MET414_Midterm_Richardson_Brendon
docx
keyboard_arrow_up
School
ECPI University, Virginia Beach *
*We aren’t endorsed by this school
Course
414
Subject
Mechanical Engineering
Date
Apr 3, 2024
Type
docx
Pages
5
Uploaded by AmbassadorWildcatMaster552
Problem One
The circular rod shown is made of the steel alloy AISI 4140 OQT 700. It has a diameter of 2.00 in and an initial length of 72 in. An axial tensile load of 35 000 lb is applied during a certain operation.
Compute:
1.
the equivalent spring constant K,
2.
the deformation X of the rod.
The Young’s modulus of the steel is known to be 30,000,000 psi.
Problem Two
Write the global stiffness matrix of the spring assemblage shown. Assume that all springs remain horizontal, the vertical bars at nodes 2 and 3 are rigid
and allowed to slide horizontally to the left or right.
Your preview ends here
Eager to read complete document? Join bartleby learn and gain access to the full version
- Access to all documents
- Unlimited textbook solutions
- 24/7 expert homework help
Problem Three
In this problem, you are asked to perform a linear static stress analysis of the
fitting
shown. The procedure is the same as that of the “Linear Static Analysis of a fitting” tutorial except for the size of the part and thus, the location of the applied load. Make sure that diagrams of displacement and Von Mises stress are included in your analysis report.
Download and save the part file
fitting altered.ipt
Start Autodesk Inventor
Open the file
fitting altered.ipt
you downloaded previously
Click
File
,
Save As
and save the part as
fitting altered Midterm.ipt
. This allows you to reuse the original part.
Enter the Nastran through “Environments” tab
Walk through the entire
Linear Static Analysis of a Fitting
tutorial and complete all the tasks. (Skip any slide that asks you to download or open the original fitting file).
Make sure that you have saved the
report
and the
Inventor file
as instructed at the end of the tutorial
Problem Four
In this problem, you are asked to perform a linear static stress analysis
of simple lever arm shown. The procedure is the same as that of
Sec 05
“Cast Lever Exercise” except for the loading
. Make sure that diagrams of displacement and Von Mises stress are included in your analysis report.
Analytically re-calculate the force R acting on point C. It will no longer be 687.5 N as previously found and listed in the slides
Download and save the part file
Cast Lever.ipt
Start Autodesk Inventor
Open the file
Cast Lever.ipt
you downloaded previously
Click
File
,
Save As
and save the part as
Cast Lever Midterm.ipt
. This allows you to reuse the original part.
Enter the Nastran through “Environments” tab
Walk through
Sec 05 Cast Lever Exercise
Links to an external site.
and complete all the tasks. Remember that while the boundary
conditions are the same, the loading
will be different
. (Skip any slide that asks you to download or open the Cast Lever file).
Generate and save the report HTML file as “Cast Lever New Load”. Make sure the displacement and Von Mises stress diagram are included.
Save the Inventor file
Related Documents
Related Questions
PROBLEM: 5 A helical valve spring is to be designed for an operating load range of 90N to 195N. The maximum deflection of the spring for this load range is 7.5 mm. Assuming a spring index of 9, a permissible shear stress of 550 N/mm2 for the material and the modulus of rigidity of 0.85x105 N/mm2. Determine the dimensions of the spring. (i.e. Diameter of the spring wire ,Mean coil diameter, Outer diameter of the spring, number of active turn and free length of the spring). Assume the spring coil is squared and ground.
arrow_forward
A helical compression spring has a scale of 500 lb/in., an outside diameter of 2.75 in, a free length of 8 inches and with squared and ground ends. The load is 1,000 lbs and the working stress on the wire material is 65000 psi. If the Wahl factor of 1.25 is to be used, calculate the following:
A. The standard wire diameter
B. The number of active coil if G = 10 800 000 psi
C. The solid height
D. The stress at solid height
arrow_forward
A helical compression spring is subjected to a maximum force, Fmax of 1250 N. The deflection
of the spring corresponding to the maximum force should be approximately 30 mm. The spring
index is 6. The allowable shear stress is 350 MPa and the modulus of rigidity is 81 370 N/mm².
Design the helical spring by calculating the wire diameter, mean coil diameter, number of active
coils and the total number of coils. State all assumptions and decisions in your design.
arrow_forward
A helical spring is made of 10 m diameter steel wire wound on a 100 mm diameter mandrel. If there are 10 active coils what is spring constant Take: C= 100 GPA What force must be applied to the spring to elongate it by 50 mm?
arrow_forward
Required information
A helical compression spring is wound using music wire of diameter, d, 2.16 mm. The
spring has an outside diameter, OD, of 27 mm with plain ground ends and 14 coils.
NOTE: This is a multi-part question. Once an answer is submitted, you will be unable to
return to this part.
What should be the free length to ensure that the torsional stress does not exceed the yield strength
when the spring is compressed solid? What is the critical free length? Is there a possibility that the spring
might buckle in service?
