
Intermediate Financial Management (MindTap Course List)
13th Edition
ISBN: 9781337395083
Author: Eugene F. Brigham, Phillip R. Daves
Publisher: Cengage Learning
expand_more
expand_more
format_list_bulleted
Question
Chapter 23, Problem 1P
a)
Summary Introduction
To determine: Economic order quality (EOQ).
b)
Summary Introduction
To determine: Maximum inventory
c)
Summary Introduction
To determine: Average inventory
d)
Summary Introduction
To determine: The number days to place the order.
Expert Solution & Answer

Want to see the full answer?
Check out a sample textbook solution
Students have asked these similar questions
What are the implications of missing a credit card payment in finance?
Omni Advisors, an international pension fund manager, uses the concepts of purchasing power parity (PPP) and the International Fisher Effect (IFE) to forecast spot exchange rates. Omni gathers the financial information as follows: Base price level 100 Current U.S. price level 105 Current South African price level 111 Base rand spot exchange rate $ 0.188 Current rand spot exchange rate $ 0.171 Expected annual U.S. inflation 7% Expected annual South African inflation 5% Expected U.S. one-year interest rate 10% Expected South African one-year interest rate 8% Required:
a. The current ZAR spot rate in USD that would have been forecast by PPP.Note: Do not round intermediate calculations. Round your answer to 4 decimal places.
b. Using the IFE, the expected ZAR spot rate in USD one year from now.Note: Do not round intermediate calculations. Round your answer to 4 decimal places.
c. Using PPP, the expected ZAR spot rate in USD four years from now.Note: Do not round intermediate calculations.…
Delta Company, a U.S. MNC, is contemplating making a foreign capital expenditure in South Africa. The initial cost of the project is ZAR11,000. The annual cash flows over the five-year economic life of the project in ZAR are estimated to be 3,300, 4,300, 5,290, 6,280, and 7,250. The parent firm's cost of capital in dollars is 9,5 percent. Long-run inflation is forecasted to be 3 percent per annum
in the United States and 7 percent in South Africa. The current spot foreign exchange rate is ZAR per USD = 3.75.
Required:.
Calculating the NPV in ZAR using the ZAR equivalent cost of capital according to the Fisher effect and then converting to USD at the current spot rate. - NPV in USD using fisher effect
Converting all cash flows from ZAR to USD at purchasing power parity forecasted exchange rates and then calculating the NPV at the dollar cost of capital. - NPV in USD using PPP rates
Are the two USD NPs different or the same?
What is the NPV in dollars if the actual pattern of ZAR per…
Chapter 23 Solutions
Intermediate Financial Management (MindTap Course List)
Knowledge Booster
Learn more about
Need a deep-dive on the concept behind this application? Look no further. Learn more about this topic, finance and related others by exploring similar questions and additional content below.Similar questions
- What is the 50/30/20 budgeting rule in finance?arrow_forwardHow do student loans impact long-term financial health?arrow_forwardWith regard to foreign currency translation methods used by foreign MNCs, Multiple Choice a. foreign currency translation methods are generally only used by U.S. based MNCs since foreign firms have a built-in hedge by being foreign. b. are generally the same methods used by U.S.-based firms. c. are exactly the same methods used by U.S.-based firms since GAAP is GAAP. d. none of the options.arrow_forward
- Cray Research sold a supercomputer to the Max Planck Institute in Germany on credit and invoiced €11.60 million payable in six months. Currently, the six-month forward exchange rate is $1.18 per euro and the foreign exchange adviser for Cray Research predicts that the spot rate is likely to be $113 per euro in six months.Required: a. What is the expected gain/loss from a forward hedge?Note: A Negative value should be indicated with a minus sign. Do not round intermediate calculations. Round your final answer in whole dollars not in millions.arrow_forwardWhat is the time value of money and how is it calculated? need answer!arrow_forwardHelp me in this question! What is the time value of money and how is it calculated?arrow_forward
arrow_back_ios
SEE MORE QUESTIONS
arrow_forward_ios
Recommended textbooks for you
- Intermediate Financial Management (MindTap Course...FinanceISBN:9781337395083Author:Eugene F. Brigham, Phillip R. DavesPublisher:Cengage LearningCornerstones of Cost Management (Cornerstones Ser...AccountingISBN:9781305970663Author:Don R. Hansen, Maryanne M. MowenPublisher:Cengage LearningPrinciples of Accounting Volume 2AccountingISBN:9781947172609Author:OpenStaxPublisher:OpenStax College
- Managerial Accounting: The Cornerstone of Busines...AccountingISBN:9781337115773Author:Maryanne M. Mowen, Don R. Hansen, Dan L. HeitgerPublisher:Cengage LearningManagerial AccountingAccountingISBN:9781337912020Author:Carl Warren, Ph.d. Cma William B. TaylerPublisher:South-Western College PubFinancial And Managerial AccountingAccountingISBN:9781337902663Author:WARREN, Carl S.Publisher:Cengage Learning,
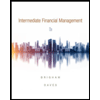
Intermediate Financial Management (MindTap Course...
Finance
ISBN:9781337395083
Author:Eugene F. Brigham, Phillip R. Daves
Publisher:Cengage Learning
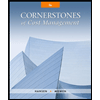
Cornerstones of Cost Management (Cornerstones Ser...
Accounting
ISBN:9781305970663
Author:Don R. Hansen, Maryanne M. Mowen
Publisher:Cengage Learning
Principles of Accounting Volume 2
Accounting
ISBN:9781947172609
Author:OpenStax
Publisher:OpenStax College
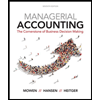
Managerial Accounting: The Cornerstone of Busines...
Accounting
ISBN:9781337115773
Author:Maryanne M. Mowen, Don R. Hansen, Dan L. Heitger
Publisher:Cengage Learning
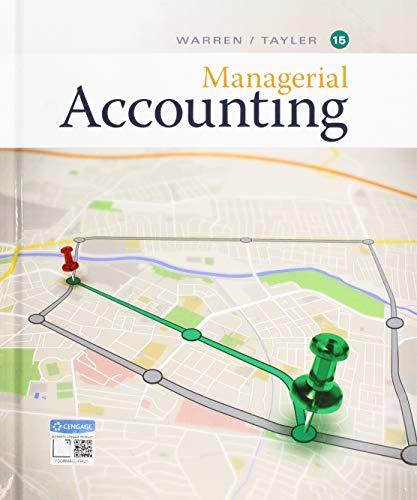
Managerial Accounting
Accounting
ISBN:9781337912020
Author:Carl Warren, Ph.d. Cma William B. Tayler
Publisher:South-Western College Pub
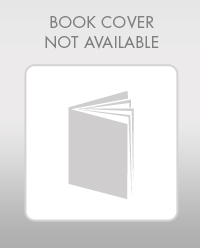
Financial And Managerial Accounting
Accounting
ISBN:9781337902663
Author:WARREN, Carl S.
Publisher:Cengage Learning,
Inventory management; Author: The Finance Storyteller;https://www.youtube.com/watch?v=DZhHSR4_9B4;License: Standard Youtube License