new_air_flow_rig_26022024
docx
keyboard_arrow_up
School
University of Technology Sydney *
*We aren’t endorsed by this school
Course
CHNG3801
Subject
Mechanical Engineering
Date
Apr 3, 2024
Type
docx
Pages
13
Uploaded by ProfessorAtomChimpanzee38
CHNG2801/CHNG9201 FLUID MECHANICS
LABORATORY EXPERIMENT
Air Flow
Preparation and Prework
Running the Equipment
TAGL: March 2024
Air flow rig AR demo V2:
https://view.vuforia.com/command/view-experience?url=https%3A%2F%2Funiversity-of-
sydney-dev.es.thingworx.com%2FExperienceService%2Fcontent%2Fprojects
%2Fair_flow_rig_v3%2Findex.html%3FexpId%3D1
Safety:
You must wear safety glasses or spectacles, laboratory coat, pants or jeans and
closed, covered footwear while in the laboratory area at all times. Failure to follow this
requirement will result in your ejection from the laboratory for the rest of the laboratory
session. You will not be given the opportunity to repeat the experiment on another day.
This practice is intended to encourage the development of good safety discipline in
industry as well as for your direct protection.
Overall Learning Objectives
Students should be able to:
1.
Identify pipework and equipment used to make fluids move (fans and pumps). What do
these pieces of equipment look like, and how do they work? (in laboratory)
2.
Calculate flow rate using the Pitot tube, and the orifice plate flow meter to measure the
flowrate in a duct. (in laboratory)
3.
Construct fan and system curves from pressure and flow rate measurements. (in
laboratory)
1
4.
Operate chemical engineering equipment safely and extract relevant measurements and
data. (in laboratory)
5.
Synthesise findings with relevant fluid mechanics theory and report results concisely.
(after laboratory)
INTRODUCTION
The aims of this experiment are (a) to compare two different flow measurement techniques,
and (b) to measure the pump and system curves for the fan and the other equipment,
respectively.
We need to compare flow measurement devices, specifically Pitot tubes (and Pitot tube
traverses) with orifice plate flow measurements.
We need to create a set of pump and system curves. The pressure decrease through the
system is the system curve (the pressure difference required by the system at a given flow
rate), which starts at atmospheric pressure. This pressure drop must equal the pressure
increase across the pump, which is the pump or fan curve). Each measurement is an operating
point where a pump curve intersects a system curve. The system curve may be changed by
altering a valve position, while a pump curve may be changed by altering the pump speed.
EQUIPMENT
Figure 1 shows a Piping and Instrumentation Diagram for the equipment.
Figure 1:
Piping and Instrumentation Diagram for the air flow experiment.
DP
DP
Negative point for Pitot tube, static pressure: negative side of digital manometer
Positive point for Pitot tube, impact pressure: positive side of digital manometer
Negative point for orifice plate flow meter: negative side
of digital manometer
Positive point
for orifice plate flow meter: in the atmosphere
Pitot tube traverse
From atmosphere
Iris valve
Orifice plate flow meter
Fan
2
PREWORK CALCULATIONS (TO BE DONE BEFORE THE LABORATORY FOR
THE EXPERIMENTS STARTING SOON)
These calculations must
be shown to the laboratory tutor on the day of the experiment and must
be completed correctly before commencing. The next section 6 of these notes gives some
examples that might be helpful.
(a)
The following pressure differences (between the impact and static tappings) were recorded
at equispaced points in a 114 mm x 127 mm rectangular duct through which air (density,
1.2 kg m
-3
; viscosity, 1.8 x 10
-5
kg m
-1
s
-1
) is flowing. Calculate the volumetric flow rate
through the duct. The pressure differences (in Pa) are as shown in the following Table 1.
Equation (1) in the next section will be important. Use a Pitot-tube coefficient (
C
) of 1
(unity).
Table 1: Pressure differences recorded by the digital pressure meter (in Pa) in each section of
the Pitot tube traverse for the air flow experiment. 75
100
125
100
100
125
150
125
75
150
175
100
50
75
125
75
Each rectangle in the grid above represents an equal area, so averaging the point velocities
directly to give an average velocity is reasonable.
3
Your preview ends here
Eager to read complete document? Join bartleby learn and gain access to the full version
- Access to all documents
- Unlimited textbook solutions
- 24/7 expert homework help
(b) This rectangular duct is followed by a circular duct of 140 mm diameter in which there is
an orifice plate flow meter. The orifice plate hole diameter is 108 mm and the pressure drop
between the upstream tapping and the throat (the hole) is 216 Pa. Given a discharge
coefficient of 0.6 for the orifice plate flow meter, calculate the volumetric flow rate as
measured by this flow meter. Equation (2) in the following section will be important.
= 0.25756 M^3/s
Note: Useful information for these calculations (above) is given in the equations in the next
section.
EXPECTATIONS IN THE LABORATORY
Suppose that we have a 140 mm diameter pipe, with an orifice plate flow meter having an
orifice diameter of 108 mm.
With a Pitot tube, in general, and here in this laboratory, the simple application of the Pitot
tube equation is helpful: u
=
C
pt
√
2
∆ P
ρ
(1)
Given that C
pt
≈ 1 and ρ
≈ 1 kg m
-3
, the pressure difference across a manometer for a velocity
of 5 ms
-1
through a test section is about (5 ms
-1
)
2
/2 = 12 Pa, and at 10 ms
-1
, the pressure
difference is (10 ms
-1
)
2
/2 = 50 Pa. In the experiment, we will use ρ
≈ 1.2 kg m
-3
, but here we
use ρ
≈ 1 kg m
-3 for convenience.
What should we expect in the orifice plate flow meter? Should the pressure differences be the
same as those from the Pitot tube?
Yes and no.
Yes, the general form of the equation is similar for all devices, and all equations for these
types of meter come from Bernoulli’s equation. For the Pitot tube, see equation (1) above.
For the orifice plate flow meter, equations (2) and (3) apply:
Q
=
C
D
A
t
√
2
∆ P
ρ
[
1
−
(
A
t
A
p
)
2
]
(2)
u
av
=
Q
A
p
(3)
4
Where C
D
is a discharge coefficient (about 0.6 for the orifice plate flow meter), u
av
is the
average pipe velocity, A
t
is the throat cross-sectional area, and A
p
is the pipe cross-sectional
area.
