LSC-Lab1-Report-MMV
doc
keyboard_arrow_up
School
Lone Star College System, North Harris *
*We aren’t endorsed by this school
Course
2425
Subject
Mechanical Engineering
Date
Jan 9, 2024
Type
doc
Pages
1
Uploaded by SuperHumanJaguar3099
Date: 09/07/2023
Section:
PHYS 2426 6301
Name Surname (Last Name):
Melody Martinez Villanueva
Laboratory #:
1
Laboratory Title:
Uncertainty and Error Propagation
Objective (in one or two sentences):
To understand the basic usage of a vernier caliper and reading the vernier scale properly.
How to determine uncertainty in either a measurement or in a calculated quantity, by
either calculating the standard deviation of data or using error propagation.
Apparatus (in one or two sentences):
The equipment used for this experiment will be a wooden block, PCV pipe, Vernier
caliper.
Theory (in one or two sentences):
With the help of a vernier caliper a trial can be run to determine the uncertainty of each
the wooden block and the PVC tube’s volume. A systematic error is more likely to cause
an uncertainty and can be calculated by using error propagation or calculating the
standard deviation.
Data:
By using two tables measuring the dimensions of the wooden block and PVC tube each
having four trials, we can determine the standard deviation and the uncertainty. The data
will be collected using the vernier caliper and the uncertainty will be collected using a
different from of an equation depending on the process.
Discussion:
Measurements were collected by using vernier caliper. Determining the uncertainty was
done by using error propagation or calculating the standard deviation.
Conclusion:
By understanding how to use and read a
vernier caliper
we found that when measuring
dimensions uncertainty is going to happen due to a systematic error. Having said
uncertainty can be found using error propagation or calculating the standard deviation.
Discover more documents: Sign up today!
Unlock a world of knowledge! Explore tailored content for a richer learning experience. Here's what you'll get:
- Access to all documents
- Unlimited textbook solutions
- 24/7 expert homework help
Related Documents
Related Questions
b) Figure 1 shows the calibration data of a sensor. Determine the static sensitivity at the
input of X= 0, X= 5 and X= 10. For which input values is the system more sensitive?
Calibration Data
300
250
y = 0.875x1.055
200
150
100
50
20
40
60
80
100
120
Input value, cm
Figure 1
c) Suppose you found a dial thermometer in a stockroom. Discuss several methods by
which you might estimate random and systematic error in the thermometer? How
would you estimate its uncertainty?
Output value, V
arrow_forward
A temperature measurement system has the following specifications:
-128 to 781°C
Range
Linearity error
0.29% FSO
Hysteresis error
0.12% FSO
Sensitivity error
0.04% FSO
Zero drift
0.32% FSO
FSO stands for "Full Scale Output". Estimate the overall instrument
uncertainty for this system based on the available information. Use the
maximum possible output range over the FSO in your computations.
arrow_forward
A temperature measurement system is composed of a sensor and a readout device. The readout device has a claimed accuracy of 0.6 °C with a resolution of 0.1 °C. The sensor has an off-the-shelf limit of error of 0.5 °C. Estimate a design-stage uncertainty in the temperature indicated by this combination.
A displacement transducer has the following specifications:
Linearity error:±0.25% reading
Drift:±0.05%/°C reading Sensitivity error: ±0.25% reading
Excitation: 10-25 V
Output: dc 0-5Vdc
Range: 0-5 cm
The transducer output is to be indicated on a voltme- ter having a stated accuracy of 0:1% reading with a resolution of 10 μV. The system is to be used at room temperature, which can vary by 10 °C. Estimate an uncertainty in a nominal displacement of 2 cm at the design stage. Assume 95% confidence.
arrow_forward
As an engineer working for a water bottling company, you collect the following
data in order to test the performance of the bottling systems. Assume normal
distribution.
Milliliters of Water in the Bottle Frequency
485
490
milliliters
495
500
505
510
515
What is the mean (in milliliters)?
milliliters
What is the standard deviation (in milliliters)?
What is the z value corresponding to 490 milliliters?
