CVE 312_Case Study
docx
keyboard_arrow_up
School
Cleveland State University *
*We aren’t endorsed by this school
Course
312
Subject
Civil Engineering
Date
Dec 6, 2023
Type
docx
Pages
10
Uploaded by HighnessWillpower5296
Your preview ends here
Eager to read complete document? Join bartleby learn and gain access to the full version
- Access to all documents
- Unlimited textbook solutions
- 24/7 expert homework help
Your preview ends here
Eager to read complete document? Join bartleby learn and gain access to the full version
- Access to all documents
- Unlimited textbook solutions
- 24/7 expert homework help
Your preview ends here
Eager to read complete document? Join bartleby learn and gain access to the full version
- Access to all documents
- Unlimited textbook solutions
- 24/7 expert homework help
Recommended textbooks for you
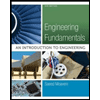
Engineering Fundamentals: An Introduction to Engi...
Civil Engineering
ISBN:9781305084766
Author:Saeed Moaveni
Publisher:Cengage Learning
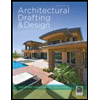
Architectural Drafting and Design (MindTap Course...
Civil Engineering
ISBN:9781285165738
Author:Alan Jefferis, David A. Madsen, David P. Madsen
Publisher:Cengage Learning
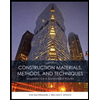
Construction Materials, Methods and Techniques (M...
Civil Engineering
ISBN:9781305086272
Author:William P. Spence, Eva Kultermann
Publisher:Cengage Learning
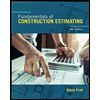
Fundamentals Of Construction Estimating
Civil Engineering
ISBN:9781337399395
Author:Pratt, David J.
Publisher:Cengage,
Recommended textbooks for you
- Engineering Fundamentals: An Introduction to Engi...Civil EngineeringISBN:9781305084766Author:Saeed MoaveniPublisher:Cengage LearningArchitectural Drafting and Design (MindTap Course...Civil EngineeringISBN:9781285165738Author:Alan Jefferis, David A. Madsen, David P. MadsenPublisher:Cengage LearningConstruction Materials, Methods and Techniques (M...Civil EngineeringISBN:9781305086272Author:William P. Spence, Eva KultermannPublisher:Cengage Learning
- Fundamentals Of Construction EstimatingCivil EngineeringISBN:9781337399395Author:Pratt, David J.Publisher:Cengage,
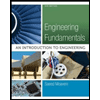
Engineering Fundamentals: An Introduction to Engi...
Civil Engineering
ISBN:9781305084766
Author:Saeed Moaveni
Publisher:Cengage Learning
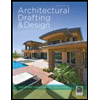
Architectural Drafting and Design (MindTap Course...
Civil Engineering
ISBN:9781285165738
Author:Alan Jefferis, David A. Madsen, David P. Madsen
Publisher:Cengage Learning
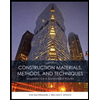
Construction Materials, Methods and Techniques (M...
Civil Engineering
ISBN:9781305086272
Author:William P. Spence, Eva Kultermann
Publisher:Cengage Learning
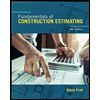
Fundamentals Of Construction Estimating
Civil Engineering
ISBN:9781337399395
Author:Pratt, David J.
Publisher:Cengage,