CHM243_Extraction
pdf
keyboard_arrow_up
School
University of Toronto, Mississauga *
*We aren’t endorsed by this school
Course
243
Subject
Chemistry
Date
Feb 20, 2024
Type
Pages
8
Uploaded by ColonelMorning8735
Experiment 3
Extraction
1
Introduction
This experiment aimed to separate the mixture of naphthalene-benzoic acid using the technique
of extraction. In order to yield pure compounds, this purification and separation process is
dependent on the properties of the substances such as their melting point and their solubility in a
specific solvent.
1
In this case, ethyl acetate possesses the ability to dissolve naphthalene and
benzoic acid, establishing its efficacy as a solvent in the experiment.
2
To add, the low boiling
point facilitates its removal from the mixture through evaporation, thereby enhancing the
purification process for isolating the compounds of interest. The addition of an immiscible
reagent, such as sodium hydroxide, assists in selectively partitioning the mixture into two distinct
layers, aqueous and organic, making the extraction process possible.
Figure 1.
Mechanism from the lab manual
1
showing the separation of benzoic acid and
naphthalene from the addition of insoluble sodium salt, forming the organic (naphthalene) and
aqueous (benzoic acid) layer.
Procedure
1.0g of naphthalene and 1.0g of benzoic acid were grinded together using a mortar and a pestle.
The mixture was dissolved in 20 mL of ethyl acetate and placed in a separatory funnel. A 10 mL
solution of cold 10% NaOH was added to the separatory funnel, shaken gently, and the cap was
removed to release pressure. Once a clear separation of layers forms, with the funnel uncapped,
the aqueous bottom layer was collected in a 100 mL beaker. Again, 10 mL of the NaOH solution
2
was introduced into the separatory funnel, gently shaken and the aqueous solution was collected
in the same 100 mL beaker. By pouring from the top of the separatory funnel, the remaining
organic layer was transferred in a 50 mL beaker.
10 mL of concentrated HCl was added dropwise to the aqueous layer until the benzoic acid
stopped precipitation. The mixture was filtered by suction using a Buchner funnel to collect the
benzoic acid. The product filtered was washed with 10 mL of ice-cold distilled water to dry. The
mass and melting point were recorded.
1.0g of anhydrous sodium sulfate was added to the organic layer extracted and the mixture was
left to stand for 5 minutes. An evaporating dish containing two boiling chips was weighed. The
solution was then filtered by gravity filtration into the evaporating dish to remove the sodium
sulfate salt. The beaker was rinsed with 3 mL of ethyl acetate and gravity filtered once again.
The evaporating dish was placed on a steam bath for 15 minutes which allowed the formation of
naphthalene crystals. The evaporating dish was weighed to determine the yield of the dried
product.
Your preview ends here
Eager to read complete document? Join bartleby learn and gain access to the full version
- Access to all documents
- Unlimited textbook solutions
- 24/7 expert homework help
3
Results
Table 1:
Melting point and % yield for the initial mixture and pure compounds.
Melting Point
% Yield (95%)
Initial mixture (naphthalene + benzoic acid)
56.2 - 107.7
℃
N/A
Pure benzoic acid
69.7 - 86.7
℃
100%
𝑎𝑐??𝑎𝑙 ?𝑒𝑖𝑔ℎ?
?ℎ𝑒𝑜𝑟𝑒?𝑖𝑐𝑎𝑙 ?𝑒𝑖𝑔ℎ?
×
100%
0.769 𝑔
1.000 𝑔 ? 95/100
×
= 80 %
Pure naphthalene
112.3 - 124.2
℃
100%
1.283 𝑔
1.000 𝑔 ? 95/100
×
= 1.35 %
Discussion
The extraction was successful, resulting in the formation of an aqueous layer (top) and an
organic layer (bottom) which contained benzoic acid and naphthalene components, respectively.
Further treatment and filtration of these liquids resulted in the production of white solids; 80%
yield of pure benzoic acid and 135% of naphthalene were recorded.
The melting point of a compound is presented in a range of values which helps to determine the
efficiency of the separation technique. The crude melting point of the benzoic acid and
naphthalene mixture was 56.2
℃
- 107.7
℃
which is a 51.5
℃
difference range. However,
following purification, the melting point of the pure benzoic acid was 69.7 - 86.7
℃
whereas
naphthalene held a melting point value of 112.3 - 124.2
℃
. The initial broad melting point range
is attributed to the presence of impurities within the compound and the narrower melting range
observed indicates a higher level of purity
7
, affirming that the compound now exists in a
homogenous state without admixture with other substances.