And no:
The orifice plate flow meter is located in a 140 mm diameter pipe, so A
p
= π/4 (0.14 m)
2
=
0.0154 m
2
.
For the orifice plate meter, A
t
= π/4 (0.108 m)
2
= 0.00916 m
2
, and rearranging equation (2),
for the orifice plate flow meter, gives
∆ P
=
(
Q
C
D
A
t
)
2
ρ
2
[
1
−
(
A
t
A
p
)
2
]
(4)
∆ P
=
(
u
av
A
p
C
D
A
t
)
2
ρ
2
[
1
−
(
A
t
A
p
)
2
]
(5)
Hence, for an average air velocity of 5 ms
-1
through the orifice plate flow meter, the pressure
difference is:
∆ P
=
(
5
×
0.0154
0.61
×
0.00916
)
2
1
2
[
1
−
(
0.00916
0.0154
)
2
]
= 61 Pa
For the Pitot tube, the pressure difference at a velocity of 5 ms
-1
is 12 Pa.
For an average air velocity of 10 ms
-1
through the orifice plate flow meter, the pressure
difference is:
∆ P
=
(
10
×
0.0154
0.61
×
0.00916
)
2
1
2
[
1
−
(
0.00916
0.0154
)
2
]
= 245 Pa
For the Pitot tube, the pressure difference at a velocity of 10 ms
-1
is 50 Pa.
For the orifice plate flow meter, the relationship between the velocity and the pressure
difference is affected by the pipe and throat cross-sectional areas and the discharge
coefficients.
TESTING PROCEDURE
Orifice Plate: To measure the pressure difference between the upstream location and the
throat in the orifice plate flowmeter, connect the plastic tube after the orifice plate to the
negative side of the digital manometer. The upstream pressure is just atmospheric pressure,
so the positive side of the manometer should just be open to the atmosphere.
5
Pitot Tube: To measure the pressure difference for the Pitot tube, connect the bottom of the
Pitot tube (connected to the impact pressure point) to the positive side of the digital
manometer with a plastic tube, and also use a plastic tube to connect the side of the Pitot tube
(connected to the static pressure point) to the negative side of the digital manometer.
Positive point for orifice plate flow meter: in the atmosphere
Pitot tube traverse points (distances from near wall):
2 mm
12 mm
19 mm
36 mm
69 mm
86 mm
These distances represent (almost) equal cross-sectional areas, so the point velocities can be
averaged to give the average velocity.
1. Flow meters: Set the flow to a high value by fully opening up the Iris valve (indicator at
the blue line) after the entry of the duct and setting the variable speed drive (v.s.d.) on
the fan to 50 Hz.
2. Flow meters: With the Iris valve fully opened (indicator at the blue line), carry out a Pitot
Tube traverse of the circular pipe using the points given above (2 mm, 12 mm, etc).
Without altering the flow, measure the pressure at the downstream tapping of the orifice
plate flow meter.
3. Flow meters: Again, with the Iris valve fully opened (indicator at the blue line), repeat the
experiment using two lower flow rates (e.g. 40 Hz, and 30 Hz on the v.s.d.), so that you
carry out measurements for three flow rates. 4. Fan and system curves (valve setting 1): Start with the Iris valve fully opened (indicator at
the blue line), set the variable speed drive (v.s.d.) on the fan to 30 Hz. Measure the static
pressure before the fan. Also, measure the pressure downstream of the orifice plate flow
meter, allowing us to calculate the flow rate. The static pressure will be less than
atmospheric pressure, due to the pressure drop along the pipe. This combination of the
static pressure and the flow rate from the flow meter is an operating point on both a
system curve (for the system with the Iris valve fully open) and on a fan curve (for the
fan at a frequency or speed of 30 Hz). The pressure drop down the pipe is equal to the
pressure at the inlet to the fan.
5. Fan and system curves (valve settings 2, 3 and 4): Change the Iris valve setting (indicator
at the blue line) to the numbers 4, 3, and the bottom line, and repeat the static pressure
measurements before the fan for settings of the variable speed drive (v.s.d.) on the fan at
6
Your preview ends here
Eager to read complete document? Join bartleby learn and gain access to the full version
- Access to all documents
- Unlimited textbook solutions
- 24/7 expert homework help
30 Hz, 40 Hz, and 50 Hz. You will have four valve settings and three fan speeds, so you
will have 12 operating points)
6. Calculate flow rates and pressure differences (increases and decreases) on the spot. If your
results are unexpected, measure them again, checking that your instrumentation is set up
correctly.
7
RESULTS AND DISCUSSION
Typical Data and Analysis
Use C
D
= 0.6 for the orifice plate flow meter. Circular duct diameter
:
105 mm
Orifice plate hole diameter
:
71 mm
Comparison between Pitot tube traverses and orifice plate flow meters
The raw data for the comparison between Pitot tube traverses and orifice plate flow meters
are shown in Table 2.
Table 2:
Raw data for the pressure differences across the Pitot tube and the orifice plate flow
meters, iris valve fully open
Fan
frequency
Pitot tube
Orifice
plate
flow
meter Point 1,
2 mm
Point 2,
12 mm
Point 3,
19 mm
Point 4,
36 mm
Point 5,
69 mm
Point 6,
86 mm
(Hz)
(Pa)
(Pa)
(Pa)
(Pa)
(Pa)
(Pa)
(Pa)
20
26
31
33
34
35
29
304
30
60
69
72
76
80
70
690
40
105
125
129
135
137
118
1200
50
170
195
201
202
209
186
1815
Processing the data and doing the calculations
Sample calculation for the Pitot tube
Row 1, 20 Hz fan frequency, iris valve fully open, column 1, point 1, 2 mm from wall, Δ
P
=
26 Pa on the Pitot tube.
Equation (1) becomes the following equation, with C
pt
≈ 1.29 at 20
o
C, including the density
of 1.2 kg m
-3
at 20
o
C:
u
=
C
pt
√
∆ P
(1)
Given that C
pt
≈ 1.29 at 20
o
C, includes the density of 1.2 kg m
-3
at 20
o
C.