The free length should be
|mm.
The critical free length should be
Buckling is likely
Eto occur.
mm.
arrow_forward
1. Design a compression helical spring to carry a load of 500 N with a deflection of 25 mm. The spring
index may be taken as 8. Assume the following values for the spring material:
Permissible shear stress
= 350 MPa
Modulus of rigidity
= 84 kN/mm2
4С - 1
0.615
Wahl's factor
where C-spring index.
4С - 4
arrow_forward
A helical compression spring has a scale of 400 lbs/inch, an inside diameter of 2.5 inches, a free length of 8 inches and with squared and ground ends. Material is to be chrome vanadium steel. For a load P of 750 lbs and for the average service
Determine the standard size wire diameter
Determine the number of active coils
Determine the solid height
Determine the stress at solid height
arrow_forward
A helical compression spring is wound using 0.12-in-diameter phosphor-bronze B159 wire. The spring index
C = 10 and the total number of coils is N = 14. You may assume that the spring has both ends squared and
ground and is supported between fixed ends. Also, Sgy = 0.45 · Sut-
a. Estimate the spring rate.
b. Estimate the static load corresponding to the yield strength.
c. What should the free length of the spring be to ensure that when it is compressed solid the torsional
stress does not exceed the yield strength?
d. Calculate the critical value of the free length of the spring to avoid buckling.
arrow_forward
Required information
A helical compression spring is wound using music wire of diameter, d, 2.16 mm. The
spring has an outside diameter, OD, of 27 mm with plain ground ends and 14 coils.
NOTE: This is a multi-part question. Once an answer is submitted, you will be unable to
return to this part.
What is the force needed to compress this spring to closure assuming that the spring will reach its shear
strength at its solid length?
The force needed to compress this spring to closure is
|N.
arrow_forward
4. A vertical spring loaded valve is required for a compressed air receiver. The valve is to start opening
at a pressure of 1 N/mm2 gauge and must be fully open with a lift of 4 mm at a pressure of 1.2 N/mm?
gauge. The diameter of the port is 25 mm. Assume the allowable shear stress in steel as 480 MPa and
shear modulus as 80 kN/mm.
Design a suitable close coiled round section helical spring having squared ground ends. Also specify
initial compression and free length of the spring.
arrow_forward
A helical compression spring is required for a mechanism under static loading with a maximum
force of 1250N. The deflection caused by this load is 30mm the ends are squared and ground.
The spring has an index of 6 and is made of cold drawn steel wire with tensile strength of 1090
N/mm and modulus of rigidity of 81370 N/mm2. The permissible shear strength is taken as 50%
of the ultimate tensile strength. Design the spring and calculate:
(a) The wire diameter
(b) Mean coil diameter.
(c) Number of active coils
(d) Total number of coils
(e) Free length of the spring
(f) Pitch of the coil
arrow_forward
Problem 4:
A helical compression spring is to be cycled between 150 lbf and 300 lbf with a 1-in stroke. The number of
cycles is low, so fatigue is not an issue. The coil must fit in a 2.1-in diameter hole with a 0.1-in clearance
all the way around the spring. Use unpeened music wire with squared and ground ends.
(a) Determine a suitable wire diameter, using a spring index of C = 7.
(b) Determine a suitable mean coil diameter.
(c) Determine the necessary spring constant.
(d) Determine a suitable total number of coils.
(e) Determine the necessary free length so that if the spring were compressed to its solid length,
there would be no yielding
arrow_forward
5. Design a helical compression spring for a maximum load of 1000 N and deflection of 25mm taking Wahl’s factor into consideration. Assume spring index as 5, maximum permissible shear stress for spring wire as 420 MPa and modulus of rigidity as 84 kN/mm2
arrow_forward
SEE MORE QUESTIONS
Recommended textbooks for you
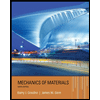
Mechanics of Materials (MindTap Course List)
Mechanical Engineering
ISBN:9781337093347
Author:Barry J. Goodno, James M. Gere
Publisher:Cengage Learning
Related Questions
- PROBLEM: 5 A helical valve spring is to be designed for an operating load range of 90N to 195N. The maximum deflection of the spring for this load range is 7.5 mm. Assuming a spring index of 9, a permissible shear stress of 550 N/mm2 for the material and the modulus of rigidity of 0.85x105 N/mm2. Determine the dimensions of the spring. (i.e. Diameter of the spring wire ,Mean coil diameter, Outer diameter of the spring, number of active turn and free length of the spring). Assume the spring coil is squared and ground.arrow_forwardA helical compression spring has a scale of 500 lb/in., an outside diameter of 2.75 in, a free length of 8 inches and with squared and ground ends. The load is 1,000 lbs and the working stress on the wire material is 65000 psi. If the Wahl factor of 1.25 is to be used, calculate the following: A. The standard wire diameter B. The number of active coil if G = 10 800 000 psi C. The solid height D. The stress at solid heightarrow_forwardA helical compression spring is subjected to a maximum force, Fmax of 1250 N. The deflection of the spring corresponding to the maximum force should be approximately 30 mm. The spring index is 6. The allowable shear stress is 350 MPa and the modulus of rigidity is 81 370 N/mm². Design the helical spring by calculating the wire diameter, mean coil diameter, number of active coils and the total number of coils. State all assumptions and decisions in your design.arrow_forward