4
During the experiment, the separatory funnel containing the mixture was agitated to improve the
separation of the liquid components. This agitation resulted in the accumulation of pressure
within the funnel, as the solvent, ethyl acetate, evaporated and contributed to the initial
∼
1
atmosphere of air pressure in the funnel. In order to alleviate this pressure, the funnel was opened
regularly after shaking to release the accumulated pressure. Once two distinct layers were
formed, and the bottom layer (containing benzoic acid) was discharged from the tip of the
separatory funnel, the upper layer (containing naphthalene) had to be poured out from the top
opening of the funnel. This precaution was taken to avoid any mixing of the organic layer with
the previously drained aqueous layer. Also, to guarantee the thorough transfer and residue
extraction of pure components, an additional precaution involving the rinsing of the beaker
previously containing the naphthalene solution with 3 mL of ethyl acetate. The performance of
this step and the second filtration of the solution in the beaker maximizes the yield by ensuring
that all components, especially any adhering to the sides or the bottom of the beaker, are
effectively transferred to the evaporation dish. When it comes to benzoic acid, the solids were
washed with ice-cold water in order to reduce the solubility of the product, maintaining it in a
solid state.
6
The process of washing the precipitates with ice-cold water also assists in the
removal of additional impurities with high solubility that are present in the ethyl acetate solvent.
Finally, to induce the formation of naphthalene crystals, the evaporating dish was placed on a
steam bath with a temperature exceeding 77.1
℃
(the boiling point of ethyl acetate). This
elevated temperature facilitated the evaporation of the solvent from the mixture which led to the
isolation of the naphthalene crystals.
5
In terms of errors, the reported yield of naphthalene, documented at 135%, surpasses the
theoretical limit of 100%. This outcome is impossible and may stem from the lingering presence
of impurities in the sample, potentially residual solvent like ethyl acetate.
8
Alternatively, a more
valid explanation could be the addition of a piece of tape to the evaporating dish for reasons of
identification before heating it in the steam bath. The failure to remove this tape before the final
measurement may have contributed to the inflated yield. Although the piece of tape is small, its
mass can exert a significant influence on the final weight of the pure compound since the initially
utilized mass was of only 1.0g.
In order to enhance the efficacy of this separation and purification technique, it is advisable to
conduct multiple extractions. This approach reduces the quantity of material retained in the
residue, thereby promoting a better extraction.
9
Additionally, employing smaller volumes of
solvent is deemed more effective than a singular extraction.
10
With that being said, extraction is a
frequently used purification and separation technique which is not only useful in chemistry labs,
but also in the context of waste treatment, food engineering, pharmaceutical and
hydrometallurgy.
11
Summary
Table 2:
Melting Point, mass and % yield of the pure benzoic acid and naphthalene compound.
Pure compounds
Melting Point
Mass
% Yield
Benzoic Acid
69.7 - 86.7
℃
0.769 g
80%
Naphthalene
112.3 - 124.2
℃
1.283 g
135%
Your preview ends here
Eager to read complete document? Join bartleby learn and gain access to the full version
- Access to all documents
- Unlimited textbook solutions
- 24/7 expert homework help
6
References
1.
Beharry, A. Experiment 1, CHM243H5S Introductory Organic Chemistry II
Course Manual, University of Toronto Mississauga, 2024
2.
Li, Q. Yi, Z. Su, M. Sun, X. Solubility of Naphthalene in Isobutyl Acetate,
n
-Butyric
Acid, Ethyl Acetate,
N
-Methyl Pyrrolidone,
N
,
N
-Dimethylformamide, and
Tetrahydrofuran.
https://pubs.acs.org/doi/10.1021/je800428r
(accessed 2024-30-01)
3.
SANLIFAN XIANG. Why is Ethyl Acetate a Good Solvent for Extraction
https://www.slchemtech.com/news/why-is-ethyl-acetate-a-good-solvent-for-extraction.html
(accessed 2024-30-01)
4.
UCLA, Extraction (Part 1).
https://www.chem.ucla.edu/~bacher/Specialtopics/extraction.html
(accessed 2024-30-01)
5.
LIBRETEXTS. Step-by-Step procedures for extraction.
https://chem.libretexts.org/Bookshelves/Organic_Chemistry/Organic_Chemistry_Lab_Technique
s_(Nichols)/04%3A_Extraction/4.06%3A_Step-by-Step_Procedures_For_Extractions
(accessed 2024-31-01)
6.