With Δ
P
= 26 Pa,
u
=
1.29
√
26
=
6.58
m s
−
1
(1)
Pitot tube: For the first row, 20 Hz fan frequency, iris valve fully open, the average velocity
for all the Pitot tube measurements is 7.21 m s
-1
. The cross-sectional area of the pipe is π/4
(0.105 m)
2
= 0.008659 m
2
, and this cross-sectional area applies for all the fan frequencies and
flow rates. Hence, the volumetric flow rate from the Pitot tube measurements for the first
row, 20 Hz fan frequency, iris valve fully open, is 7.21 m s
-1
× 0.008659 m
2
= 0.0624 m
3
s
-1
(
Q
Pitot
).
8
Sample calculation for the orifice plate flow meter
Row 1, 20 Hz fan frequency, iris valve fully open, Δ
P
= 304 Pa for the orifice plate flow
meter.
Equation (2) for the orifice plate flow meter follows:
Q
=
C
D
A
t
√
2
∆ P
ρ
[
1
−
(
A
t
A
p
)
2
]
(2)
Where C
D
is a discharge coefficient (about 0.6 for the orifice plate flow meter), A
t
is the
throat cross-sectional area, and A
p
is the pipe cross-sectional area (0.008659 m
2
, from above).
The throat cross-sectional area (
A
t
) is π/4 (0.071 m)
2
= 0.003959 m
2
.
Substituting the values into equation (2) gives:
Q
orifice
=
0.6
×
0.003959
√
2
×
304
1.2
[
1
−
(
0.003959
0.008659
)
2
]
=
0.0601
m
3
s
−
1
(2)
The comparisons between the volumetric flow rates from the Pitot tube traverses and the
orifice plate flow meters are shown in Table 3.
Table 3:
Volumetric flow rate comparison between the Pitot tube and the orifice plate flow
meters, iris valve fully open
Pitot tube
Fan
freq.
Point
1, 2
mm
Point
2,
12
mm
Point
3, 19
mm
Point
4, 36
mm
Point
5, 69
mm
Point
6, 86
mm
Pitot
tube
average
velocity
Q
Pitot
,
Pitot
tube
volu-
metric
flow rate
Q
orifice
,
orifice
plate
volu-
metric
flow rate
(Hz)
(m s
-1
)
(m s
-1
)
(m s
-1
)
(m s
-1
)
(m s
-1
)
(m s
-1
)
(m s
-1
)
(m
3
s
-1
)
(m
3
s
-1
)
20
6.58
7.18
7.41
7.52
7.63
6.95
7.21
0.0624
0.0601
30
10.0
10.7
10.9
11.2
11.5
10.8
10.9
0.0941
0.0906
40
13.2
14.4
14.7
15.0
15.1
14.0
14.4
0.125
0.119
50
16.8
18.0
18.3
18.3
18.6
17.6
17.9
0.155
0.147
Comparison between Pitot tube traverses and orifice plate flow meters
The raw data for the pump and system curves are shown in Tables 4 and 5.
9
Your preview ends here
Eager to read complete document? Join bartleby learn and gain access to the full version
- Access to all documents
- Unlimited textbook solutions
- 24/7 expert homework help
Table 4:
Raw data for fan and system curves, the pressure differences across the orifice plate
flow meter (for calculating the volumetric flow rates)
Valve position
Fan
frequency
Fully open
4/5 open
3/5 open
2/5 open
1/5 open
(Hz)
(Pa)
(Pa)
(Pa)
(Pa)
(Pa)
20
293
274
225
143
38
30
663
612
505
326
92
40
1173
1079
891
578
158
50
1813
1670
1378
890
261
Table 5:
Raw data for fan and system curves, the pressure at the inlet of the fan and the outlet
of the measurement tube (below atmospheric pressure)
Valve position
Fan
frequency
Fully open
4/5 open
3/5 open
2/5 open
1/5 open
(Hz)
(Pa)
(Pa)
(Pa)
(Pa)
(Pa)
20
314
323
330
340
340
30
714
726
743
766
770
40
1265
1285
1316
1359
1360
50
1960
1990
2035
2100
2110
The raw data in Table 5 may be used directly, since the pressure below atmospheric pressure
at the inlet to the fan and the outlet of the tube gives both the pressure drop across the tube
and the pressure increase across the fan, for the following reasons. The pressure drops along
the tube from atmospheric pressure to the pressure at the inlet to the fan, so this pressure is
the pressure required for this volumetric flow rate on the system curve. The pressure
increases across the fan from the pressure at the inlet to the fan to atmospheric pressure, so
this pressure is the pressure increase across the fan at this volumetric flow rate on the fan or
pump curve.
The pressure difference data in Table 4 must be converted to volumetric flow rates as shown
in the sample calculation applying equation (2) to the flow meter comparison.
Taking the pressure difference in the first row, first column, fan frequency 20 Hz, fully open
iris valve, Δ
P
= 293 Pa for the orifice plate flow meter, and using equation (2), gives:
Q
orifice
=
0.6
×
0.003959
√
2
×
293
1.2
[
1
−
(
0.003959
0.008659
)
2
]
=
0.0590
m
3
s
−
1
(2)
The remaining data in Table 4 have been calculated as above and placed into Table 6.
10
When plotting the fan (pump) and system curves, each point is a point on both fan and system
curves. The x-coordinate (abscissa) comes from a row, column location in Table 6, for the
volumetric flow rate. The y-coordinate (ordinate) comes from a row, column location in
Table 4, for both the pressure drop across the tube (system curve) and the pressure increase
across the fan (fan curve). The resulting fan and system curves are shown in Figure 2.
