CUSTOM FABRICATIONS INC.(STAND-ALONE PC-BASEDACCOUNTING SYSTEM)(Prepared by Will Richens and MichaelCatchpole, Lehigh University)CUSTOM FABRICATIONS Inc. is a bicyclemanufacturing firm founded in 2000 that currentlyemploys 126 people. The company produces custombicycles in its factory located near Los Angeles, CA.Each bicycle is tailored to a rider based on a numberof different measurements, including height, weight,inseam, and arm length. These measurements aretaken at 30 professional bicycle shops around SouthernCalifornia, which are certified to size CUSTOMFABRICATIONS cycles. By accepting orders onlythrough licensed dealers, CUSTOM FABRICATIONSensures that each bike matches its rider precisely.CUSTOM FABRICATIONS’ custom bikesare considered extremely high quality and the companytakes pride in using only the best componentssourced from around the world. Accordingly, CUSTOMFABRICATIONS purchases from a cast ofhundreds of suppliers, chosen for their commitmentto quality and reliability. Demand for CUSTOM FABRICATIONS’ cycleshas grown exponentially in recent years. The surge indemand was somewhat unexpected and the company’sfactory has been operating at capacity for over a year.As a result, current orders face a production backlog ofapproximately 5–6 weeks. The company’s operationshave been further hampered by severe inefficienciesand control weaknesses attributed to its legacyaccounting system. Your firm has been hired as anoutside consultant to suggest improvements in thecompany’s accounting procedures. The followingparagraphs describe the company’s expenditure cycle.Purchases SystemAll purchases of raw materials are initiated in theCUSTOMFABRICATIONS’ purchasing department. A clerk in the department monitors inventory levelsfrom his PC, which is linked to the inventory subsidiaryledger. Once a part needs to be replenished, he createsa hard-copy purchase order. One copy is mailed to thevendor, a blind copy of the purchase order is sent to thewarehouse, and the third copy is filed in the purchasingdepartment.Typically within 3–5 business days, the warehousereceives the ordered parts and the packing slip fromthe vendor, which the warehouse clerk reconcileswith the blind copy of the purchase order. Once thereconciliation is complete, the warehouse clerk preparesa three-part hard-copy receiving report statingthe quantity and condition of the items received. Onecopy of the receiving report is sent to the generalledger department to update the digital inventorycontrol account. The second copy is sent to theaccounts payable department, and the third is sentto the purchasing department to update the inventorysubsidiary ledger.Within a week, the mail room receives the supplier’sinvoice, which is immediately sent to the accounts payabledepartment. The AP clerk reconciles the invoicewith the receiving report and then records a liability inthe AP subsidiary ledger from the department PC.Finally, the clerk prints an AP summary from the terminaland sends it to the general ledger clerk. Cash Disbursements SystemThe accounts payable clerk regularly checks theaccounts payable subsidiary account at his terminalto ensure timely payment to vendors. For those itemsdue for payment, he sends approval in the form of apayment voucher to the cash disbursementsdepartment.For control purposes, cash disbursements are processedmanually. The details of the check arerecorded in the hard-copy cash disbursements journal,and the check is mailed to the vendor. The clerkthen prepares a journal voucher and sends it to thegeneral ledger.Once the general ledger clerk receives the journalvoucher, the AP summary, and the receiving report,she updates the affected general ledger accountsfrom the department PC.Requireda. Create a data flow diagram of the current system.b. Create a system flowchart of the existing system.c. Analyze the physical internal control weaknessesin the system in details . d. Describe the risks associated with these controlweaknesses.e. Prepare a system flowchart of a redesignedcomputer-based system that resolves thecontrol weaknesses that you identified. Explainyour solution.
Process Costing
Process costing is a sort of operation costing which is employed to determine the value of a product at each process or stage of producing process, applicable where goods produced from a series of continuous operations or procedure.
Job Costing
Job costing is adhesive costs of each and every job involved in the production processes. It is an accounting measure. It is a method which determines the cost of specific jobs, which are performed according to the consumer’s specifications. Job costing is possible only in businesses where the production is done as per the customer’s requirement. For example, some customers order to manufacture furniture as per their needs.
