Lab 3_Instruction Manual_Fall2023 (1)
pdf
keyboard_arrow_up
School
University of Notre Dame *
*We aren’t endorsed by this school
Course
139L
Subject
Mechanical Engineering
Date
Dec 6, 2023
Type
Pages
7
Uploaded by BaronElectron11976
1
ME139L
–
Experimental Heat Transfer
Background and Guidelines for Lab 3
Convective Heat Transfer from a
Boundary Layer Flow on a Flat Plate
Note: This lab meets near the wind tunnel in ETC 1.204. Submit your data to your TA
before leaving the lab. The TA will provide the complete data set from all sections.
Objective
The goal of this lab is to provide an experience of using a wind tunnel to measure local heat
transfer coefficients and Nusselt numbers on a flat plate under laminar and turbulent flow
conditions. Similar measurements are used to obtain the convective heat transfer coefficient
needed for designing gas turbine blades, computer heat sinks, and tube banks used in steam
generation in a boiler or air cooling in the coil of an air conditioner, among many other
industrial applications. You will learn how measurements are made inside the thermal and
hydrodynamic boundary layers, how surface temperatures are determined, and how free stream
conditions are measured.
Your lab session will obtain two data sets. You will perform analysis on both data sets to
produce results for thermal and hydrodynamic boundary layer growth, local heat transfer
coefficients, and local Nusselt numbers for laminar and turbulent flow on a flat plate.
Background
•
The wind tunnel to be used was specifically constructed for determination of heat transfer
coefficients on a flat plate. It can be operated with varying free stream velocities up to the
maximum velocity of about 25 m/s. The test section contains a flat plate, 0
.
633 m long and
0
.
203 m wide, positioned in the center of the wind tunnel.
•
Electrical heating elements are sandwiched between two stainless steel plates that form the
flat plate. Two heating elements are used, one in the front half of the plate, and the other in
the back half. Each heating element is independently connected to a power source.
•
Thermocouples positioned at intervals of 2.54 cm (1 inch) are embedded in the plate along
the centerline. These thermocouples are connected to a Keithley data acquisition system that
is used in combination with a pre-constructed LabVIEW virtual instrument (vi) to monitor
and record surface temperature distribution along the length of the flat plate.
•
The wind tunnel is instrumented with a thermocouple probe and a Preston tube that can be
traversed vertically to provide measurements inside the thermal and hydrodynamic boundary
layers. A Preston probe is a Pitot probe placed in contact with a wall. A Pitot probe measures
the dynamic pressure and flow velocity. Screens may also be used to help condition the flow.
•
Finally, a movable “trip”
that disrupts the boundary layer can be used to generate a turbulent
flow.
PreLab Preparation
Complete an individual prelab assignment for submission before your lab session.
Lab Work
2
Meet with your TA during your regularly assigned lab period. Your TA will conduct a
demonstration of how data is taken in the wind tunnel. The students in each section will then
be divided into two groups to work through the lab procedures provided in the attachment and
answer the questions as you go along.
The Excel spread-sheet that your team prepared in
the PreLab will be used to your calculations.
Record your notes, calculations, and observations on the attached sheets. You may also create
additional pages containing photos, sketches, and/or calculations.
Procedures
Equipment
•
Wind tunnel setup
•
Boundary layer trip
•
Flow conditioning screens
Experiment
•
In the wind tunnel facility, a variety of surface heating rates, flow velocities, and test
configurations are possible. These include velocities in the range between 12 and 25 m/s,
flow conditioning screens that may be either on or off, and a boundary layer trip that may
be placed at the leading edge of the plate or anywhere downstream.
•
Each lab session will complete two experiments and exchange the associated data sets for
subsequent analysis. Therefore, your memorandum will be based on two data sets.
•
Your TA will tell you which configurations will be tested. You are required to submit your
completed Excel data sheet to your TA via email. This will be part of your grade.
•
Two groups will use the same freestream velocity, but run the measurements at two
different locations. It will take some time for the flow to reach steady state for the first
group to start the measurements, whereas the second group can start their measurements
promptly after changing the probe location.
•
Under the guidance of your TA, use the available time in the lab to begin data processing.
Operation of the wind tunnel
At the beginning of the lab, your TA will demonstrate operation of the wind tunnel and, with
the TA’s
help, you will conduct the data acquisition exercise. Detailed instructions for the
operation of the equipment are attached.
