Busi5010Assessment2
docx
keyboard_arrow_up
School
Fayetteville State University *
*We aren’t endorsed by this school
Course
5310
Subject
Business
Date
Feb 20, 2024
Type
docx
Pages
5
Uploaded by MasterLionPerson973
Accounting Tools
Professor Bitter
Marcia Clarke
MBA-FPX5010
Capella University
December 31, 2023
Introduction
The Acme Pickle Company is renowned for producing top-notch pickles, prompting the owner of Super Deals grocery chain to propose a partnership. The offer on the table is $9.50 per case for 2,000 cases of Acme Pickles. However, with a production cost of $10 per case, the company is contemplating whether to accept or reject the deal. Customers have the option to purchase a case of Acme Pickles for $20. The company is currently reevaluating the accuracy of its manufacturing cost calculations to determine the feasibility of the transaction.
Production and fixed costs
Production costs are categorized into variable and fixed components based on their responsiveness to changes in production levels. Variable costs, as demonstrated in studies such as "A planar facility location–allocation problem with fixed and/or variable cost structures for rural electrification" (Akbas & Kocaman, 2023), are expenses that vary proportionally with the quantity of goods or services produced. These costs typically include raw materials, direct labor, and utilities directly linked to production volume. The rationale behind variable costs is their direct correlation to the inputs required for manufacturing; as production increases, so do these costs, and vice versa. This flexibility allows businesses to adjust their expenses in tandem with fluctuations in production levels, making variable costs dynamic and responsive. In contrast, fixed costs, exemplified in research like "Fixed costs and recreation value" (English et al., 2019),
remain constant irrespective of changes in production volume. These costs encompass essential infrastructure expenses such as rent, salaries of permanent staff, insurance, and depreciation. Fixed costs are incurred to maintain the overall operational framework of a business and do not fluctuate with production variations. This stability in fixed costs provides a foundation for businesses to operate, and they are crucial for the day-to-day functioning of the enterprise. The distinct characteristics of variable and fixed costs enable businesses to analyze their cost structures effectively and make informed decisions regarding production levels and overall financial stability.
Benefit of recalculating the cost of pickle production
Recalculating the cost of pickle production can provide several benefits to the Acme Pickle Company. Firstly, it ensures accurate and up-to-date information regarding the actual cost of producing each case of pickles. This precision is crucial for making informed business decisions, especially when considering a partnership offer such as the one from the Super Deals grocery chain. By reevaluating the production cost, the company gains clarity on its financial standing and can assess the feasibility of the proposed transaction more accurately. To recalculate the production cost, the company would need to review and update all the factors contributing to the cost per case. This includes a comprehensive examination of variable costs such as raw materials, labor, and utilities, as well as fixed costs like rent and insurance. Any changes in these elements or miscalculations in the initial cost assessment could be identified and
corrected. The result of the recalculation would be an adjusted cost per case, allowing the company to better understand the true profitability of the partnership deal. The benefit to the company of recalculating the cost is twofold. Firstly, it ensures that the company is not operating
at a loss by accepting an offer below the actual production cost. Secondly, it provides a basis for negotiation with potential partners. Armed with accurate cost information, the Acme Pickle Company can make informed decisions to maximize its profitability and maintain a sustainable business model. Additionally, precise cost calculations contribute to overall financial transparency and help in strategic planning for future business ventures. After a thorough recalculation, the cost of production for each case of pickles remains consistent at $10.00. The reassessment encompassed all items on the cost list that contribute to the production cost. It's essential to note that all these costs are product cost, meaning they directly impact the cost of production. The meticulous recalibration ensures that every relevant expense is considered, and the firm's initial cost of production calculation has been verified for accuracy. Any omission of these costs in the calculation would have led to a significant error, emphasizing the importance of a comprehensive and precise approach to cost assessment in maintaining financial integrity.
Financial Accounting of Production Cost
Financial accounting is primarily concerned with providing a comprehensive overview of
a company's financial performance to external stakeholders, adhering to generally accepted accounting principles (GAAP) or International Financial Reporting Standards (IFRS). In the context of production cost, financial accounting aggregates all costs associated with manufacturing and presents them in financial statements. Financial accounting ensures compliance with external reporting standards, offering a standardized presentation of production costs (Akbas & Kocaman, 2023). External stakeholders, such as investors and regulators, gain a transparent view of a company's financial health, including production costs (Prokhorov & Dreisbach, 2022). Financial accounting may lack the detailed breakdown of production costs needed for internal decision-making, as it aims for a broad perspective (Dyakova, 2020). It prioritizes meeting external reporting standards, potentially limiting its usefulness for internal managerial decisions.
Managerial Accounting of Production Cost
Managerial accounting is tailored for internal decision-making, allowing management to plan, control, and optimize operations. It provides detailed insights into various cost components,
such as variable and fixed costs, without strict adherence to external reporting standards. Managerial accounting offers a granular breakdown of production costs, facilitating detailed analysis and optimization of resource allocation (Fülöp et al., 2021). Unlike financial accounting,
managerial accounting is flexible and can be customized to meet specific internal needs (Shutikov et al., 2020). Due to its internal focus, managerial accounting may be subject to bias for specific managerial objectives, potentially affecting the reliability of data (Dharmawardane et
al., 2021). The absence of standardized reporting may hinder communication with external stakeholders and pose challenges in external decision-making (English et al., 2019).
