A Veterans Administration (VA) hospital needs to decide which type of boiler fuel system will most efficiently provide the required steam energy output for heating, laundry, and sterilization purposes. The present boilers were installed in the early 1970s and are now obsolete. Much of the auxiliary equipment is also old and requires repair. Because of these general conditions, an engineering recommendation was made to replace the entire plant with a new boiler-plant building that would house modern equipment. The cost of demolishing the old boiler plant would be almost a complete loss, as the salvage value of the scrap steel and used brick is estimated to be only about $1,000. The VA hospital's engineer finally selected two alternative proposals as being worthy of more intensive analysis. The hospital's annual energy requirement, measured in termsof steam output, is approximately 145,000,000 pounds of steam. As a general rule for analysis, 1 pound of steam is approximately 1,000 BTUs, and 1 cubic foot of natural gas is approximately 1,000 BTUs. The two alternatives are as follows: Proposal 1: Build a new coal-fired boiler plant, which would cost $2.570,300. To meet the requirements for particulate emission asset by the Environmental Protection Agency (EPA), the new coal-fired boiler, even if it burned lowsulfur coal, would need an electrostatic precipitator, which would cost approximately $145,000. The new plant would last for 20 years. One pound of dry coal yields about 14,300 BTUs. To convert the 145,000,000 pounds of steam energy into the common unit of BTUs, it is necessary to multiply by 1,000. To find BTU input requirements, it is necessary to divide by the relative boiler efficiency for type of fuel. The boiler efficiency for coal is 0.75. The coal price is estimated to be $125 per metricton.Proposal 2: Build a gas-fired boiler plant with No. 2 fuel oil as a standby.This system would cost $1,289,340 with an expected service life of 20 years.Since small household or commercial users entirely dependent on gas forenergy have priority, large plants must have oil switch-over capabilities. Ithas been estimated that 6% of 145,000,000 pounds (or 8,700,000 pounds) of steam energy would result from the switch between oil and gas. The boiler efficiency would be 0.78 for gas and 0.81 for oil. The heat value of natural gas is approximately 1,000,000 BTU/MCF (million cubic feet), and for No. 2 fuel oil it is 139,400 BTU/gal. The estimated gas price is $14.50/MCF, and the No. 2 fuel-oil price is $2.93 per gallon.(a) Calculate the annual fuel costs for each proposal.(b) Determine the unit cost per steam pound for each proposal. Assume i = 10%.(c) Which proposal is more economical?
A Veterans Administration (VA) hospital needs to decide which type of boiler fuel system will most efficiently provide the required steam energy output for heating, laundry, and sterilization purposes. The present boilers were installed in the early 1970s and are now obsolete. Much of the auxiliary equipment is also old and requires repair. Because of these general conditions, an engineering recommendation was made to replace the entire plant with a new boiler-plant building that would house modern equipment. The cost of demolishing the old boiler plant would be almost a complete loss, as the salvage value of the scrap steel and used brick is estimated to be only about $1,000. The VA hospital's engineer finally selected two alternative proposals as being worthy of more intensive analysis. The hospital's annual energy requirement, measured in terms
of steam output, is approximately 145,000,000 pounds of steam. As a general rule for analysis, 1 pound of steam is approximately 1,000 BTUs, and 1 cubic foot of natural gas is approximately 1,000 BTUs. The two alternatives are as follows:
Proposal 1: Build a new coal-fired boiler plant, which would cost $2.570,300. To meet the requirements for particulate emission asset by the Environmental Protection Agency (EPA), the new coal-fired boiler, even if it burned lowsulfur coal, would need an electrostatic precipitator, which would cost approximately $145,000. The new plant would last for 20 years. One pound of dry coal yields about 14,300 BTUs. To convert the 145,000,000 pounds of steam energy into the common unit of BTUs, it is necessary to multiply by 1,000. To find BTU input requirements, it is necessary to divide by the relative boiler efficiency for type of fuel. The boiler efficiency for coal is 0.75. The coal price is estimated to be $125 per metricton.
Proposal 2: Build a gas-fired boiler plant with No. 2 fuel oil as a standby.
This system would cost $1,289,340 with an expected service life of 20 years.
Since small household or commercial users entirely dependent on gas for
energy have priority, large plants must have oil switch-over capabilities. It
has been estimated that 6% of 145,000,000 pounds (or 8,700,000 pounds) of steam energy would result from the switch between oil and gas. The boiler efficiency would be 0.78 for gas and 0.81 for oil. The heat value of natural gas is approximately 1,000,000 BTU/MCF (million cubic feet), and for No. 2 fuel oil it is 139,400 BTU/gal. The estimated gas price is $14.50/MCF, and the No. 2 fuel-oil price is $2.93 per gallon.
(a) Calculate the annual fuel costs for each proposal.
(b) Determine the unit cost per steam pound for each proposal. Assume i = 10%.
(c) Which proposal is more economical?

Trending now
This is a popular solution!
Step by step
Solved in 2 steps with 3 images

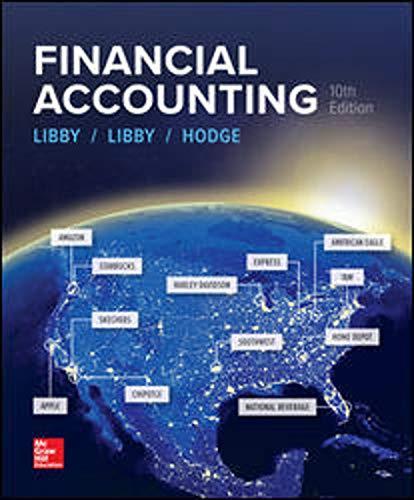
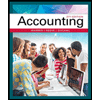
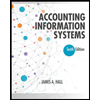
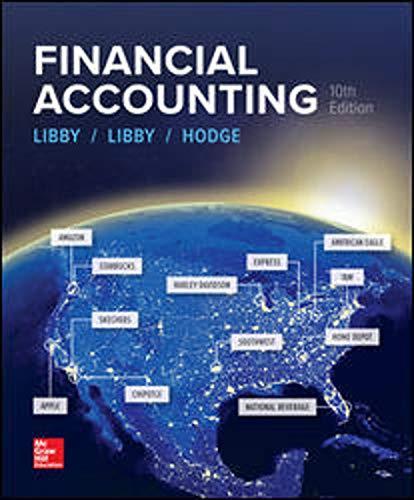
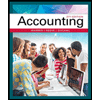
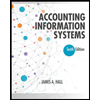
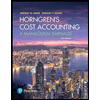
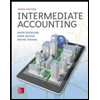
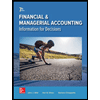