You should review and understand these
instructions before the lab.
Important: Make sure that the wind tunnel is running before connecting the
heaters to the power supply
—
if the wind tunnel is not running and the heaters
are left on, the tunnel test section will overheat and can melt.
The heaters must be disconnected from the electrical outlet whenever the wind tunnel is not
running. Our tests have shown that temperatures for the lowest flow speed stay below 85
o
C. If
you ever observe temperatures above 100
o
C, disconnect the heaters while the fan remains
3
running and check the flow velocity. If necessary, increase the flow speed.
Lab calculations
1.
Expected Boundary Layer (BL) transition:
Using the Lab 3 Data Processing Sheet that you prepared in your prelab exercise, calculate the
expected location for a transition from a laminar to turbulent boundary layer at the free-stream
velocity used in your experiment. Use the actual velocity that you measured, which may be
slightly different from the velocity that was assigned due to limits in setting the RPM values
for the fan. Check your result with hand calculations.
Calculations:
Result:
x
tr
=
m
2.
Expected BL thickness:
Using the Lab 3 Data Processing Sheet, compute the (velocity) boundary layer thicknesses
expected at the two measurement positions (25 and 50
cm
from the leading edge) for both
laminar and turbulent conditions. Use the actual velocity measured in your experiment. Check
your result with hand calculations. You can also use the results in your prelab to save time.
However, please note that the prelab results are only rough estimations, since the actual
velocity may be different from the target velocity.
Calculations:
Results for expected boundary layer thickness [mm]:
Table 1 Expected boundary layers
Position
Laminar
Turbulent
x = 25 cm
x = 50 cm
Your preview ends here
Eager to read complete document? Join bartleby learn and gain access to the full version
- Access to all documents
- Unlimited textbook solutions
- 24/7 expert homework help
4
Important Note: Once you have completed the experiment and the lab calculations, submit the
completed Excel worksheet to the TA by the due date specified by your TA. Note that correct
contents and timely submission of the work sheet is part of the lab grade.
Wind Tunnel Start-up and Operation Procedures
Under TA supervision
1.
Change the setup of the tunnel (trip location, screens, etc.) if necessary.
a)
Make sure that both heaters are disconnected and the fan is stopped.
b)
To change the trip position:
•
Carefully
take the traverse off of the wind tunnel.
Note: make sure that you pull
the sensors out of the slots on the top panel without bumping them on the sides.
•
Remove the top cover by un-latching the latches holding it in place.
•
Change the trip position.
•
Remove the bottom cover by un-latching the latches holding it in place.
•
Change the trip position.
•
Reassemble the wind tunnel.
c)
For insertion / removal of the screens:
•
Screens are accessed from the top of the inlet manifold by removing the screws.
2.
Start the wind tunnel:
a)
Verify secure power connection.
b)
Check the VFD control unit to verify that the cooling fan is active. If it is not,
disconnect the power to the unit and restart.
c)
Do not enter the VFD menu setting
s because it is possible to damage the fan.
3.
Set the wind tunnel velocity using the inclined manometer connected to the Preston tube for
measuring the stagnation pressure and a pressure tap in the wall that measures the static
pressure.
a)
Check the level on top of the manometer and make adjustment if necessary by
gently pushing on the manometer setup.
b)
Move the traverse to the front of the tunnel upstream of the flat plate and position
the Preston tube about 2 inch from the top of the plate. Press the foam firmly into
the slots on the top of the tunnel to seal the tunnel.
Make sure the foam is sealed
around the sensors
.
Note:
when moving the traverse, make sure that the Preston
tube and thermocouple are not resting on the plate to prevent scratching the plate.
c)
Turn on the fan by pressing the FWD button on the controller.
Note: the fan will
revert to its previous RPM settings, so it is a good idea to hold the “down” arrow
to stop an unwanted increase in fan RPM.
d)
Set the fan to the desired speed by pressing the up and down arrow buttons. You
are given values in the unit of m/s so you need to convert the unit to ft/min.
Adjust
the velocity to be as close as possible to the value specified by the TA and
record the actual velocity read on the manometer.
Read the velocity at the
middle of the meniscus.
Note: the fan has a delay when the RPM is changed on the
5
controller, so be careful not to overshoot the velocity.
e)
Record the fan speed and velocity used in your experiment.
Table 2 Fan speed and actual velocity
Actual Velocity (ft/min)
Actual Fan speed (rpm)
4.