ONE PART OF CHEMISTRY. Recrystallization.
https://1chemistry.blogspot.com/2011/08/recrystallization.html
(accessed 2024-31-01)
7
7.
Mettler Toledo. What is a Melting Point ?
https://www.mt.com/ca/en/home/applications/Application_Browse_Laboratory_Analytics/Thermal
_Values/melting-point-determination.html
(accessed 2024-31-01)
8.
LIBRETEXTS. Theoretical Yield and % Yield.
https://chem.libretexts.org/Bookshelves/Introductory_Chemistry/Introductory_Chemistry_(CK-1
2)/12%3A_Stoichiometry/12.09%3A_Theoretical_Yield_and_Percent_Yield#:~:text=However%
2C%20percent%20yields%20greater%20than,the%20products%20of%20the%20reaction
.
(accessed 2024-31-01)
9.
LIBRETEXTS. Extraction Theory.
https://chem.libretexts.org/Bookshelves/Organic_Chemistry/Organic_Chemistry_Lab_Technique
s_(Nichols)/04%3A_Extraction/4.05%3A_Extraction_Theory
(accessed 2024-31-01)
10. Palleros, D. Liquid-Liquid Extraction.
https://www.chem.tamu.edu/rgroup/gladysz/documents/extractions.pdf
(accessed 2024-31-01)
11. Grow, C. Tan, M. Yeap, S. Chin, N.
A Review on Extraction Techniques and Its Future
Applications in Industry,
European Journal of Lipid Science and Technology
, 2021,
123(4).
Related Documents
Related Questions
Suppose you took your two compounds, dissolved them in tertbutyl methyl ether and then added them to a separatory funnel. Now suppose you add in aqueous sodium bicarbonate and vigorusly shake the contents of the separatory funnel.
ethanol will be dissolved in tert butyl methyl ether ether and valeric acid will be dissolved in the aqueous sodium bicarbonate layer.
Draw the EXACT chemical structure that will exist in each of the layers after shaking with sodium bicarbonate. (Is it neutral or charged?)
arrow_forward
A mixture of the two compounds shown below is dissolved in ether. Using the information given in the experiment, select all the correct statements regarding the extraction and isolation of the two compounds.
محمد
age
X
Y
A. X can be extracted from the organic layer using hydrochloric acid.
OB. Y can precipitate if hydrochloric acid is added to the salt of Y in the aqueous layer.
OC. Y can be extracted from the organic layer using hydrochloric acid.
D. X can precipitate if hydrochloric acid is added to the salt of X in the aqueous layer
arrow_forward
Question 1
You are employed as a co-op student at the Drug and Alcohol Testing Association of Canada (DATAC) developing analytical tests for sports doping agents. You are asked to prepare a procedure for the extraction of methylphenidate, the active compound in Ritalin, from urine samples (consider them as simple aqueous layers, you do not need to consider other components!). The goal of the procedure is to extract the methylphenidate into an organic layer which will then be evaporated and the residue will be tested for the drug.
You find that methylphenidate is highly soluble in 2-methyltetrahydrofuran, a bio-renewable solvent. Draw the structure of 2-methyltetrahydrofuran and give two reasons why it is a good solvent choice for liquid-liquid extraction. (Please find the image attached below to help you with this question)
Question 2 (cont. from scenario 1).
Your colleague is helping you develop the urine test. They suggest that the urine should be adjusted to a pH above 7 before…
arrow_forward
Please answer this NEATLY, COMPLETELY, and CORRECTLY for an UPVOTE.
1-butanol, 2-butanol, and diisopropyl ether all tested negatve (immiscible) in the solubility test with concentrated H2SO4. Considering the structure of the compounds, what generalization can be made for a substance to be soluble in concentrated H2SO4?
arrow_forward
Benzoic acid and water were added to the test tube labeled "b.a." After stirring the
mixture, sodium hydroxide (NaOH) vas added until the solid disappeared. Finally,
hydrochloric acid was added drop by drop until blue litmus paper turned red. The
solid present in the test tube after the addition of HCI is most likely:
benzoic acid
benzyl acetate
O benzyl chloride
sodium benzoate
arrow_forward
You need to recrystallize compound A. You are given several solvents to choose from. Briefly describe an experiment to determine what solvent is the best choice to recrystallize compound A.
arrow_forward
A student use the same protocol as in the lab manual to extract benzoic acid, phenol, and naphthalene. Below are the steps he took
Step 1 - Dissolve all three in 15 ml ether and place in separatory funnel
Step 2- Add 15 ml of sodium carbonate and mix well
Step3 - Isolate the aqueous layer and Add hydrochloric acid, which resulted in a precipitate
Step 4- Add 15 ml of sodium hydroxide to the ether layer and mix
Step 5- Isolate the aqueous layer and add hydrochloric acid, which resulted in a precipitate.
