Concept explainers
Management at the Kerby Corporation has determined the following aggregated demand
An employee can produce an average of 10 units per month. Each worker on the payroll costs $2,000 in regular—time wages per month. Undertime is paid at the same rate as regular time. In accordance with the labor contract in force, Kerby Corporation does not work overtime or use subcontracting. Kerby can hire and train a new employee for $2,000 and lay off one for $500. Inventory costs $32 per unit on hand at the end of each month. At present, 140 employees are on the payroll and anticipation inventory is zero.
- Prepare a production plan that only uses a level workforce and anticipation inventory as its supply options. Minimize the inventory left over at the end of the year. Layoffs. undertime, vacations, subcontracting, backorders, and stockouts are not options. The plan may call for a one-time adjustment of the workforce before month 1 begins.
- Prepare a production plan using a chase strategy, relying only on hiring and layoffs.
- Prepare a mixed—strategy production plan that uses only a level workforce and anticipation inventory through month 7 (an adjustment of the workforce may be made before month 1 begins) then switches to a chase strategy for months 8 through 12.
- Contrast these three plans on the basis of annual costs.

Want to see the full answer?
Check out a sample textbook solution
Chapter 10 Solutions
OPERATIONS MANAGEMENT CUSTOM ACCESS
Additional Business Textbook Solutions
Principles of Operations Management: Sustainability and Supply Chain Management (10th Edition)
Corporate Finance (4th Edition) (Pearson Series in Finance) - Standalone book
Business Essentials (12th Edition) (What's New in Intro to Business)
Marketing: An Introduction (13th Edition)
Essentials of MIS (13th Edition)
Horngren's Cost Accounting: A Managerial Emphasis (16th Edition)
- As part of your new role, as a strategy consultant and member of the steering committee, discuss what logistics and transportation strategies you will execute to achieve operational efficiencies and facilitate economic growth in SA. The committee would like to have a implementable strategic transport and logistics plan to realise the roadmap vision based on the subsection numbering given below! QUESTION ONE Introduction: Must include an overview and history of South Africa's Road, rail and freight transport network. Marks 5arrow_forward1.2 What are the current freight and logistic challenges on the road network 10 1.3 Discuss key relevant financials of infrastructure, industries and revenue resulting in this logistics crisis. 15arrow_forwardAs part of your new role, as a strategy consultant and member of the steering committee, discuss what logistics and transportation strategies you will execute to achieve operational efficiencies and facilitate economic growth in SA. The committee would like to have a implementable strategic transport and logistics plan to realise the roadmap vision based on the subsection numbering given below: QUESTION ONE Marks 5 Introduction: Must include an overview and history of South Africa's Road, rail and freight transport network. 1.1 Assess what led to such logistical inefficiencies/collapse of a previously world class freight network 10 1.2 What are the current freight and logistic challenges on the road network 10 1.3 Discuss key relevant financials of infrastructure, industries and revenue resulting in this logistics crisis. 15 1.4 Discuss how the key stakeholder partnerships - current and future are critical to government and business as part of the overall intermodal transport strategy.…arrow_forward
- What are the current freight and logistic challenges on the road network Discuss key relevant financials of infrastructure, industries and revenue resulting in this logistics crisis. 10 15arrow_forward1.5 If you examine the freight supply and value chain, what transport and infrastructure strategies and 25 plans need to be implemented to improve operation efficiencies and reduce costs. 5 1.6 15 Discuss how implementation of a strategic intermodal transport plan can further unlock and improve South Africa's GDP and international recognition.arrow_forwardA certain business process is no longer providing the desired benefits, therefore it needs to be re-designed through a project. You have to: Choose the business process to re-design and specify the reason why it is no longer satisfactory. Ask ChatGPT (or a similar generative AI; specify name and version) to create a Project Charter for the process redesign project. Modify and refine the response provided by the AI tool ensuring it complies with the instructor’s lesson, with particular focus on the project goals, project objectives, and deliverables (remember: project objectives must be SMART!). Your work must be delivered in the following format: a)Describe the business process to re-design (example: “The process of hiring and integrating new employees into the Sales Administration department”. Do not exceed 20 words) b)Specify the reason to re-design the business process which is already in place (describe the reason why the current process is no longer satisfactory, for…arrow_forward
