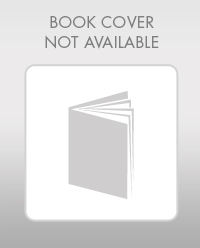
Precision Machining Technology
3rd Edition
ISBN: 9781337795302
Author: Peter, Hoffman.
Publisher: Cengage Learning,
expand_more
expand_more
format_list_bulleted
Concept explainers
Textbook Question
thumb_up100%
Chapter 8.2, Problem 1RQ
Name the two primary machine axes on most CNC turning machines.
- a. ________________
- b. ________________
Expert Solution & Answer

Want to see the full answer?
Check out a sample textbook solution
Students have asked these similar questions
B/40 The body is constructed of a uniform square plate, a uniform straight rod, a uniform quarter‐circular rod, and a particle (negligible dimensions). If each part has the indicated mass, determine the mass moments of inertia of the body about the x‐, y‐, and z‐axes. Answer Given.
(read image) Answer:
(read image) Answer Given
Chapter 8 Solutions
Precision Machining Technology
Ch. 8.1 - What is an ATC?Ch. 8.1 - What is an MCU and what is its function?Ch. 8.1 - Briefly describe a ball screw and a linear guide.Ch. 8.1 - Explain the benefits of using the absolute...Ch. 8.1 - Explain the benefits of using the incremental...Ch. 8.1 - Which coordinate system uses an angle and a...Ch. 8.1 - What is the name for the type of motor used to...Ch. 8.1 - Supposing a programmer, using absolute mode,...Ch. 8.1 - What is a modal code?Ch. 8.1 - What is another name for the Cartesian coordinate...
Ch. 8.1 - List four G-codes and describe their functions. a....Ch. 8.1 - List four M-codes and describe their functions. a....Ch. 8.1 - What is the name of the character that ends each...Ch. 8.1 - Explain the purpose of the safe-start portion of a...Ch. 8.2 - Name the two primary machine axes on most CNC...Ch. 8.2 - Explain the difference between a turning center...Ch. 8.2 - List the three common types of live toolholders....Ch. 8.2 - Name three major collet styles used in...Ch. 8.2 - Name three types of workholding devices for...Ch. 8.2 - Name three major styles of turning machines....Ch. 8.2 - Explain why some workholding devices can be run at...Ch. 8.2 - Explain the difference between an OD grooving tool...Ch. 8.2 - When machining workpieces made from bar stock,...Ch. 8.2 - Describe how a sub-spindle can be used to increase...Ch. 8.2 - How does a Swiss turning center differ from a...Ch. 8.3 - Write the X- and Z-axis coordinates for the part...Ch. 8.3 - To perform a facing cut using a tool with a nose...Ch. 8.3 - Explain the difference between rigid tapping and...Ch. 8.3 - How must the feed rate for tapping using a...Ch. 8.3 - Describe what happens to a concave radius (fillet)...Ch. 8.3 - Describe what happens to an outside chamfer when...Ch. 8.3 - If a G1 code command is programmed partway through...Ch. 8.3 - List and briefly describe the two methods for...Ch. 8.3 - Explain in your own words the difference between...Ch. 8.3 - In your own words, describe a canned cycle.Ch. 8.3 - List two types of canned cycles besides roughing...Ch. 8.4 - What machine mode is generally used to manually...Ch. 8.4 - MDI stands for _________ ___________ ________.Ch. 8.4 - Which must be set first, the tool geometry offset...Ch. 8.4 - What is the process called where a program is sent...Ch. 8.4 - Explain the purpose of homing.Ch. 8.4 - What is the process called when a new program is...Ch. 8.4 - When setting up a machine to run a program that...Ch. 8.4 - What does MCS stand for?Ch. 8.4 - What is used to adjust the clamping pressure of...Ch. 8.4 - What does MCS stand for?Ch. 8.4 - What does WCS stand for?Ch. 8.4 - A workpiece offset is the distance from __________...Ch. 8.5 - Explain the difference between a machining center...Ch. 8.5 - Name the two major types of ATCs and briefly...Ch. 8.5 - What are the two basic types of tapping...Ch. 8.5 - What are the three most common styles of collets...Ch. 8.5 - What are the two basic types of tapping...Ch. 8.5 - Prob. 6RQCh. 8.5 - A programmable indexing fixture creates a fourth...Ch. 8.5 - A _______ ________ uses interchangeable tooling...Ch. 8.5 - Briefly describe a tombstone used for CNC...Ch. 8.5 - A custom ______ can be designed and built to hold...Ch. 8.5 - The combination of the machining operations...Ch. 8.6 - What are the three major axes used during CNC mill...Ch. 8.6 - What command would be given to turn on the spindle...Ch. 8.6 - What G-code designates IPM feed rate mode? IPR...Ch. 8.6 - What is the purpose of a clearance plane in CNC...Ch. 8.6 - What is the purpose of work coordinate systems?Ch. 8.6 - Briefly define linear interpolation.Ch. 8.6 - If during the last operation on a part, a G1 code...Ch. 8.6 - Briefly describe the use of I and J for the arc...Ch. 8.6 - Write two blocks of code that could be used to...Ch. 8.6 - Briefly explain the difference between rigid and...Ch. 8.6 - Define the initial plane for a canned drilling or...Ch. 8.6 - A G98 in a canned cycle sets the return point to...Ch. 8.6 - A _____ code is used to cancel a canned cycle.Ch. 8.6 - What two codes are used to activate automatic...Ch. 8.6 - What two codes are used to activate automatic...Ch. 8.6 - What code is used to cancel automatic cutter...Ch. 8.7 - Which must be set first, a work offset or a tool...Ch. 8.7 - What mode is used to manually enter programs into...Ch. 8.7 - What is the process called when a program is sent...Ch. 8.7 - Explain what may occur that makes it necessary to...Ch. 8.7 - Explain the purpose of homing.Ch. 8.7 - What is the process called when a new program is...Ch. 8.7 - What are two actions that can be taken during the...Ch. 8.7 - When automatic cutter radius compensation is used...Ch. 8.7 - Which machine mode allows short, temporary program...Ch. 8.7 - Which machine mode is used to run the machine...Ch. 8.7 - What are the two controls on the machine's control...Ch. 8.7 - What control panel feature can be used to slow a...Ch. 8.8 - Prob. 1RQCh. 8.8 - Prob. 2RQCh. 8.8 - What are the three primary steps in creating a CNC...Ch. 8.8 - Prob. 4RQCh. 8.8 - What is the definition of entity?Ch. 8.8 - Why should a toolpath be verified on the screen of...Ch. 8.8 - What is a post-processor used for?Ch. 8.8 - What is it called when mutiple touching entities...Ch. 8.8 - What type of cutting tool is usually used for...