Power into the heater is determined using the electrical resistance of the heaters.
a)
Use the Keithley multimeter to measure the resistance of the heaters across the
plugs and measure the voltage in the electrical outlet.
Note: for the resistance/
voltage measurements, you need to switch the Keithley multimeter to front input
(button on right hand side of the front panel) and you may need to turn it off and
back on if it does not respond.
Table 3 Power measurements
Resistance of the front heater (Ohms)
Resistance of the back heater (Ohms)
Voltage of the power outlet (Volts)
5.
Power on the laptop and log in. Also make sure that the Keithley instrument is turned on,
connected to the laptop through the
bottom
USB port, and set to the back input.
6.
Connect the heaters and record the start time of the experiment. If the heaters have already
been on from a previous experiment, make a note that the plate was not initially at room
temperature.
Table 4 Time measurements
Time at start of experiment:
7.
Use the LabVIEW vi ME139L_windtunnel.vi (shortcut on the desktop) to monitor the
temperature distribution along the plate. In case the vi cannot establish a connection to the
Keithley instrument, close the LabVIEW vi, make sure the Keithley instrument is turned
on and the input is set to the back, and reload the vi. If necessary turn the Keithley device
off and back on. You can work on your lab calculations while waiting for equilibrium
(steady state) to be reached.
8.
Once equilibrium is reached, record the time and calculate the total time that it takes to
reach equilibrium.
6
9.
Table 5 Time measurements (The second group of each section needs to ask the first
group for the data)
Time Equilibrium is reached:
Total time to equilibrium (min)
Also, record any observations and peculiarities of the temperature profiles.
Notes:
10.
Save the temperature distribution along the plate to a file (you will be prompted for a file
name). This will be saved as a text file.
11.
Open the Excel template that you prepared in your prelab.
a)
Fill in information about the test configuration.
b)
Observe that the calculated data seems reasonable.
c)
Open the file containing the temperature profile along the plate and copy the data
to the template in the space provided for this data.
12.
Stop LabVIEW vi; turn the Keithley multimeter off and on to re-initialize the instrument.
13.
On the Keithley multimeter, select channel 212 (connected to thermocouple mounted on
traverse) and change measurement type to “Temperature.”
14.
Use your prelab spreadsheet to calculate expected boundary layer thicknesses at x = 25 cm
and x = 50 cm.
15.
Measure the freestream (FS) velocity and temperature with the movable Preston tube and
thermocouple about 2 inches off of the plate, at 25 cm and 50 cm from the leading edge.
Table 6 measurements for the freestream velocity and temperature
FS Velocity at 25 cm:
FS Temperature at 25 cm:
FS Velocity at 50 cm:
FS Temperature at 50 cm:
16.
Measure temperature and velocity profiles and estimate the boundary layer thicknesses at
two positions, 25 cm and 50 cm from the leading edge of the plate. Record this data in the
Excel template. Use an increment such that you
take at least 15 measurements in the
boundary layer
. To determine the approximate increment size, divide the boundary layer
thicknesses calculated in step 13 by fifteen. The theoretical thickness may not be exactly
what you find experimentally so continue taking measurements until you have measured
three velocities and temperatures in the freestream (outside the velocity and thermal
boundary layers).
Note: when moving the traverse, make sure to seal the tunnel with the
Your preview ends here
Eager to read complete document? Join bartleby learn and gain access to the full version
- Access to all documents
- Unlimited textbook solutions
- 24/7 expert homework help
7
foam by pushing it into the slots for each measurement.
a)
The
velocity boundary layer
will be measured using the Preston tube that is
mounted on a traverse with a 0
.
001 inch resolution. The difference between the
stagnation pressure measured with the Preston tube and static pressure from the
wall tap is the dynamic pressure, which is a function of velocity. This can be read
directly on the inclined manometer. Recall that static pressure is constant through
the boundary layer.
Note: wait for each reading to stabilize on the manometer.
b)
The
thermal boundary layer
will be measured simultaneously with the velocity
boundary layer. The thermocouple mounted on the traverse is connected to channel
212 of the Keithley multimeter.
Record any observations and peculiarities found during the measurements (e.g.,
fluctuations of the measured values, etc.).
Notes:
Shut-down procedure:
17.
Unplug the heaters.
18.
Reduce fan RPM slowly by using the down arrow followed by the STOP key.