Z =
6
12
20
33
18
11
00
8
arrow_forward
Areas Under the Standard Normal Curve-The Values Were Generated Using the Standard Normal
Distribution Function of Excel
Note that the standard normal curve is symmetrical about the mean.
z
0
0.01
0.02
0.03
0.04
0.05
0.06
0.07
0.08
0.09
0.1
0.11
0.12
1
0.95
0.96
0.97
0.98
0.99
1.01
1.02
1.03
1.04
1.05
Mean - 0
1.06
1.07
1.08
1.09
A
0.0000
0.0040
0.0080
0.0120
0.0160
0.0199
0.0239
0.0279
0.0319
0.0359
0.0398
0.0438
0.0478
A
0.3186
0.3212
0.3238
0.3264
0.3289
0.3315
0.3340
0.3365
0.3389
Z
0.3413
0.3438
0.3461
0.3485
0.3508
0.3531
0.3554
0.3577
0.3599
0.3621
0.13
0.14
0.15
0.16
0.17
0.18
0.19
0.2
0.21
0.22
0.23
0.24
0.25
1.12
1.13
1.14
1.15
1.16
1.17
A
z
0.0517
0.0557
0.26
0.27
0.28
0.29
0.0596
0.0636
0.0675 0.3
0.0714 0.31
0.0753 0.32
0.0793 0.33
0.0832 0.34
0.0871 0.35
0.0910
0.0948
0.0987
1.18
1.19
1.2
1.21
1.22
1.23
1.24
1.25
1.26
1.27
1.28
A
0.3643
0.3665
0.3686
0.3708
0.3729
0.3749
0.3770
0.3790
0.3810
0.36
0.3830
0.3849
0.3869
0.3888
0.3907
0.3925
0.3944
0.3962
0.3980
0.3997
0.37…
arrow_forward
4:07
3G l.
Moodle
A bbb2.du.edu.om
EE
...Session (15-3-
Said Grami O
College of Engineering
Vision for the Future
Question 3
During a step function calibration, a first-order instrument
is exposed to a step change of 200 units.
1- If after 1.5 s the instrument indicates 140 units, find the
instrument time constant.
2- find the error in the indicated value after 2 s
S.
3- Find the raise time at 90 % of the system.
y(0)=0 units; K=1 unit/unit.
Question 4
A first order instrument with a time constant of 2 seconds is to
be used to measure a periodic input. If a dynamic error of
±2% can be tolerated,
1- determine the maximum frequency of periodic input that
can be measured.
2- What is the associated time lag (in seconds) at that
frequency?
MECH374: Instrumentation and Measurement
Said Grami
Practice
arrow_forward
Instrumentation & Measurements
This homework measures your capability to design/analyze various components/variables of ameasurement system based on what you have studied.
Question is Attached in image. Thank you.
arrow_forward
Chapter 12 - Lecture Notes.pptx: (MAE 272-01) (SP25) DY...
Scores
arrow_forward
We wish to measure a characteristic of a machined part whose nominal size is 50 mm at 20 °C. For this, two different instruments are used; an analog micrometer and a digital vernier caliper, both recently calibrated and with the same resolution (0.01 mm). The calibration certificate data of the analog micrometer and the digital vernier are shown in tables 5 and 6 respectively. In both cases the calibration uncertainty does not include the contribution of resolution uncertainty. Additionally, there are drift studies for both instruments and it is established that the drift of the micrometer is ± 0.002 mm while the drift of the vernier is ± 0.02 mm.
The same number of measurements were performed with both instruments to avoid repeatability biases under controlled environmental conditions. Table 7 shows the results of the measurements of both instruments. The temperature of the piece was monitored with a digital thermometer whose calibration uncertainty is 0.1 °C, which already includes…
arrow_forward
1. A process manufacturing missile component parts is being controlled, with the
performance characteristic being the tensile strength in pounds per square inch. Samples
of size 4 each are taken every hour and 30 samples are reported as below:
30
30
30
45219.84, Σ-1Τι = 321.6, Σ
i= 1$i = 110.5
(a) Find trial control limits for X and R charts.