ABC Costing
Cost Accounting is a form of managerial accounting that helps the company in assessing the total variable cost so as to compute the cost of production. Cost accounting is generally used by the management so as to ensure better decision-making. In comparison to financial accounting, cost accounting has to follow a set standard ad can be used flexibly by the management as per their needs. The types of Cost Accounting include – Lean Accounting, Standard Costing, Marginal Costing and Activity Based Costing.
CUSTOM FABRICATIONS INC.
(STAND-ALONE PC-BASED
ACCOUNTING SYSTEM)
(Prepared by Will Richens and Michael
Catchpole, Lehigh University)
CUSTOM FABRICATIONS Inc. is a bicycle
manufacturing firm founded in 2000 that currently
employs 126 people. The company produces custom
bicycles in its factory located near Los Angeles, CA.
Each bicycle is tailored to a rider based on a number
of different measurements, including height, weight,
inseam, and arm length. These measurements are
taken at 30 professional bicycle shops around Southern
California, which are certified to size CUSTOM
FABRICATIONS cycles. By accepting orders only
through licensed dealers, CUSTOM FABRICATIONS
ensures that each bike matches its rider precisely.
CUSTOM FABRICATIONS’ custom bikes
are considered extremely high quality and the company
takes pride in using only the best components
sourced from around the world. Accordingly, CUSTOM
FABRICATIONS purchases from a cast of
hundreds of suppliers, chosen for their commitment
to quality and reliability. Demand for CUSTOM FABRICATIONS’ cycles
has grown exponentially in recent years. The surge in
demand was somewhat unexpected and the company’s
factory has been operating at capacity for over a year.
As a result, current orders face a production backlog of
approximately 5–6 weeks. The company’s operations
have been further hampered by severe inefficiencies
and control weaknesses attributed to its legacy
accounting system. Your firm has been hired as an
outside consultant to suggest improvements in the
company’s accounting procedures. The following
paragraphs describe the company’s expenditure cycle.
Purchases System
All purchases of raw materials are initiated in the
CUSTOMFABRICATIONS’ purchasing department. A clerk in the department monitors inventory levels
from his PC, which is linked to the inventory subsidiary
ledger. Once a part needs to be replenished, he creates
a hard-copy purchase order. One copy is mailed to the
vendor, a blind copy of the purchase order is sent to the
warehouse, and the third copy is filed in the purchasing
department.
Typically within 3–5 business days, the warehouse
receives the ordered parts and the packing slip from
the vendor, which the warehouse clerk reconciles
with the blind copy of the purchase order. Once the
reconciliation is complete, the warehouse clerk prepares
a three-part hard-copy receiving report stating
the quantity and condition of the items received. One
copy of the receiving report is sent to the general
ledger department to update the digital inventory
control account. The second copy is sent to the
accounts payable department, and the third is sent
to the purchasing department to update the inventory
subsidiary ledger.
Within a week, the mail room receives the supplier’s
invoice, which is immediately sent to the accounts payable
department. The AP clerk reconciles the invoice
with the receiving report and then records a liability in
the AP subsidiary ledger from the department PC.
Finally, the clerk prints an AP summary from the terminal
and sends it to the general ledger clerk. Cash Disbursements System
The accounts payable clerk regularly checks the
accounts payable subsidiary account at his terminal
to ensure timely payment to vendors. For those items
due for payment, he sends approval in the form of a
payment voucher to the cash disbursements
department.
For control purposes, cash disbursements are processed
manually. The details of the check are
recorded in the hard-copy cash disbursements journal,
and the check is mailed to the vendor. The clerk
then prepares a journal voucher and sends it to the
general ledger.
Once the general ledger clerk receives the journal
voucher, the AP summary, and the receiving report,
she updates the affected general ledger accounts
from the department PC.
Required
a. Create a data flow diagram of the current system.
b. Create a system flowchart of the existing system.
c. Analyze the physical internal control weaknesses
in the system in details . d. Describe the risks associated with these control
weaknesses.
e. Prepare a system flowchart of a redesigned
computer-based system that resolves the
control weaknesses that you identified. Explain
your solution.

Trending now
This is a popular solution!
Step by step
Solved in 5 steps with 5 images

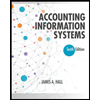
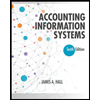