In summary, financial accounting prioritizes external reporting and transparency, adhering to external standards, while managerial accounting offers detailed insights for internal decision-making with a more flexible and customized approach. Both methods serve distinct purposes, and a balanced use of both is often essential for comprehensive financial management.
Your preview ends here
Eager to read complete document? Join bartleby learn and gain access to the full version
- Access to all documents
- Unlimited textbook solutions
- 24/7 expert homework help
Recommendations
The evidence to support the decision of not selling pickles to Super Deals for $9.50 a case and seeking renegotiation or quitting the contract can be derived from the provided cost report and financial analysis. The cost report indicates that the cost per case for producing 9,000 cases of pickles is $10.00. Selling the cases to Super Deals at $9.50 would result in a loss of $0.50 per case. The total production costs for 9,000 cases amount to $90,000. Selling all cases at the proposed price of $9.50 would only generate $85,500 in revenue, resulting in a net loss of $4,500. The information indicates that the company is operating well beyond its break-even point at the current production level. Accepting the proposed price would jeopardize this profitability and erode the company's margins. The evidence suggests that Acme Pickle Company has the option to negotiate a more favorable price with Super Deals. The solid financial position, evidenced by the profitable production level, provides leverage for renegotiation. Selling the product at a loss is not sustainable in the long term and could negatively impact the financial health of Acme Pickle Company. The evidence supports the need
to secure a pricing structure that ensures profitability. The decision not to accept the proposed price aligns with the strategic objective of maintaining profitability and sustainable growth. The evidence supports the stance that a loss-making deal is not in the best interest of the company. Assessing the broader market conditions, customer demand, and the company's position within the industry can provide additional evidence to support the decision. If the market supports a higher price, it strengthens the case for renegotiation. Conducting a financial forecast considering
various pricing scenarios can provide evidence of the potential impact on the company's financial
performance. This evidence aids in making informed decisions regarding the contract. In summary, the evidence from the cost report, production costs, and overall financial analysis clearly supports the decision not to sell pickles to Super Deals for $9.50 a case. Seeking renegotiation or, if necessary, quitting the contract aligns with the company's financial objectives
and long-term sustainability.
References
Akbas, B., & Kocaman, A. S. (2023). A planar facility location–allocation problem with fixed and/or variable cost structures for rural electrification. Computers & Operations Research, 154, 106202.
https://doi.org/10.1016/j.cor.2023.106202
Dharmawardane, C., Sillanpää, V., & Holmström, J. (2021). High-frequency forecasting for grocery point-of-sales: Intervention in practice and theoretical implications for operational design. Operations Management Research, 14(1-2), 38-
60.
https://doi.org/10.1007/s12063-020-00176-7
Dyakova, O. V. (2020). Development of a methodology for sharing the enterprise total costs into
the fixed and variable components in the cost-management tools' improvement. IOP Conference Series. Materials Science and Engineering, 913(5), 52024.
https://doi.org/10.1088/1757-899X/913/5/052024
English, E., Herriges, J. A., Lupi, F., McConnell, K., & von Haefen, R. H. (2019). Fixed costs and recreation value. American Journal of Agricultural Economics, 101(4), 1082-
1097.
https://doi.org/10.1093/ajae/aaz012
Fülöp, Á., Bakó, K., & Stanciu, A. (2021). separation of fixed and variable costs from mixed costs at a water and sewerage operator. Analele Universităţii Din Oradea. Ştiinţe Economice, 30(30 (1)), 220-226.
https://doi.org/10.47535/1991AUOES30(1)024
Prokhorov, O., & Dreisbach, D. (2022). The impact of renewables on the incidents of negative prices in the energy spot markets. Energy Policy, 167, 113073.
https://doi.org/10.1016/j.enpol.2022.113073
Shutikov, M. A., Feofanov, A. N., & Ponomarev, K. S. (2020). Introducing a quality factor into the MES system when calculating machinery production schedule together with measuring equipment. IOP Conference Series. Materials Science and Engineering, 971(4), 42079.
https://doi.org/10.1088/1757-899X/971/4/042079
Related Documents
Recommended textbooks for you
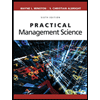
Practical Management Science
Operations Management
ISBN:9781337406659
Author:WINSTON, Wayne L.
Publisher:Cengage,
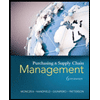
Purchasing and Supply Chain Management
Operations Management
ISBN:9781285869681
Author:Robert M. Monczka, Robert B. Handfield, Larry C. Giunipero, James L. Patterson
Publisher:Cengage Learning
Recommended textbooks for you
- Practical Management ScienceOperations ManagementISBN:9781337406659Author:WINSTON, Wayne L.Publisher:Cengage,Purchasing and Supply Chain ManagementOperations ManagementISBN:9781285869681Author:Robert M. Monczka, Robert B. Handfield, Larry C. Giunipero, James L. PattersonPublisher:Cengage Learning
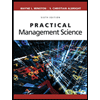
Practical Management Science
Operations Management
ISBN:9781337406659
Author:WINSTON, Wayne L.
Publisher:Cengage,
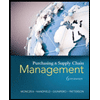
Purchasing and Supply Chain Management
Operations Management
ISBN:9781285869681
Author:Robert M. Monczka, Robert B. Handfield, Larry C. Giunipero, James L. Patterson
Publisher:Cengage Learning