The figure shows a cutaway view of an assembly in which a solid bronze [G = 6,500 ksi] rod (1) is fitted inside of an aluminum alloy [G = 4,000 ksi] tube (2). The tube is attached to a fixed plate at C, and both the rod and the tube are welded to a rigid end plate at A. The rod diameter is d₁ = 1.65 in. The outside diameter of the tube is D2 = 3.6 in. and its wall thickness is t2 = 0.155 in. Overall dimensions of the assembly are a = 42 in. and b = 12 in. The allowable shear stresses for the bronze and aluminum materials are 9500 psi and 7800 psi, respectively. Further, the rotation angle of end B must be limited to a magnitude of 4.9°. Based on these constraints, what is the maximum torque Tg that can be applied at end B?
The figure shows a cutaway view of an assembly in which a solid bronze [G = 6,500 ksi] rod (1) is fitted inside of an aluminum alloy [G = 4,000 ksi] tube (2). The tube is attached to a fixed plate at C, and both the rod and the tube are welded to a rigid end plate at A. The rod diameter is d1 = 1.65 in. The outside diameter of the tube is D2 = 3.6 in. and its wall thickness is t2 = 0.155 in. Overall dimensions of the assembly are a = 42 in. and b = 12 in. The allowable shear stresses for the bronze and aluminum materials are 9500 psi and 7800 psi, respectively. Further, the rotation angle of end B must be limited to a magnitude of 4.9°. Based on these constraints, what is the maximum torque TB that can be applied at end B?
![The figure shows a cutaway view of an assembly in which a solid bronze [G = 6,500 ksi] rod (1) is fitted inside of
an aluminum alloy [G = 4,000 ksi] tube (2). The tube is attached to a fixed plate at C, and both the rod and the
tube are welded to a rigid end plate at A. The rod diameter is d₁ = 1.65 in. The outside diameter of the tube is
D₂ = 3.6 in. and its wall thickness is t2 = 0.155 in. Overall dimensions of the assembly are a = 42 in. and b = 12 in.
The allowable shear stresses for the bronze and aluminum materials are 9500 psi and 7800 psi, respectively.
Further, the rotation angle of end B must be limited to a magnitude of 4.9°. Based on these constraints, what is
the maximum torque TB that can be applied at end B?
Fixed
End
12
plate
plate
d₁
Rod (1)
Tube (2)
a
D₂
Answer:
TB =
A
Ib.in
b
TB
B](/v2/_next/image?url=https%3A%2F%2Fcontent.bartleby.com%2Fqna-images%2Fquestion%2F749be18b-22f2-4fe5-9f05-6fa35acbb4d0%2Fb42021c9-b397-4599-b3b7-fc85f6bf7202%2Fdffdu1h_processed.png&w=3840&q=75)

Step by step
Solved in 3 steps with 3 images

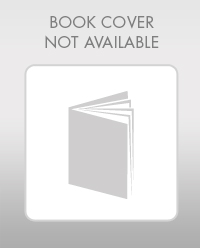
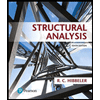
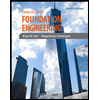
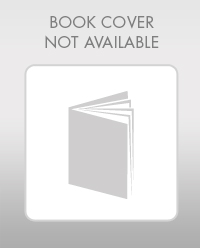
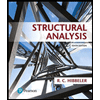
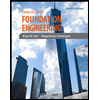
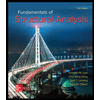
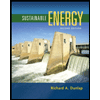
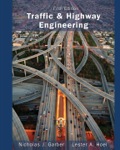