Kingston Industries manufactures two types of computerized scoreboards, custom and standard, each of which involves three manufacturing processes, namely: cutting, assembly and packaging. The company uses an activity-based costing system to allocate its overhead cost to the manufacturing processes. In using the activity-based costing system, the company uses four overhead activities; production set-up, procurement, quality control and materials management, in each production department. An activity analysis of the overhead related to the cutting department revealed the following estimated costs and activity bases for the four overhead activities: Activity Costs Activity Base $ Production set-up 43 200 Number of set-ups Procurement 156 000 Number of purchase orders Quality control 175 000 Number of inspections Materials management 150 000 Number of components Total 524 200 The activity based usage quantities for each product in the cutting department are as follows: Set-ups Purchase Orders Inspections Components Unit Volume Custom 400 1 000 2 000 300 5 000 Standard 80 200 500 100 5 000 Total 480 1 200 2 500 400 10 000 Determine an activity rate for each activity. Calculate the total overhead cost assigned to each product in the cutting department using the rates computed in part (i). Determine the unit activity (overhead) cost for each product in the cutting department.
Kingston Industries manufactures two types of computerized scoreboards, custom and standard, each of which involves three manufacturing processes, namely: cutting, assembly and packaging. The company uses an activity-based costing system to allocate its
In using the activity-based costing system, the company uses four overhead activities; production set-up, procurement, quality control and materials management, in each production department.
An activity analysis of the overhead related to the cutting department revealed the following estimated costs and activity bases for the four overhead activities:
Activity |
Costs Activity Base |
|
$ |
Production set-up |
43 200 Number of set-ups |
Procurement |
156 000 Number of purchase orders |
Quality control |
175 000 Number of inspections |
Materials management |
150 000 Number of components |
Total |
524 200 |
The activity based usage quantities for each product in the cutting department are as follows:
|
Set-ups |
Purchase Orders |
Inspections |
Components |
Unit Volume |
Custom |
400 |
1 000 |
2 000 |
300 |
5 000 |
Standard |
80 |
200 |
500 |
100 |
5 000 |
Total |
480 |
1 200 |
2 500 |
400 |
10 000 |
- Determine an activity rate for each activity.
- Calculate the total overhead cost assigned to each product in the cutting department using the rates computed in part (i).
- Determine the unit activity (overhead) cost for each product in the cutting department.
- Identify TWO other methods of costing manufactured goods.
- Explain, highlighting ONE distinct point why ABC is considered to be a more accurate method of costing.

Step by step
Solved in 2 steps with 1 images

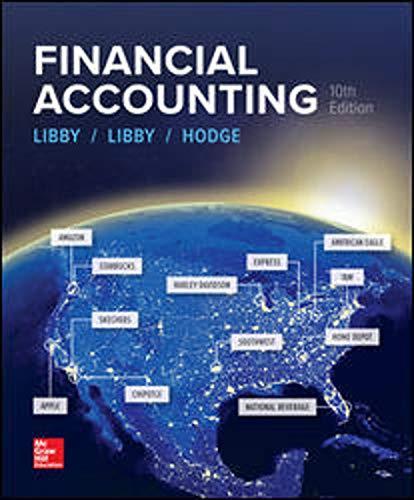
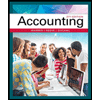
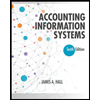
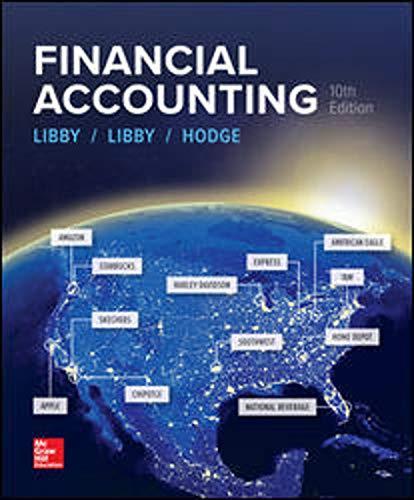
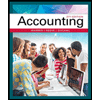
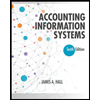
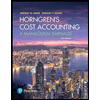
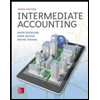
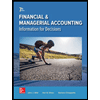