Grendizer Co. has received an enquiry from a customer for the supply of 500 units of a new product, product B22. Negotiations on the final price to charge the customer are in progress and the sales manager has asked you to supply relevant cost information. The following information is available: 1. Each unit of product B22 requires the following raw materials: a. Raw material type i. X:4kg ii. Y:6kg The company has 5,000 kg of material X currently in stock. This was purchased last year at a cost of $7 per kg. If not used to make product B22, this stock of X could either be sold for $7.50 per kg or converted at a cost of $1.50 per kg, so that it could be used as a substitute for another raw material, material Z, which the company requires for other production. The current purchase price per kilogram for materials is $9.50 for material Z and $8.25 per kg for material X. There are 10,000 kilograms of raw material Y in inventory, valued on a FIFO basis at a total cost of $142,750. Of this current inventory, 3,000 kilograms were purchased six months ago at a cost of $13.75 per kg. The rest of the inventory was purchased last month. Material Y is used regularly in normal production work. Since the last purchase of material Y a month ago, the company has been advised by the supplier that the price per kilogram has been increased by 4%. Each unit of product B22 requires the following number of labor hours in its manufacture: a. Type of labor: Skilled: 5 hours Unskilled: 3 hours (Paid @ $ 6 per hour) 5. There is a shortage of skilled labor, so that if production of B22 goes ahead it will be necessary to transfer skilled workers from other work to undertake it. The other work on which skilled workers are engaged at present is the manufacture of product B16. The selling price and variable cost information for B16 are as follows: $/unit $/unit Selling price. 100 Less: variable costs of production Skilled labour (3 hours) 24 Other variable costs 31 55 Contribution 45 The company has a surplus of unskilled workers who are paid a fixed wage for a 37-hour week. It is estimated that there are 900 hours of unused unskilled labor time available during the period of the contract. The balance of the unskilled labor requirements could be met by working overtime, which is paid at time and a half. The company absorbs production overheads by a machine hour rate. This absorption rate is $22.50 per hour, of which $8.75 is for variable overheads and the balance is for fixed overheads. If production of product B22 is undertaken, it is estimated that an extra $4,000 will be spent on fixed costs. Spare machining capacity is available and each unit of B22 will require two hours of machining time in its manufacture using the existing equipment. In addition, special finishing machines will be required for two weeks to complete the B22. These machines will be hired at a cost of $2,650 per week, and there will be no overhead costs associated with their use. Cash spending of $3,250 has been incurred already on development work for the production of B22. It is estimated that before production of the B22 begins, another $1,750 will have to be spent on development, making a total development cost of $5,000. Requirement: Calculate the minimum price that the company should be prepared to accept for the 500 units of product B22.
Process Costing
Process costing is a sort of operation costing which is employed to determine the value of a product at each process or stage of producing process, applicable where goods produced from a series of continuous operations or procedure.
Job Costing
Job costing is adhesive costs of each and every job involved in the production processes. It is an accounting measure. It is a method which determines the cost of specific jobs, which are performed according to the consumer’s specifications. Job costing is possible only in businesses where the production is done as per the customer’s requirement. For example, some customers order to manufacture furniture as per their needs.
ABC Costing
Cost Accounting is a form of managerial accounting that helps the company in assessing the total variable cost so as to compute the cost of production. Cost accounting is generally used by the management so as to ensure better decision-making. In comparison to financial accounting, cost accounting has to follow a set standard ad can be used flexibly by the management as per their needs. The types of Cost Accounting include – Lean Accounting, Standard Costing, Marginal Costing and Activity Based Costing.
Grendizer Co. has received an enquiry from a customer for the supply of 500 units of a new product, product B22. Negotiations on the final price to charge the customer are in progress and the sales manager has asked you to supply relevant cost information. The following information is available:
1. Each unit of product B22 requires the following raw materials: a. Raw material type
i. X:4kg
ii. Y:6kg
-
The company has 5,000 kg of material X currently in stock. This was purchased last year at a cost of $7 per kg. If not used to make product B22, this stock of X could either be sold for $7.50 per kg or converted at a cost of $1.50 per kg, so that it could be used as a substitute for another raw material, material Z, which the company requires for other production. The current purchase price per kilogram for materials is $9.50 for material Z and $8.25 per kg for material X.
