BUS740CS2
docx
keyboard_arrow_up
School
Southern New Hampshire University *
*We aren’t endorsed by this school
Course
740
Subject
Business
Date
Feb 20, 2024
Type
docx
Pages
8
Uploaded by fmalik89
1
Case Study: Dell Inc.: Improving the Flexibility of the Desktop PC Supply Chain
Assignment
Faizan Malik
Doctor of Business Administration, Liberty University
BUSI 740: Supply Chain Management
Dr. Thomas Spotts
September 10, 2022
2
Abstract
Founded in 1984, Dell introduced a new business model for the personal computer market, eliminating the middleman and selling their products directly to their consumers. With this business model, Dell quickly rose to the top ranks within the personal computer market and began introducing new products, such as printers and televisions, as well. Given their success, Dell eventually began manufacturing some of their products offshore in China, which subsequently introduced new issues related to costs, manufacturing, and delivery of their products. In this case study, we will review the logistics of Dell’s manufacturing process and associated issue, review issues proposed by Dell to mitigate these issues, and suggest additional solutions.
3
Why does L5 incur higher manufacturing and logistics costs than L6? What are some of the costs that are incurred in L5, but not in L6? Are there any costs that apply to only L6 but not L5?
Dell manufactures their desktop computers and several other of their products in a ten-
level system, with each level increasing the overall integration of the device. In Level 5 (L5), the desktop chassis, floppy disk drive, and fan are assembled and in Level (L6), the motherboard is also installed onto the chassis (Simchi-Levi et al., 2021). L5 manufacturing incurs a higher manufacturing costs and logistics due to a multitude of reasons. One of the main culprits is due to the higher costs associated with L5 manufacturing. Beginning with the transportation and assembly each of the levels, L5 devices are manufactured in China and then shipped via ocean freight, with the motherboards then being shipped via air freight separately, and then assembled in the United States. L6 devices, on the contrary, are fully assembled in China and then shipped to either the United States or Ireland via ocean freight. The air freight needed to ship motherboard separately increases the overheard for L5 manufacturing, as air freight rates can be upwards of 2.5 times greater than ocean freight (Hummels, 2007). Dell has also faced supply chain issues related to providing chipsets to their manufactures in China, with more then 60% of L5 manufacturing being the result of a lack of motherboard to complete L6 manufacturing in 2005 (Simchi-Levi et al., 2021). As a result of Dell’s inability to meet motherboard demands, they began utilizing 3
rd
-party integrators (3PIs) which produce lower quality products. Any issues with faulty or low-quality motherboards only further delays the supply chain and increases
costs for L5 manufacturing. Lastly, Dell’s forecasting for chipsets has been poor resulting in increased demand and delivery times, which also increases overhead due to the additional costs incurred with supplying additional chipsets.
Your preview ends here
Eager to read complete document? Join bartleby learn and gain access to the full version
- Access to all documents
- Unlimited textbook solutions
- 24/7 expert homework help
4
Which of the six proposed manufacturing solutions should Dell implement, based on the survey result (Table 6-1)? Why? What are the pros and cons of this recommendation?
To mitigate the increasing costs of L5 manufacturing, Dell assembled a business process improvement (BPI) team, who proposed six potential solutions. These proposed solutions included keeping the process as is, performing L5-10 manufacturing domestically, assembling motherboards to chassis at a supplier logistics center (SLC), assembling motherboards to chassis within a leased building, managing 3PIs directly, and transferring L6 manufacturing to Mexico (Simchi-Levi et al., 2021). Based on their survey results of complexity and cost analysis, option 3A (integration at the SLC) would be recommended. Logistic centers often act as focal points for
the flow of raw material, providing points of access for shipping and other logistic functions, without additional infrastructure costs (Hamzeh, 2007). Beginning with cost per box, if Dell were to complete integration at the SLC, they would save nearly 29% per unit as compared to their existing model and is only marginally more expensive than the cheapest option (Option 4) of moving integration to Mexico. In addition to reducing cost per box, option 3A also has the benefit of improved supplier quality engineer level on a regional level and significant improved supplier quality engineer level on a global level when compared to Option 4. By reducing costs associated with manufacturing and shipping of motherboards, and having increased control over quality and L5 assembly, Dell can mitigate many of the issues discussed earlier. Despite the numerous benefits of option 3A, it is not without its own drawbacks. With manufacturing essentially moving in-house, the overall complexity of production control, operations, process engineering, and cost accounting increase significantly when compared to their current methods. To obtain the full benefits, Dell must outline and execute a production plan that can meet
5
customer demands, as well having proper management in place to ensure smooth process engineering and accounting for the increased use of the SLC. How easily sustainable is your recommendation for the previous question if the chipset supply shortage further deteriorates?
If Dell encountered further deuteriation of their chipset supply, option 3A would likely not be a sustainable model for Dell. However, given the fact that chipsets are an integral component of motherboards, it is likely that none of the presented options would mitigate such a shortage as motherboards are manufactured outside of the ten-level manufacturing process. Option 3A does offer the benefit of less complex worldwide procurement, when compared to the existing model, meaning if the chipset supply shortage worsened, they could more easily procure
the material needed to assemble motherboards which will also help to expand their supplier relations. As stated by Rajagopal and Bernard (1993), “Growth, if indeed not survival, frequently
depends upon the willingness to seek and evaluate options beyond the company's immediate circle of customers and suppliers - and this entails preparedness to "break the mold" of existing relationships and, implicitly perhaps, to replace them with new or refocused associations.”