19.
Disconnect power to the fan control unit (Note: the unit will remain on for a short period
of time after being unplugged to allow for cooling)
20.
Switch off the power strip used for heaters, multimeter, and laptop.
Related Documents
Related Questions
8) Consider two liquids, A and B. with temperatures Te > TA. The two objects are put into thermal contact for a
time period. Without just saying 'heat flows from hot to cold' how would you prove to someone that a quantity of
heat flowed from B to Á. (think of James Joule's experiments)
9) If the temperature of the sun were to suddenly double, by what multiplicative factor would the thermal radiation
change ? Show Work
arrow_forward
Mechanical engineering aircon topic. Please help to solve the problem asap. Will upvote for your answer
arrow_forward
i need the answer quickly
arrow_forward
Hi please show calculations or diagrams if required thank you
arrow_forward
please show steps with explanation of the formulas and calculs for more understanding. Thank you!
arrow_forward
7) Give two disadvantages of empirical thermometers.
8) Consider two liquids, A and B. with temperatures Te > TA. The two objects are put into thermal contact for a
time period. Without just saying 'heat flows from hot to cold' how would you prove to someone that a quantity of
heat flowed from B to A. (think of James Joule's experiments)
9) If the temperature of the sun were to suddenly double, by what multiplicative factor would the thermal radiation
change ? Show Work
arrow_forward
Please include explanation and show handwritten solution
arrow_forward
This question is from Heat Transfer class. Please show all steps, thank you!
arrow_forward
After the sinking of RMS Titanic, US operated the International Ice patrol with the purpose of monitoring the presence and movements of icebergs in the Atlantic and Arctic oceans. Once, they observed a unique tabular iceberg in a form of a rectangle (250 km x 50 km x 300 m). How many years would it take to melt the iceberg solely by heat from the sun if the ice absorbs a mean of 98 J/m2 -s, 12.5 hrs per day? Note: the exposed area for heating is 250 km x 50 km and the density is 920 kg/m3 .
This is my solution.
arrow_forward
Pls help ASAP and pls show all steps. PLS ASAP
arrow_forward
V:01
Expert Q&A
Done
Question 1: In your own words, write down the differences
between thermodynamic and heat transfer. (3 Marks)
Question 2: Estimate the heat loss per square metre of surface
through a brick wall 0.5 m thick when the inner surface is at 400
K and the outside surface is at 300 K. The thermal conductivity
of the brick may be taken as 0.7 W/mK. (2 Marks)
Question 3: A furnace is constructed with 0.20 m of firebrick,
0.10 m of insulating brick, and 0.20 m of building brick. The
inside temperature is 1200 K and the outside temperature is 330
K. If the thermal conductivities are as shown in the figure below,
estimate the heat loss per unit area. (5 Marks)
1200 K
330 K
Insulating
brick
X-0.10m
k= 0.21
Ordinary
brick
X=0.20 m
Fire brick
X= 0.20 m
k= 1.4
k= 0.7
(W/mK)
arrow_forward
HEAT TRANSFER
CASE: I want to know what temperature in (°F) the cylinder will have inside. It's a heat transfer problem.
what is T2 ?
HEAT TRANSFER
They gave me an answer all squashed together that i can't make sense of it. If you could help me makes sense of it thank you!
arrow_forward
Im not sure how ro go about this, can you help me figure out these answers or how to get these answers?
arrow_forward
Verify the answer 113kpa.
Please show detailed work in a handwritten format.
Subject: Mechanical engineering,Fluid mechanics.
The Question asks: A 2.5 m tall steel cylinder has a cross sectional area of 1.5 m^2 . At the bottom with a height of 0.5 m is liquid water on top of which is a 1 m high layer of gasoline. The gasoline surface is exposed to atmospheric air at 101kPa. What is the highest pressure in the water?
arrow_forward
4 ) Every temperature measuring instrument makes use of specific physical property in order to measure temperature objectively . Which physical properties are used in thermocouple , PT sensors and mercury - in - glass thermometer ? Briefly describe each of this methods.
arrow_forward
Material properties sheet is attached
arrow_forward
A composite wall is made up of 10 cm of common brick against 15cm of concrete with 1.5 cm of plaster on inside of wall. Assume still air in room at 25 °C. The outside air at 40 °C the wind velocity is 25 km/hr. Note: Use standard tables for values of thermal conductivities and film co-efficient. Find: a) The thermal resistance of wall b) The overall heat transfer cop-efficient. c) The steady state heat transfer rate per unit area of wall d) Heat transfer if the outside and inside film resistances are disgraded
arrow_forward
Why do vapor bubbles get larger in boiling water as they approach the surface? Type your detailed answer on Canvas using thermal concepts.
