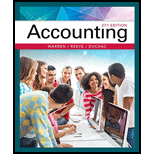
Concept explainers
Capital expenditures budget
On January 1, 20Y2, the controller of Omicron Inc. is planning capital expenditures for the years 20Y2-20Y5. The following interviews helped the controller collect the necessary information for the capital expenditures budget:
Director of Facilities A construction contract was signed in late 20Y1 for the construction of a new factory building at a contract cost of $10,000,000. The construction is scheduled to begin in 20Y2 and be completed in 20Y3.
Vice President of Manufacturing: Once the new factory building is finished, we plan to purchase $15 million m equipment in late 20Y3. I expect that an additional $200,000 will be needed early in the following year (20Y4) to test and install the equipment before we can begin production. If sales continue to grow, I expect we'll need to invest another $1,000,000 in equipment in 20Y5.
Chief Operating Officer: We have really been growing lately. I wouldn't be surprised if we need to expand the size of our new factory building in 20YS by at least 35%. Fortunately, we expect inflation to have minimal impact on construction costs over the next four years In addition. I would expect the cost of the expansion to be proportional to the size of the expansion.
Director of Information Systems: We need to upgrade our information systems to wireless network technology. It doesn't make sense to do this until after the new factory building is completed and producing product. During 20Y4, once the factory is up and running, we should equip the whole facility with wireless technology. I think it would cost us $800,000 today to install the technology. However, prices have been dropping by 25% per year, so it should be less expensive at a later date.
Chief Financial Officer: I am excited about our long-term prospects. My only short-term concern is managing our
Use this interview information to prepare a capital expenditures budget for Omicron Inc. for the years 20Y2-20Y5.

Trending nowThis is a popular solution!

Chapter 22 Solutions
Accounting
- Could you help me solve this financial accounting question using appropriate calculation techniques?arrow_forwardPlease explain the solution to this general accounting problem with accurate explanations.arrow_forwardBrown Corporation has 850 defective units of a product that cost $4.25 per unit in direct costs and $8.40 per unit in indirect costs when produced last year. The units can be sold as scrap for $5.30 per unit or reworked at an additional cost of $2.75 per unit and sold at the full price of $14.90. The incremental net income (loss) from the choice of reworking the units would be____.arrow_forward
- Andy Manufacturing produces plastic and metal kitchen utensils. In preparing the current budget, Andy's management estimated a total of $380,000 in manufacturing overhead costs and 19,000 direct labor hours for the coming year. In December, Andy's accountants reported actual manufacturing overhead incurred of $93,000 and 18,200 direct labor hours used during the year. Andy applies overhead based on direct labor hours. Required: What was Andy's predetermined overhead rate for the year? How much manufacturing overhead did Andy apply during the year?arrow_forwardWhat is the correct option ? for general accounting questionarrow_forwardPlease provide the correct answer to this general accounting problem using valid calculations.arrow_forward
- Managerial AccountingAccountingISBN:9781337912020Author:Carl Warren, Ph.d. Cma William B. TaylerPublisher:South-Western College PubFinancial And Managerial AccountingAccountingISBN:9781337902663Author:WARREN, Carl S.Publisher:Cengage Learning,Survey of Accounting (Accounting I)AccountingISBN:9781305961883Author:Carl WarrenPublisher:Cengage Learning
- Principles of Accounting Volume 2AccountingISBN:9781947172609Author:OpenStaxPublisher:OpenStax College
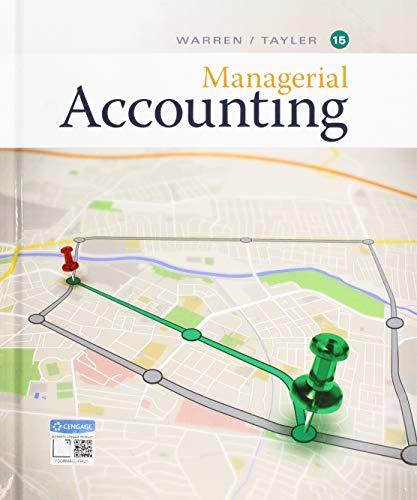
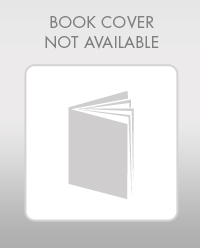
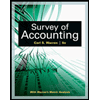