(b) Repeat part (a) for X and S charts.
arrow_forward
Lab 2-Measurement Asynch - Tagged.pdf
Page 4 of 7
?
Part I: Taking Measurements & Estimating Uncertainties for a single measurement
www.stefanelli.eng.br
The mass of the object is_
0
i
Parts on a tripie peam palance
0
0
10 20 30
1
100
2 3
40
200
4
+/-
50 60 70
5
300
7
400
80
Qv Search
8
90
9
500
100
9
10 g
www.stefanelli.eng.br
arrow_forward
2. Consider the voltmeter calibration data in Table 1. The sensitivity of the pressure
sensor is 0.5 V/kPa (given by manufacturer) and the linear curve fit for the upscale
calibration is given as y = 0.9829 x + 0.1095 . Plot the data using a suitable scale.
a) Specify the percent maximum hysteresis based on full-scale range.
b) Referring to increasing input calibration, determined the sensitivity and
linearity errors.
Increasing input (mV)
Decreasing input (mV)
Y
Y
0.0
0.1
5.0
5.0
1.0
1.1
4.0
4.2
2.0
2.1
3.0
3.2
3.0
3.0
2.0
2.2
4.0
4.1
1.0
1.2
5.0
5.0
0.0
0.2
Table 1: Calibration results
arrow_forward
Record the dimensions of the known (calibration) block using the caliper and dial gauge on the table below. Indicate the
units of each measurement. Calculate the average length of each side of the block.
Dimension
Caliper (Units)
0.995
1.455
0.985
Ruler(in) A: 0.9
B: 1.5
C: 0.9
A
B
C
Dimension
A
B
Instrument
Use the average dimensions (see Problem 2a) of the known block to calibrate the LVDT at your workstation. Record the
voltage on the table below:
LVDT Offset: 0.556 (Do not include the offset value in your average dimensions)
C
Ave Dimension (Units)
(Dial Gauge)
0.997
1.659
0.949
0.964 in
1.538 in
0.945 in
oltage
Average Dimension
1.244 volt
1.994
1.28
0.964 in
1.538 in
0.945 in
arrow_forward
3. The results of a simple calibration of pressure transducer and its specification are
shown in Figure 1 and Table 1. The sensitivity of the pressure sensor is 0.5 V/kPa
(given by manufacturer) and the linear curve fit for the upscale calibration is given
as y = 0.51x +0.02 .
a) Calculate the hysteresis and linearity errors for this calibration.
b) Please discuss either the pressure transducer can now be used for the actual
measurement or not.
Table 1: Pressure tansducer specification
Оperation
Input range
0- 5 kPa
+ 15 V
0 - 2.5 V
Excitation
Output range
Performance
Linearity error
± 3 %
Hysteresis
Less than + 15%
Sensitivity error
+ 5%
Thermal sensitivity error
+ 0.02% / °C
Temperature range
0 - 50 °C
2.5
upacale mesurement
downscale measurement
0.5
0.5
3.5
pressure, kPa
Оприt, voltage ((V)
Upscale
Input, pressure
(kPa)
Downscale
0.00
0.00
1
0.53
0.48
2
1.05
0.94
3
1.62
1.45
4
2.12
1.95
5
2.50
2.50
Figure 1: Calibration results (plot and tabulated data)
arrow_forward
Problem 2.
The sides of a thin rectangular block are measured using different digital calipers as 25.00 + 0.05 mm
and 17.50 + 0.01 mm. Based on the data, the perimeter of the block is calculated as 85.0 mm by adding
the length of the four sides. What is the uncertainty in the perimeter of the block expressed in mm?
arrow_forward
A thermocouple was used to measure the temperature. Over the range of temperatures expected in the experiment, a linear regression
analysis was performed for the temperature as a function of voltage. The best-fit equation was T = (-0.008563 + 220*V), where V is
the thermocouple voltage. The voltage was fed into a 11-bit A/D converter with a voltage range of -8 V to 8 V.
Determine the measurement resolution (in °C) due to the ADC?
