Labor Variances Cinturon Corporation produces high-quality leather belts. The company's plant in Boise uses a standard costing system and has set the following standards for materials and labor: Leather (3 strips @ $4) Direct labor (0.75 hr. @ $12) Rate variance $12.00 Total prime cost During the first month of the year, the Boise plant produced 92,000 belts. Actual leather purchased was 287,500 strips at $3.60 per strip. There were no beginning or ending inventories of leather. Actual direct labor was 79,200 hours at $15.00 per hour. Efficiency variance 9.00 Required: 1. Break down the total variance for labor into a rate variance and an efficiency variance using the columnar and formula approaches. Total variance $21.00 2. CONCEPTUAL CONNECTION As part of the investigation of the unfavorable variances, the plant manager interviews the production manager. The production manager complains strongly about the quality of the leather strips. He indicates that the strips are of lower quality than usual and that workers have to be more careful to avoid a belt with cracks and more time is required. Also, even with extra care, many belts have to be discarded and new ones produced to replace the rejects. This replacement work has also produced some overtime demands. What corrective action should the plant manager take? 1. Return to suppliers that provide the quality corresponding to the price standard. 2. Employ more skilled labor at a cost lesser than the savings made by buying cheap material and improve the product quality. 3. There is no need to change anything. The sales are not affected by this low quality of raw material.
Variance Analysis
In layman's terms, variance analysis is an analysis of a difference between planned and actual behavior. Variance analysis is mainly used by the companies to maintain a control over a business. After analyzing differences, companies find the reasons for the variance so that the necessary steps should be taken to correct that variance.
Standard Costing
The standard cost system is the expected cost per unit product manufactured and it helps in estimating the deviations and controlling them as well as fixing the selling price of the product. For example, it helps to plan the cost for the coming year on the various expenses.
Do Not provide hand written solution.
maintain accuracy


Trending now
This is a popular solution!
Step by step
Solved in 3 steps

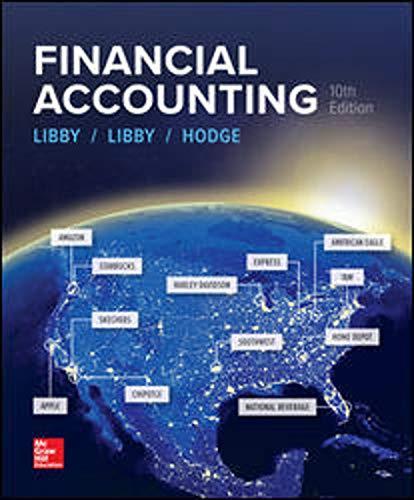
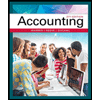
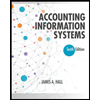
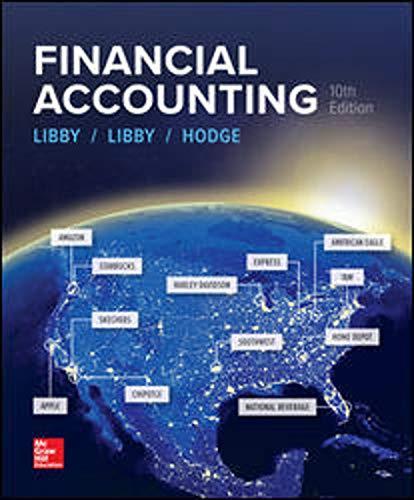
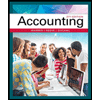
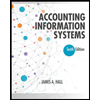
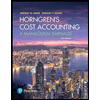
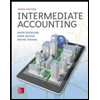
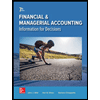