Table 6:
Calculated volumetric flow rates corresponding to the pressure differences across
the orifice plate flow meter (from Table 4) for the fan and system curves
Valve position
Fan
frequency
Fully open
4/5 open
3/5 open
2/5 open
1/5 open
(Hz)
(m
3
s
-1
)
(m
3
s
-1
)
(m
3
s
-1
)
(m
3
s
-1
)
(m
3
s
-1
)
20
0.0590
0.0571
0.0517
0.0412
0.0213
30
0.0888
0.0853
0.0775
0.0623
0.0331
40
0.1181
0.1133
0.1029
0.0829
0.0433
50
0.1468
0.1409
0.1280
0.1029
0.0557
0.0000
0.0500
0.1000
0.1500
0
1000
2000
3000
Fully open
4/5 open
3/5 open
2/5 open
1/5 open
20 Hz
30 Hz
40 Hz
50 Hz
Air flow rate, m3/s
Pressure increase or decrease, Pa
Figure 2:
Fan (pump) and system curves for the air flow experiment.
11
12
Your preview ends here
Eager to read complete document? Join bartleby learn and gain access to the full version
- Access to all documents
- Unlimited textbook solutions
- 24/7 expert homework help
Discussion
1.
You must prepare a concise report to your manager summarising the key findings.
Your support calculations and raw data should be included in the Appendices that
should be attached to your report.
2.
Calculate and compare the flows given by the two methods of measurement. 3.
Calculate the Reynolds Number for each flow rate and comment on the likely state of
flow (laminar or turbulent). Do not plot Reynolds number against flow rate because they
are directly proportional by definition!
4.
Discuss the uncertainties in the measurements and how these uncertainties propagate
through to affect the results. The appendix has notes on how to do this. What effects
do the uncertainties in all the input numbers (diameters, pressure differences,
densities) for the calculations have on the final results (e.g. flow rates)?
5.
The fan/pump and system curves show that there are two ways to control the flow rate
through the equipment (below the maximum flow rate). One way is to reduce the fan
frequency using the variable speed drive. The other way is to close the valve. Given
that the power required to pump the fluid (air) is the product of the pressure rise
across the pump (fan), in Pa, and the volumetric flow rate, in m
3
s
-1
, what is the lowest
energy cost way to achieve a volumetric flow rate that is half the maximum
volumetric flow rate? At this halfway value of the maximum volumetric flow rate,
what is the difference in power requirements between reducing the volumetric flow
rate by (a) closing the valve, or (b) reducing the fan/pump speed?
REFERENCES
Coulson, J M, Richardson, J F, Backhurst, J R, Harker, J H, (1999) Chemical Engineering.
Volume 1: Fluid Flow, Heat Transfer and Mass Transfer
, 6th Edition, Pergamon, Oxford.
There are many other books on fluid mechanics, fluids engineering in the library. 13
Related Documents
Related Questions
https://drive.google.com/file/d/1X0Sk9U2pT7lwJ9IB--kLkGngHm46SywH/view?usp=sharing
arrow_forward
11°C
Mostly cloudy
ליזום
Queen's Online
x
MEE1018 2221ES2 1.1 X
Past paper examples ex
Cengal Appendix1 Slu x
b Security | bartleby
https://qubstudentcloud.sharepoint.com/sites/exampastpapers/Papers/MEE/MEE1018/MEE1018 2221ES2_1_198.pdf
@
✩
Draw
n
F2
£
1
2
3
Ꮕ
W
a
Ask Copilot
2
of 15
(b) During a process, 2 kg of methane (CH) is heated from 800 K to 1200 K at constant
volume. Mcarbon 12 kg/kmol, Maydrogen = 1 kg/kmol and Cp(Methane) 2.2537 kJ/kg.K
(i) Determine the specific gas constant for methane.
(ii) Calculate the change in entropy during the process.
(iii) Determine the work done.
=
[6 marks]
(c) An air conditioning unit with COP = 8 removes heat from a room to the atmosphere at a rate
of 2 kW. Assuming electrical and mechanical efficiencies are 100%, determine the rate of
heat transfer to the atmosphere and the required power input.
[3 marks]
(d) 4 kg of a gas undergoes the cycle in Figure Q1(d). Describe each process in the cycle and
calculate the net work.
E
P (kPa)
<»
120
DII…
arrow_forward
Course Home
llege.com/course.html?courseld=17313546&OpenVellumHMAC=1c89e19b153e443490bb4df0da3b2ded#10001
to
Review | Constants
pour unistur very unu sıyın
mm nyurve.
Fv = 390 N
Sur
Previous Answers
Mountaineers often use a rope to lower themselves
down the face of a cliff (this is called rappelling). They
do this with their body nearly horizontal and their feet
pushing against the cliff (Eigure 1). Suppose that an
78.6-kg climber, who is 1.88 m tall and has a center of
gravity 1.0 m from his feet, rappels down a vertical cliff
with his body raised 40.4° above the horizontal. He
holds the rope 1.54 m from his feet, and it makes a
20.7° angle with the cliff face.
✓ Correct
Part D
Figure
1 of 1
What minimum coefficient of static friction is needed to prevent the climber's feet from slipping on
the cliff face if he has one foot at a time against the cliff?
Express your answer using two significant figures.
{—| ΑΣΦ
?
fs=
Submit
Provide Feedback
Next >
P Pearson
Copyright © 2022 Pearson…
arrow_forward
this is a practice problem, not a graded assignment
arrow_forward
Chrome
File
Edit
View
History
Bookmarks
People
Tab
Window
Help
McGraw-Hill Campus - ALEKS Science - CHM1045 GEN CHEM 1 BLENDED 669113
A bconline.broward.edu/d21/le/content/466883/fullscreen/12868783/View
McGraw-Hill Campus - ALEKS Science
O GASES
Interconverting pressure and force
A chemistry graduate student is designing a pressure vessel for an experiment. The vessel will contain gases at pressures up to 470.0 MPa. The student's
design calls for an observation port on the side of the vessel (see diagram below). The bolts that hold the cover of this port onto the vessel can safely withstand
a force of 2.80 MN.
pressure vessel
bolts
side
View
port
Calculate the maximum safe diameter w of the port. Round your answer to the nearest 0.1 cm.