O 0.851
None
O 3.113
1.710
0.393
4.960
1.144
O 3.797
arrow_forward
Can someone please help me to answer all of the following questions thank you!!
arrow_forward
Question 4
arrow_forward
How would you solve this
arrow_forward
mecha
arrow_forward
A Pitot tube measures a pressure difference Pa = Pt- Ps (dynamic = total - static)
between the front and side of the Pitot tube. The dynamic pressure is given by the
kinetic energy due to the airspeed v, allowing airspeed to be calculated from the
measured pressure difference.
(a)
P₁ = ² pv² ⇒ v=
When designing a Pitot tube, a manufacturer wants to make it precise enough to measure
airspeed to within 0.5 % uncertainty, i.e. = 0.005, at sea level.
Av
p=(1.225 +0.0005) kg/m³ at sea level.
(b)
2Pd
Av
Using error propagation, derive an expression for Simplify as much as
possible!
ΔΡΑ
Pd
Calculate the maximum permissible %-uncertainty in Pa, i.e.
allow the Pitot tube to meet the manufacturer's requirements.
Hint: Answer 1%
x 100, that will
arrow_forward
SEE MORE QUESTIONS
Recommended textbooks for you
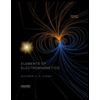
Elements Of Electromagnetics
Mechanical Engineering
ISBN:9780190698614
Author:Sadiku, Matthew N. O.
Publisher:Oxford University Press
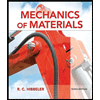
Mechanics of Materials (10th Edition)
Mechanical Engineering
ISBN:9780134319650
Author:Russell C. Hibbeler
Publisher:PEARSON
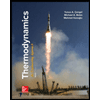
Thermodynamics: An Engineering Approach
Mechanical Engineering
ISBN:9781259822674
Author:Yunus A. Cengel Dr., Michael A. Boles
Publisher:McGraw-Hill Education
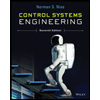
Control Systems Engineering
Mechanical Engineering
ISBN:9781118170519
Author:Norman S. Nise
Publisher:WILEY
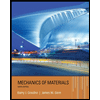
Mechanics of Materials (MindTap Course List)
Mechanical Engineering
ISBN:9781337093347
Author:Barry J. Goodno, James M. Gere
Publisher:Cengage Learning
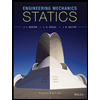
Engineering Mechanics: Statics
Mechanical Engineering
ISBN:9781118807330
Author:James L. Meriam, L. G. Kraige, J. N. Bolton
Publisher:WILEY
Related Questions
- b) Figure 1 shows the calibration data of a sensor. Determine the static sensitivity at the input of X= 0, X= 5 and X= 10. For which input values is the system more sensitive? Calibration Data 300 250 y = 0.875x1.055 200 150 100 50 20 40 60 80 100 120 Input value, cm Figure 1 c) Suppose you found a dial thermometer in a stockroom. Discuss several methods by which you might estimate random and systematic error in the thermometer? How would you estimate its uncertainty? Output value, Varrow_forwardA temperature measurement system has the following specifications: -128 to 781°C Range Linearity error 0.29% FSO Hysteresis error 0.12% FSO Sensitivity error 0.04% FSO Zero drift 0.32% FSO FSO stands for "Full Scale Output". Estimate the overall instrument uncertainty for this system based on the available information. Use the maximum possible output range over the FSO in your computations.arrow_forwardA temperature measurement system is composed of a sensor and a readout device. The readout device has a claimed accuracy of 0.6 °C with a resolution of 0.1 °C. The sensor has an off-the-shelf limit of error of 0.5 °C. Estimate a design-stage uncertainty in the temperature indicated by this combination. A displacement transducer has the following specifications: Linearity error:±0.25% reading Drift:±0.05%/°C reading Sensitivity error: ±0.25% reading Excitation: 10-25 V Output: dc 0-5Vdc Range: 0-5 cm The transducer output is to be indicated on a voltme- ter having a stated accuracy of 0:1% reading with a resolution of 10 μV. The system is to be used at room temperature, which can vary by 10 °C. Estimate an uncertainty in a nominal displacement of 2 cm at the design stage. Assume 95% confidence.arrow_forward
