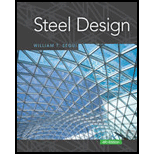
(a)
The maximum service load using LRFD.

Answer to Problem 7.6.5P
The maximum service load is
Explanation of Solution
Given:
Tension member is
Steel Used is
Thickness of gusset plate is
Diameter of the bolt is
Ratio of live load to dead load is
Calculation:
The properties for
The ultimate tensile stress is
The yield strength is
Write the expression for cross-sectional area of the bolt.
Here, cross-sectional area of the bolt is
Substitute
Write the expression for nominal shear capacity of one bolt.
Here, nominal shear stress of one bolt is
Substitute
Write the expression for slip critical shear strength per bolt for class A surfaces.
Here, the ratio of the mean actual bolt pre-tensioned to the specified bolt pre-tensioned is
Substitute
Write the expression to calculate the nominal bearing strength of an edge bolt
Here, nominal bearing strength is
With the upper limit of nominal bearing strength of the edge bolt,
Write the expression to calculate the value of
Here, height of the bolt is
Write the expression to calculate the value of
Here, spacing between the bolts is
Write the expression to calculate the height of the bolt.
Calculate the value of
Substitute
Calculate the value of
Substitute
Calculate the nominal bearing strength for edge bolts.
Substitute
Calculate the upper limit of nominal bearing strength for edge bolts.
Substitute
Thus, the minimum value of
Write the expression to calculate the nominal bearing strength of inner bolt
With the upper limit of nominal bearing strength of the inner bolt,
Calculate the value of
Substitute
Calculate the nominal bearing strength for inner bolts.
Substitute
Calculate the upper limit of nominal bearing strength for inner bolts.
Substitute
Thus, the minimum value of
Write the expression to calculate the nominal strength in yielding.
Here, yield strength is
Substitute
Here, the width of the section is
Substitute
Write the expression to calculate the diameter of the hole.
Here, diameter of the hole is
Substitute
Write the expression to calculate the effective area.
Here, area of holes is
Substitute
Substitute
Write the expression for nominal strength for fracture.
Here, nominal strength for fracture is
Substitute
Write the expression for gross shear area.
Here, thickness of member is
Substitute
Write the expression for the net area in shear.
Here, net area in shear is
Substitute
Substitute
Write the expression for net area in tension.
Here, tension length is
Substitute
Write the expression for the nominal strength in block shear.
Here, reduction factor is
Substitute
Write the expression for nominal shear strength in gross shear.
Here, nominal shear strength in gross shear is
Substitute
Thus, the nominal shear strength is taken as
Write the expression for design strength per bolt.
Here, load reduction factor is
Substitute
Calculate the design strength for slip per bolt.
Substitute
Write the expression for total bolt strength.
Here, total strength is
Substitute
Write the expression for design strength in yielding.
Here, load reduction factor in yielding is
Substitute
Write the expression for design strength for fracture.
Here, design strength for fracture is
Substitute
Write the expression for design strength for block shear.
Here, design strength for block shear is
Substitute
Thus, the bolt strength is
Write the expression for total factored load.
Here, total factored load is
Substitute
Thus,
Calculate the total load.
Conclusion:
Thus, the maximum service load is
(b)
The maximum service load using ASD.

Answer to Problem 7.6.5P
The maximum service load is
Explanation of Solution
Calculation:
Write the expression to calculate the allowable strength for shear per bolt.
Here, allowable strength is
Substitute
Calculate the allowable strength for slip per bolt.
Substitute
Calculate the allowable strength for bearing per bolt.
Substitute
Thus, the minimum value of allowable strength for shear is considered and is equal to
Write the expression for total bolt strength.
Substitute
Write the expression for allowable strength in yielding.
Here, safety factor is
Substitute
Calculate the allowable strength in fracture.
Substitute
Calculate the allowable strength for block shear.
Substitute
Calculate the total bolt strength in yielding.
Substitute
Thus, the design strength is
Write the expression for total factored load.
Here, allowable factored load is
Substitute
Conclusion:
Thus, the maximum service load is
Want to see more full solutions like this?