- A helical spring is made of 10 m diameter steel wire wound on a 100 mm diameter mandrel. If there are 10 active coils what is spring constant Take: C= 100 GPA What force must be applied to the spring to elongate it by 50 mm?arrow_forwardRequired information A helical compression spring is wound using music wire of diameter, d, 2.16 mm. The spring has an outside diameter, OD, of 27 mm with plain ground ends and 14 coils. NOTE: This is a multi-part question. Once an answer is submitted, you will be unable to return to this part. What should be the free length to ensure that the torsional stress does not exceed the yield strength when the spring is compressed solid? What is the critical free length? Is there a possibility that the spring might buckle in service? The free length should be |mm. The critical free length should be Buckling is likely Eto occur. mm.arrow_forward1. Design a compression helical spring to carry a load of 500 N with a deflection of 25 mm. The spring index may be taken as 8. Assume the following values for the spring material: Permissible shear stress = 350 MPa Modulus of rigidity = 84 kN/mm2 4С - 1 0.615 Wahl's factor where C-spring index. 4С - 4arrow_forward
- A helical compression spring has a scale of 400 lbs/inch, an inside diameter of 2.5 inches, a free length of 8 inches and with squared and ground ends. Material is to be chrome vanadium steel. For a load P of 750 lbs and for the average service Determine the standard size wire diameter Determine the number of active coils Determine the solid height Determine the stress at solid heightarrow_forwardA helical compression spring is wound using 0.12-in-diameter phosphor-bronze B159 wire. The spring index C = 10 and the total number of coils is N = 14. You may assume that the spring has both ends squared and ground and is supported between fixed ends. Also, Sgy = 0.45 · Sut- a. Estimate the spring rate. b. Estimate the static load corresponding to the yield strength. c. What should the free length of the spring be to ensure that when it is compressed solid the torsional stress does not exceed the yield strength? d. Calculate the critical value of the free length of the spring to avoid buckling.arrow_forwardRequired information A helical compression spring is wound using music wire of diameter, d, 2.16 mm. The spring has an outside diameter, OD, of 27 mm with plain ground ends and 14 coils. NOTE: This is a multi-part question. Once an answer is submitted, you will be unable to return to this part. What is the force needed to compress this spring to closure assuming that the spring will reach its shear strength at its solid length? The force needed to compress this spring to closure is |N.arrow_forward
- 4. A vertical spring loaded valve is required for a compressed air receiver. The valve is to start opening at a pressure of 1 N/mm2 gauge and must be fully open with a lift of 4 mm at a pressure of 1.2 N/mm? gauge. The diameter of the port is 25 mm. Assume the allowable shear stress in steel as 480 MPa and shear modulus as 80 kN/mm. Design a suitable close coiled round section helical spring having squared ground ends. Also specify initial compression and free length of the spring.arrow_forwardA helical compression spring is required for a mechanism under static loading with a maximum force of 1250N. The deflection caused by this load is 30mm the ends are squared and ground. The spring has an index of 6 and is made of cold drawn steel wire with tensile strength of 1090 N/mm and modulus of rigidity of 81370 N/mm2. The permissible shear strength is taken as 50% of the ultimate tensile strength. Design the spring and calculate: (a) The wire diameter (b) Mean coil diameter. (c) Number of active coils (d) Total number of coils (e) Free length of the spring (f) Pitch of the coilarrow_forwardProblem 4: A helical compression spring is to be cycled between 150 lbf and 300 lbf with a 1-in stroke. The number of cycles is low, so fatigue is not an issue. The coil must fit in a 2.1-in diameter hole with a 0.1-in clearance all the way around the spring. Use unpeened music wire with squared and ground ends. (a) Determine a suitable wire diameter, using a spring index of C = 7. (b) Determine a suitable mean coil diameter. (c) Determine the necessary spring constant. (d) Determine a suitable total number of coils. (e) Determine the necessary free length so that if the spring were compressed to its solid length, there would be no yieldingarrow_forward
arrow_back_ios
SEE MORE QUESTIONS
arrow_forward_ios
Recommended textbooks for you
- Mechanics of Materials (MindTap Course List)Mechanical EngineeringISBN:9781337093347Author:Barry J. Goodno, James M. GerePublisher:Cengage Learning
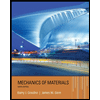
Mechanics of Materials (MindTap Course List)
Mechanical Engineering
ISBN:9781337093347
Author:Barry J. Goodno, James M. Gere
Publisher:Cengage Learning