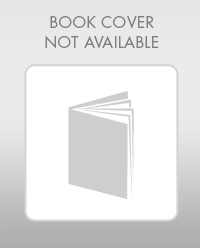
Operations Management: Processes And Supply Chains (12th Global Edition) - Does Not Include Mylab Operations Management
12th Edition
ISBN: 9780134890357
Author: Lee J. Krajewski, Manoj K. Malhotra
Publisher: Pearson Global Edition
expand_more
expand_more
format_list_bulleted
Concept explainers
Question
Chapter C, Problem 7P
Summary Introduction
Interpretation: The best order quantity is to be calculated.
Concept Introduction: Specific quantity of an item to be delivered at a specific date is lot size. Ordering optimum size (creating no additional or shortage of materials in stock) at minimum ordering cost is EOQ.
Expert Solution & Answer

Want to see the full answer?
Check out a sample textbook solution
Students have asked these similar questions
Analyze Walmart Inc. operations and conducting a strengths, weaknesses, opportunities, and threats (SWOT) analysis. Pay attention to Walmart Inc. strengths and opportunities to come up with a social cause that meshes well with them. Focusing on areas where Walmart Inc. excels and then finding a social cause that can benefit from Walmart Inc. strengths can also ultimately help
Consider how shareholder and stakeholder theories of ethics will impact the selection of a target social cause for Walmart Inc to pursue.
What responsibility does Walmart Inc. owe to its stockholders and stakeholders? Will pursuing a social responsibility program detract from the responsibilities to these two groups? Any program that is implement will redirect resources toward the social cause and away from the stockholders and stakeholders. Is it ethical?
Walmart Inc SWOT analysis. Justify each item of the analysis.
Evaluate the ethical implications of pursuing a social responsibility program in terms of the…
Detail Instructions
Consider the following activities, activity times and precedence relations for a hypothetical Athletic
Club Building project.
Activity Activity Description
Normal Time (weeks)
Immediate
Predecessors
A
Form project team
9
B
Prepare renovation plans
12
A
C
Demolish interior space
10
B
D
Upgrade utility systems
20
A
E
Select equipment, furniture &
10
B
fixtures
F
Hire Staff
10
A
G
Renovate building
30
B,C
H
Purchase equipment, furniture &
26
E
fixtures
Install equipment, furniture &
4
D.G.H
fixtures
3
FI
J
Train staff
How do you think smaller companies, with less sophisticated systems compared to giants like Amazon, can apply Little's Law to optimize their operations?
Please Provide a reference
Chapter C Solutions
Operations Management: Processes And Supply Chains (12th Global Edition) - Does Not Include Mylab Operations Management
Knowledge Booster
Learn more about
Need a deep-dive on the concept behind this application? Look no further. Learn more about this topic, operations-management and related others by exploring similar questions and additional content below.Similar questions
- What are your thoughts on how businesses can account for real-world variability when applying Little's Law, especially in industries where demand is highly unpredictable? Please provide referencearrow_forwardHow can businesses integrate Petri Net modeling with Little's Law to enhance supply chain resilience, especially in unexpected disruptions such as supplier delays or demand fluctuations? Please provide a refernencearrow_forwardHow can businesses integrate Petri Net modeling with Little's Law to enhance supply chain resilience, especially in unexpected disruptions such as supplier delays or demand fluctuations?arrow_forward
- Learning Activity 5: Expansion in Global Markets Discussion Questions: Bubble (or “boba”) tea is a milky tea containing chewy tapioca balls. It is has gained huge popularity in markets across Asia and is now also in North America and Europe. In your view will the recent exponential growth continue, and will it be at the expense of other drinks such as traditional black or green tea or coffee? Can global markets continue to support its growth, and what age group is mainly targeted?arrow_forwardDyson, a high-tech home appliance maker, has cut ties with Malaysian supplier ATA IMS Bhd following an audit of the company's labour practices and allegations by a whistleblower. ATA is already under US investigation over forced labour allegations. Dyson has terminated its contracts and is in talks with its customer over the audit findings. ATA, which produces parts for Dyson's vacuum cleaners and air purifiers, tumbled 30% to its lowest since April 2020. The termination is a significant blow for Malaysia, a major electronics manufacturing hub, which has faced scrutiny this year over claims of abusive working and living conditions. Dyson terminated the relationship with six months' contractual notice, hoping it would give ATA the impetus to improve and enable an orderly withdrawal in the interests of the workers they employ. Former ATA worker Dhan Kumar Limbu was beaten by police in Malaysia after sharing information about conditions at the factory with activists. ATA denied all…arrow_forwardQuestion content area Part 1 Oakwood Hospital is considering using ABC analysis to classify laboratory SKUs into three categories: those that will be delivered daily from their supplier (Class A items), those that will be controlled using a continuous review system (B items), and those that will be held in a two bin system (C items). The following table shows the annual dollar usage for a sample of eight SKUs. Fill in the blanks for annual dollar usage below. (Enter your responses rounded to the nearest whole number.) Part 2 Rank the SKUs in descending order on the basis of their annual dollar usage and fill in the table with the ranked SKU's percentage of dollar usage. (Enter your responses rounded to two decimal places.)arrow_forward