O cm
Explanation
Check
O2021 McGraw-Hill Education. All Rights Reserved. Terms of Use
FEB
arrow_forward
spital
7 334 3140 (Med
391 2659
ai Queers
$ 307 7683
P 808 9646
X
Online Course | CHNU X
e to search
https://university.chnnyc.org/#/online-courses/3fa2e3bd-5548-487b-9f07-5afe50ba5f5c
DCA A1C
Menu
O
Tefinical Dept art
Rosanny-2443
Bi
a dca alc weekls matian XQ dca alc manual - Sear X DCA Vantage Analyze X Privacy error
4
✓Clean exterior of analyzer
Change air filter
7184832 777-2
Which of the following are weekly maintenance
tasks? Check all that apply.
Clean cartridge spring
Perform optical test
Clean barcode window
F6
Fr
hp
LANGUAGE LINE
844-401 8401
LIC-6417
10
FB
Chip
FO
xMail-Tyron Grant-CX a covermymeds - Search X
G
F10
F11
B
F12
Drink
Pit
Bom
x 3
SUBMIT
Fra
Seark
Lock
Pass
Se
arrow_forward
O NWP Assessment Builder UI Appl X
O NWP Assessment Player UI Appli X
+
->
A education.wiley.com/was/ui/v2/assessment-player/index.html?launchld=4599c668-aabf-4aa6-a299-d14a1c37f643#/question/2
E
E Apps
Q Hydrogeology Flas..
3 That Time I Got Rei...
MATLAB Online R2..
Chem Exam 2 Flash..
СОР2030 Мodule 3...
A SSMagon - ME137L...
S Easy to use Online...
E Reading list
>>
E Chapter 4 Homework
Question 3 of 14
>
0/1
Your answer is incorrect.
Refrigerant 134a enters a well-insulated nozzle at 200 Ibf/in.?, 140°F, with a velocity of 120 ft/s and exits at 50 Ibf/in.? with a velocity
of 1500 ft/s.
For steady-state operation, and neglecting potential energy effects, determine the temperature, in °F, and the quality of the refrigerant
at the exit.
T2 =
i
72.78
°F
X2 =
i
75.9019
eTextbook and Media
Hint
7:31 PM
O Type here to search
30°C Partly cloudy
22/09/2021
D
arrow_forward
iPhone -...
blem Set 1
Question 1 of 10
View Policies
Current Attempt in Progress
X =
y =
Electric C...
Z=
I
eTextbook and Media
Save for Later
in https://m...
education.wiley.com
National...
The force, F, of the wind blowing against a building is given by F = CopV²A/2, where Vis the wind speed, p the density of the air, A the
cross-sectional area of the building, and CD is a constant termed the drag coefficient. Determine the dimensions of the drag coefficient,
x, y, and z in the expression CD = M*LYT.
i
WP Problem...
W Support -...
WP NWP Ass...
-/10 E
Start Pag
Attempts: 0 of 5 used
Submit Answer
arrow_forward
permanent-magnet (pm) genera x
Bb Blackboard Learn
L STAND-ALONE.mp4 - Google Dri x
O Google Drive: ülwgjuó jc lis u
O ME526-WindEnergy-L25-Shuja.p x
O File | C:/Users/Administrator/Desktop/KFUPM%20Term%232/ME526/ME526-WindEnergy-L25-Shuja.pdf
(D Page view
A Read aloud
T) Add text
V Draw
Y Highlight
O Erase
17
of 26
Wind Farms
Consider the arrangement of three wind turbines in the following schematic in which wind
turbine C is in the wakes of turbines A and B.
Given the following:
- Uo = 12 m/s
A
-XẠC = 500 m
-XBC = 200 m
- z = 60 m
- Zo = 0.3 m
U.
-r, = 20 m
B
- CT = 0.88
Compute the total velocity deficit, udef(C) and the velocity at wind turbine C, namely Vc.
Activate Windows
Go to Settings to activate Windows.
Wind Farms (Example Answer)
5:43 PM
A 4)) ENG
5/3/2022
I!
arrow_forward
-Sear x
dynamics systems questions 1[1 x
Week 15-Mechanical (Tutorials x +
| C:/Users/40332698/AppData/Local/Packages/microsoft
windowscommunicationsapps_8wekyb3d8bbwe/LocalState/Files/SO/145/Attachments/dynamics%...
Q
- +3
Page view A Read aloud Add textDraw
Highlight
V
Erase
ate the
3/104 The car is moving with a speed vo= 105 km/h up
the 6-percent grade, and the driver applies the
brakes at point A, causing all wheels to skid. The
coefficient of kinetic friction for the rain-slicked
bogne-road is = 0.60. Determine the stopping distance
ed ISAB. Repeat your calculations for the case when the
booga car is moving downhill from B to A.
the case
-8.0
ai noilsi' SA noitisoq de JDT mot gainnige ge
= $1 bacilyon
A
S
→ vo
6
search
10.
$
R
F
T
V
25
%
5
T
G
B
O Ai
O
A
6
Y
H
N
&
7
U
J
Fa
★
8
M
1
K
FO
100
9
prt sc
F10
O
L
)
O
home
P
;
B
A
end
F12
{
?
+
insert
}
1
To
6
9°C Cloudy DENG
^
7
arrow_forward
O NWP Assessment Builder UI Appl X
O NWP Assessment Player UI Appli X
+
->
A education.wiley.com/was/ui/v2/assessment-player/index.html?launchld=4599c668-aabf-4aa6-a299-d14a1c37f643#/question/13
E
E Apps
Q Hydrogeology Flas...
3 That Time I Got Rei...
MATLAB Online R2...
Chem Exam 2 Flash...
COP2030 Module 3..
6 SSMagon - ME137L...
S Easy to use Online...
E Reading list
>>
E Chapter 4 Homework
Question 14 of 14
-/1
View Policies
Current Attempt in Progress
As shown in the figure, a 300-ft tank contains 25 lb of H2O initially at 30 lbf/in?. The tank is connected to a large steam line carrying
steam at 200 Ibf/in?, 450°F. Steam flows into the tank through a valve until the tank pressure reaches p2 = 120 lbf/in? and the
temperature is 400°F, at which time the valve is closed.
Steam at
200 lbf/in.².
