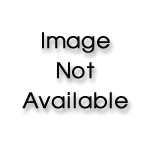
a.
To identify: That Company H should make rather than buy.
Concept Introduction: Decision making is a process in which members of an organization select a particular course of action in response to both problem and opportunity. The objective of decision making is to gain a maximum and profitable result.
b.
To calculate: The break even quantity.
Concept Introduction: Break-even point is explained as a point where a company is earning no profits and incurring no losses reflecting that total cost is equivalent to total income.
c.
To identify: The other consideration that might be important.
Concept Introduction: Decision making is a process in which members of an organization select a particular course of action in response to both problem and opportunity. The objective of decision making is to gain a maximum and profitable result.

Want to see the full answer?
Check out a sample textbook solution
Chapter A Solutions
MyLab Operations Management with Pearson eText -- Access Card -- for Operations Management: Processes and Supply Chains
- FORMATIVE ASSESSMENT 1 Read the article below and answer ALL the questions Pick n Pay reveals strategy to restore its business 27 May 2024 [100 MARKS] Following a disappointing full year performance for FY24, Pick n Pay CEO Sean Summers has unveiled the new board- approved six-point strategy to restore the Group's core Pick n Pay supermarket business to profitability. PHASED APPROACH IMPLEMENTATION Leverage strength of partnerships Leadership and people 2 Reset the store estate 3 Improve offer to drive sales 4 Optimise operating model Leverage strength of partnerships Recapitalisation Pick n Pay Prod FY26 FY27 Before Tax break-even FY25 Halve Group H2 FY24 H1 FY25 H2 FY25 H1 FY26 H2 FY26 HI FY27 H2 FY27 KEY IMPACT AND/OR TARGETED OUTCOMES Appointing the right people, in the optimal roles, to Directly and indirectly impact revenue growth drivers and 1 drive sales and realise margin improvement 5 enhances gross and operating margins 2 Expected notable associated savings/loss avoidance…arrow_forwardWith an enormous amount of data stored in databases and data warehouses, it is increasinglyimportant to develop powerful tools for analysis of such data and mining interestingknowledge from it. Data mining is a process of inferring knowledge from such huge data. Themain problem related to the retrieval of information from the World Wide Web is theenormous number of unstructured documents and resources, i.e., the difficulty of locating andtracking appropriate sources. Your company is considering investing in a Human Resource Information System (HRIS).Briefly explain the strategies for justifying HRIS investments.arrow_forwardYour company is considering investing in a Human Resource Information System (HRIS).Briefly explain the strategies for justifying HRIS investments.arrow_forward
- EXPLAIN Human Resource Information System (HRIS)arrow_forwardRead the mini-case study below and answer the following questions.With an enormous amount of data stored in databases and data warehouses, it is increasinglyimportant to develop powerful tools for analysis of such data and mining interestingknowledge from it. Data mining is a process of inferring knowledge from such huge data. Themain problem related to the retrieval of information from the World Wide Web is theenormous number of unstructured documents and resources, i.e., the difficulty of locating andtracking appropriate sources.Briefly explain any five (5) types of information you can get from data mining.arrow_forwardProblem 1: Practice Problems Chapter 6 Managing Quality The accounts receivable department has documented the following defects over a 30-day period: Category Frequency Invoice amount does not agree with the check amount 108 Invoice not on record (not found) 24 No formal invoice issued Check (payment) not received on time 18 30 Check not signed 8 Invoice number and invoice referenced do not agree 12 What techniques would you use and what conclusions can you draw about defects in the accounts receivable department? Problem 2: Prepare a flow chart for purchasing a Big Mac at the drive-through window at McDonalds. Problem 3: Draw a fishbone chart detailing reasons why a part might not be correctly machined.arrow_forward
- Problem 5: Development of a new deluxe version of a particular software product is being considered. The activities necessary for the completion of this project are listed in the table below along with their costs and completion times in weeks. Activity Normal Crash Normal Crash Immediate Time Time Cost Cost Predecessor A 4 3 2,000 2,600 B 2 1 2,200 2,800 A C 3 3 500 500 A D 8 4 2,300 2,600 A E 6 3 900 1,200 B, D F 3 2 3,000 4,200 C, E G 4 2 1,400 2,000 F a. What is the project expected completion date? b. What is the total cost required for completing this project on normal time? c. If you wish to reduce the time required to complete this project by 1 week, which activity should be crashed, and how much will this increase the total cost?arrow_forwardI need answer typing clear urjent no chatgpt used pls i will give 5 Upvotes.with diagramarrow_forwardnot use ai pleasearrow_forward
- provide scholarly reseach and references for the following 1. explain operational risks and examples of such risk faced by management at financial institutions 2. discuss the importance of establishing an effective risk management policy at financial institutions to manage operational risk, giving example of a risk management strategy used by financial institutions to mitigate such risk. 3. what is the rold of the core principles of effective bank supervision as it relates to operational risk, in the effective management of financial institutions.arrow_forwardPlease show all units, work, and steps needed to solve this problem I need answer typing clear urjent no chatgpt used pls i will give 5 Upvotes.arrow_forwardIM.82 A distributor of industrial equipment purchases specialized compressors for use in air conditioners. The regular price is $50, however, the manufacturer of this compressor offers quantity discounts per the following discount schedule: Option Plan Quantity Discount A 1 - 299 0% B 300 - 1,199 0.50% C 1,200+ 1.50% The distributor pays $56 each time it places an order with the manufacturer. Holding costs are negligible (none) but they do earn 10% annual interest on all cash balances (meaning there will be a financial opportunity cost when they put cash into inventory). Annual demand is expected to be 10,750 units. When there is no quantity discount (Option Plan A, the first row of the schedule listed above), what is the adjusted order quantity? (Display your answer to the nearest whole number.) 491 Based on your answer to the previous question, and based on the annual demand as stated above, what will be the annual ordering costs? (Display your answer to the…arrow_forward
- Purchasing and Supply Chain ManagementOperations ManagementISBN:9781285869681Author:Robert M. Monczka, Robert B. Handfield, Larry C. Giunipero, James L. PattersonPublisher:Cengage LearningMarketingMarketingISBN:9780357033791Author:Pride, William MPublisher:South Western Educational Publishing
- Practical Management ScienceOperations ManagementISBN:9781337406659Author:WINSTON, Wayne L.Publisher:Cengage,Contemporary MarketingMarketingISBN:9780357033777Author:Louis E. Boone, David L. KurtzPublisher:Cengage Learning
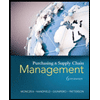
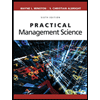
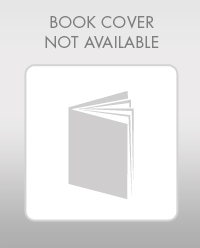