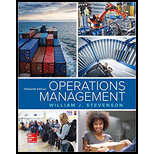
a)
To determine: The standard time for the operation.
Introduction: The amount of the dependency on human effort by an organization in terms of achieving its goals is given by the work design. It is directly linked to the productivity of an organization where good work design helps in achieving high productivity.
a)

Answer to Problem 10P
Explanation of Solution
Given information:
Element | Performance rating | Observations (minutes per cycles) | Allowance | |||||
1 | 2 | 3 | 4 | 5 | 6 | |||
1 | 1.1 | 1.2 | 1.17 | 1.16 | 1.22 | 1.24 | 1.15 | 0.15 |
2 | 1.15 | 0.83 | 0.87 | 0.78 | 0.82 | 0.85 | 0 | 0.15 |
3 | 1.05 | 0.58 | 0.53 | 0.52 | 0.59 | 0.6 | 0.54 | 0.15 |
Formula:
Calculation of standard time of operation:
Element | Performance rating | Observations (minutes per cycles) | Allowance | Observed time | Normal time | Afjob | Standard time | |||||
1 | 2 | 3 | 4 | 5 | 6 | |||||||
1 | 1.1 | 1.2 | 1.17 | 1.16 | 1.22 | 1.24 | 1.15 | 0.15 | 1.198 | 1.317 | 1.15 | 1.52 |
2 | 1.15 | 0.83 | 0.87 | 0.78 | 0.82 | 0.85 | 0 | 0.15 | 0.83 | 0.954 | 1.15 | 1.10 |
3 | 1.05 | 0.58 | 0.53 | 0.52 | 0.59 | 0.6 | 0.54 | 0.15 | 0.564 | 0.592 | 1.15 | 0.68 |
Standard time for operation | 3.29 |
Excel Worksheet:
Element 1:
Observed time is calculated by taking mean for the 1.2, 1.17, 1.16, 1.22, 1.24 and 1.15 which gives 1.198.
Normal time is calculated by multiplying observed timing, 1.198 and performance rating, 1.1 which yields 1.317 minutes.
Allowance factor is calculated by adding 1 with the allowance factor 0.15 to give 1.15.
Standard time for element 1 is calculated by multiplying normal time of 1.317 minutes with allowance factor of 1.15 which gives 1.52 minutes.
Same process applies for element 2 and 3 which yields the standard times as 1.10 and 0.68. The standard time for operation is obtained by adding 1.52, 1.10 and 1.68 minutes which gives 3.29 minutes.
Hence, the standard time for the operation is 3.29 minutes.
b)
To determine: The number of observations for element 2.
Introduction: The amount of the dependency on human effort by an organization in terms of achieving its goals is given by the work design. It is directly linked to the productivity of an organization where good work design helps in achieving high productivity.
b)

Answer to Problem 10P
Explanation of Solution
Given information:
Element | Performance rating | Observations (minutes per cycles) | Allowance | |||||
1 | 2 | 3 | 4 | 5 | 6 | |||
1 | 1.1 | 1.2 | 1.17 | 1.16 | 1.22 | 1.24 | 1.15 | 0.15 |
2 | 1.15 | 0.83 | 0.87 | 0.78 | 0.82 | 0.85 | 0 | 0.15 |
3 | 1.05 | 0.58 | 0.53 | 0.52 | 0.59 | 0.6 | 0.54 | 0.15 |
Confidence= 95.5%
1% of true value
Formula:
Calculation of number of observations for element A:
In the above formula the sample standard deviation is calculated by,
Calculation of standard deviation:
Element 2 | Differences | Square of differences | Standard deviation |
0.83 | 0 | 0 | 0.0339 |
0.87 | 0.04 | 0.0016 | |
0.78 | -0.05 | 0.0025 | |
0.82 | -0.01 | 0.0001 | |
0.85 | 0.02 | 0.0004 | |
Mean=0.83 | SSQ=0.0046 |
Excel worksheet:
Z value for confidence interval of 95.5% is 2.00.
The confidence interval
- Using z = 2.00:
The number of observations from the standard z table for confidence level of 95.5% is calculated by dividing the product of 2.00 and 0.0339 with product of 0.01 and 0.83 and squaring the resultant which gives 66.7272.
- Using z = 2.01:
The number of observations from the standard z table for confidence level of 95.5% is calculated by dividing the product of 2.01 and 0.0339 with product of 0.01 and 0.83 and squaring the resultant which gives 67.3962.
Hence, the number of observation is 68.
c)
To determine: The number of observations needed to estimate the mean time for element 2 within 0.01 minute of its true value.
Introduction: The amount of the dependency on human effort by an organization in terms of achieving its goals is given by the work design. It is directly linked to the productivity of an organization where good work design helps in achieving high productivity.
c)