Knowledge Booster
Learn more about
Need a deep-dive on the concept behind this application? Look no further. Learn more about this topic, mechanical-engineering and related others by exploring similar questions and additional content below.Similar questions
- B/16. The plane area shown in the top portion of the figure is rotated 180° about the x‐axis to form the body of revolution of mass m shown in the lower portion of the figure. Determine the mass moment of inertia of the body about the x‐axis. Answer Givenarrow_forward(read image) Answer:arrow_forward(read image) Answer:arrow_forward
- 2nd Law of Thermodynamics A 1.5-ft3 rigid tank contains saturated refrigerant-134 at 170 psia. Initially, 20 percent of the volume isoccupied by liquid and the rest by vapor. A valve at the top of the tank is now opened, and vapor is allowedto escape slowly from the tank. Heat is transferred to the refrigerant such that the pressure inside the tankremains constant. The valve is closed when the last drop of liquid in the tank is vaporized. Determine thetotal heat transfer for this process.arrow_forwardDraw the shear and bending-moment diagrams for the beam and loading shown, and determine the maximum normal stress due to bending. 4.8 kips/ft 32 kips B C D E I Hinge 8 ft. 2 ft 5 ft 5 ft W12 x 40arrow_forward2nd Law of Thermodynamics A rigid, insulated tank that is initially evacuated is connected through a valve to the supply line that carrieshelium at 300 kPa and 140◦C. Now the valve is opened, and helium is allowed to flow into the tank until thepressure reaches 300 kPa, at which point the valve is closed. Determine the flow work of the helium in thesupply line and the final temperature of the helium in the tank.arrow_forward
- Draw the shear and bending-moment diagrams for the beam and loading shown, and determine the maximum normal stress due to bending. 5 kips 10 kips B I W14 x 22 -5 ft -8 ft 5 ft-arrow_forward2nd Law of Thermodynamics Liquid water at 200 kPa and 25◦C is heated in a chamber by mixing it with superheated steam at 200 kPaand 250◦C. cold water enters the chamber at a rate of 2 kg/s. If the mixture leaves the mixing chamber at50◦C, determine the mass flow rate of the superheated steam required.arrow_forwardThe 2nd Law of Thermodynamics Refrigerant-134a enters the compressor of a refrigeration system as saturated vapor at 0.16 MPa, and leavesas superheated vapor at 0.9 MPa and 70◦C at a rate of 0.08 kg/s. Determine the rates of energy transfers bymass into and out of the compressor. Assume the kinetic and potential energies are negligible.arrow_forward
- 2nd Law of Thermodynamics Water enters the tubes of a cold plate at 65◦C with an average velocity of 50 ft/min and leaves at 110◦F. Thediameter of the tubes is 0.2 in. Assuming 20 percent of the heat generated is dissipated from the componentsto the surroundings by convection and radiation, and the remaining 80 percent is removed by the coolingwater, determine the amount of heat generated by the electronic devices mounted on the cold plate.arrow_forwardThe 2nd Law of Thermodynamics Refrigerant-134a enters a diffuser steadily as saturated vapor 500 kPa with a velocity of 170 m/s, and it leavesat 600 kPa and 50◦C. the refrigerant is gaining heat at a rate of 2.5 kJ/s as it passes through the diffuser. Ifthe exit area is 75 percent greater than the inlet area, determine (a) the exit velocity (b) the mass flow rate of the refrigerant.arrow_forward2nd Law of Thermodynamics Refrigerant-134a is throttled from the saturated liquid state at 850 kPa to a pressure of 200 kPa. Determinethe temperature drop during this process and the final specific volume of the refrigerant.arrow_forward
arrow_back_ios
SEE MORE QUESTIONS
arrow_forward_ios
Recommended textbooks for you
- Precision Machining Technology (MindTap Course Li...Mechanical EngineeringISBN:9781285444543Author:Peter J. Hoffman, Eric S. Hopewell, Brian JanesPublisher:Cengage Learning
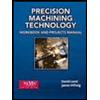
Precision Machining Technology (MindTap Course Li...
Mechanical Engineering
ISBN:9781285444543
Author:Peter J. Hoffman, Eric S. Hopewell, Brian Janes
Publisher:Cengage Learning
Types of Manufacturing Process | Manufacturing Processes; Author: Magic Marks;https://www.youtube.com/watch?v=koULXptaBTs;License: Standard Youtube License