- Sam's Pet Hotel operates 51 weeks per year, 6 days per week, and uses a continuous review inventory system. It purchases kitty litter for $13.00 per bag. The following information is available about these bags: > Demand 70 bags/week > Order cost $58.00/order > Annual holding cost 30 percent of cost > Desired cycle-service level = 80 percent >Lead time 4 weeks (24 working days) > Standard deviation of weekly demand = 15 bags > Current on-hand inventory is 320 bags, with no open orders or backorders. a. Suppose that the weekly demand forecast of 70 bags is incorrect and actual demand averages only 45 bags per week. How much higher will total costs be, owing to the distorted EOQ caused by this forecast error? The costs will be $ higher owing to the error in EOQ. (Enter your response rounded to two decimal places.)arrow_forwarda. The average aggregate inventory value of the product if Ruby-Star used vendor 1 exclusively is $enter your response here. (Enter your response as a whole number.) b. The aggregate inventory value of the product if Ruby-Star used vendor 2 exclusively is shown below. c. How would your analysis change if average weekly demand increased to 160 units per week? The aggregate inventory values are shown below.arrow_forwarda. What order quantity should be used? lures. (Enter your response rounded to the nearest whole number.) b. What reorder point should be used? (Enter your response rounded to the nearest whole number.) c. What is the total annual cost for this inventory system? (Enter your response rounded to two decimal places)arrow_forward
- Oakwood Hospital is considering using ABC analysis to classify laboratory SKUS into three categories: those that will be delivered daily from their supplier (Class A items), those that will be controlled using a continuous review system (B items), and those that will be held in a two bin system (C items). The following table shows the annual dollar usage for a sample of eight SKUS. Fill in the blanks for annual dollar usage below. (Enter your responses rounded to the nearest whole number.) SKU Unit Value Demand (units) Annual Dollar Usage 1 $1.10 30,000 $ 2 $0.02 125,000 $ 3 $0.20 65,000 S 4 $0.02 1,100 SA 5 $1.40 150 SA 678 $4.10 900 $ $0.80 350 $ $0.55 80 EA $arrow_forwardDyson, a high-tech home appliance maker, has cut ties with Malaysian supplier ATA IMS Bhd following an audit of the company's labour practices and allegations by a whistleblower. ATA is already under US investigation over forced labour allegations. Dyson has terminated its contracts and is in talks with its customer over the audit findings. ATA, which produces parts for Dyson's vacuum cleaners and air purifiers, tumbled 30% to its lowest since April 2020. The termination is a significant blow for Malaysia, a major electronics manufacturing hub, which has faced scrutiny this year over claims of abusive working and living conditions. Dyson terminated the relationship with six months' contractual notice, hoping it would give ATA the impetus to improve and enable an orderly withdrawal in the interests of the workers they employ. Former ATA worker Dhan Kumar Limbu was beaten by police in Malaysia after sharing information about conditions at the factory with activists. ATA denied all…arrow_forwardQuestion 4 (25 Marks) Discuss how developing internal performance measures to track the performance of supplier development, can create efficiency for Pick n Pay.arrow_forward
arrow_back_ios
SEE MORE QUESTIONS
arrow_forward_ios
Recommended textbooks for you
- Purchasing and Supply Chain ManagementOperations ManagementISBN:9781285869681Author:Robert M. Monczka, Robert B. Handfield, Larry C. Giunipero, James L. PattersonPublisher:Cengage LearningMarketingMarketingISBN:9780357033791Author:Pride, William MPublisher:South Western Educational PublishingPractical Management ScienceOperations ManagementISBN:9781337406659Author:WINSTON, Wayne L.Publisher:Cengage,
- Contemporary MarketingMarketingISBN:9780357033777Author:Louis E. Boone, David L. KurtzPublisher:Cengage Learning
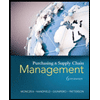
Purchasing and Supply Chain Management
Operations Management
ISBN:9781285869681
Author:Robert M. Monczka, Robert B. Handfield, Larry C. Giunipero, James L. Patterson
Publisher:Cengage Learning
Marketing
Marketing
ISBN:9780357033791
Author:Pride, William M
Publisher:South Western Educational Publishing
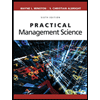
Practical Management Science
Operations Management
ISBN:9781337406659
Author:WINSTON, Wayne L.
Publisher:Cengage,
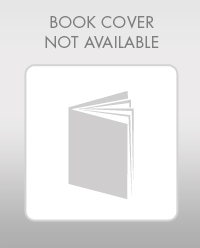
Contemporary Marketing
Marketing
ISBN:9780357033777
Author:Louis E. Boone, David L. Kurtz
Publisher:Cengage Learning
Inventory Management | Concepts, Examples and Solved Problems; Author: Dr. Bharatendra Rai;https://www.youtube.com/watch?v=2n9NLZTIlz8;License: Standard YouTube License, CC-BY