Step 6- dry the ether layer and collect the solid that is left
arrow_forward
Acetic acid, salicylic acid, benzoic acid all of them undergo esterification test separately with n-propyl alcohol and concentrated sulfuric acid. Which among the three is the fastest in showing the formation of pleasant odor. Arrange them from fastest to slowest. Explain and support your answer
arrow_forward
EXTRACTION FLOW CHART
Draw the appropriate chemical structure (acid, base, neutral, conjugate base, conjugate acid) in
the appropriate box in the following flow chart. Copy this into your laboratory notebook as part
of the prelab. Indicate if the compound is present in solution or as a solid.
Diethyl Ether Solution
H₂N-
OH
benzoic acid
Lower Aqueous Layer
6 M NaOH
OCH CH₂
9-Fluorenone
Ethyl 4-aminobenzoate
(Benzocaine)
3 M HCI
Upper Organic Layer
3 M NaOH
Lower Aqueous Layer
Upper Organic Layer
6 M HCI
arrow_forward
3. The sequence for separating a solution of benzoic acid, naphthalene and 2-naphthol
via extraction starts by washing the solution with aqueous sodium bicarbonate and follows
with washing the resulting organic extract with aqueous sodium hydroxide. Why are the
aqueous bases used in this order rather than the reverse order? Provide drawings and a brief
explanation. The information below might be useful.
OH
Benzoic acid
pka= 4.20
Base
NaHCO3
NaOH
OH
2-naphthol
pka= 9.5
Conjugate Acid
H₂CO3
H₂O
naphthalene
pka
6.4
16
1
arrow_forward
This experiment is the Separation of a mixture of 3-nitroaniline, Benzoic acid, and naphthalene using an acid-base separation extraction technique
What properties of the three compounds in this experiment allow you to use the above technique to separate them?Why are you asked to use multiple portions of the solvent at the extraction steps?Why are you asked not to discard any solvents until you have obtained your products?
arrow_forward
H 1
please help me with these problems, i will rate thank you.
arrow_forward
State a 'distillation' method you could use in the laboratory, while performing this synthesis, to ensure you have a high percentage of compound A. (think about Le Chatelier's principle)You can use any other method too
arrow_forward
1. A compound of molecular formula C5H100 forms a yellow precipitate with
reagent and a yellow precipitate with reagents for the iodoform test.
2,4-dinitrophenylhydrazine
a) Draw the structural formulae on a piece of paper, take a picture of them and upload the image
below.
b) Name the two (2) compounds that fit these tests.
arrow_forward
d)
for your recovered 1-phenylcyclohexanol is 50-55 °C. Is your 1-phenylcyclohexanol pure or impure? How do
you know? Please be specific.
The literature melting point of 1-phenylcyclohexanol is 59-62 °C. The melting point range you observed
arrow_forward
SEE MORE QUESTIONS
Recommended textbooks for you
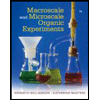
Macroscale and Microscale Organic Experiments
Chemistry
ISBN:9781305577190
Author:Kenneth L. Williamson, Katherine M. Masters
Publisher:Brooks Cole
Related Questions
- Suppose you took your two compounds, dissolved them in tertbutyl methyl ether and then added them to a separatory funnel. Now suppose you add in aqueous sodium bicarbonate and vigorusly shake the contents of the separatory funnel. ethanol will be dissolved in tert butyl methyl ether ether and valeric acid will be dissolved in the aqueous sodium bicarbonate layer. Draw the EXACT chemical structure that will exist in each of the layers after shaking with sodium bicarbonate. (Is it neutral or charged?)arrow_forwardA mixture of the two compounds shown below is dissolved in ether. Using the information given in the experiment, select all the correct statements regarding the extraction and isolation of the two compounds. محمد age X Y A. X can be extracted from the organic layer using hydrochloric acid. OB. Y can precipitate if hydrochloric acid is added to the salt of Y in the aqueous layer. OC. Y can be extracted from the organic layer using hydrochloric acid. D. X can precipitate if hydrochloric acid is added to the salt of X in the aqueous layerarrow_forwardQuestion 1 You are employed as a co-op student at the Drug and Alcohol Testing Association of Canada (DATAC) developing analytical tests for sports doping agents. You are asked to prepare a procedure for the extraction of methylphenidate, the active compound in Ritalin, from urine samples (consider them as simple aqueous layers, you do not need to consider other components!). The goal of the procedure is to extract the methylphenidate into an organic layer which will then be evaporated and the residue will be tested for the drug. You find that methylphenidate is highly soluble in 2-methyltetrahydrofuran, a bio-renewable solvent. Draw the structure of 2-methyltetrahydrofuran and give two reasons why it is a good solvent choice for liquid-liquid extraction. (Please find the image attached below to help you with this question) Question 2 (cont. from scenario 1). Your colleague is helping you develop the urine test. They suggest that the urine should be adjusted to a pH above 7 before…arrow_forward