450°F
Tank
Valve
(1)
Initially:
30 lbfin.?, mı = 25 lb
|(2)
Finally:
Ibfin.?, 400°F.
P2
Determine the amount of mass that enters the tank, in Ib, and the heat transfer to the tank from its…
arrow_forward
M Inbox - wep10@zips.uakron.edu
O My Akron Experience - The Univ
B Homepage - Statics 801
O Pearson MyLab and Mastering
b The equivalent resultant force, di x
Course Home
A https://openvellum.ecollege.com/course.html?courseld=16245503&OpenVellumHMAC=67fab398401alafde96db3b49e605db9#10001
O My Courses
KAssignment 10o
Course Home
Problem 4.137
3 of 4
Syllabus
I Review
Scores
Replace the three forces acting on the plate by a wrench. Suppose
that FA = {450i}N, FB = {-350k} N, and Fc = {300j} N.
(Figure 1)
Part B
eТext
Determine the couple moment of the wrench.
Express your answer to three significant figures and include the appropriate units. Enter positive value if the sense of direction of the couple moment is the
same as that of the resultant force and negative value if the sense of direction of the couple moment is opposite to that of the resultant force.
Study Area
Document Sharing
TH HẢ
?
User Settings
Value
Units
Course Tools
>
Submit
Previous Answers Request Answer
X Incorrect; Try…
arrow_forward
Τρ
סוי
D2L Notes de cours 2 - MA...
D2L Solutions d'examen -...
B https://uottawa.brights...
ChatGPT
← Homework 4 - Fall 2024
Question 1 of 6
View Policies
>
education.wiley.com
ELG 3736 - Google Docs
On mesure la traînée s...
WP Homework 4 - Fall 2024
X W Question 1 of 6 - Hom...
- / 20
0
Current Attempt in Progress
The spring of modulus k = 203 N/m is compressed a distance of 300 mm and suddenly released with the system at rest. Determine the
absolute velocities of both masses (positive if to the right, negative if to the left) when the spring is unstretched. Neglect friction.
k
2 kg
= 203 N/m
wwwwww
5.6 kg
Answers:
2kg mass,
v=
5.6kg mass,
v =
Hi
eTextbook and Media
Save for Later
m/s
m/s
Attempts: 0 of 1 used Submit Answer
arrow_forward
Newton’s 2nd Law Lab (Modeling friendly lab)
Go to the PhET simulation Forces & Motion. https://phet.colorado.edu/sims/html/forcesandmotionbasics/latest/forcesandmotionbasics_en.html
Select “Acceleration”
Click to show Forces, Sum of Forces, Values, Mass, and Acceleration.
There are two experiments for this activity – make sure you include both.
Experiment #1: Acceleration vs. Force
In this lab you will determine the relationship between acceleration and net force.
Choose a mass at the beginning, and keep it constant for this entire experiment.
Set the friction to zero. This will make your Applied Force equal to the net force.
Record data for five different values of Applied Force.
Graph Acceleration vs. Net Force.
Graph this in Google sheets(you want a line graph - it should only have one line).
Make sure that Applied Force information is used as the x value
Make sure that Acceleration information is used as the y value
Add a trendline – see what fits best –…
arrow_forward
O NWP Assessment Builder UI Appl X
O NWP Assessment Player UI Appli X
+
->
i education.wiley.com/was/ui/v2/assessment-player/index.html?launchld=4599c668-aabf-4aa6-a299-d14a1c37f643#/question/12
E
E Apps
Q Hydrogeology Flas..
3 That Time I Got Rei..
MATLAB Online R2..
Chem Exam 2 Flash...
СОР2030 Моdule 3..
6 SSMagon - ME137L...
S Easy to use Online...
E Reading list
>>
Chapter 4 Homework
Question 5
0/1
Question 13 of 14
-/ 1
Math Fill in the Blank
X Incorrect
Question 6
1/1
v Correct
As shown in the figure, Refrigerant 22 enters the compressor of an air conditioning unit operating at steady state at 40°F, 80 lbf/in?
and is compressed to 160°F, 200 Ib;/in?. The refrigerant exiting the compressor enters a condenser where energy transfer to air as a
separate stream occurs, and the refrigerant exits as a liquid at 200 lb;/in?, 90°F. Air enters the condenser at 70°F, 14.7 Ib;/in? with a
volumetric flow rate of 1000 ft°/min and exits at 110°F. Neglect stray heat transfer and kinetic and…
arrow_forward
SEE MORE QUESTIONS
Recommended textbooks for you
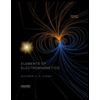
Elements Of Electromagnetics
Mechanical Engineering
ISBN:9780190698614
Author:Sadiku, Matthew N. O.