-
There are 10,000 kilograms of raw material Y in inventory, valued on a FIFO basis at a total cost of $142,750. Of this current inventory, 3,000 kilograms were purchased six months ago at a cost of $13.75 per kg. The rest of the inventory was purchased last month. Material Y is used regularly in normal production work. Since the last purchase of material Y a month ago, the company has been advised by the supplier that the price per kilogram has been increased by 4%.
-
Each unit of product B22 requires the following number of labor hours in its manufacture:
a. Type of labor:
-
Skilled: 5 hours
-
Unskilled: 3 hours (Paid @ $ 6 per hour)
5. There is a shortage of skilled labor, so that if production of B22 goes ahead it will be necessary to transfer skilled workers from other work to undertake it. The other work on which skilled workers are engaged at present is the manufacture of product B16. The selling price and variable cost information for B16 are as follows:
$/unit $/unit
Selling price. 100
Less: variable costs of production
Skilled labour (3 hours) 24
Other variable costs 31
55
Contribution 45
-
The company has a surplus of unskilled workers who are paid a fixed wage for a 37-hour week. It is estimated that there are 900 hours of unused unskilled labor time available during the period of the contract. The balance of the unskilled labor requirements could be met by working overtime, which is paid at time and a half.
-
The company absorbs production
overheads by a machine hour rate. This absorption rate is $22.50 per hour, of which $8.75 is for variable overheads and the balance is for fixed overheads. If production of product B22 is undertaken, it is estimated that an extra $4,000 will be spent on fixed costs. Spare machining capacity is available and each unit of B22 will require two hours of machining time in its manufacture using the existing equipment. In addition, special finishing machines will be required for two weeks to complete the B22. These machines will be hired at a cost of $2,650 per week, and there will be no overhead costs associated with their use. -
Cash spending of $3,250 has been incurred already on development work for the production of B22. It is estimated that before production of the B22 begins, another $1,750 will have to be spent on development, making a total development cost of $5,000.
Requirement: Calculate the minimum price that the company should be prepared to accept for the 500 units of product B22.

Step by step
Solved in 6 steps with 5 images

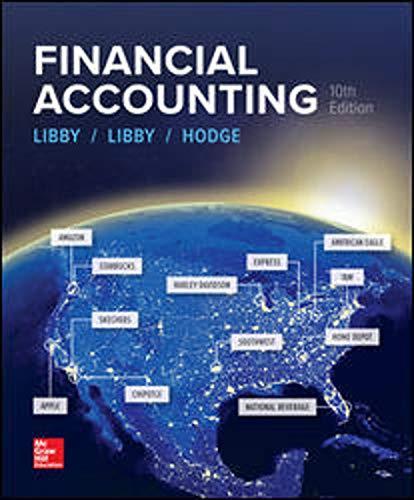
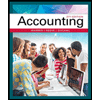
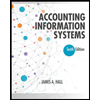
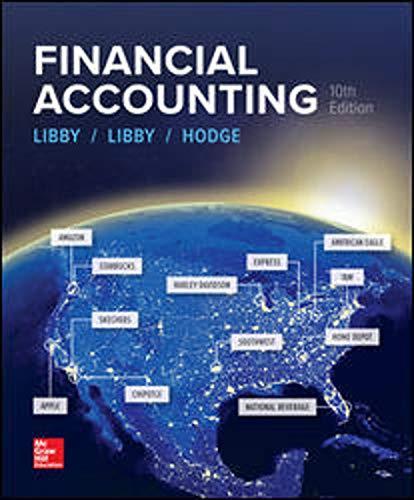
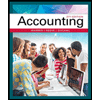
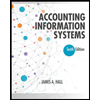
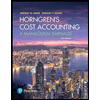
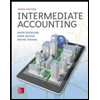
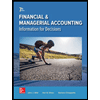