BIUA A-IEE 33I X x, EE
2 V TT 12pt
• Paragraph
esc
&
%23
%$4
4
5
1
S
F
LE
!! e
arrow_forward
SEE MORE QUESTIONS
Recommended textbooks for you
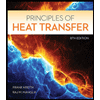
Principles of Heat Transfer (Activate Learning wi...
Mechanical Engineering
ISBN:9781305387102
Author:Kreith, Frank; Manglik, Raj M.
Publisher:Cengage Learning
Related Questions
- 8) Consider two liquids, A and B. with temperatures Te > TA. The two objects are put into thermal contact for a time period. Without just saying 'heat flows from hot to cold' how would you prove to someone that a quantity of heat flowed from B to Á. (think of James Joule's experiments) 9) If the temperature of the sun were to suddenly double, by what multiplicative factor would the thermal radiation change ? Show Workarrow_forwardMechanical engineering aircon topic. Please help to solve the problem asap. Will upvote for your answerarrow_forwardi need the answer quicklyarrow_forward
- Hi please show calculations or diagrams if required thank youarrow_forwardplease show steps with explanation of the formulas and calculs for more understanding. Thank you!arrow_forward7) Give two disadvantages of empirical thermometers. 8) Consider two liquids, A and B. with temperatures Te > TA. The two objects are put into thermal contact for a time period. Without just saying 'heat flows from hot to cold' how would you prove to someone that a quantity of heat flowed from B to A. (think of James Joule's experiments) 9) If the temperature of the sun were to suddenly double, by what multiplicative factor would the thermal radiation change ? Show Workarrow_forward
- Please include explanation and show handwritten solutionarrow_forwardThis question is from Heat Transfer class. Please show all steps, thank you!arrow_forwardAfter the sinking of RMS Titanic, US operated the International Ice patrol with the purpose of monitoring the presence and movements of icebergs in the Atlantic and Arctic oceans. Once, they observed a unique tabular iceberg in a form of a rectangle (250 km x 50 km x 300 m). How many years would it take to melt the iceberg solely by heat from the sun if the ice absorbs a mean of 98 J/m2 -s, 12.5 hrs per day? Note: the exposed area for heating is 250 km x 50 km and the density is 920 kg/m3 . This is my solution.arrow_forward
- Pls help ASAP and pls show all steps. PLS ASAParrow_forwardV:01 Expert Q&A Done Question 1: In your own words, write down the differences between thermodynamic and heat transfer. (3 Marks) Question 2: Estimate the heat loss per square metre of surface through a brick wall 0.5 m thick when the inner surface is at 400 K and the outside surface is at 300 K. The thermal conductivity of the brick may be taken as 0.7 W/mK. (2 Marks) Question 3: A furnace is constructed with 0.20 m of firebrick, 0.10 m of insulating brick, and 0.20 m of building brick. The inside temperature is 1200 K and the outside temperature is 330 K. If the thermal conductivities are as shown in the figure below, estimate the heat loss per unit area. (5 Marks) 1200 K 330 K Insulating brick X-0.10m k= 0.21 Ordinary brick X=0.20 m Fire brick X= 0.20 m k= 1.4 k= 0.7 (W/mK)arrow_forwardHEAT TRANSFER CASE: I want to know what temperature in (°F) the cylinder will have inside. It's a heat transfer problem. what is T2 ? HEAT TRANSFER They gave me an answer all squashed together that i can't make sense of it. If you could help me makes sense of it thank you!arrow_forward
arrow_back_ios
SEE MORE QUESTIONS
arrow_forward_ios
Recommended textbooks for you
- Principles of Heat Transfer (Activate Learning wi...Mechanical EngineeringISBN:9781305387102Author:Kreith, Frank; Manglik, Raj M.Publisher:Cengage Learning
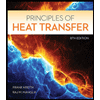
Principles of Heat Transfer (Activate Learning wi...
Mechanical Engineering
ISBN:9781305387102
Author:Kreith, Frank; Manglik, Raj M.
Publisher:Cengage Learning