IEEN 4316 Chapter 2 homework 2
docx
keyboard_arrow_up
School
Texas A&M University, Kingsville *
*We aren’t endorsed by this school
Course
5322
Subject
Business
Date
Apr 3, 2024
Type
docx
Pages
6
Uploaded by SuperHumanReindeer3726
IEEN 4316
Chapter 2 Product, Process, and Schedule Design
Please read chapter 2 and complete the following problems on page 74-82.
1. 2.13-
Let Input to Process 1 be I
1
and output from Process 1 be O
1
As defective rate of process 1 is 3%. O
1
= I
1
*(1-3%)=97%*I
1
O
2
= 97%*I
1
*(1-5%) = 95%*97%*I
1
O
3
= 95%*97%*I
1
*(1-7%) = 93%*95%*97%*I
1
1000 = 93%*95%*97%*I
1
=0.857*I
1
Hence, I
1
= 1000/0.857 = 1166.86
1167 units
Hence the required inputs should be 1167 units to meet a demand of 1000 units
To compute the scrap rate, we will take an input of 1167 units and compute the scrap units and scrap cost at each process. In the first case where defective rates are 3%, 5% and 7% respectively. (Note that
output units and defective units are rounded below)
Output of process 1 = 1167*(1-3%) = 1132 and defective units = 1167*3% = 35. Hence scrap cost = 35*5 = 175
Output of process 1 = 1132*(1-5%) = 1076 and defective units = 1132*5% = 56. Hence scrap cost = 56*10 = 560
Output of process 1 = 1076*(1-7%) = 1000 and defective units = 1076*7% = 76. Hence scrap cost = 76*15 = 1140
Hence total scrap cost = 175+560+1140 = $1875
Output of process 1 = 1167*(1-7%) = 1085 and defective units = 1167*7% = 82. Hence scrap cost = 82*5 = 410
Output of process 1 = 1085*(1-5%) = 1030 and defective units = 1085*5% = 55. Hence scrap cost = 55*10 = 550
Output of process 1 = 1030*(1-3%) = 1000 and defective units = 1030*3% = 30. Hence scrap cost = 30*15 = 300
Hence total scrap cost = 410+550+300= $1410
2. 2.14
to satisfy a demand of 1,000
units, the rework cost would be $36
for Process 1
, $S3×38
for Process 2
, and $Si×56
for Process 3
. If the scrap rates on processes 1and3
are reversed, the rework cost would not change, as it is dependent on the rework rates rather than the scrap rates.
3. 2.17
The number of machines needed to perform each operation can be calculated using the following formula:
number of machines = (standard time * (1 - (1 - efficiency) * (1 - reliability))) / (available time per day)
For operation 1, the number of machines needed is:
(3 minutes * (1 - (1 - 100%) * (1 - 95%))) / (16 hours / 60 minutes) = 1.25 = 2 machines
For operation 2, the number of machines needed is:
(2 minutes * (1 - (1 - 95%) * (1 - 90%))) / (16 hours / 60 minutes) = 1.08 = 2 machines
For operation 3, the number of machines needed is:
(5 minutes * (1 - (1 - 102%) * (1 - 90%))) / (16 hours / 60 minutes) = 1.58 = 2 machines
For operation 4, the number of machines needed is:
(10 minutes * (1 - (1 - 90%) * (1 - 95%))) / (8 hours / 60 minutes) = 2.22 = 3 machines
4. 2.18
Production Required= 10000 Parts/Yr
Weekly Production= 192.3 =192 parts/week (Rounded off) (52weeks in
year)
Time available in a week= 6days x 8 hrs= 48 hrs= 2880 mins/week
Input Operation 1-------- I1=192/(1-D1)(1-D2)(1-D3) = 192/(1-0.03)(1-
0.05)(1-0.05) =219 Parts
Input Operation 2-------- I2=192/(1-D1)(1-D2)(1-D3) = 192/(1-0.05)(1-
0.05) = 212 Parts
Input Operation 3-------- I3=192/(1-D1)(1-D2)(1-D3) = 192/(1-0.05) = 202 Parts
Required Number of machines (F=SQ/ (E x H x R))
Operation1 M/c A= (5x 219)/(1.08 x 2880 x 0.98) = 0.359 =1 (Rounded
up)
Operation2 M/c B= (3x 212)/(0.95 x 2880 x 0.95) = 0.23 =1 (Rounded up)
Operation3 M/c A= (3x 202)/(0.9 x 2880 x 0.95) = 0.246 =1 (Rounded up
5. 2.20
for 1 product we require 1 part A and 3 part B and 1 part C
for 15000 product, we require 15000 part A 45000part B and 15000 part C
as scrap factor of m/c 2 is 10%, we require 15000/(100-10)%= 16666.66 part before m/c 2
and 16666.66/0.8 = 20834 parts before machine 1
so raw material for part A is required for 20834 parts
similarly raw material required for part B = (45000/0.7)= 64286
similarly raw material required for part C = (15000/0.75)/0.7= 28572
6. 2.21
he percent change in the requirement for each input would be -5% if each
process was able to reduce its scrap estimate by 5%. This means that the requirement for each input would decrease by 5%.
From the estimation perspective, the percent change in the requirement for each input would be 5%. This means that the scrap rate would be reduced by 5%, resulting in a decrease in the amount of scrap that needs to be produced to reach the desired output. This would result in a decrease in the overall cost of the process, as less scrap needs to be produced.
From the continuous improvement perspective, the percent change in the
requirement for each input would be a positive 5%. This means that the process is becoming more efficient, as it is able to produce more output with less input. This could lead to cost savings, as less resources are needed to produce the same output. It could also lead to improved quality, as the process is able to produce more consistent output with less
variation.