- As an engineer working for a water bottling company, you collect the following data in order to test the performance of the bottling systems. Assume normal distribution. Milliliters of Water in the Bottle Frequency 485 490 milliliters 495 500 505 510 515 What is the mean (in milliliters)? milliliters What is the standard deviation (in milliliters)? What is the z value corresponding to 490 milliliters? Z = 6 12 20 33 18 11 00 8arrow_forwardAreas Under the Standard Normal Curve-The Values Were Generated Using the Standard Normal Distribution Function of Excel Note that the standard normal curve is symmetrical about the mean. z 0 0.01 0.02 0.03 0.04 0.05 0.06 0.07 0.08 0.09 0.1 0.11 0.12 1 0.95 0.96 0.97 0.98 0.99 1.01 1.02 1.03 1.04 1.05 Mean - 0 1.06 1.07 1.08 1.09 A 0.0000 0.0040 0.0080 0.0120 0.0160 0.0199 0.0239 0.0279 0.0319 0.0359 0.0398 0.0438 0.0478 A 0.3186 0.3212 0.3238 0.3264 0.3289 0.3315 0.3340 0.3365 0.3389 Z 0.3413 0.3438 0.3461 0.3485 0.3508 0.3531 0.3554 0.3577 0.3599 0.3621 0.13 0.14 0.15 0.16 0.17 0.18 0.19 0.2 0.21 0.22 0.23 0.24 0.25 1.12 1.13 1.14 1.15 1.16 1.17 A z 0.0517 0.0557 0.26 0.27 0.28 0.29 0.0596 0.0636 0.0675 0.3 0.0714 0.31 0.0753 0.32 0.0793 0.33 0.0832 0.34 0.0871 0.35 0.0910 0.0948 0.0987 1.18 1.19 1.2 1.21 1.22 1.23 1.24 1.25 1.26 1.27 1.28 A 0.3643 0.3665 0.3686 0.3708 0.3729 0.3749 0.3770 0.3790 0.3810 0.36 0.3830 0.3849 0.3869 0.3888 0.3907 0.3925 0.3944 0.3962 0.3980 0.3997 0.37…arrow_forward4:07 3G l. Moodle A bbb2.du.edu.om EE ...Session (15-3- Said Grami O College of Engineering Vision for the Future Question 3 During a step function calibration, a first-order instrument is exposed to a step change of 200 units. 1- If after 1.5 s the instrument indicates 140 units, find the instrument time constant. 2- find the error in the indicated value after 2 s S. 3- Find the raise time at 90 % of the system. y(0)=0 units; K=1 unit/unit. Question 4 A first order instrument with a time constant of 2 seconds is to be used to measure a periodic input. If a dynamic error of ±2% can be tolerated, 1- determine the maximum frequency of periodic input that can be measured. 2- What is the associated time lag (in seconds) at that frequency? MECH374: Instrumentation and Measurement Said Grami Practicearrow_forward
- Instrumentation & Measurements This homework measures your capability to design/analyze various components/variables of ameasurement system based on what you have studied. Question is Attached in image. Thank you.arrow_forwardChapter 12 - Lecture Notes.pptx: (MAE 272-01) (SP25) DY... Scoresarrow_forwardWe wish to measure a characteristic of a machined part whose nominal size is 50 mm at 20 °C. For this, two different instruments are used; an analog micrometer and a digital vernier caliper, both recently calibrated and with the same resolution (0.01 mm). The calibration certificate data of the analog micrometer and the digital vernier are shown in tables 5 and 6 respectively. In both cases the calibration uncertainty does not include the contribution of resolution uncertainty. Additionally, there are drift studies for both instruments and it is established that the drift of the micrometer is ± 0.002 mm while the drift of the vernier is ± 0.02 mm. The same number of measurements were performed with both instruments to avoid repeatability biases under controlled environmental conditions. Table 7 shows the results of the measurements of both instruments. The temperature of the piece was monitored with a digital thermometer whose calibration uncertainty is 0.1 °C, which already includes…arrow_forward