Publisher:Oxford University Press
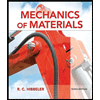
Mechanics of Materials (10th Edition)
Mechanical Engineering
ISBN:9780134319650
Author:Russell C. Hibbeler
Publisher:PEARSON
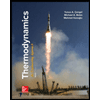
Thermodynamics: An Engineering Approach
Mechanical Engineering
ISBN:9781259822674
Author:Yunus A. Cengel Dr., Michael A. Boles
Publisher:McGraw-Hill Education
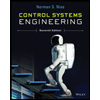
Control Systems Engineering
Mechanical Engineering
ISBN:9781118170519
Author:Norman S. Nise
Publisher:WILEY
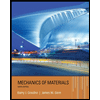
Mechanics of Materials (MindTap Course List)
Mechanical Engineering
ISBN:9781337093347
Author:Barry J. Goodno, James M. Gere
Publisher:Cengage Learning
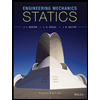
Engineering Mechanics: Statics
Mechanical Engineering
ISBN:9781118807330
Author:James L. Meriam, L. G. Kraige, J. N. Bolton
Publisher:WILEY
Related Questions
- https://drive.google.com/file/d/1X0Sk9U2pT7lwJ9IB--kLkGngHm46SywH/view?usp=sharingarrow_forward11°C Mostly cloudy ליזום Queen's Online x MEE1018 2221ES2 1.1 X Past paper examples ex Cengal Appendix1 Slu x b Security | bartleby https://qubstudentcloud.sharepoint.com/sites/exampastpapers/Papers/MEE/MEE1018/MEE1018 2221ES2_1_198.pdf @ ✩ Draw n F2 £ 1 2 3 Ꮕ W a Ask Copilot 2 of 15 (b) During a process, 2 kg of methane (CH) is heated from 800 K to 1200 K at constant volume. Mcarbon 12 kg/kmol, Maydrogen = 1 kg/kmol and Cp(Methane) 2.2537 kJ/kg.K (i) Determine the specific gas constant for methane. (ii) Calculate the change in entropy during the process. (iii) Determine the work done. = [6 marks] (c) An air conditioning unit with COP = 8 removes heat from a room to the atmosphere at a rate of 2 kW. Assuming electrical and mechanical efficiencies are 100%, determine the rate of heat transfer to the atmosphere and the required power input. [3 marks] (d) 4 kg of a gas undergoes the cycle in Figure Q1(d). Describe each process in the cycle and calculate the net work. E P (kPa) <» 120 DII…arrow_forwardCourse Home llege.com/course.html?courseld=17313546&OpenVellumHMAC=1c89e19b153e443490bb4df0da3b2ded#10001 to Review | Constants pour unistur very unu sıyın mm nyurve. Fv = 390 N Sur Previous Answers Mountaineers often use a rope to lower themselves down the face of a cliff (this is called rappelling). They do this with their body nearly horizontal and their feet pushing against the cliff (Eigure 1). Suppose that an 78.6-kg climber, who is 1.88 m tall and has a center of gravity 1.0 m from his feet, rappels down a vertical cliff with his body raised 40.4° above the horizontal. He holds the rope 1.54 m from his feet, and it makes a 20.7° angle with the cliff face. ✓ Correct Part D Figure 1 of 1 What minimum coefficient of static friction is needed to prevent the climber's feet from slipping on the cliff face if he has one foot at a time against the cliff? Express your answer using two significant figures. {—| ΑΣΦ ? fs= Submit Provide Feedback Next > P Pearson Copyright © 2022 Pearson…arrow_forward
- this is a practice problem, not a graded assignmentarrow_forwardChrome File Edit View History Bookmarks People Tab Window Help McGraw-Hill Campus - ALEKS Science - CHM1045 GEN CHEM 1 BLENDED 669113 A bconline.broward.edu/d21/le/content/466883/fullscreen/12868783/View McGraw-Hill Campus - ALEKS Science O GASES Interconverting pressure and force A chemistry graduate student is designing a pressure vessel for an experiment. The vessel will contain gases at pressures up to 470.0 MPa. The student's design calls for an observation port on the side of the vessel (see diagram below). The bolts that hold the cover of this port onto the vessel can safely withstand a force of 2.80 MN. pressure vessel bolts side View port Calculate the maximum safe diameter w of the port. Round your answer to the nearest 0.1 cm. O cm Explanation Check O2021 McGraw-Hill Education. All Rights Reserved. Terms of Use FEBarrow_forwardspital 7 334 3140 (Med 391 2659 ai Queers $ 307 7683 P 808 9646 X Online Course | CHNU X e to search https://university.chnnyc.org/#/online-courses/3fa2e3bd-5548-487b-9f07-5afe50ba5f5c DCA A1C Menu O Tefinical Dept art Rosanny-2443 Bi a dca alc weekls matian XQ dca alc manual - Sear X DCA Vantage Analyze X Privacy error 4 ✓Clean exterior of analyzer Change air filter 7184832 777-2 Which of the following are weekly maintenance tasks? Check all that apply. Clean cartridge spring Perform optical test Clean barcode window F6 Fr hp LANGUAGE LINE 844-401 8401 LIC-6417 10 FB Chip FO xMail-Tyron Grant-CX a covermymeds - Search X G F10 F11 B F12 Drink Pit Bom x 3 SUBMIT Fra Seark Lock Pass Searrow_forward
- O NWP Assessment Builder UI Appl X O NWP Assessment Player UI Appli X + -> A education.wiley.com/was/ui/v2/assessment-player/index.html?launchld=4599c668-aabf-4aa6-a299-d14a1c37f643#/question/2 E E Apps Q Hydrogeology Flas.. 3 That Time I Got Rei... MATLAB Online R2.. Chem Exam 2 Flash.. СОР2030 Мodule 3... A SSMagon - ME137L... S Easy to use Online... E Reading list >> E Chapter 4 Homework Question 3 of 14 > 0/1 Your answer is incorrect. Refrigerant 134a enters a well-insulated nozzle at 200 Ibf/in.?, 140°F, with a velocity of 120 ft/s and exits at 50 Ibf/in.? with a velocity of 1500 ft/s. For steady-state operation, and neglecting potential energy effects, determine the temperature, in °F, and the quality of the refrigerant at the exit. T2 = i 72.78 °F X2 = i 75.9019 eTextbook and Media Hint 7:31 PM O Type here to search 30°C Partly cloudy 22/09/2021 Darrow_forwardiPhone -... blem Set 1 Question 1 of 10 View Policies Current Attempt in Progress X = y = Electric C... Z= I eTextbook and Media Save for Later in https://m... education.wiley.com National... The force, F, of the wind blowing against a building is given by F = CopV²A/2, where Vis the wind speed, p the density of the air, A the cross-sectional area of the