The significance of this change in the requirements for each input can have a significant impact on the decision-making process of the process designer. If the designer is able to reduce the scrap rate by 5%, it could lead to cost savings that could benefit the company. It could also lead to improved quality, as the process is able to produce more consistent output with less variation. Additionally, it could lead to
improved efficiency, as the process is able to produce more output with less resources. This could all lead to an overall improved
Your preview ends here
Eager to read complete document? Join bartleby learn and gain access to the full version
- Access to all documents
- Unlimited textbook solutions
- 24/7 expert homework help
performance of the process, leading to increased profitability for the company.
Overall, the percent change in the requirement for each input can have
a significant impact on the decision-making process of the process designer. It can lead to cost savings, improved quality, and improved efficiency, all of which can lead to improved performance of the process. This can ultimately lead to increased profitability for the company.
7.
2.22
Express the production input of mschine of part be in the production process. I4=O6(1−d6)(1−d4)
Here, produciton input of the machine 4 of part B is I4, the desired output at assembly station 6 is O6.
Percentage of defective item of machine 4 is d4 and percentage of defective item at assembly station 6 is d4. Substitute 15000 unit for O6, 0.154 for d4 and 0.3 for d6.
To find I4=15,000(1−0.3)(1−0.15)=25,210.28≈25,210 unit
Express the number of machins required for operation
f=SQEHR
Where F= number of machines required per operation
S= Standard time per unit produced
Q= Number of units to be produced per operation
E = Actual performance H=Amount kof time available per machine
R= Reliability of machine is R
F4=S4Q4E4HR4=4×25,2100.98×5,400×0.95=20.05≈20 machines Thus, machine fraction for I4 is 20
Substitute 1500 units for O6, 0.10 for d4 and 0.25 for d6 in equation (1), we get I4=22,222 units
Substitute 4 min for S4 is 22222 units for Q4, 0.98 for E4, 5400 min/week for H and 0.95 for R4 in equation 3, we get F4=4×22,2220.98×5,400×0.95=14.68≈18 machines Hence, reducing scrap percentage will reduce the machine fractions, facilities planner has to decide about the utilization of space to increase the production with machines.
8.
2.23
the minimum number of machines required to meet the desired output
of 750 nondefective parts in an eight-hour shift is 36 machines, real-
world manufacturing scenarios often require additional machines or other optimizations to account for variability, efficiency, and economic factors.
9.
2.28
10. 2.29
=n×100×BINOMDIST(n,n,0.88,FALSE)−n×80×BINOMDIST(0,n,0.88,FALSE)
We can repeat this calculation for n = 1, 2, 3, ... and find the n that gives the
maximum expected profit.
Once we have the maximum expected profit, we can use the formula:
Probability of losing money =BINOMDIST(0,n,0.88,FALSE)
to find the probability of losing money on the transaction.
In excel, the BINOMDIST function can be used to calculate the probabilities. The code for this problem would look like the following:
=n×100×BINOMDIST(n,n,0.88,FALSE)−n×80×BINOMDIST(0,n,0.88,FALSE)
=BINOMDIST(0,n,0.88,FALSE)
Where n is the number of castings produced.
11. 2.30
a)The table in step 1 gives the probability of 4 or more good castings [P(X ≥ 4] out of n castings produced.
(b) Thus, to maximize expected profit 5 castings should be produced. (c)
The customer would accept only 4 good castings, a loss would be incurred if the number of good castings is less than for which the probability 12. 2.38
or product a, X=2 min and Y=2.5 min
For product b, X=1 min and Y=1.5 min
For product t, X=6 min and Y=8 min
The total time of product X is 9 minutes and for Y is 12 minutes. Given,
Co is cost per operator hour and Cm is cost per machine hour If one operator is assigned to one machine, the unit costs are as follows:
The total cost per unit of X=2×(15+50)60+1×1560+6×5060=$7.42
The total cost per unit of As the activity times are a,b and t, it ia possible to have less number of
operators as independent machine times for both the products (X=6,Y=8) is double the sum of other activity times a and b (X=3,Y=4).
One operator can handle two machines at a time, so far five machines, we should have maximum three operators to have minimum cost per unit produced
Total machine time per unit of X=8(2+6)=64 minutes
Total machine time per unit of Y=10.5(2.5+8)=110.25 minutes total machine time per unit of X=64 minutes
Total machine time per unit of Y=110.25 minutes
13. 2.41
a) The ideal machine assignment would be to have one operator assigned to each machine.
b) If three machines are assigned to an operator, the duration of the repeating cycle would be 20 minutes with no idle time for machines or operators.
c) The cost per unit produced if three machines are assigned to an operator would be $16/3.
14.
2.51 pick up one of the facilities in the problem to work on
Your preview ends here
Eager to read complete document? Join bartleby learn and gain access to the full version
- Access to all documents
- Unlimited textbook solutions
- 24/7 expert homework help
Related Documents
Recommended textbooks for you
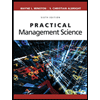
Practical Management Science
Operations Management
ISBN:9781337406659
Author:WINSTON, Wayne L.
Publisher:Cengage,
Recommended textbooks for you
- Practical Management ScienceOperations ManagementISBN:9781337406659Author:WINSTON, Wayne L.Publisher:Cengage,
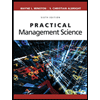
Practical Management Science
Operations Management
ISBN:9781337406659
Author:WINSTON, Wayne L.
Publisher:Cengage,