How good is the methodology employed by the BPI team to determine the optimal manufacturing option for Dell? Are there more effective approaches?
The methodology employed by the BPI to improve manufacturing for Dell was both comprehensive and effective. By surveying various stakeholders within the organization that were impacted by the chipset supply shortage, the BPI was able complexity and costs associated with various variables of each of the six proposed options. However, there may be more effective
6
approaches to obtain more optimal manufacturing. By improving their demand forecasting, Dell may be able to better utilize a push-pull strategy within their manufacturing process, in which partially completed products are stored or “pushed” and then completed upon order by a customer or “pulled.” This strategy is beneficial in repetitive manufacturing, such as that done by
Dell, and has he benefits of “reduced in-process inventory, shortened delivery lead times while maintaining or improving delivery dependability, increased productivity and machine utilization”
(Huang & Kusiak, 1998). Dell may also look to enter the chipset sector themselves to avoid any delays caused by shortages. By doing so, Dell can further streamline their manufacturing process
and reduce costs.
How can Dell effectively address the root causes contributing to the increase of L5 manufacturing?
Simchi-Levi et al. (2021) identified the four root causes of the increased L5 manufacturing as chipset supply issues, quality and engineering issues, inaccurate forecasting, and new product introduction (NPI). To effectively address these root causes, Dell must deploy multiple strategies to their manufacturing process. As discussed earlier, to address the chipset shortage issues, Dell may benefit from utilizing a push-pull strategy that allows for them to increase their inventory, which will decrease manufacturing and lead times. This will likely also address issues related to the quality of malfunctioning motherboards, as they have a stock of the highest quality chipsets needed to complete customer orders on demand. To improve upon their issues related to forecasting, Dell may look to introduce Artificial Intelligence (AI) to automate this process. In traditional forecasting, organizations often are faced with irregular results and become less when accurate when face with changing demands (Amirkolaii et al., 2017). If AI
Your preview ends here
Eager to read complete document? Join bartleby learn and gain access to the full version
- Access to all documents
- Unlimited textbook solutions
- 24/7 expert homework help
7
was adopted by Dell, the organization can have continuously updating forecast based on the current demand and can eliminate any of the guess work associated with traditional demand forecasting. AI would also potentially assist with issues related to NPI, as it can anticipate the demands for new products prior to their release by recognizing patterns and identifying trends.
Conclusion
Despite their continued success, Dell has not been immune to supply chain issues faced by organizations throughout all industries. With on-going chipset shortages and increasing costs for their ten-level manufacturing process, Dell assembled a BPI to help the organization mitigate some on-going issues. Although the suggestions offered by the BPI may help Dell in the short-
term, given the potential for the chipset shortage to worsen, it is likely that the proposals are not sustainable. As such, Dell may look to additional methodologies such as utilizing push-pull strategy or manufacturing chipsets in-house, to continue to grow and maintain their position within the industry.
8
References
Amirkolaii, K. N., Baboli, A., Shahzad, M. K., & Tonadre, R. (2017). Demand forecasting for irregular demands in business aircraft spare parts supply chains by using artificial intelligence (AI). IFAC-PapersOnLine, 50
(1), 15221-15226.
Hamzeh, F. R., Tommelein, I. D., Ballard, G., & Kaminsky, P. (2007, July). Logistics centers to support project-based production in the construction industry. In Proceedings of the 15th Annual Conference of the International Group for Lean Construction (IGLC 15)
(pp. 181-191).
Huang, C. C., & Kusiak, A. (1998). Manufacturing control with a push-pull approach. International Journal of Production Research, 36
(1), 251-276.
Hummels, D. (2007). Transportation costs and international trade in the second era of globalization. Journal of Economic perspectives
, 21(3), 131-154.
Rajagopal, S., & Bernard, K. N. (1993). Globalization of the procurement process. Marketing Intelligence & Planning.
Simchi-Levi, D., Kaminsky, P., & Simchi-Levi, E. (2021).
Designing and Managing the Supply Chain: Concepts, Strategies and Case Studies
(4th ed.). New York, NY: Richard D. Irwin, Inc. ISBN: 9780073403366.
Related Documents
Recommended textbooks for you
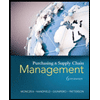
Purchasing and Supply Chain Management
Operations Management
ISBN:9781285869681
Author:Robert M. Monczka, Robert B. Handfield, Larry C. Giunipero, James L. Patterson
Publisher:Cengage Learning
Marketing
Marketing
ISBN:9780357033791
Author:Pride, William M
Publisher:South Western Educational Publishing
Recommended textbooks for you
- Purchasing and Supply Chain ManagementOperations ManagementISBN:9781285869681Author:Robert M. Monczka, Robert B. Handfield, Larry C. Giunipero, James L. PattersonPublisher:Cengage LearningMarketingMarketingISBN:9780357033791Author:Pride, William MPublisher:South Western Educational Publishing
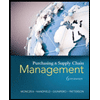
Purchasing and Supply Chain Management
Operations Management
ISBN:9781285869681
Author:Robert M. Monczka, Robert B. Handfield, Larry C. Giunipero, James L. Patterson
Publisher:Cengage Learning
Marketing
Marketing
ISBN:9780357033791
Author:Pride, William M
Publisher:South Western Educational Publishing