- The demand for subassembly S is 100 units in week 7. Each unit of S requires 1 unit of T and 2 units of U. Each unit of T requires 1 unit of V, 2 units of W, and 1 unit of X. Finally, each unit of U requires 2 units of Y and 3 units of Z. One firm manufactures all items. It takes 2 weeks to make S, 1 week to make T, 2 weeks to make U, 2 weeks to make V, 3 weeks to make W, 1 week to make X, 2 weeks to make Y, and 1 week to make Z. Click the icon to view the product structure and the time-phased product structure. Click the icon to view the on-hand inventory. Construct a net material requirements plan using on-hand inventory (enter your responses as whole numbers). Item 1 2 3 Week 4 Lead Time 5 6 7 (weeks) S Gross req On hand Net req Order receipt Order release T Gross req On hand Net req Order receipt Order release Gross rea 100 100arrow_forwardIt is January 1 of year 0, and Merck is trying to determine whether to continue development of a newdrug. The following information is relevant. You can assume that all cash flows occur at the ends of therespective years.■ Clinical trials (the trials where the drug is tested on humans) are equally likely to be completed in year1 or 2.■ There is an 80% chance that clinical trials will succeed. If these trials fail, the FDA will not allow thedrug to be marketed.■ The cost of clinical trials is assumed to follow a triangular distribution with best case $100 million,most likely case $150 million, and worst case $250 million. Clinical trial costs are incurred at the end ofthe year clinical trials are completed.■ If clinical trials succeed, the drug will be sold for five years, earning a profit of $6 per unit sold.■ If clinical trials succeed, a plant will be built during the same year trials are completed. The cost of theplant is assumed to follow a triangular distribution with best case $1…arrow_forward1) Under “Costs of Quality”, costs associated with quality can be classified into four categories: appraisal, prevention, internal failures, and external failures. The costs of quality for Corley Motors Logistics is given in the table. Cost Elements Amount Checking outbound boxes for errors $31,000 Quality planning $10,625 Downtime due to conveyor/computer problems $342,125 Incoming product inspection $21,000 Customer complaint rework $33,000 Correcting erroneous orders before shipping $36,550 Quality training of associates $25,925 Correction of typographical errors--pick tickets $11,475 a) Classify the quality cost elements given in the table into the different quality cost categories (prevention, appraisal, internal failure, external failure). b) Total the quality costs in each of the different quality cost categories (prevention, appraisal, internal failure, external failure). c) Using a) and b), suggest which areas…arrow_forward
- Note: In chapter 9, section 9.4 of the Stevenson text, the costs of quality are covered; chapter 9 Stevenson lecture power point slide 7 touches upon this topic; see lecture video, 3.55 mins to 4.54 mins. 2) The production process at Hansa Ceylon Coffee fills boxes with dark arabica coffee. The data for the fill weight (in ounces) of eight samples are presented below. A sample size of six was used. The firm’s operations analyst wants to construct X-bar and R-charts to monitor the filling process. Sample Sample Mean Sample Range 1 15.80 0.42 2 16.10 0.38 3 16.02 0.08 4 15.95 0.15 5 16.12 0.42 6 16.18 0.23 7 15.87 0.36 8 16.20 0.40 a) Calculate the upper and lower control limits for the X-bar chart. b) Calculate the upper and lower control limits for the R chart. c) Is the process under control? Why or why not? Note: In chapter 10, section 10.3 of the Stevenson text, control charts for variables are…arrow_forwardDo the inherent differences between private and public sector objectives—profit versus publicgood—render private sector category management practices unsuitable for public sectorpurchasing, where open tendering is the norm?You have now undergone the Category Management classes and your superiors have requestedfor your input on how to integrate some of the learnings into the public sector policy. Discuss and elaborate what are the activities and governance you would introduce in yourrecommendations without violating the principle of transparency and accountability withinyour organisation. This is based on Singapore context. Pls provide a draft with explanation, examples and useful links for learning purposes. Citations will be good too. This is a module in SUSS called category management and supplier evaluationarrow_forwardTravelling and working internationally can lead to a life of adventure and unique career experiences. For businesses, selecting the right candidates to take on foreign assignments can propel, delay, or deny the success of the international ventures. As an international manager, identify key competencies you would look for in choosing expatriates. What might be some of their concerns in taking on overseas assignments? What are some best practices in supporting expats during and after their assignments?arrow_forward
- Practical Management ScienceOperations ManagementISBN:9781337406659Author:WINSTON, Wayne L.Publisher:Cengage,MarketingMarketingISBN:9780357033791Author:Pride, William MPublisher:South Western Educational PublishingPurchasing and Supply Chain ManagementOperations ManagementISBN:9781285869681Author:Robert M. Monczka, Robert B. Handfield, Larry C. Giunipero, James L. PattersonPublisher:Cengage Learning
- Management, Loose-Leaf VersionManagementISBN:9781305969308Author:Richard L. DaftPublisher:South-Western College Pub
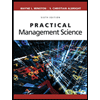
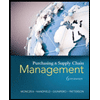
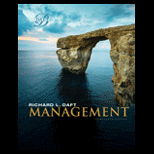