Hanks Inc. produces glass jars in a single department; the jars are then sold to candle manufacturers. All materials are added at the start of the process, and conversion costs are applied uniformly throughout che production process. Cost of Production Report Weighted Average Method (WAM) Equivalent Units of Production (EUP) Breakage commonly occurs at the end of the production process when a machine pushes air into the jars co form their openings. Hanks expects a maximum of 5 percent of the units started into production be "lost" during processing. For convenience, quantities will be discussed in terms of jars rather than raw material inputs. Recyclable shipping containers are provided by buyers and, therefore, are not a cost to Hanks Inc. Whole DM Production Data Beginning WIP Inventory Units Started Units CONVERSION 12,000 90,000 Units to Account For 102,000 The company uses the WA method of calculating equivalent units. Beginning WIP Inventory (completed) Started and Completed Units Completed Ending WIP Inventory Normal Spoilage (90,000 5%) Abnormal Spoilage (7,800-4,500) Units Accounted For 12,000 67,200 79,200 15,000 4,500 Below are the basic information for the month of June: 12,000 67,200 12,000 67,200 Jars 15,000 11,250 Beginning WIP Inventory (60% complete) 12,000 Started during month 90,000 3,300 102,000 3,300 3,300 Jars completed and transferred 79,200 97,500 93,750 Ending WIP Inventory (75% complete) 15,000 Spoiled jars 7,800 Cost Data Costs in Beginning WIP Inventory Current Period Costs Total Cost to Account For Divide by EUP Cost per WA EUP Costs 16,230 101,745 117,975 3,459 19,041 22,500 19,689 Beginning WIP Inventory Material 120,786 $ 16,230 140,475 Conversion 3,459 $ 19,689 97,500 93,750 1.45 1.21 0.24 Current period Material $101,745 Conversion 19,041 120,786 Cost Assignment Transferred Out (79,200*1.45) Ending WIP Inventory: Direct Material (15,000*1.21) Total cost to be accounted for $140,475 114,840 18,150 2,700 Conversion (11,250*0.24) Abnormal Loss (3,300*1.45) Total Cost Accounted For 20,850 4,785 140,475
Variance Analysis
In layman's terms, variance analysis is an analysis of a difference between planned and actual behavior. Variance analysis is mainly used by the companies to maintain a control over a business. After analyzing differences, companies find the reasons for the variance so that the necessary steps should be taken to correct that variance.
Standard Costing
The standard cost system is the expected cost per unit product manufactured and it helps in estimating the deviations and controlling them as well as fixing the selling price of the product. For example, it helps to plan the cost for the coming year on the various expenses.
Prepare the Cost of Production Report of Hanks, Inc. using the FIFO Costing Method. Refer to our sample problem for the given.


Trending now
This is a popular solution!
Step by step
Solved in 4 steps with 4 images

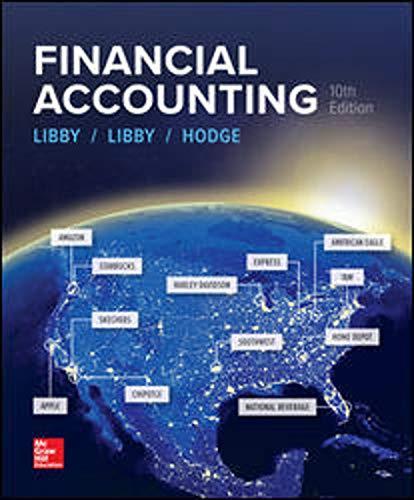
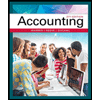
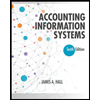
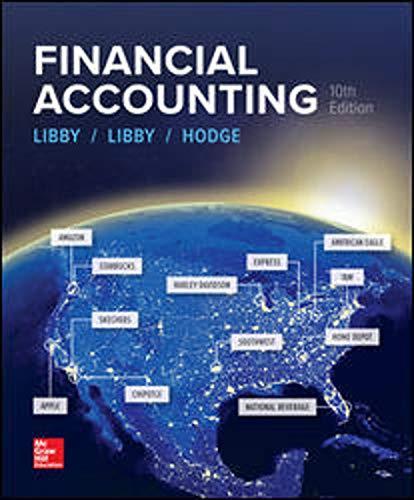
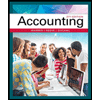
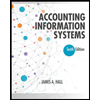
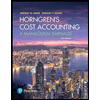
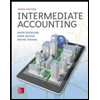
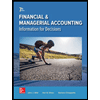