Answer to Problem 10P
Explanation of Solution
Given information:
Element | Performance rating | Observations (minutes per cycles) | Allowance | |||||
1 | 2 | 3 | 4 | 5 | 6 | |||
1 | 1.1 | 1.2 | 1.17 | 1.16 | 1.22 | 1.24 | 1.15 | 0.15 |
2 | 1.15 | 0.83 | 0.87 | 0.78 | 0.82 | 0.85 | 0 | 0.15 |
3 | 1.05 | 0.58 | 0.53 | 0.52 | 0.59 | 0.6 | 0.54 | 0.15 |
Confidence= 95.5%
0.10 minute of actual value.
Formula:
Calculation of number of observations for element C:
In the above formula the sample standard deviation is calculated by,
Z value for confidence interval of 95.5% is 2.00.
The confidence interval
- Using z = 2.00:
The number of observations from the standard z table for confidence level of 95.5 is calculated by dividing the product of 2.00 and 0.0339 with 0.01 and squaring the resultant which gives 45.9684.
- Using z = 2.00:
The number of observations from the standard z table for confidence level of 95.5 is calculated by dividing the product of 2.01 and 0.0339 with 0.01 and squaring the resultant which gives 46.4292.
Hence, the number of observations needed to estimate the mean time for element 2 within 0.01 minute of its true value is 46.
Want to see more full solutions like this?
Chapter 7 Solutions
OPERATIONS MANAGEMENT(LL)-W/CONNECT
- The deaths are included in the discharges; this includes deaths occurring in less than 48 hours and postoperative deaths. Rehabilitation had 362 discharges, 22 deaths, 1<48 hours, 0 Postoperative. what is the gross death rate for the rehabilitation service?arrow_forwardA copy machine is available 24 hours a day. On a typical day, the machine produces 100 jobs. Each job takes about 3 minutes on the machine, 2 minutes of which is processing time and 1 minute is setup time (logging in, defining the job). About 20 percent of the jobs need to be reworked, in which case the setup time and the processing time have to be repeated. The remainder of the time, the equipment is idle. What is the OEE of the equipment?arrow_forwardHow do you think we can keep updating Toyota's ideas as new technologies come out and what customers want keeps changing?arrow_forward
- Given how TPS has helped change things in so many fields, do you think there are parts of it that might be hard to use in areas that aren’t about making things, like in healthcare or services? If so, why do you think that might be?arrow_forwardDo you feel there is anything positive about rework?arrow_forwardDo you think technology can achieve faster setup times? How would it be implemented in the hospital workforce?arrow_forward
- In your experience or opinion, do you think process changes like organizing workspaces make a bigger difference, or is investing in technology usually the better solution for faster setups?arrow_forwardHave you seen rework done in your business, and what was done to prevent that from occurring again?arrow_forwardResearch a company different than case studies examined and search the internet and find an example of a business that had to rework a process. How was the organization affected to rework a process in order to restore a good flow unit? Did rework hurt a process or improve the organization's operational efficiency? • Note: Include a reference with supportive citations in the discussion reply in your post.arrow_forward
- Setup time is very important in affecting a process and the capacity of a process. How do you reduce setup time? Give examples of reducing setup time. Please Provide a referenecearrow_forwardDo you think TPS was successful? If so, how? Are there other companies that have used TPS? If so, give examples. Please provide a referencearrow_forwardGiven the significant impact on finances, production timelines, and even equipment functionality, as you pointed out, what do you believe is the most effective single strategy a company can implement to significantly reduce the occurrence of rework within their operations?arrow_forward
- Management, Loose-Leaf VersionManagementISBN:9781305969308Author:Richard L. DaftPublisher:South-Western College PubUnderstanding Management (MindTap Course List)ManagementISBN:9781305502215Author:Richard L. Daft, Dorothy MarcicPublisher:Cengage Learning
- Practical Management ScienceOperations ManagementISBN:9781337406659Author:WINSTON, Wayne L.Publisher:Cengage,
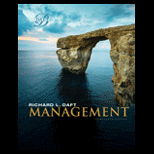
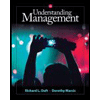
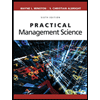