Dwayne Cole, owner of Florida firm that manufactures display cabinets, develops an 8-month aggregate plan. Demand and capacity (in units) are forecast as follows: Сарacity Jan Feb Mar Apr Мay Jun Jul Aug Source (Units) Regular 235 255 290 300 300 290 300 290 Time Overtime 20 24 26 24 30 28 30 30 Subcontract| 12 16 15 17 17 19 19 20 Demand 255 294 321 301 330 320 345 340 The cost of production each unit is $1000 on regular time, $1300 on overtime, and $1800 on a subcontract. Inventory carrying cost is $200 per unit per month. There is no beginning or ending inventory in stock, and no backorders are permitted from period to period. Let the production workforce vary by using regular time first, then overtime and then subcontracting. a) Set up a production plan that minimizes cost by producing exactly what the demand in each month. This plan allows no backorders or inventory. What is this plan's cost? b) Through better planning, regular time production can be set at exactly the same amount, 275 units, per month. If demand cannot be met, there is no cost assigned to shortages and they will not be filled. Does this alter the solution? c) If overtime costs per unit rise from $1300 to $1400, will your answer to part a) change? What if overtime costs then fall to $1200?
Dwayne Cole, owner of Florida firm that manufactures display cabinets, develops an 8-month aggregate plan. Demand and capacity (in units) are forecast as follows: Сарacity Jan Feb Mar Apr Мay Jun Jul Aug Source (Units) Regular 235 255 290 300 300 290 300 290 Time Overtime 20 24 26 24 30 28 30 30 Subcontract| 12 16 15 17 17 19 19 20 Demand 255 294 321 301 330 320 345 340 The cost of production each unit is $1000 on regular time, $1300 on overtime, and $1800 on a subcontract. Inventory carrying cost is $200 per unit per month. There is no beginning or ending inventory in stock, and no backorders are permitted from period to period. Let the production workforce vary by using regular time first, then overtime and then subcontracting. a) Set up a production plan that minimizes cost by producing exactly what the demand in each month. This plan allows no backorders or inventory. What is this plan's cost? b) Through better planning, regular time production can be set at exactly the same amount, 275 units, per month. If demand cannot be met, there is no cost assigned to shortages and they will not be filled. Does this alter the solution? c) If overtime costs per unit rise from $1300 to $1400, will your answer to part a) change? What if overtime costs then fall to $1200?
Practical Management Science
6th Edition
ISBN:9781337406659
Author:WINSTON, Wayne L.
Publisher:WINSTON, Wayne L.
Chapter2: Introduction To Spreadsheet Modeling
Section: Chapter Questions
Problem 20P: Julie James is opening a lemonade stand. She believes the fixed cost per week of running the stand...
Related questions
Question

Transcribed Image Text:Dwayne Cole, owner of Florida firm that manufactures display cabinets, develops an 8-month
aggregate plan. Demand and capacity (in units) are forecast as follows:
Сараcity
Jan
Feb
Mar
Apr
Маy
Jun
Jul
Aug
Source
(Units)
Regular
235
255
290
300
300
290
300
290
Time
30
19
Overtime
20
Subcontract 12
24
26
24
30
28
30
16
15
17
17
19
20
Demand
255
294
321
301
330
320
345
340
The cost of production each unit is $1000 on regular time, $1300 on overtime, and $1800 on a
subcontract. Inventory carrying cost is $200 per unit per month. There is no beginning or
ending inventory in stock, and no backorders are permitted from period to period. Let the
production workforce vary by using regular time first, then overtime and then subcontracting.
a) Set up a production plan that minimizes cost by producing exactly what the demand in
each month. This plan allows no backorders or inventory. What is this plan's cost?
b) Through better planning, regular time production can be set at exactly the same amount,
275 units, per month. If demand cannot be met, there is no cost assigned to shortages
and they will not be filled. Does this alter the solution?
c) If overtime costs per unit rise from $1300 to $1400, will your answer to part a) change?
What if overtime costs then fall to $1200?
Expert Solution

This question has been solved!
Explore an expertly crafted, step-by-step solution for a thorough understanding of key concepts.
This is a popular solution!
Trending now
This is a popular solution!
Step by step
Solved in 5 steps with 4 images

Recommended textbooks for you
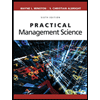
Practical Management Science
Operations Management
ISBN:
9781337406659
Author:
WINSTON, Wayne L.
Publisher:
Cengage,
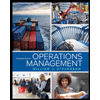
Operations Management
Operations Management
ISBN:
9781259667473
Author:
William J Stevenson
Publisher:
McGraw-Hill Education
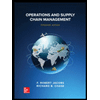
Operations and Supply Chain Management (Mcgraw-hi…
Operations Management
ISBN:
9781259666100
Author:
F. Robert Jacobs, Richard B Chase
Publisher:
McGraw-Hill Education
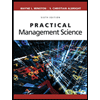
Practical Management Science
Operations Management
ISBN:
9781337406659
Author:
WINSTON, Wayne L.
Publisher:
Cengage,
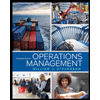
Operations Management
Operations Management
ISBN:
9781259667473
Author:
William J Stevenson
Publisher:
McGraw-Hill Education
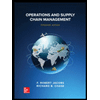
Operations and Supply Chain Management (Mcgraw-hi…
Operations Management
ISBN:
9781259666100
Author:
F. Robert Jacobs, Richard B Chase
Publisher:
McGraw-Hill Education
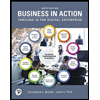
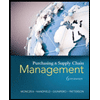
Purchasing and Supply Chain Management
Operations Management
ISBN:
9781285869681
Author:
Robert M. Monczka, Robert B. Handfield, Larry C. Giunipero, James L. Patterson
Publisher:
Cengage Learning
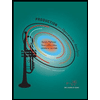
Production and Operations Analysis, Seventh Editi…
Operations Management
ISBN:
9781478623069
Author:
Steven Nahmias, Tava Lennon Olsen
Publisher:
Waveland Press, Inc.