE LINING All boards fixed with a continuous grain pattern Visible nail heads treated as specified PLASTIC LAMINATE Joins sealed 3.
MATERIALS AND COMPONENTS GP cement complies with AS 3972 Lime putty mixes mixed minimum 16 hours before use; complies with AS 1672.1 Gypsum plaster is as specified Gauged mixes is as specified SUBSTRATE Defects in substrate repaired Substrate requires second coat Loose material and dust removed from substrate Embedded items sheathed Metal laths fixed as specified PLASTERING Number of coats and thickness is as specified Curing even and within required timeframe V joints installed as specified 45
/ 47
Downloaded by Bob Young (bobby319163@gmail.com)
lOMoARcPSD|27337005
Your preview ends here
Eager to read complete document? Join bartleby learn and gain access to the full version
- Access to all documents
- Unlimited textbook solutions
- 24/7 expert homework help
Movement joints installed as specified Correct finish as specified or as shown on drawing
4.
MATERIALS AND COMPONENTS All materials are as specified Moisture content checked Timber finished to required dimensions Plywood complies with AS/NZS 2270 and AS/NZS 2271 Particleboard complies with AS/NZS 1859.1 Moisture resistant medium density fibreboard complies with AS/NZS 1859.2 Wet processed fibreboard complies with AS/NZS 1859.4 Decorative overlaid wood panels complies with AS 1859.3 High pressure decorative laminated sheet complies with AS/NZS 2924.1
CONSTRUCTION Components manufactured square and installed plumb Fasteners and adhesives used correctly No visible fixings except where specified CUPBOARD AND DRAWER UNITS Plinth material and installation as specified Carcasses, drawer fronts, shelves and doors material and installation as specified Door hinges as specified Self closing action and hold open function operating as specified Drawer units operating smooth and true. BENCHTOPS Materials are as specified CEILING ACCESS Access panel provided as specified
TIMBER ROOF TRUSSES Trusses marked as specified Certification provided Support trusses installed Ties and wind bracing provided Nail plated prefabricated roof trusses complies to AS 4440 Support for water containers complies to AS/NZS 3500.4 CONCRETE Correct concrete grade used as specified Grout is as specified Concrete placing is as specified Concrete protected from premature drying Pre-mixed supply of concrete complies to AS 1379 46
/ 47
Downloaded by Bob Young (bobby319163@gmail.com)
lOMoARcPSD|27337005
Your preview ends here
Eager to read complete document? Join bartleby learn and gain access to the full version
- Access to all documents
- Unlimited textbook solutions
- 24/7 expert homework help
Grout for blockwork cores complies with AS 3700, grout clause REINFORCED MASONRY Cleaning holes provided Bond beam installed as specified Starter bars secure Lintel blocks installed as specified Core filling grout is as specified Core holes Bond beams Lintels
Presentation (5 Marks)
Refer to rules of presentation on the OLS. Please submit your assessment as one
document. 47
/ 47
Downloaded by Bob Young (bobby319163@gmail.com)
lOMoARcPSD|27337005
Your preview ends here
Eager to read complete document? Join bartleby learn and gain access to the full version
- Access to all documents
- Unlimited textbook solutions
- 24/7 expert homework help
Recommended textbooks for you
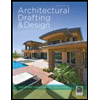
Architectural Drafting and Design (MindTap Course...
Civil Engineering
ISBN:9781285165738
Author:Alan Jefferis, David A. Madsen, David P. Madsen
Publisher:Cengage Learning
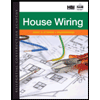
Residential Construction Academy: House Wiring (M...
Civil Engineering
ISBN:9781285852225
Author:Gregory W Fletcher
Publisher:Cengage Learning
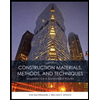
Construction Materials, Methods and Techniques (M...
Civil Engineering
ISBN:9781305086272
Author:William P. Spence, Eva Kultermann
Publisher:Cengage Learning
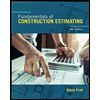
Fundamentals Of Construction Estimating
Civil Engineering
ISBN:9781337399395
Author:Pratt, David J.
Publisher:Cengage,
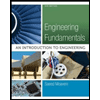
Engineering Fundamentals: An Introduction to Engi...
Civil Engineering
ISBN:9781305084766
Author:Saeed Moaveni
Publisher:Cengage Learning
Recommended textbooks for you
- Architectural Drafting and Design (MindTap Course...Civil EngineeringISBN:9781285165738Author:Alan Jefferis, David A. Madsen, David P. MadsenPublisher:Cengage LearningResidential Construction Academy: House Wiring (M...Civil EngineeringISBN:9781285852225Author:Gregory W FletcherPublisher:Cengage LearningConstruction Materials, Methods and Techniques (M...Civil EngineeringISBN:9781305086272Author:William P. Spence, Eva KultermannPublisher:Cengage Learning
- Fundamentals Of Construction EstimatingCivil EngineeringISBN:9781337399395Author:Pratt, David J.Publisher:Cengage,Engineering Fundamentals: An Introduction to Engi...Civil EngineeringISBN:9781305084766Author:Saeed MoaveniPublisher:Cengage Learning
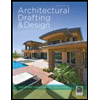
Architectural Drafting and Design (MindTap Course...
Civil Engineering
ISBN:9781285165738
Author:Alan Jefferis, David A. Madsen, David P. Madsen
Publisher:Cengage Learning
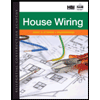
Residential Construction Academy: House Wiring (M...
Civil Engineering
ISBN:9781285852225
Author:Gregory W Fletcher
Publisher:Cengage Learning
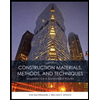
Construction Materials, Methods and Techniques (M...
Civil Engineering
ISBN:9781305086272
Author:William P. Spence, Eva Kultermann
Publisher:Cengage Learning
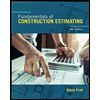
Fundamentals Of Construction Estimating
Civil Engineering
ISBN:9781337399395
Author:Pratt, David J.
Publisher:Cengage,
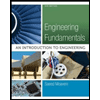
Engineering Fundamentals: An Introduction to Engi...
Civil Engineering
ISBN:9781305084766
Author:Saeed Moaveni
Publisher:Cengage Learning