- 1. A process manufacturing missile component parts is being controlled, with the performance characteristic being the tensile strength in pounds per square inch. Samples of size 4 each are taken every hour and 30 samples are reported as below: 30 30 30 45219.84, Σ-1Τι = 321.6, Σ i= 1$i = 110.5 (a) Find trial control limits for X and R charts. (b) Repeat part (a) for X and S charts.arrow_forwardLab 2-Measurement Asynch - Tagged.pdf Page 4 of 7 ? Part I: Taking Measurements & Estimating Uncertainties for a single measurement www.stefanelli.eng.br The mass of the object is_ 0 i Parts on a tripie peam palance 0 0 10 20 30 1 100 2 3 40 200 4 +/- 50 60 70 5 300 7 400 80 Qv Search 8 90 9 500 100 9 10 g www.stefanelli.eng.brarrow_forward2. Consider the voltmeter calibration data in Table 1. The sensitivity of the pressure sensor is 0.5 V/kPa (given by manufacturer) and the linear curve fit for the upscale calibration is given as y = 0.9829 x + 0.1095 . Plot the data using a suitable scale. a) Specify the percent maximum hysteresis based on full-scale range. b) Referring to increasing input calibration, determined the sensitivity and linearity errors. Increasing input (mV) Decreasing input (mV) Y Y 0.0 0.1 5.0 5.0 1.0 1.1 4.0 4.2 2.0 2.1 3.0 3.2 3.0 3.0 2.0 2.2 4.0 4.1 1.0 1.2 5.0 5.0 0.0 0.2 Table 1: Calibration resultsarrow_forward
arrow_back_ios
SEE MORE QUESTIONS
arrow_forward_ios
Recommended textbooks for you
- Elements Of ElectromagneticsMechanical EngineeringISBN:9780190698614Author:Sadiku, Matthew N. O.Publisher:Oxford University PressMechanics of Materials (10th Edition)Mechanical EngineeringISBN:9780134319650Author:Russell C. HibbelerPublisher:PEARSONThermodynamics: An Engineering ApproachMechanical EngineeringISBN:9781259822674Author:Yunus A. Cengel Dr., Michael A. BolesPublisher:McGraw-Hill Education
- Control Systems EngineeringMechanical EngineeringISBN:9781118170519Author:Norman S. NisePublisher:WILEYMechanics of Materials (MindTap Course List)Mechanical EngineeringISBN:9781337093347Author:Barry J. Goodno, James M. GerePublisher:Cengage LearningEngineering Mechanics: StaticsMechanical EngineeringISBN:9781118807330Author:James L. Meriam, L. G. Kraige, J. N. BoltonPublisher:WILEY
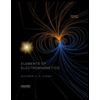
Elements Of Electromagnetics
Mechanical Engineering
ISBN:9780190698614
Author:Sadiku, Matthew N. O.
Publisher:Oxford University Press
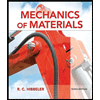
Mechanics of Materials (10th Edition)
Mechanical Engineering
ISBN:9780134319650
Author:Russell C. Hibbeler
Publisher:PEARSON
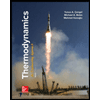
Thermodynamics: An Engineering Approach
Mechanical Engineering
ISBN:9781259822674
Author:Yunus A. Cengel Dr., Michael A. Boles
Publisher:McGraw-Hill Education
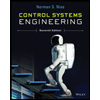
Control Systems Engineering
Mechanical Engineering
ISBN:9781118170519
Author:Norman S. Nise
Publisher:WILEY
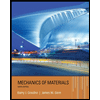
Mechanics of Materials (MindTap Course List)
Mechanical Engineering
ISBN:9781337093347
Author:Barry J. Goodno, James M. Gere
Publisher:Cengage Learning
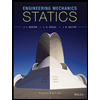
Engineering Mechanics: Statics
Mechanical Engineering
ISBN:9781118807330
Author:James L. Meriam, L. G. Kraige, J. N. Bolton
Publisher:WILEY