- Please answer this NEATLY, COMPLETELY, and CORRECTLY for an UPVOTE. 1-butanol, 2-butanol, and diisopropyl ether all tested negatve (immiscible) in the solubility test with concentrated H2SO4. Considering the structure of the compounds, what generalization can be made for a substance to be soluble in concentrated H2SO4?arrow_forwardBenzoic acid and water were added to the test tube labeled "b.a." After stirring the mixture, sodium hydroxide (NaOH) vas added until the solid disappeared. Finally, hydrochloric acid was added drop by drop until blue litmus paper turned red. The solid present in the test tube after the addition of HCI is most likely: benzoic acid benzyl acetate O benzyl chloride sodium benzoatearrow_forwardYou need to recrystallize compound A. You are given several solvents to choose from. Briefly describe an experiment to determine what solvent is the best choice to recrystallize compound A.arrow_forward
- A student use the same protocol as in the lab manual to extract benzoic acid, phenol, and naphthalene. Below are the steps he took Step 1 - Dissolve all three in 15 ml ether and place in separatory funnel Step 2- Add 15 ml of sodium carbonate and mix well Step3 - Isolate the aqueous layer and Add hydrochloric acid, which resulted in a precipitate Step 4- Add 15 ml of sodium hydroxide to the ether layer and mix Step 5- Isolate the aqueous layer and add hydrochloric acid, which resulted in a precipitate. Step 6- dry the ether layer and collect the solid that is leftarrow_forwardAcetic acid, salicylic acid, benzoic acid all of them undergo esterification test separately with n-propyl alcohol and concentrated sulfuric acid. Which among the three is the fastest in showing the formation of pleasant odor. Arrange them from fastest to slowest. Explain and support your answerarrow_forwardEXTRACTION FLOW CHART Draw the appropriate chemical structure (acid, base, neutral, conjugate base, conjugate acid) in the appropriate box in the following flow chart. Copy this into your laboratory notebook as part of the prelab. Indicate if the compound is present in solution or as a solid. Diethyl Ether Solution H₂N- OH benzoic acid Lower Aqueous Layer 6 M NaOH OCH CH₂ 9-Fluorenone Ethyl 4-aminobenzoate (Benzocaine) 3 M HCI Upper Organic Layer 3 M NaOH Lower Aqueous Layer Upper Organic Layer 6 M HCIarrow_forward
- 3. The sequence for separating a solution of benzoic acid, naphthalene and 2-naphthol via extraction starts by washing the solution with aqueous sodium bicarbonate and follows with washing the resulting organic extract with aqueous sodium hydroxide. Why are the aqueous bases used in this order rather than the reverse order? Provide drawings and a brief explanation. The information below might be useful. OH Benzoic acid pka= 4.20 Base NaHCO3 NaOH OH 2-naphthol pka= 9.5 Conjugate Acid H₂CO3 H₂O naphthalene pka 6.4 16 1arrow_forwardThis experiment is the Separation of a mixture of 3-nitroaniline, Benzoic acid, and naphthalene using an acid-base separation extraction technique What properties of the three compounds in this experiment allow you to use the above technique to separate them?Why are you asked to use multiple portions of the solvent at the extraction steps?Why are you asked not to discard any solvents until you have obtained your products?arrow_forwardH 1 please help me with these problems, i will rate thank you.arrow_forward
arrow_back_ios
SEE MORE QUESTIONS
arrow_forward_ios
Recommended textbooks for you
- Macroscale and Microscale Organic ExperimentsChemistryISBN:9781305577190Author:Kenneth L. Williamson, Katherine M. MastersPublisher:Brooks Cole
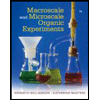
Macroscale and Microscale Organic Experiments
Chemistry
ISBN:9781305577190
Author:Kenneth L. Williamson, Katherine M. Masters
Publisher:Brooks Cole