building, and CD is a constant termed the drag coefficient. Determine the dimensions of the drag coefficient, x, y, and z in the expression CD = M*LYT. i WP Problem... W Support -... WP NWP Ass... -/10 E Start Pag Attempts: 0 of 5 used Submit Answerarrow_forwardpermanent-magnet (pm) genera x Bb Blackboard Learn L STAND-ALONE.mp4 - Google Dri x O Google Drive: ülwgjuó jc lis u O ME526-WindEnergy-L25-Shuja.p x O File | C:/Users/Administrator/Desktop/KFUPM%20Term%232/ME526/ME526-WindEnergy-L25-Shuja.pdf (D Page view A Read aloud T) Add text V Draw Y Highlight O Erase 17 of 26 Wind Farms Consider the arrangement of three wind turbines in the following schematic in which wind turbine C is in the wakes of turbines A and B. Given the following: - Uo = 12 m/s A -XẠC = 500 m -XBC = 200 m - z = 60 m - Zo = 0.3 m U. -r, = 20 m B - CT = 0.88 Compute the total velocity deficit, udef(C) and the velocity at wind turbine C, namely Vc. Activate Windows Go to Settings to activate Windows. Wind Farms (Example Answer) 5:43 PM A 4)) ENG 5/3/2022 I!arrow_forward
- -Sear x dynamics systems questions 1[1 x Week 15-Mechanical (Tutorials x + | C:/Users/40332698/AppData/Local/Packages/microsoft windowscommunicationsapps_8wekyb3d8bbwe/LocalState/Files/SO/145/Attachments/dynamics%... Q - +3 Page view A Read aloud Add textDraw Highlight V Erase ate the 3/104 The car is moving with a speed vo= 105 km/h up the 6-percent grade, and the driver applies the brakes at point A, causing all wheels to skid. The coefficient of kinetic friction for the rain-slicked bogne-road is = 0.60. Determine the stopping distance ed ISAB. Repeat your calculations for the case when the booga car is moving downhill from B to A. the case -8.0 ai noilsi' SA noitisoq de JDT mot gainnige ge = $1 bacilyon A S → vo 6 search 10. $ R F T V 25 % 5 T G B O Ai O A 6 Y H N & 7 U J Fa ★ 8 M 1 K FO 100 9 prt sc F10 O L ) O home P ; B A end F12 { ? + insert } 1 To 6 9°C Cloudy DENG ^ 7arrow_forwardO NWP Assessment Builder UI Appl X O NWP Assessment Player UI Appli X + -> A education.wiley.com/was/ui/v2/assessment-player/index.html?launchld=4599c668-aabf-4aa6-a299-d14a1c37f643#/question/13 E E Apps Q Hydrogeology Flas... 3 That Time I Got Rei... MATLAB Online R2... Chem Exam 2 Flash... COP2030 Module 3.. 6 SSMagon - ME137L... S Easy to use Online... E Reading list >> E Chapter 4 Homework Question 14 of 14 -/1 View Policies Current Attempt in Progress As shown in the figure, a 300-ft tank contains 25 lb of H2O initially at 30 lbf/in?. The tank is connected to a large steam line carrying steam at 200 Ibf/in?, 450°F. Steam flows into the tank through a valve until the tank pressure reaches p2 = 120 lbf/in? and the temperature is 400°F, at which time the valve is closed. Steam at 200 lbf/in.². 450°F Tank Valve (1) Initially: 30 lbfin.?, mı = 25 lb |(2) Finally: Ibfin.?, 400°F. P2 Determine the amount of mass that enters the tank, in Ib, and the heat transfer to the tank from its…arrow_forwardM Inbox - wep10@zips.uakron.edu O My Akron Experience - The Univ B Homepage - Statics 801 O Pearson MyLab and Mastering b The equivalent resultant force, di x Course Home A https://openvellum.ecollege.com/course.html?courseld=16245503&OpenVellumHMAC=67fab398401alafde96db3b49e605db9#10001 O My Courses KAssignment 10o Course Home Problem 4.137 3 of 4 Syllabus I Review Scores Replace the three forces acting on the plate by a wrench. Suppose that FA = {450i}N, FB = {-350k} N, and Fc = {300j} N. (Figure 1) Part B eТext Determine the couple moment of the wrench. Express your answer to three significant figures and include the appropriate units. Enter positive value if the sense of direction of the couple moment is the same as that of the resultant force and negative value if the sense of direction of the couple moment is opposite to that of the resultant force. Study Area Document Sharing TH HẢ ? User Settings Value Units Course Tools > Submit Previous Answers Request Answer X Incorrect; Try…arrow_forward
arrow_back_ios
SEE MORE QUESTIONS
arrow_forward_ios
Recommended textbooks for you
- Elements Of ElectromagneticsMechanical EngineeringISBN:9780190698614Author:Sadiku, Matthew N. O.Publisher:Oxford University PressMechanics of Materials (10th Edition)Mechanical EngineeringISBN:9780134319650Author:Russell C. HibbelerPublisher:PEARSONThermodynamics: An Engineering ApproachMechanical EngineeringISBN:9781259822674Author:Yunus A. Cengel Dr., Michael A. BolesPublisher:McGraw-Hill Education
- Control Systems EngineeringMechanical EngineeringISBN:9781118170519Author:Norman S. NisePublisher:WILEYMechanics of Materials (MindTap Course List)Mechanical EngineeringISBN:9781337093347Author:Barry J. Goodno, James M. GerePublisher:Cengage LearningEngineering Mechanics: StaticsMechanical EngineeringISBN:9781118807330Author:James L. Meriam, L. G. Kraige, J. N. BoltonPublisher:WILEY
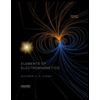
Elements Of Electromagnetics
Mechanical Engineering
ISBN:9780190698614
Author:Sadiku, Matthew N. O.
Publisher:Oxford University Press
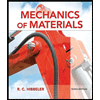
Mechanics of Materials (10th Edition)
Mechanical Engineering
ISBN:9780134319650
Author:Russell C. Hibbeler
Publisher:PEARSON
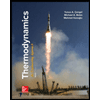
Thermodynamics: An Engineering Approach
Mechanical Engineering
ISBN:9781259822674
Author:Yunus A. Cengel Dr., Michael A. Boles
Publisher:McGraw-Hill Education
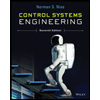
Control Systems Engineering
Mechanical Engineering
ISBN:9781118170519
Author:Norman S. Nise
Publisher:WILEY
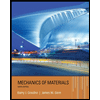
Mechanics of Materials (MindTap Course List)
Mechanical Engineering
ISBN:9781337093347
Author:Barry J. Goodno, James M. Gere
Publisher:Cengage Learning
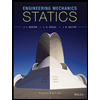
Engineering Mechanics: Statics
Mechanical Engineering
ISBN:9781118807330
Author:James L. Meriam, L. G. Kraige, J. N. Bolton
Publisher:WILEY