One unit of A is made of one unit of B and one unit of C. B is made of four units of C and one unit each of E and F. C is made of two units of D and one unit of E. E is made of three units of F. Item C has a lead time of one week; Items A, B, E, and F have two-week lead times; and Item D has a lead time of three weeks. Lot-for-lot (L4L) lot sizing is used for Items A, D, and E; lots of size 50, 100, and 50 are used for Items B, C, and F, respectively. Items A, C, D, and E have on-hand (beginning) inventories of 15, 55, 100, and 10, respectively; all other items have zero beginning inventory. We are scheduled to receive 10 units of A in Week 1, 100 units of C in Week 1, and 100 units of D in Week 3; there are no other scheduled receipts. If 50 units of A are required in week 10, use the low-level-coded bill-of-materials (product structure tree) to find the necessary planned-order releases for all components. (Leave the cells blank, whenever zero (0) is required.)
One unit of A is made of one unit of B and one unit of C. B is made of four units of C and one unit each of E and F. C is made of two units of D and one unit of E. E is made of three units of F. Item C has a lead time of one week; Items A, B, E, and F have two-week lead times; and Item D has a lead time of three weeks. Lot-for-lot (L4L) lot sizing is used for Items A, D, and E; lots of size 50, 100, and 50 are used for Items B, C, and F, respectively. Items A, C, D, and E have on-hand (beginning) inventories of 15, 55, 100, and 10, respectively; all other items have zero beginning inventory. We are
If 50 units of A are required in week 10, use the low-level-coded bill-of-materials (product structure tree) to find the necessary planned-order releases for all components. (Leave the cells blank, whenever zero (0) is required.)


Trending now
This is a popular solution!
Step by step
Solved in 2 steps

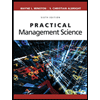
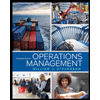
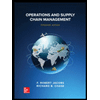
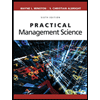
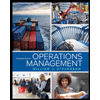
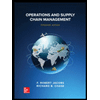
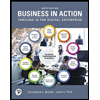
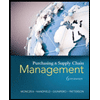
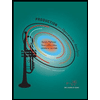