Chapter 7 Solutions
Bundle: Steel Design, Loose-leaf Version, 6th + Mindtap Engineering, 1 Term (6 Months) Printed Access Card
- Consider a pool of saturated water at atmospheric pressure. The base of the pool is made of thick polished copper square plate of length 1 m. To generate steam, exhaust gas is flowing underneath and parallel to the base plate with velocity 3 m/s and average temperate of 1090°C. The bottom surface the plate is at constant temperature of 110°. Use the properties of air for exhaust gas. a) Determine the boiling heat transfer rate. b) Determine the temperature of the top surface of the plate. Comment on the results. c) Examine the impact of your assumptions on your solutions. (what will change if any of the assumptions is not valid?)arrow_forward-The axial deflection pipe in inches. -The lateral deflection of the beam in inches -The total deflection of the beam like structure in inches ? all to 4 sig figs AI did not help. as i input what i get im not sure if its a rounding error or what.arrow_forward1. For the foundation shown below: Qapp = 60 kips (Load obtained from structural engineer) 1.5 ft G.W.T. 3 ft Poorly Graded Sand (SP): Ym 115 pcf (above G.W.T.) Ysat 125 pcf (below G.W.T.) c' = 0, ' = 35° K Square footing, 4' x 4' Foundation Dimension Information: 1-ft x 1-ft square concrete column. 1-ft thick "foot" flanges. Yconc=150 pcf *Assume weight of reinforcing steel included in unit weight of concrete. *Assume compacted backfill weighs the same as in-situ soil. Assume this foundation is being designed for a warehouse that had a thorough preliminary soil exploration. Using the general bearing capacity equation: a. Calculate the gross applied bearing pressure, the gross ultimate bearing pressure, and determine if the foundation system is safe using a gross bearing capacity ASD approach. Please include the weight of the foundation, the weight of the backfill soil, and the effect of the uplift pressure caused by the presence of the water table in your bearing capacity…arrow_forward
- ٢٥ ٠٥:٤٠١٠ 2025 ChatGPT VivaCut Onet Puzzle مسلم X Excel JPG I❤> PDF Copilot Chat Bot PDF2IMG iLovePDF NokoPrint O.O StudyX ☑ W CapCut Candy Crush DeepSeek Word ☐ Saga 啡 AcadAl ل TikTokarrow_forwardRefer to the figure below. Given: L = 7 m, y = 16.7 kN/m², and ø' = 30°. L L3 ση Sand γ $' D T LA L σε σε IN P Sand 1. Calculate the theoretical depth of penetration, D. (Enter your answer to three significant figures.) D= m 2. Calculate the maximum moment. (Enter your answer to three significant figures.) Mmax kN-m/marrow_forwardWhy is it important for construction project managers to be flexible when dealing with the many variable factors that pop up in a project?arrow_forward
- What are some reasons for why a company would accelerate a construction project?arrow_forwardFor the design of a shallow foundation, given the following: Soil: ' = 20° c' = 52 kN/m² Unit weight, y = 15 kN/m³ Modulus of elasticity, E, = 1400 kN/m² Poisson's ratio, μs = 0.35 Foundation: L=2m B=1m Df = 1 m Calculate the ultimate bearing capacity. Use the equation: 1 - qu = c' NcFcs Fcd Fcc +qNqFqsFqdFqc + ½√BN√Fãs F√dƑxc 2 For '=20°, Nc = 14.83, N₁ = 6.4, and N₁ = 5.39. (Enter your answer to three significant figures.) qu = kN/m²arrow_forwardA 2.0 m wide strip foundation carries a wall load of 350 kN/m in a clayey soil where y = 15 kN/m³, c' = 5.0 kN/m² and ' = 23°. The foundation depth is 1.5 m. For ' = 23°: Nc = 18.05; N₁ = 8.66; Ny = = = 8.20. Determine the factor of safety using the equation below. qu= c' NcFcs FcdFci+qNqFqsFq 1 F + gd. 'qi 2 ·BN√· FF γί Ysyd F (Enter your answer to three significant figures.) FS =arrow_forward
- Steel Design (Activate Learning with these NEW ti...Civil EngineeringISBN:9781337094740Author:Segui, William T.Publisher:Cengage Learning
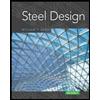